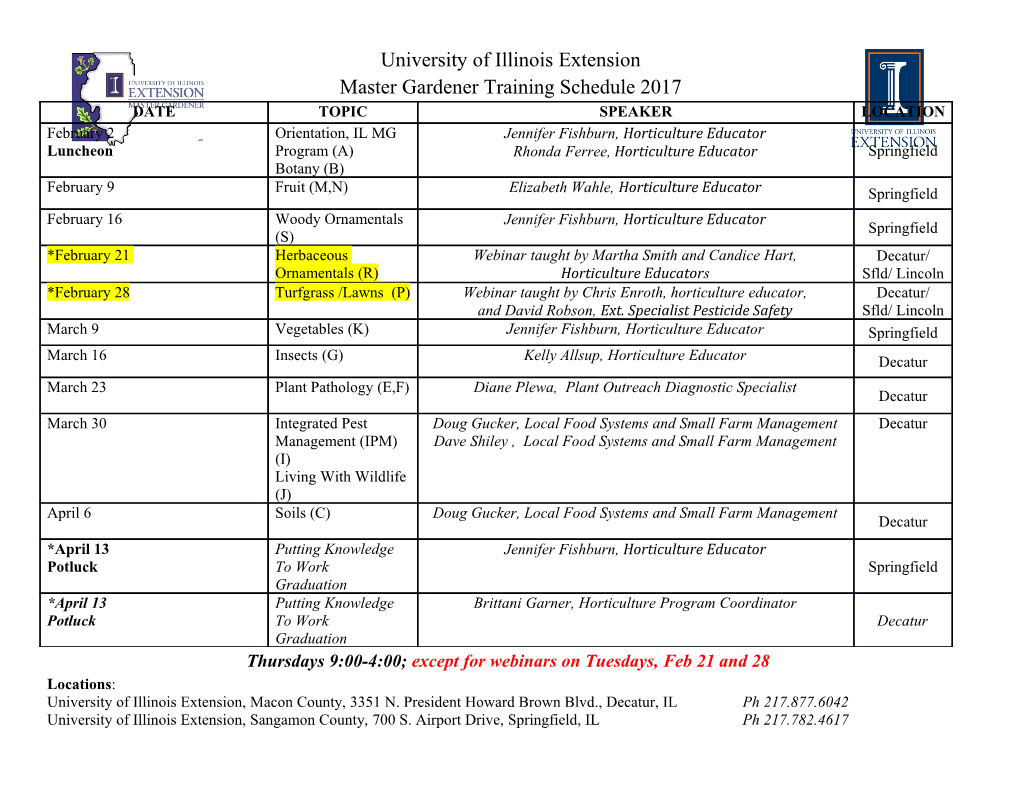
Imperial Journal of Interdisciplinary Research (IJIR) Vol-3, Issue-1, 2017 ISSN: 2454-1362, http://www.onlinejournal.in Performance and Analysis on Valveless Pulse Jet Engine U. Sreekanth1, B. Subba Rao2, & Dr A.Nagaraju3 1Assistant Professor, Department of Mechanical Engineering, Geethanjali College of Engineering and technology, Hyderabad, India. 2Associate Professor, Department of Mechanical Engineering, Geethanjali College of Engineering and technology,, Hyderabad, India. 3Mechanical Engineering Department, Jawaharlal Nehru Technological University, Anantapur, A.P. India. Abstract: The pulsejet has recently received more of the engine and the possible aerospace research interests due to its simple design, which applications provided the necessary motivation for can be developed into low-cost micro-scale further investigation. This project aimed to develop propulsion devices for use in many of today’s new a valve less pulsejet engine with optimal applications such as UAVs. However, the relatively dimensions to give desired thrust. 2 low thermal efficiency of pulsejets has always been To gain an understanding of the pulsejet engine the major obstacle in their development. The goal and to gain statistical data for the design stage a of this research is to investigate the possibility of review of current literature on pulsejets was using pulsejets in certain applications where the conducted. This section outlines the mechanisms of pulsejet can trade its low efficiency with low cost, pulsejet operation with a comparison to other simple design, and light weight aerospace propulsion devices. This work investigates pulsejet operation in a numerical approach, although the focus here is 3. Valve Pulsejets on the computational research. The fluid A valve pulsejet consists of four mechanics and acoustics are studied numerically to components; intake chamber, combustion chamber, understand the physics behind pulsejets and their exhausts runner and a mechanical valve. Figure-1 operations. The objectives include valve less illustrates the layout of a typical valve pulsejet pulsejets, improved model design for valve less design. pulsejets, obtaining preliminary thrust performance data on model pulsejets, and finally, the effect of intake and exhaust lengths on pulsejet thrust 1. Keywords: Pulsejet, Thermal efficiency, Thrust, Exhaust temperature, Pressure 2. INTRODUCTION A pulsejet engine is essentially a hollow tube that Fig.1 Layout of Argus 014 (Luft46 2007) utilizes sound waves to induce fluid flow and A valve pulsejet works on the principal of produce thrust. Pulsejet engines have few moving wave rarefaction and the Cadency effect. Air is parts making them economical to construct and introduced into the engine through the intake maintain. This advantage makes them ideal for use where it is mixed with the fuel that is introduced in Unmanned Aerial Vehicles (UAVs), however, through an injector. This air/fuel mixture is then development within recent years has been confined transferred through a mechanically operated valve to industrial projects and enthusiasts. The pulsejet into the combustion chamber. In the combustion engine was first invented in 1891 and relied on the chamber the air/fuel mixture is ignited and expands vaporization of water. Later designs were air rapidly. As the gas expands it produces a sharp breathing and extensive research was conducted up pressure increase within the engine that causes until 1960 when it was concluded the design would gases to exit the exhaust runner to create thrust. As not offer a feasible alternative to the developing this happens, a partial vacuum is generated behind turbine jet engines. After 1984, most interest was the exiting mass due to the Cadency effect, which lost and interest was predominately from is discussed in more detail later. This partial enthusiasts due to the limited costs. The simplicity vacuum uses air pressure differential to open the Imperial Journal of Interdisciplinary Research (IJIR) Page 34 Imperial Journal of Interdisciplinary Research (IJIR) Vol-3, Issue-1, 2017 ISSN: 2454-1362, http://www.onlinejournal.in valve to allow in the fresh air/fuel charge. While this is occurring, the pressure wave in the exhaust has reached the end of the pipe and reflected to create a rarefaction wave that forces the flame front to recede back towards the combustion chamber. Due to the Cadency effect, the movement of the air back towards the combustion chamber creates a partial vacuum behind the flame front, pulling in cooler, denser air. This cool dense air also acts as Fig.2 Principal of a valve less pulsejet an aerodynamic barrier to help contain the next combustion event, thus increasing combustion chamber pressure. The receding flame front reaches When the deflagration begins, a zone of the combustion chamber and ignites the new significantly elevated pressure travels outward air/fuel mixture repeating the process. The through both air masses as a “compression wave” frequency of the pulsations is dependent on the This wave moves at the speed of sound through geometry of the engine but is commonly of the both the intake and