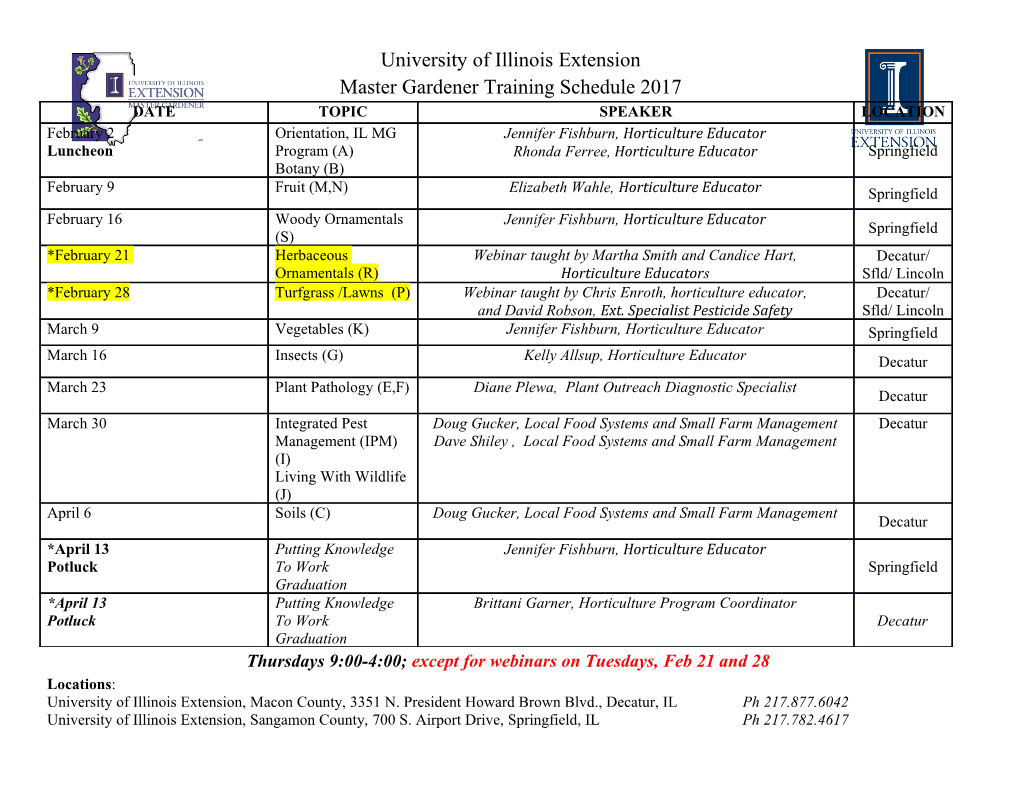
Weldability of Nitrogen-Strengthened Stainless Steels The addition of nitrogen increases yield strength at subzero temperatures and improves resistance to attack by pitting type corrosive media BY R. H. ESPY ABSTRACT. The development of the with the high base metal nitrogen con­ in austenite, information on the four nitrogen-strengthened austenitic stainless tent. alloys is presented. Composition, me­ steels has resulted in materials having chanical properties, cold work hardening, interesting and useful properties that are Introduction wear and galling, corrosion resistance quite different from the conventional AISI and weldability are covered. In each 300 series of stainless steels. The element The development of the nitrogen case, Type 304 stainless is included for nitrogen performs several very interest­ strengthened austenitic stainless steels comparison. ing functions. Nitrogen not only strength­ has resulted in materials having interest­ ens the steel at room temperature, but its ing and useful properties that are quite Composition addition imparts the property of increas­ different from the conventional AISI 300 ing yield strength at subzero tempera­ series of stainless steels. Nitrogen per­ Alloys 33, 40, 50 and 60 are chemically tures. forms several functions. It not only balanced to have an austenite stability In pitting type corrosive media, nitro­ strengthens at room temperature but the well above that of Type 304 stainless. gen (like molybdenum and chromium) nitrogen addition imparts the property of The compositions are shown in Table 1. improves resistance to attack. Where increasing yield strengths at sub zero The four alloys are available in most nitrogen alloying permits, the use of nick­ temperatures. Surface hardening by met­ product forms with the exception of alloy el content less than 6% or silicon addi­ al and particle abrasion results in unusual­ 60 which has not been available in sheet tions improves resistance to transgranular ly good wear and galling characteristics. form. stress corrosion cracking. Nitrogen added In pitting type corrosion media, nitro­ to the steel inhibits carbon migration so gen, like molybdenum and chromium, Mechanical Properties that weld areas show little carbide pre­ improves resistance to attack. Where cipitation even at 0.06% carbon. These nitrogen alloying permits, the use of nick­ The effect of nitrogen as a solid solu­ attractive features of nitrogen additions el contents less than 6% or silicon addi­ tion strengthener is very evident on are used in four commercial alloys, each tions improved resistance to transgranu­ mechanical properties as shown in Tables designed to maximize properties of spe­ lar stress corrosion cracking. Nitrogen 2, 3 and 4. Yield strengths at room cial interest. additions inhibit carbon migration so that temperature are about 20 ksi (138 MPa) weld heat-affected zones show little car­ higher than that of Type 304, and ulti­ Weld filler deposits for four base metal bide precipitation even at 0.06% carbon, mate tensile strengths also average