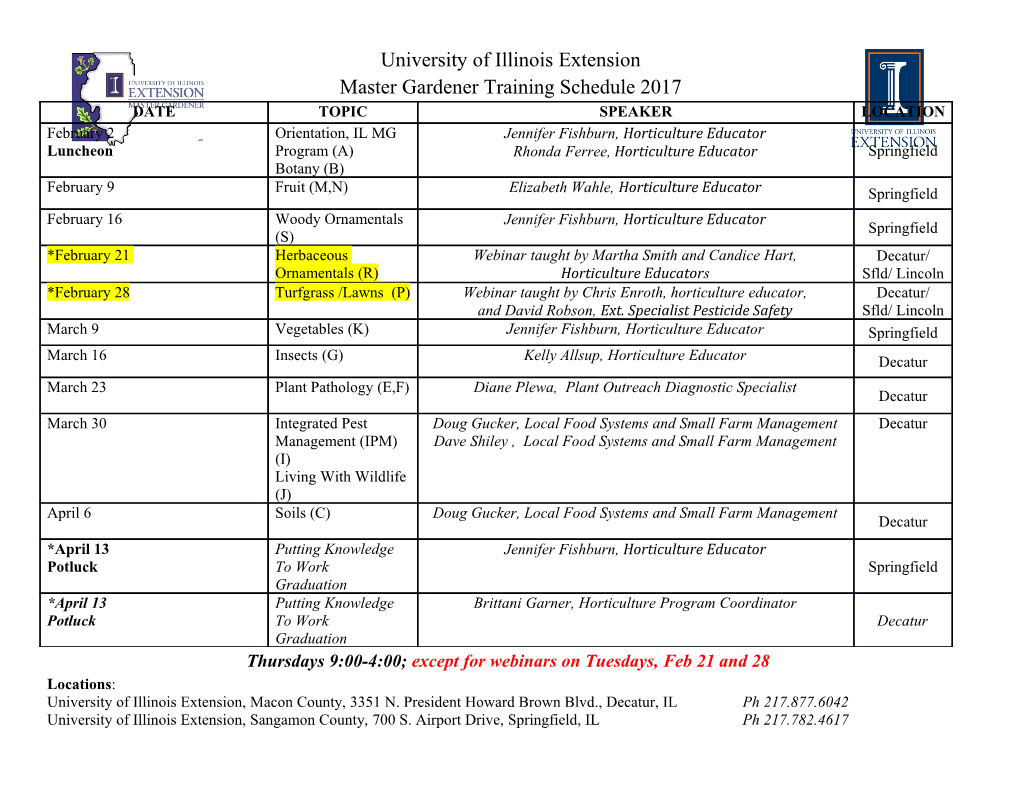
International Journal of Engineering & Technology IJET-IJENS Vol: 11 No: 04 30 Effect of Polystyrene-Modified Natural Rubber as High Molecular Weight Modifier in Polypropylene Based Binary Blends Ong S.K. and Azanam S. Hashim Abstract— Laboratory synthesized polystyrene-modified can improve PP/NR blend performance since it resulted in natural rubber (SNR) was used in polypropylene (PP) based as finely dispersed micron-sized vulcanized rubber in its modifier. PP volume was reduced while natural rubber (NR) and thermoplastic matrix [21-22]. For the applications in TPE, SNR volume were increased. The range of ratios evaluated are sulfur vulcanization system is known to give the best 70/30; 55/45, 50/50 and 45/55 by volume. PP/SNR blends resulted in better tensile properties, flexural properties, impact strength, elastomeric properties and more suitable for thermoplastic elastic energy and reprocessing retention properties but similar natural rubber (TPNR) [12]. The sulfur vulcanization system tear strength in comparison with PP/NR blends at the similar known as dynamic vulcanization was introduced by Gessler blend ratios. Those mechanical properties are in agreement with and Haslett [23] in 1962 and later developed by Fisher [24], morphological analysis. In comparing PP based blends in this Coran and Patel [25], Coran et al. [26, Abdou-Sabet and Fath study with relevant thermoplastic elastomer (TPE), results [5] and Ousa et al. [27]. In the mentioned studies curatives showed that PP/NR: 70/30 and PP/SNR: 70/30 blends have better tensile properties compare to polyolefins/ NR. While in were added in-situ during melt mixing. This method is thought comparison with Santoprene®, those blends are at the higher end to be less effective as curatives will dispersed in both of Santoprene® tensile strength and modulus 100 and lower end thermoplastic and rubber phases. This study will use the of Santoprene® elongation at break. modified dynamic vulcanization method. In this study, polystyrene-modified natural rubber (SNR) Index Term— natural rubber. polypropylene, polystyrene- was investigated as modifier in PP based blends. SNR modified natural rubber, thermoplastic elastomer prepared in the laboratory by in-situ polymerization of styrene in deprotienized natural rubber latex (DPNR) contains I. INTRODUCTION approximately 25% polystyrene (PS) and 75% NR by weight. POLYMER blends consist of two or more polymers. The PP based blends investigated will focus on the application Properties of a blend depend mainly on the matrix phase but of SNR as modifier in PP based blends on the tensile factor like amount, size, shape and interfacial adhesion of the properties, flexural properties, impact strength, tear strength dispersed phase also play a role. Basis thermodynamics, and retention properties. Selected blend ratios was compared Flory-Hüggins theory and equation-of-state theories are used with relevant TPE. to explain polymer blends behavior [1]–[4] Many studies on PP/rubber blends have been carried out. II. MATERIALS AND METHODS Some of the rubbers studied are Ethylene Propylene Diene Monomer (EPDM) rubber [9], nitrile rubber as oil resistant A. Materials TPE [6], [7], [9] and butyl rubber in low air and moisture The PP used is grade Titanpro 