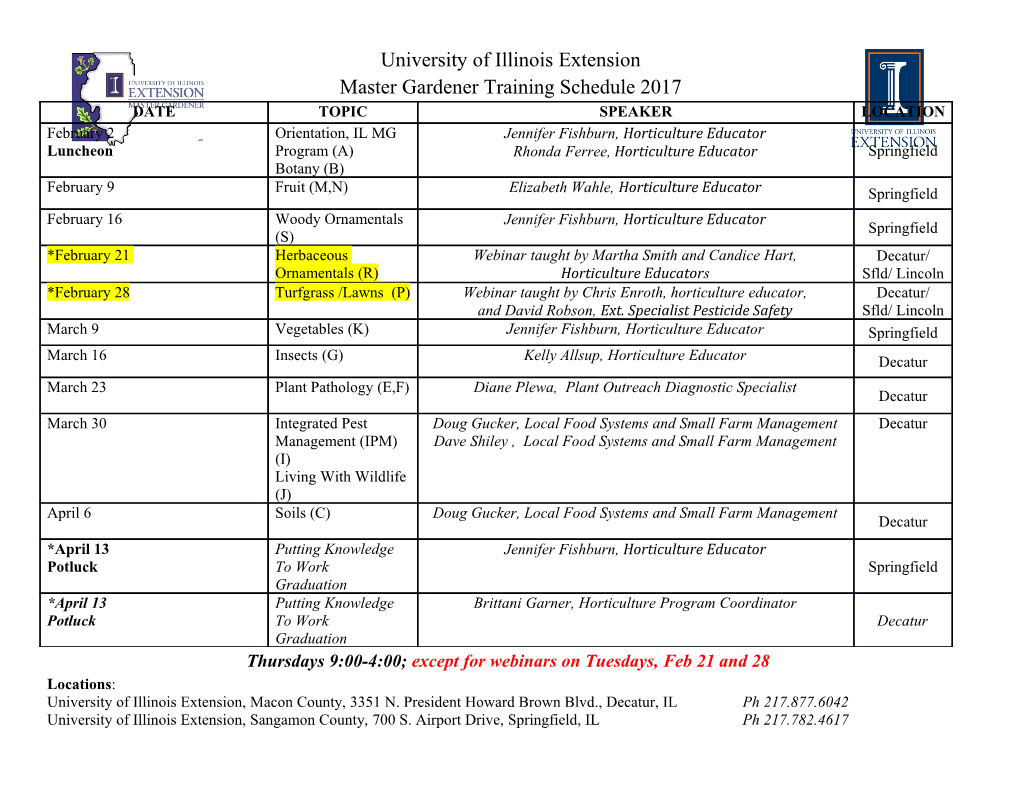
United States Patent [191 [111 3,734,582 Beauchet [451 May22,1973 [54] COMBINATION BEARING MATERIALS Primary Examiner-Charles J. Myhre Assistant Examiner-Frank Susko [75] Inventor: Jean Beauchet, Annecy (Haute Attorney-Stevens, Davis, Miller & Mosher Savoie ), France [73] Assignee: Societe Nouvelle De Roulements, An [57] ABSTRACT necy (Haute Savoie), France This invention relates to the manufacture of rolling [22] Filed: ' Oct. 29, 1971 contact bearings wherein the outer and inner races or rings were hitherto made of the same steel grade and [21] Appl. No.: 194,069 subjected to a heat treatment with or without a Related US. Application Data preliminary cementation. [63] Continuation of Ser. No. 4,729, Jan. 21, 1970, aban According to this invention, the inner races of the doned. bearings are made of cementation steel and the outer races as well as the rolling-contact members, such as [52] U.S. Cl ................................................. ..308/l73 balls and rollers from core-hardened alloy steel. The [51] Int. Cl. ...................................................... ..F16c treatment consists of a case-hardening or cementation [58] Field of Search .................... ..308/8, 2, 241, 237, applied to the inner races and of a hardening process 7 308/177 applied to the outer races and rolling bodies. [56] References Cited 2 Claims, 2 Drawing Figures UNITED STATES PATENTS 3,275,389 9/1966 Neilson et a1 ........................ _.308/8.2 3,734,582 1 2 COMBINATION BEARING MATERIALS creased fragility but also by a distortion of the treated parts, as a consequence of the above-described stress This is a continuation of application Ser. No. 4,729, effects, this distortion being frequently too important ?led Jan. 21, 1970, now abandoned. to be removed during the subsequent grinding and su The present invention relates to a novel method of per-?nishing operations. The distortion is considerably utilizing materials hytherto used in a conventional fash more pronounced in the case of cementation steel parts ion in the manufacture of races or rings of rolling than in the case of alloy steel parts of the “100 C 6” contact bearings, such as ball-bearings and taper-roller, grade, for these parts are subjected to two successive barrel-rollers or cylindrical-roller bearings, and the operations, notably the case-hardening operation tak like. ing place at a temperature higher than that at which the It is already known in the manufacture of bearing parts made of said “ 100 C 6" alloy steel are maintened races to use chromium steel alloys of a grade corre before hardening them. sponding substantially as a rule to the alloy 100 C 6 ac It is the essential object of the present invention to cording to the French Standards AF NOR NF A 35 551, minimize these inconveniences by combining the use of or to the American Standards SAE J 404 F, i.e., alloys 15 these materials in the manufacture of rolling-contact of which the composition lies approximately within the bearing parts with a view to takethe best advantage of following percent limits (by weight) : C = 0.95 to 1.10, their properties as a function of the service, mounting Cr = 1.50 to 1.60, Ni = 0.30, Mn = 0.25 to 0.40, Si = and manufacturing conditions and requirements of 0.10 to 0.35, P + S é 0.025, the residue being Fe. these parts. It is also known to manufacture bearing races or rings 20 Rolling-contact bearings according to the present in from cementation or case-hardened steel, i.e., of which vention are shown in the accompanying drawings the composition lies within the following limits given in wherein: percent by weight : C = 0.15 to 0.25, Si=0.20 to 0.35, FIG. 1 is a partially schematic, plan view of a bearing Mn = 0.30 to 0.60, Cr= 0.20 to 0.60, Ni = 1.65 to 2.00, shown in the direction of its axis of rotation. Mo = 0.20 to 0.30, A1 = 0.015 to 0.045, P + S é 25 FIG. 2 is a partially schematic, cross-sectional view 0.055. of the bearing shown in FIG. 1, taken along line 11-11 In either case the steel hardness necessary for a satis of FIG. 1. factoryoperation and useful life of the bearing is ob The method of manufacturing rolling-contact bear tained by submitting the parts to a suitable heat treat ings according to this invention is characterized by the 30 ment. use, in combination, of materials hardened and pre In the case of a steel of the above-de?ned grade “ 100 stressed by heat treatment so that the inner and surface C 6" having a relatively high carbon content this treat stresses developed during this treatment and known per ment consists of a hardening step causing the parts to se counteract and compensate the stresses subse acquire a relatively high and substantially