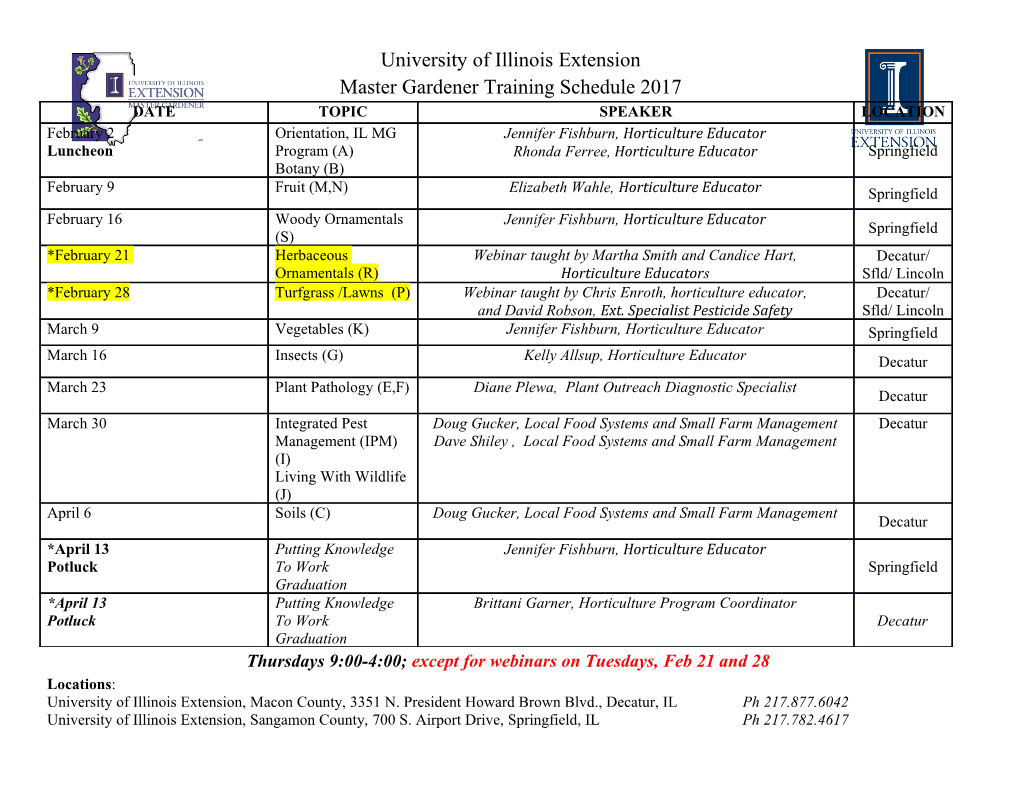
Monolithic Piezoelectric Insect with Resonance Walking Shannon A. Rios1, Andrew J. Fleming2 and Yuen Kuan Yong3 was able to achieve a forward travel speed of 0.9 body lengths per second [7]. This robot was approximately 4.8 cm long and consisted of three leg pairs where each pair of legs were driven by three piezoelectric benders arranged to amplify the displacement and produce a tripod gait. Another example of a miniature piezoelectric robot is high- lighted in the works of Oldham et al.. This work focused on the modeling, control and manufacture of multi-degree-of-freedom microrobotic legs that utilize thin-film PZT actuators [8], [9]. It is estimated that a robot using this form of actuator would achieve a forward locomotion speed of 27 mm/s. Additional work has characterized the effect of dynamic contact iterations on micro- robotic leg structures [10]. Nguyen et al. have produced a tethered meso-scaled hexapod robot driven by ‘soft’ dielectric elastomer actuators [11]. The elastomer’s were segregated into four separate actuators able to produce three DoFs per leg. The constructed robot weighed Fig. 1. MinRAR V2. approximately 80 g and was able to achieve a forward locomotion speed of 4 mm/s when driven with a 3.5 kV square wave at 0.5 Hz. Abstract—This article describes the design, manufacture and per- An example of a novel approach to miniature robotic locomo- formance of an untethered hexapod robot titled MinRAR V2. This tion can be seen in the works of Hariri et al. [12]–[14]. These works robot utilizes a monolithic piezoelectric element, machined to allow outline the design and development of a meso-scaled robot driven for individual activation of bending actuators. The legs were designed by a traveling wave in an aluminum beam. The traveling wave is so that the first two resonance modes overlap and therefore produce excited by one or two piezoelectric patches at either end of an a walking motion at resonance. The monolithic construction signifi- cantly improves the matching of resonance modes between legs when aluminum beam and the speed of the robot can be controlled by compared to previous designs. Miniature control and high voltage varying the amplitude of the voltage. Another robot developed by driving electronics were designed to drive 24 separate piezoelectric Hariri et al. uses a similar method to excite a standing wave on elements powered from a single 3.7 V lithium polymer battery. The a legged robot [15]. These robots are able to achieve a forward robot was driven both tethered and untethered and was able to achieve a maximum forward velocity of 98 mm/s when driven at 190 Hz and locomotion speed of 246.5 mm/s and 40 mm/s respectively. 6 mm/s at 5 Hz untethered. The robot is capable of a wide range of The work of Lee et al. shows a more extreme simplification movements including banking, on the spot turning and reverse motion. of actuators and control [16]. Their work outlines a tethered miniature inchworm style robot that is driven by a single elec- tromagnetic actuator. This robot can produce forward locomotion I. INTRODUCTION speeds of up to 36 mm/s and measures 12.2 mm x 11 mm x 9 mm in size and has a mass of 2.86 g. Autonomous walking robots are complex machines comprised The use of resonant vibration in miniature robotics was also of many sensors, actuators and control electronics. Due to the reported by Becker et al. in their work on piezo-driven micro complexity, significant challenges are involved with miniaturiza- robots [17]. Their work outlines the development of a range of tion. Construction methods and mechanics that work well in robots capable of traveling over both land and water. These robots macro-scale robots may not be suitable for miniaturization due to used forced vibration to achieve two axis locomotion utilizing a the dominance of surface forces including friction [1]. By replacing single piezoelectric actuator. standard mechanical components such as motors, bearings and As well as walking robots, piezoelectric actuators have also been other sliding joints with flexures and piezoelectric actuators, this applied to flying [18] and even swimming robots [19]. The work problem can be mitigated. of L. Cen and A. Erturk describes a fish like autonomous robot There has been a wide variety of miniature robots developed that uses a macro-fiber composite, flexible piezoelectric actuator over the past decade. For example, Wood et al. developed several for propulsion. This robot was able to achieve an untethered miniature robots utilizing piezoelectric bender actuators for loco- swimming speed of up to 7.3 cm/s when driven with a 5 Hz motion [2]–[6]. One such example is a 1.7 g hexapod robot that actuation signal [19]. The Authors are with the Precision Mechatronics Laboratory, School Similar principles that