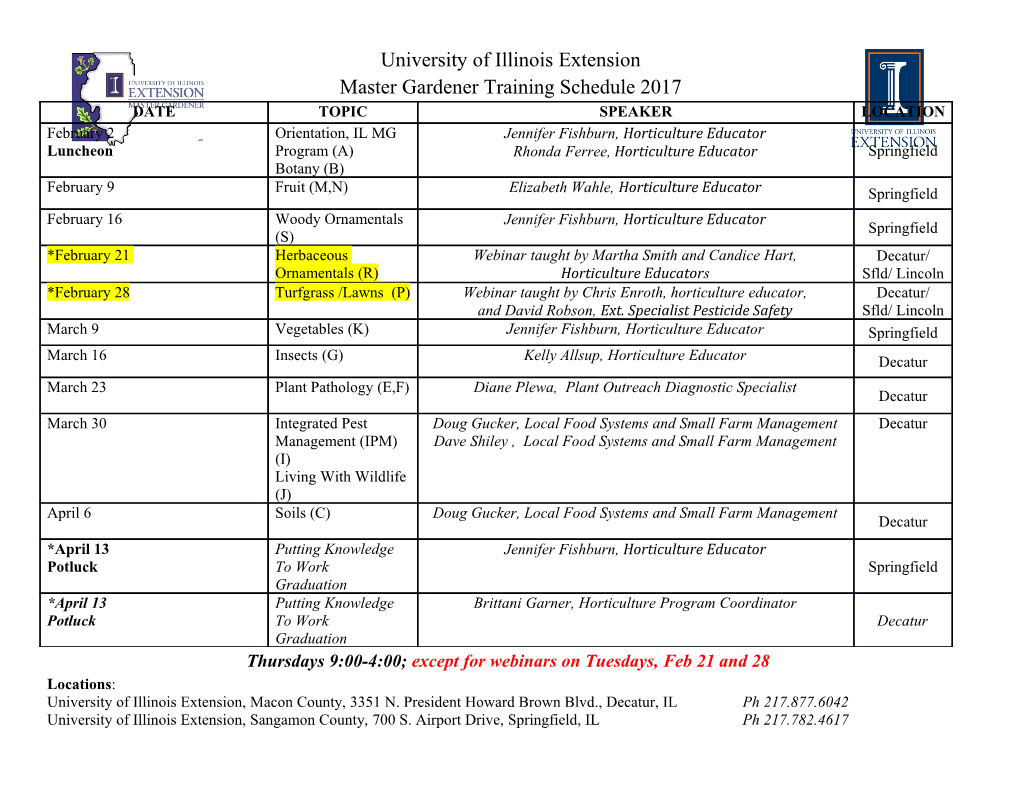
Analysis of the transversely isotropy, due to the production process, of carbon black filled SBR Gianfilippo Dottore Department of Civil Engineering and Architecture University of Catania (Italy) email: gianfi[email protected] Abstract—Through tensile tests of uniaxial and planar type, Transversely isotropic behavior, caused by the rubber cal- was proceeded to the mechanical characterization of SBR rubber endering process [20], has made more difficult the analysis. sheets filled with particles of carbon black. The analysis has The phenomenon is well known in the literature, so that were allowed defining the elastic features, the storage modulus, the transversal contraction coefficient (both obtained from uniaxial already made attempts to characterize elastomers which have testing) and the shear modulus (from the planar/pure shear transverse isotropy [21], [22], [23]. tests). Due to the calendering process by which was obtained, the Therefore, tests were performed at different loading di- elastomer sheet it’s shown transversely isotropic, with different rections, in order to assess the behavioral differences of the mechanical behavior in the direction of processing with respect to material between the direction of calendering and the direction the transverse direction. Therefore, it was essential to evaluate two different values for each storage modulus, depending that orthogonal to it. the sample was loaded in the direction of calendering or in that orthogonal to it. II. CONSTITUTIVE EQUATIONS Index Terms—Transversal Isotropy, Hyperelasticity, SBR, Car- Most of engineering materials belongs to the category of bon Black, Calendering. simple materials, for which the stress tensor T is a function of the history of the position gradient F = r x [2]: I. INTRODUCTION The Styrene Butadiene Rubber (SBR) arises from copoly- T (x; t) = T (F (x; τ); x0; t) τ 2 [0; t] (1) merization of Butadiene and Styrene. The latter, present to the extent of 20-25% of the copolymer, increases both strength and Among the simple materials, those elastic exhibit a stress stiffness from SBR with respect to the butadiene rubber (BR) state as a function of the single value of the deformation [1], [2]. Often, it is filled with carbon black, carbon charges gradient: of nanometric particles obtained from the combustion of hydrocarbons, the presence of which improves the mechanical T (x; t) = T (F (x; τ); x0; t) (2) properties and slows the aging. The SBR is the most usage According to this constitutive relationship, stress does not rubber [3], [4], [5], [6], [7], [8], [9], being able to provide depend on the deformation path (Cauchy elasticity), but it mechanical properties similar to those of natural rubber at a is not the same for the deformation work that it performs. lower cost. The elastomer is