tailpipe air masses. (Because order of 50-200Hz these air masses are significantly elevated in 4. Valve less Pulsejets temperature as a result of earlier cycles, the speed of sound in them is much higher than it would be in The principal of valveless pulsejets is much normal outdoor air.) When a compression wave the same as for the valved case but with the air in reaches the open end of either tube, a low the intake and exhaust pipes acting as the valves to pressure rarefaction wave starts back in the help contain combustion and increase combustion opposite direction, as if "reflected" by the open chamber pressure. Figure-2 illustrates a sustained end. This low pressure region returning to the pulse cycle from start-up through two complete combustion zone is, in fact, the internal mechanism cycles. of the Kadenacy effect, there will be no "breathing" of fresh air into the combustion zone until the The "valve less" pulsejet is not really valve less. It arrival of the rarefaction wave. just uses the mass of air in the intake tube as its valve, in place of a mechanical valve. It cannot do this without moving the intake air outward, and this 5. THEORETICAL MODELLING OF volume of air itself has significant mass, just as the PULSE JET air in the tailpipe does. Therefore, it is not blown Theoretical models allow experiments to away instantly by the deflagration but is be conducted without the need for physically accelerated over a significant fraction of the cycle building a test rig, thus reducing cost and time. In all known successful valveless pulsejet development time. Pulse jets have an intricate designs, the intake air mass is a small fraction of pulsating combustion system, making them very the tailpipe air mass (due to the smaller dimensions difficult to model. Computer simulations allow the of the intake duct). This means that the intake air flow to be analyzed and engine dimensions varied mass will be cleared out of contact with the body of to optimize performance. The aim of the computer the engine faster than the tailpipe mass will. The model developed as part of this project was carefully designed imbalance of these two air 1 To provide understanding of how the masses is important for the proper timing of all internal processes occur. parts of the cycle. 2 To predict the performance of the experimental and prototype pulsejet. From Figure-2, the cycle starts with the 3 To develop a toolbox for designing initial air/fuel mixture in the combustion chamber pulsejets. being ignited by a spark or similar combustion Understanding the complexity of the initiator. Air is required to initiate combustion and pulsejet cycle was the major hurdle in developing a to promote the pulsating combustion. The initial computer model. Simple iterative techniques expansion of combustion chamber gas caused by handled fluid properties such as pressure, combustion moves out of both intake and exhaust temperature and velocity; however, were unable to runners, with the pressure waves generated by the handle compression or rarefaction waves. The combustion rare acted at both ends. The intake model accounted for gradual area changes, wall runner is shorter than the exhaust so the intake friction, heat transfer, entropy gradient sand wave is reflected first, drawing in the new charge boundary conditions. of air that is mixed with the fuel 6. Initial Conceptual Design The initial choice of the design configuration was facilitated using a combination Imperial Journal of Interdisciplinary Research (IJIR) Page 35 Imperial Journal of Interdisciplinary Research (IJIR) Vol-3, Issue-1, 2017 ISSN: 2454-1362, http://www.onlinejournal.in of group discussions. The final choice was to 9. Pressure develop a linear engine design similar to an The pressure plays a main role for successful existing amateur design, the Advanced Focused operation of Pulse jet engine. The design model of Wave Engine (FWE), which can be seen in Figure pulse jets produced desired amounts of pressures 5-1.The main factors that drove the choice of this about 9.4 Pa design were ease of manufacture, experimental adaptability and small unit size. The FWE concept required only one cone element, as opposed to a greater number of cone elements in a u-shaped design. Neglecting the combustion chamber end cap, the remainder of the elements used in construction of the engine were pipe elements. In relation to this, the FWE provided the ability for experimental adaptation. The Lockwood-Hiller design uses predominantly conical elements; hence the only element that could be readily interchanged during experimentation would be the U-section of constant area Fig.4 Velocity graph of Analyzed Focused Wave Engine Fig. 3 Experimental focused wave engine design Piping that allows the exhaust and intake to be placed parallel, this only provides adjustability of the exhaust length. In contrast, the FWE design would allow a number of exhaust and intake lengths to be fabricated for interchanging, providing a greater scope for experimental investigation and design optimization.
Details
-
File Typepdf
-
Upload Time-
-
Content LanguagesEnglish
-
Upload UserAnonymous/Not logged-in
-
File Pages5 Page
-
File Size-