are applied to miniature robot actuators of Electrical Engineering and Computer Science at the University of are also applied to a wide range of other piezoelectric actuators Newcastle, Callaghan, NSW 2308, AUSTRALIA such as micro-grippers [20] and transducers [21]–[24] The works of 1 [email protected] Fujun Wang et al. describe the design and control of a piezoelectric [email protected] micro-gripper that uses a three-stage flexure-based amplification [email protected] technique to achieve a large amplification factor of up to 22.6 [25]. This work was performed in part at the University of Adelaide OptoFab node of the Australian National Fabrication Facility utilizing Common- This article describes the design, manufacture and performance wealth and It. SA State Government funding. of a monolithic miniature hexapod robot named MinRAR V2 and Fig. 3. Leg diagram. Main Main Inv Fig. 2. Monolithic chassis. All dimensions given in mm. Left Right Inv Left Inv Right shown in Figure 1. This work builds on previous research into A A the use of piezoelectric actuators in miniature robots described 1 1 in [26]–[28] by improving the monolithic chassis construction B B techniques, refining the resonant leg design and by miniaturizing A A the control electronics to allow for un-tethered operation. The Left 2 2 Right following section outlines the configuration of the robot and the B B mechanical modeling is discussed. Subsequently the electrical A A design and control methodology is described. Lastly the exper- 3 3 imental results are discussed and the article is concluded with a B B comparison to existing miniature robots. Fig. 4. Actuator wiring diagram. II. CONFIGURATION The MinRAR V2 is a monolithic hexapod robot that uses a piezo- electric bimorph body and aluminum end-effectors to produce motion. The geometry of the body, shown in Figure 2, is similar to difference is referred to as the ‘step-phase’ and a wide range of the previous monolithic robot described in [27] and is comprised motions can be achieved by changing this, for example, when the of six legs that are driven with a tripod style gait to produce an two benders are driven in phase (0 step-phase), a lifting motion ambulatory motion. The body was milled from a single sheet of ± of the leg will be produced, similarly, when driven out of phase 0.4 mm PZT-5A series poled bimorph supplied from Piezo Systems (step-phase of 180 ) a swinging motion is produced. Nominally, Inc. using an ultrasonic milling machine. ± a step-phase of 90 is used for walking as this produces equal Differing from the MinRAR V1, the V2 is designed to be com- ± proportions of lifting and swinging. Any step-phase between these pletely un-tethered and includes all control and power electronics two extremes will produce a combination of lifting and swinging. as well as a small lithium polymer battery. Additionally, the When the legs are driven with a step phase greater than 180 or monolithic chassis of the V2 lacks a central brass shim and the ± less than 0 the motion will be reversed, in this way the robot can nickel electrodes were machined instead of etched. Removing the ± be made to walk backward or turn on the spot. brass shim from the piezo elements improves the reliability of the machining process and by milling the electrodes during this ma- The actuators are controlled using the dual bipolar series elec- chining process instead of etching them after simplifies the overall trical configuration, which drives the top and bottom piezoelectric construction process. Also issues with resistive uniformity were electrodes 180± out of phase with each other and was chosen so removed when switching to milled instead of etched electrodes. that the central electrode, which is common between all actuators, Each leg is comprised of two piezoelectric bimorph actuators can be grounded [29]. Using this method a total of six control mounted side-by-side and joined at their tips by a flexure and signals are required to drive MinRAR V2, three primary drive end-effector as per Figure 3. Motion can be achieved when the signals (Main, Right and Left) and three inverse drive signals (Main two benders are driven independently with a sinusoidal waveform Inv, Right Inv and Left Inv). Figure 4 shows the connection diagram and the phase difference between these drive signals determines for the top layer of the miniature robot and for the bottom layer, the proportions of lifting and swinging that occur. This phase the signals are phase shifted by 180±. TABLE I TABLEOF STIFFNESS AND INERTIA Stiffness JFx 0.1056 Nm JFz 0.0667 Nm JPx 0.0977 Nm JPz 0.2326 Nm Ky 6.0695 kN/m Inertia 8 2 IPx 1.7039x10¡ kg.m 9 2 IPz 1.5398x10¡ kg.m 9 2 IL 6.4065x10¡ kg.m Fig.
Details
-
File Typepdf
-
Upload Time-
-
Content LanguagesEnglish
-
Upload UserAnonymous/Not logged-in
-
File Pages7 Page
-
File Size-