6431 purchased from Titan permeability TPE [10]. PP Polymers (Malaysia), with density and melt flow index 0.9 Studies on polypropylene/natural rubber (PP/NR) blends gcm-3 and 12 g/10min respectively. The NR used is SMRL have also been carried out and mainly focusing on its grade. application as thermoplastic elastomer (TPE) and toughened The following materials are used in SNR synthesized: blend for low temperature applications [11]-[20]. For the styrene as monomer (Aldrich Chemical Company), interest of impact properties, maximum rubber content is in ammonium persulphate (N2H8O8S2) as initiator (Fluka the range of 20–25% [18]. Chemical Company), and DPNR latex supplied by Sumitomo Rubber Industries (Malaysia) Studies have showed that cross-linking of the rubber phase B. Preparation and Characterization of SNR Ong S. K. is with Universiti Kuala Lumpur, Malaysian Institute of SNR was synthesized by in-situ polymerization of styrene Chemical and Bioengineering Technology, Section of Polymer Engineering in DPNR latex and characterized according to procedures Technology, Vendor City 78000 Taboh Naning, Alor Gajah, Melaka, previously reported [13], [29]. Styrene monomer was purified Malaysia (e-mail: [email protected]). Azanam S. Hashim is with Universiti Kuala Lumpur, Malaysian Institute using inhibitor remover-packed column before it was of Chemical and Bioengineering Technology, Section of Polymer Engineering polymerized. In-situ polymerization of styrene in DPNR latex Technology, Vendor City 78000 Taboh Naning, Alor Gajah, Melaka, was carried out at 60oC for 5 hours at styrene: dry rubber Malaysia (e-mail: [email protected]). 113204-9595 IJET-IJENS @ August 2011 IJENS I J E N S International Journal of Engineering & Technology IJET-IJENS Vol: 11 No: 04 31 ration of 25:75 by weight. Upon completion of the reaction presented in Fig. 1 showed that both blend have similar shape time, the rubber was dried at room temperature to obtain gum and PP/SNR: 70/30 blend was shifted up compare to PP/NR: SNR. 70/30 blend. As mentioned, SNR contains about 25% PS Methanol was used to determine the degree of conversion of which are grafted onto the NR backbone. The grafted PS the resultant SNR (styrene to PS). Tetrahydrofuran, petroleum contributed to the stiffness and strength of PP/SNR blend. ether and ethyl acetate were used in sol-gel analysis for the Looking at the total volume of thermoplastic/rubber ratio determination of degree of grafted PS on NR. Gum SNR cure between PP/NR: 70/30 blend and PP/SNR: 70/30 blend, the characteristic and tensile properties were evaluated prior to latter blend is having higher amount of thermoplastic; i.e. PP melt mixing. and PS from SNR. At lower rubber amount, the blend is expected to be stiffer and stronger. This is in agreement with the results observed; i.e. PP/SNR: 70/30 blend is stiffer and C. Melt Mixing of PP Based Blends stronger than PP/NR blend. Melt mixing was carried out using Brabender Plasticoder o The morphology analysis is shown in Fig. 2. It is obvious Model PLE 331 at 180 C and rotor speed 50 rpm [9]. All that from Fig. 2 PP/SNR: 70/30 blend has better homogeneity blends ratios are based on volume and blend using the method. compare to PP/NR: 70/30 blend. The results obtained from First PP was preheated in the mixing chamber