used mainly where there is a need The hyperelastic materials are, instead, conservative elastic for high-friction surfaces, so that the 70% of the production materials (Green elasticity), i.e. for which, there being an is for tires tread [10], [11], [12], [13]. elastic potential function ' = '(F), which can be derived The mechanical characterization of a material consists in from stress, the differential form of the deformation work is determining the current constitutive law between stress and exact strain [3], [14], [15], [16]. The characterization process is particularly critical for elas- @'t = T (3) tomers, due the large deformations that, for the same elastomer @F I definition [17], [18], can tolerate without reaching the failure. −t The aim of this experimental analysis is reached the where TI := JTF is the first tensor of Piola-Kirchhoff, mechanical characterization of styrene-butadiene rubber, im- with J = det F. proved in its quality by the introduction of fillers of carbon The simple assumption of linear elastic material is correct if black (25%) in the blend [4], [19]. you can overlook the time-dependent effects (such as sliding The analysis developed is focused on tracking of math- and relaxation) [2], [24], [25] and for small deformations. ematical functions, which correlated stress and strain, and Circumstance, the latter, in which it is allowed the stress- on evaluation, starting with these functions, of the storage strain relationship linearization. The linear stress-strain law modules assumed at the beginning of the rubber test. is represented in classic form, tensorial, from equations Tij = P3 4 h;k=1 CijhkEhk, which contain the 3 = 81 constants Cijhk Copyright c 2017 held by the authors. of the elastic tensor di of order 4. Since the stress and strain 7 symmetry of the tensors requires six independent components and of the stress tensor as a function of the six independent 2 1 − vxy − vxy 0 0 0 3 components of the strain tensor, only 36 independent constants Ex Ey Ey vyx 1 vyz are needed to determine the linear elastic relationship. 6− − 0 0 0 7 6 Ex Ey Ey 7 6− vyx − vyz 1 0 0 0 7 −1 6 Ex Ey Ey 7 C = 6 7 6 0 0 0 1=Gxy 0 0 7 2 3 2 3 2 3 2 3 6 7 σx σ(1) "_x "_(1) 4 0 0 0 0 1=Gxy 0 5 2(1+v ) 6 σy 7 6 σ(2) 7 6 "_y 7 6 "_(2) 7 0 0 0 0 0 yz 6 7 6 7 6 7 6 7 Ey 6 σz 7 6 σ(3) 7 6 "_z 7 6 "_(3) 7 σ := 6 7 = 6 7 ; "_ := 6 7 = 6 7 6τxy7 6 σ(4) 7 6γ_ xy7 6 "_(4) 7 where the 6 modules present are defined as follows 6 7 6 7 6 7 6 7 4τxz5 4 σ(5) 5 4γ_ xz5 4 "_(5) 5 τyz σ(6) γ_ yz "_(6) σi Ei = σ(i) 6= 0; σ(k) = 0 8k 6= i "i We can express the linear relationship in a matrix simplified using independent components vectors "j vji = σ(i) 6= 0; σ(k) = 0 8k 6= i "i 2 3 2 3 2 3 τij σx c11 c12 c13 c14 c15 c16 "x G = ij γ 6 σy 7 6c21 c22 c23 c24 c25 c267 6 "y 7 ij 6 7 6 7 6 7 6 σz 7 6c31 c32 c33 c34 c35 c367 6 "z 