about compositions required composition ad­ and show reduced carbide precipitation 20 ksi (138 MPa) higher. justments to achieve structures of ferrite at carbon levels above 0.06%. in a matrix of austenite. Nitrogen content At temperatures below room temper­ was also lowered to minimize occurrence These properties are used by Armco in ature, solid solution strengtheners have of porosity. The nitrogen levels its NITRONIC* stainless steel nos. 33, 40, employed with the two phase structures 50 and 60 —each designed to optimize were generally sufficient to give weld­ properties of special interest. To better *NlTRONlC is a trademark of Armco Inc., ment tensile strengths equal to those of understand the effect of nitrogen alloying Middletown, Ohio. the unwelded base metals. In autogenous welding, special practices like reduced travel speeds or refusion techniques are required to avoid porosity associated Table 1—Typical Compositions of NITRONIC Stainless Steel Alloys Austenite'3' stability Based on paper sponsored by the American Alloy type c Mn Si Cr Ni Mo N V Cb factor Iron and Steel Institute for presentation at the A WS 61st Annual Meeting held in Los Angeles, 33 .05 12.5 .40 17.50 3.5 - .31 - - 44.30 California, during April 14-18, 1980. 40 .03 9.0 .60 20.50 6.7 — .30 - - 46.40 50 .04 5.0 .40 21.25 12 2 2.2 .27 .15 .15 49.95 R. H. ESPY, now retired, was with Armco Inc., 60 .07 8.0 4.00 16.50 8.2 - .14 - - 39.00 Middletown, Ohio, at the time of the paper's AISI 304 .06 1.4 .50 18.25 9.0 - .04 - - 30.65 presentation at the A WS 61st Annual Meet­ ing. (a) (30 X ",C) + -Mn + ,Cr + "„Ni + '..Mo + (30 X °„N) = Austenite stability (actor WELDING RESEARCH SUPPLEMENT 1149-s 3 the effect of increasing both ultimate Table 2—Mechanical Properties' * of Alloys 33, 40, 50 and 60 at Room Temperature tensile strengths and yield strengths. The higher ultimate tensile strength of Type 0.2"„YS, CVN, 304 at extremely low temperatures is Alloy ksi (MPa) ksi (MPa) ft-lb (i) related to the transformation from the 33 110(758) 60 (414) 55 70 230(313) room temperature austenite to martens­ 40 110(690) 57 (393) 53 75 205 (279) ite. Note that the yield strength for Type 50 120(827) 60 (414) 50 70 170(231) 304 is not significantly increased. 60 103 (710) 60 (414) 64 74 > 240 (> 326) AISI 304 86 (593) 40 (276) 60 70 185 (252) (a) UTS-ultimate tensile strength; YS-yield strength; El-elongation in 2 in. (50.8 mm); RA - reduction in area; CVN-Charpy Work Hardening V-notch. The work hardening phenomena asso­ ciated with austenitic stainless steels is that of austenite transformation to mar­ Table 3—Mechanical Properties'3' of Alloys 33, 40, 50 and 60 at -320F (-196 X) tensite (a hard magnetic phase). The degree of transformation with any given UTS, 0.2"„YS, CVN, amount of cold work is related to the Alloy ksi (MPa) ksi (MPa) El, % \, % ft-lb (I) inherent austenite stability of the alloy and the temperature at which the defor­ 33 216 (1,489) 155 (1,069) 20 20 48 (65) 40 203 (1,400) 150 (1,034) 24 65 (88) mation takes place. 