for 3 minutes morphology analysis is in good agreement with the tensile followed by another 3 minutes for melt mixing at 50rpm, and properties where both showed that PP/SNR: 70/30 blend that then either NR of SNR was charged-in at 3rd minute. Mixing th exhibit better homogeneity also contributed to better tensile stopped at 8 minute. Both NR and SNR were masticated and properties as compare to PP/NR: 70/30 blend. compounded separately in two-roll mill using an efficient vulcanization (EV) system as shown in Table 1. Mastication and compounding for both NR and SNR were carried out prior B. Others Mechanical Properties to melt mixing. Table 3 shows the tear strength, elastic energy per unit deflection, flexural properties and impact strength for PP/NR: 70/30 blend and PP/SNR: 70/30 blend. Results showed that D. Measurements the tear strength for PP/NR and PP/SNR blends are The final blends were molded using compression molding 2 o comparable. From study by Nguyen Van Tho [29], it showed machine KAO Tech with 100 kg/cm force at 170 C. Tensile that SNR has lower tear strength as compare to NR as the test and tear test were carried out at room temperature allylic sites was grafted with PS. However due to higher according to ASTM D638 and ISO 43 type 3 respectively degree of compatibility of PP/SNR blend compare to PP/NR using Tensometer M 500 type with cross head speed of 50 blend; i.e. showed by the morphology analysis; the tear mm/min. A nip of 0.5 mm for tear test specimens was made at strength of both binary blends are comparable. the centre of the crescent. Three-point bending flexural test In the classical beam theory on the unnotched specimen, was carried out according to ASTM D790 using Tensometer elastic energy at critical stage, Uc is given by equation (1) [30] M 500 type with cross head speed of 5 mm/min at room temperature. Impact test was carried out using Zwick Impact 2 o Tester according to ASTM D256 at -27 C. Blends morphology c U BSW (1) were analyzed using SEM model Leice Cambridge S–360. c 18E f Reprocessing retention properties were carried out by reprocess the blends using the similar melt mixing method as mentioned above. Tensile properties for the reprocess blends where Uc is the elastic energy at critical stage (J); c is the were evaluated and percentage of retention properties was critical stress in a three point bending system (MPa); Ef is the reported. flexural modulus (GPa); B is the sample depth (mm); S is the beam span (mm) and W is the sample width. The elastic III. RESULTS AND DISCUSSION energy can be reported as elastic energy per unit deflection, Uy by normalized the sample deflected dimension. Uy represent A. Tensile Properties the inherent property of a material and theoretically correlate Tensile properties of PP/NR blends and PP/SNR blends are well with its mechanical properties such as flexural properties summarized in Table 2. Tensile properties decrease with the and impact strength. This means that at higher Uy, higher increase of rubber loading from 30% to 55% except for PP/NR flexural strength, flexural modulus and impact strength is blends where no significant change for modulus at 100% expected.
Details
-
File Typepdf
-
Upload Time-
-
Content LanguagesEnglish
-
Upload UserAnonymous/Not logged-in
-
File Pages8 Page
-
File Size-