7 6 7 = 6 7 6 7 The elements on the main diagonal are the modules of 6τxy7 6c41 c42 c43 c44 c45 c467 6γxy7 6 7 6 7 6 7 normal deformability 1=Ei and tangential 1=Gij; those that 4τxz5 4c51 c52 c53 c54 c55 c565 4γxz5 appear outside of the same diagonal such as the modules τyz c61 c62 c63 c64 c65 c66 γyz of transverse deformability −vji=Ei. The symmetry of the previous matrix adds the condition vyx=Ex = vxy=Ey, which The linear elastic relationship is defined by 6 × 6 = 36 reduces to 5 the independent components. In the case of components of the C tensor of order 2 of elastic constants. transversely isotropic material plates, which present the x or Assuming the occurrence of a potential elastic (hyperelastic y axis of transverse symmetry, assuming the status of plane material), according to the Schwartz theorem, the elasticity stress σz = τxz = τyz = 0 and writing separately the tensors are symmetrical and the constants are reduced to 21 equations: [3]. They are called transversely isotropic those materials, which vyx 1 have an isotropic response in the plane orthogonal to an axis, "z = − σx + (σz − vyzσy) Ex Ey said axis of transverse symmetry. By choosing a base having the x-axis parallel to symmetry transverse γxz = 0 2 3 2 3 2 3 γyz = 0 σx c11 c12 c13 0 0 0 "x 6 σy 7 6c12 c22 c23 0 0 0 7 6 "y 7 6 7 6 7 6 7 the constitutive relation can be narrowed to only three 6 σz 7 6c13 c23 c33 0 0 0 7 6 "z 7 6 7 = 6 7 6 7 stress and three strain components in the x and y directions, 6τxy7 6 0 0 0 c44 0 0 7 6γxy7 6 7 6 7 6 7 becoming [27], [3]: 4τxz5 4 0 0 0 0 c44 0 5 4γxz5 c22−c23 τyz 0 0 0 0 0 2 γyz 2 v E 3 2 3 Ex xy x 0 2 3 σx 1−vxy vyx 1−vxy vyx "x In this case, the elastic response is described by 5 indepen- vyxEy Ey 4 σy 5 = 6 0 7 = 4 "y 5 dent parameters [26]. 4 1−vxy vyx 1−vxy vyx 5 τxy γxy The constitutive equation can be formulated in terms of 0 0 Gxy engineering constants [3], inverting the stress-strain relation 2 3 2 1 − vxy 0 3 2 3 "x Ex Ey σx v 2 3 2 3 " = 6 yx 1 0 7 = σ "x σx 4 y 5 Ex Ey 4 y 5 4 1 5 γxy 0 0 τxy 6 "y 7 6 σy 7 Gxy 6 7 6 7 6 "z 7 −1 6 σz 7 6 7 = C 6 7 6γxz7 6τxy7 where there is a symmetry condition vyx=Ex = vxy=Ey, 6 7 6 7 4γxz5 4τxz5 whose effect is that only 4 of the 5 elastic constants appearing γyz τyz in the above matrix are independent. 8 III. PURE SHEAR IN PLANAR TEST A valid constitutive model must properly describe the material behavior for each stress state. A single test as a simple uniaxial tensile test does not allow the construction of a reliable model in every situation. It then requires the programming of tests set that provide different stress mode. The uniaxial tensile test is then flanked by planar tensile and equibiaxial tests [4], [19].
Details
-
File Typepdf
-
Upload Time-
-
Content LanguagesEnglish
-
Upload UserAnonymous/Not logged-in
-
File Pages7 Page
-
File Size-