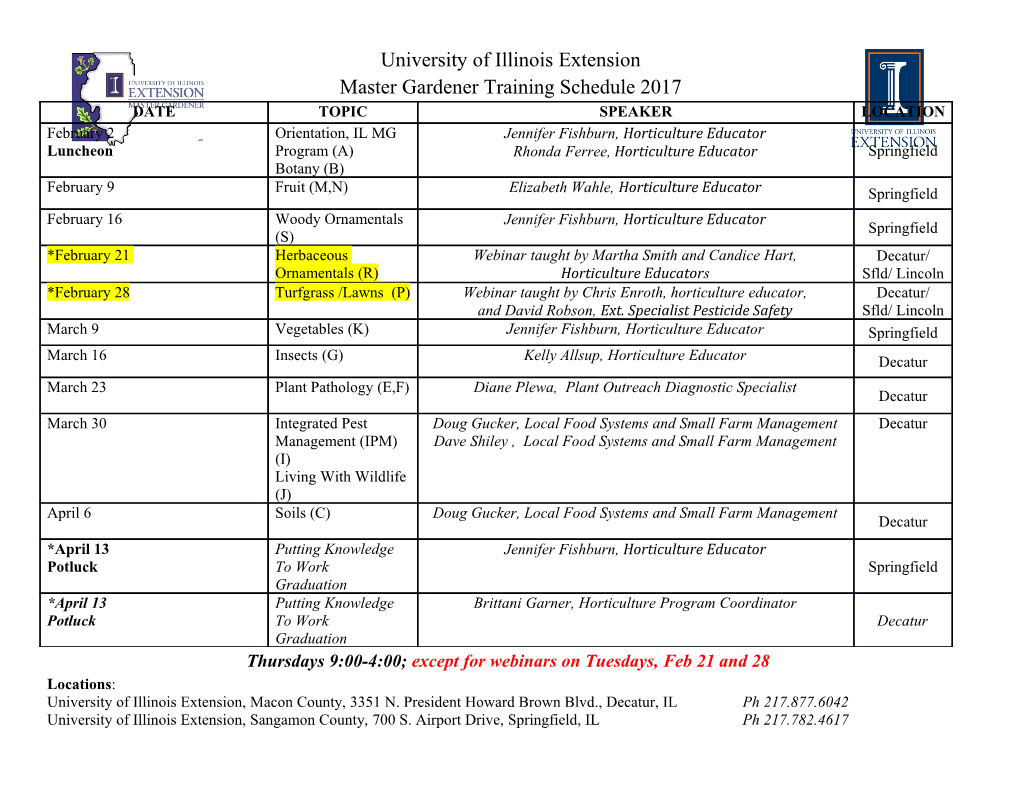
Is SpaceX’s Raptor engine the king of rocket engines? May 25, 2019 In BLOG Blue Origin Featured SPACEX SpaceX’s new Raptor engine is a methane fueled full flow staged combustion cycle engine and it’s so hard to develop, no engine like this has ever flown before! Now this topic can be really intimidating so in order to bring the Raptor engine into context, we’re going to do an overview of a few common types of rocket engine cycles then compare the Raptor to a few other common rocket engines, like SpaceX’s current work horse, the Merlin, The Space Shuttle’s RS-25, the RD-180, Blue Origin’s BE-4 and the F-1 engine. https://www.youtube.com/watch?v=LbH1ZDImaI8 And if that’s not enough, not only is SpaceX using a crazy engine cycle, they’re also going to be using Liquid Methane as their fuel, again something that no orbital rocket has ever used! So we’ll also go over the unique characteristics of liquid methane as a rocket fuel and see if we can figure out why SpaceX went with Methane for the Raptor engine. We’ll also break down and explain all the different engine cycle types so you know what the full flow staged combustion cycle is, how it works, and how it compares to the other cycles. So by the end of this article hopefully we’ll have the context to know why the raptor engine is special, how it compares to other rocket engines, why it’s using methane and hopefully find out if the Raptor engine will be the new king of rocket engines… In case you didn’t notice when you clicked on this article… this is a VERY VERY long article… sorry, not sorry. BUT, if you’re anything like me, you keep hearing a lot of hype about the Raptor engine and you want to appreciate it… but you don’t even know where to start. Well, I’ve spent quite a while really studying up on this subject so I can lay down a good foundation in order to help us fully appreciate the Raptor engine, well and quite frankly, all rocket engines! And if you’re anything like me, maybe you’ve stared at diagrams like this for hours and your head explodes every single time. So to avoid that, I’ve personally whipped up some very simplified versions of the rocket engine cycles for us all to enjoy, which will hopefully help us grasp these concepts. Now we’re going to start with a super quick physics lesson, but bear with me, we’ll dive in and get plenty of nitty gritty details… we’ll leave no stone unturned and by the end of this article hopefully you’ll have a strong grasp of how rocket engines work, the different versions of liquid fueled rocket engines, why methane is a valid choice for fuel, and you’ll know exactly how the Raptor engine stacks up against some other popular rocket engines. Rockets are basically just propellant with some skin around it to keep it in place and they have a thing on the back that can throw said propellant really really fast. And to way over simplify it even more, the faster you can throw that propellant, the better. The easiest way to do this is by storing all the propellant in your tanks under really high pressure, then put a valve on one end of the tank and a propelling nozzle that accelerates the propellant into workable thrust. DONE! No crazy pumps, or complicated systems, just open a valve and let er rip. This is called a pressure fed rocket engine and there’s a few main types; cold gas, monoprop and bipropellant pressure fed engines. You’ll often find these used for reaction control systems because they’re simple, reliable and quick. But pressure fed engines have one big limiting factor. Pressure always flows from high to low, so the engine can never be higher pressure than the propellant tanks. In order to store propellant under high pressure, your tanks will need to be strong and therefore thicker and heavier. Look at composite overwrapped pressure vessels or COPVs. They’re capable of storing gasses at up to almost 10,000 psi or about 700 bar. Despite this, there’s still a limited amount of propellant and pressure they can store. This does not scale up very well when you’re trying to deliver a payload to orbit. So smart rocket scientists quickly realized in order to make the rocket as lightweight as possible, there’s really only ONE thing they could do. Increase the enthalpy. That would be a great 90’s metal band name. You’re welcome internet. Enthalpy is basically the relationship between volume, pressure and temperature. A higher pressure and temperature inside the combustion chamber equals higher efficiency and more mass shoved through the rocket engine