50 226 (1,558) 128 (883) 41 51 50 (68) A very interesting phenomena associ­ 60 213 (1,469) 109 (752) 60 67 144 (196) ated with nitrogen strengthened alloys is AISI 304 215 (1,482) 47 (324) - 110(150) that two kinds of hardening may take place. One hardening mechanism occurs (a) UTS-ultimate tensile strength; YS —yield strength; El - elongation in 2 in. (50.8 mm); RA-reduction in area; CVN —Charpy V-notch. with the normal transformation of aus­ tenite to martensite, and the second hardening results from the formation of epsilon phase in the cold work austen­ Table 4—Mechanical Properties of Alloys 33 40, 50 and 60 at 1000 F (538 C) ite. All four stainless steels (i.e., alloys 33, UTS, 0.2°„YS, 40, 50 and 60) considered here are very Alloy ksi (MPa) ksi (MPa) EL, % RA, % stable and do not transform to martensite on cold deformation. However, they still 33 74 (510) 32 (221) 47 76 work harden as shown in Table 5, most 40 71 (490) 30 (207) 35 - 50 89 (614) 48(331) 36 62 probably by the formation of epsilon 60 74 (510) 28 (193) 51 73 phase. The work hardening rate appears AISI 304 56 (386) 22 (152) 44 34 to be about the same as is experienced with Type 304, an alloy that hardens (a) UTS-ultimate tensile strength; YS —yield strength; El-elongation in 2 in. (50,8 mm); RA —reduction in area; CVN —Charpy principally by austenite transformation to V-notch. martensite. Compared to Type 304, one big difference is that the four alloys can be mechanically cold formed into com­ Table 5—Effect of Cold Work on Alloys 33, 40, 50 and 60<a> ponents and retain their non-magnetic property normally associated with all of 60°o reduction the austenitic stainless steels when in the annealed condition. UTS, 0.2% YS, Magnetic Alloy ksi (MPa) ksi (MPa) El, % Hardness permeability 33 222 (1,531) 199 (1,372) 5 Rc45 1.001 40 202 (1,393) 182 (1,255) 6 Rc40 1.02 Wear and Galling 50 234 (1,613) 216 (1,489) 9 - 1.004 60 240 (1,655) 195 (1,344) 12 Rc43 1.05 In looking at wear and galling charac­ AISI 304 187 (1,289) 174 (1,200) 5 Rc38 ss4 teristics, three types of wear are often considered: (a) UTS-ultimate tensile strength; YS-yield strength; El - elongation in 2 in. (50.8 mm); RA-reduction in area; CVN —Charpy 1. Particle to metal wear such as in V-notch. handling ores. 2. Metal to metal wear such as in gears. Table 6—Wear and Galling Properties of Alloys 33, 40, 50 and 60 3. Metal to metal galling such as in bolting. Metal to Metal to Metal to Metal In the first type of wear, alloys that particle wear'3' metal wear,'b' galling'c' occurs tend to work harden on deformation (lower index no. mg loss/ at load of indicated wear well under the peening action of Alloy shows less wear) 1000 cycles ksi (MPa) rock and ore particles. In the second and third wear applications, alloys that tend 33 .76 7.39 30 (207) to work harden and exhibit a surface 40 8.94 8(55) phenomena or have a high hardness and 50 1.04 9.95 2(14) 60 .76 2.79 50+ (345+) exhibit a surface phenomena will resist AISI 304 1.0 12.77 2(14) wear and galling under sliding loads.
Details
-
File Typepdf
-
Upload Time-
-
Content LanguagesEnglish
-
Upload UserAnonymous/Not logged-in
-
File Pages8 Page
-
File Size-