constant quently developing during the mounting and service of hardness throughout the mass of the treated material. these parts, in order to reduce the strain thereof. In the case of cementation or case-hardened steel the The method of this invention consists more particu initial material is a low-carbon and therefore “non larly in making the inner races 10 of rolling-contact hardening" steel. Then this material is surface-enriched bearings (as shown in FIGS. 1 and 2) from cementation with carbon by applying a suitable cementation process steel and the outer races 11 as well as the rolling mem to a variable depth which however is always very re bers 2 of these bearing from core-hardening steel alloy. duced in comparison with the total mass or thickness In either case the steel and the heat treatment to be ap of the part. Then, the part is hardened in order to ob plied thereto are elected with a view to produce parts tain in the carbon-enriched ?lm a hardness comparable having a suitable hardness of the order of 62 HRc with that of the aforesaid steel grade “100 C 6.” The 45 points. hardness of the remaining portion of the part which has With this manufacturing method the distortion of the retained its initial composition is not increased appre parts is reduced to a minimum since the part most sub ciably but nevertheless this portion reserves a very ject to distortion, i.e., the outer race having a reduced good core resilience. cross-section in proportion to its dimensions, and more However, the heat treatment of a steel is attended by particularly the races of taper-roller bearings, are made tresses developing at the outer periphery of the treated parts. In the case of core-hardening steel, the hardening of core-hardening steel. The manufacture of the inner process begins at this outer periphery. The resulting race of cementation steel is troublefree as far as distor change of structure is attended by an increment in the tion is concerned for this part is considerably thicker and does not show any appreciable distortion after the ’ specific volume of the part and when the core thereof 55 is hardened in turn this causes traction stresses to de heat treatment. velop in the outer peripheral film or layer of the art. On On the other hand, the manufacturing technique ac the other hand, in the case of cementation steel, the in cording to this invention is attended by advantageous ternal structure of the part remains substantially un features for certain applications from the point of view of the strength of materials. The inner races of roller changed and counteracts any tendency of the periph 60 eral ?lm or outer layer to increase in volume, so that contact bearings are fitted as a rule on the correspond~ the surface layer of the part become compression ing shafts with a certain degree of tightness, whereby stressed. these races are more or less stressed and this, added to On the other hand, cementation steel parts have a the stresses resulting from the service loads supported by the shafts, increase the fragility of the parts in case better core resiliency than core-hardening steel parts 65 and therefore are less fragiles in case of shocks. of shocks. This condition is particularly true in the case Finally, the heat treatment of a steel with a view to of taper-roller bearings due to the presence of ?anges increase its hardness is attended not only by an in which may undergo important ?exion stresses. 3,734,582 3 4 In this case. the fact of making these parts from ce ing contact member and the outer ring race, for as al mentation steel permits of reducing this fragility in case ready explained hereinabove, the inner ring is more fre of shocks because these parts combine a good core re quently stressed than the outer ring, and with a greater silience with compression prestress in the outer layer intensity since the two bodies involved have curvatures which will counteract he traction stress resulting from of opposite sign. the load and also from the ?tting of'the parts on their For these various reasons it is advantageous to make shafts. the rolling bodies and the inner races or rings of bear On the other hand, as the dimensions of the inner ings from metals of different relationships, i.e., to use race or ring are considerably smaller than those of the core-hardening steel for the rolling bodies and cemen outer race or ring (notably in the perimeter of the race tation steel for the inner races or rings. working surface pro-per), the stress exerted thereon I claim: per surface unit is higher and as a rule its useful life is 1.
Details
-
File Typepdf
-
Upload Time-
-
Content LanguagesEnglish
-
Upload UserAnonymous/Not logged-in
-
File Pages4 Page
-
File Size-