equals more thrust. So in order to shove more propellant into the engine, you could either increase the pressure in the tanks, or just shoot the propellant into the combustion chamber with a high powered PUMP. Huh, the second option sounds like a good idea! But PUMPS moving hundreds of liters of fuel per second require a lot and boy do I mean a lot of energy to power them. So what if you took a tiny rocket engine and aimed it right at a turbine to spin it up really fast? You could exchange some of the rocket propellant’s chemical energy for kinetic energy which then could be used to spin these powerful pumps. Welcome to turbopumps and the staged combustion cycle! But you’ve still got some limiting factors, like how high pressure always wants to go to low pressure and how heat has that habit of melting things… So you’ve got to keep all these factors in check while trying to squeeze every bit of power out of your engine. Now there’s actually a lot of cycles here we could talk about, but I’m going to stick with the three most common, or at least the three that matter the most when putting the Raptor into context. We have the gas generator cycle, the partial flow staged combustion cycle and lastly we’ll look at the full flow staged combustion cycle… and perhaps in a future article I’ll try and do a full rundown of all liquid fueled rocket engines including fun new alternatives like the electric pump fed engines seen on Rocket Lab’s Electron rocket. So let’s start with the gas generator cycle otherwise known as the open cycle. This is probably one of the most common types of liquid fueled rocket engines used on orbital rockets. It’s definitely more complicated than a pressure fed system, but it’s fairly simple, well at least compared to their closed cycle counter parts. Now I’m going to way way over simplify this so it’s as easy to grasp as possible. In real life there’s literally dozens of valves, a hive of wires and extra small pipes, helium to back pressure the tanks, fuel flowing through the nozzle and the combustion chamber to cool it, and an ignition source for the preburner and the combustion chamber…. But again, for the purposes of making this simple and as digestible as possible, just know there’s a lot of stuff missing, but we’re focusing on the flow of these engines to get that concept down. Then once you grasp these simple versions, it’ll be much easier to look at one like this and not have your head explode. The gas-generator cycle works by pumping the fuel and oxidizer into the combustion chamber using a turbopump. The turbopump has a few main parts, a mini rocket engine called the preburner, a turbine connected to a shaft and then a pump or two that push propellant into the combustion chamber. You might hear the turbopump assembly called the powerpack because it really is what powers the engine. In the open cycle system, the spent propellant from the preburner is simply dumped overboard and does not contribute any significant thrust. This makes it less efficient since the fuel and oxidizer used to spin the pumps is basically wasted. Now the funny thing about a turbopump is that it’s kind of has a chicken and egg syndrome situation that makes it pretty difficult to start up since the preburner that powers the turbopump needs high pressure fuel and oxidizer to operate… So the preburners requires the turbopumps to spin before it can get up to full operational pressure itself, but the turbopumps need the preburner to fire in order to spin the turbopumps… but the preburner needs the turbopumps etc etc This makes starting a gas generator tricky. There’s a few ways to do this, but we don’t need to get into all of that in this article, that sounds like a fun topic for a future article though. So back to the turbopumps, remember, pressure always flows from high to low, so the turbopumps need to be a higher pressure than the chamber pressure. This means the inlets leading into the preburner is actually the highest pressure point in the entire rocket engine, everything downstream is lower pressure. But notice something here. Take a look at SpaceX’s Merlin engine which runs on RP-1 or Rocket Propellant 1 and Liquid Oxygen. Notice how black the smoke is coming out of the preburner exhaust… Why would it be so sooty compared to the main combustion chamber which leaves almost no visible exhaust? Well that’s because rocket propellant can get super hot….
Details
-
File Typepdf
-
Upload Time-
-
Content LanguagesEnglish
-
Upload UserAnonymous/Not logged-in
-
File Pages26 Page
-
File Size-