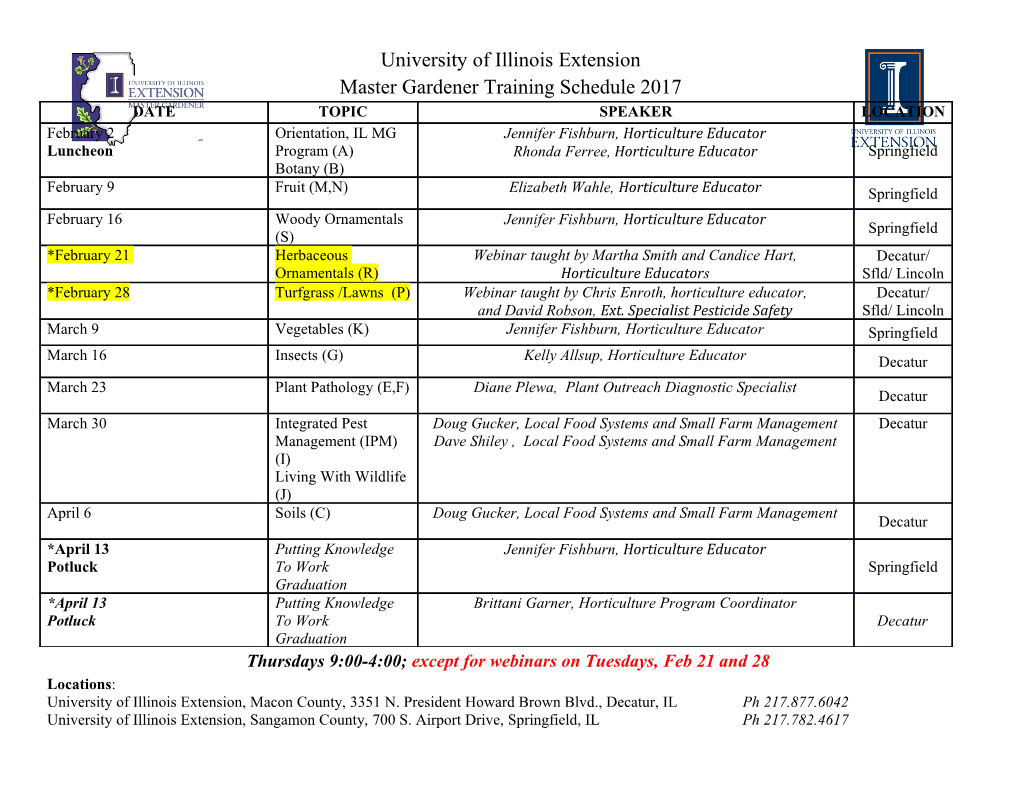
General Purpose Machine Tools “LATHE OPERATIONS” V.Gunasegaran Assistant Professor Department of Mechanical Engineering School of Mechanical Sciences BSAU, Chennai - 48 V.Gunasegaran, Assistant Professor, Department of Mechanical Engineering, BSACIST, Chennai - 48 Introduction Lathe is a machine, which removes the metal from a piece of work to the required shape & size Used to manufacture cylindrical shapes from a range of materials including; steels and plastics The Lathe may be operated by – Manual lathes – Computer controlled lathes (CNC machines) V.Gunasegaran, Assistant Professor, Department of Mechanical Engineering, BSACIST, Chennai - 48 Photograph of lathe V.Gunasegaran, Assistant Professor, Department of Mechanical Engineering, BSACIST, Chennai - 48 Principal parts V.Gunasegaran, Assistant Professor, Department of Mechanical Engineering, BSACIST, Chennai - 48 Types of Lathe According to the configuration – Vertical – Horizontal • Centre lathe, Engine lathe, bench lathe According to the Purpose or use – General purpose – Single purpose – Special purpose • Tool room lathe, tracer / copying lathe V.Gunasegaran, Assistant Professor, Department of Mechanical Engineering, BSACIST, Chennai - 48 Contd., According to the size and capacity – Small (low duty) – Medium (medium duty) – Large (heavy duty) – Mini or micro • Table top lathe According to the degree of automation – Non-automatic – Semi-automatic – Automatic V.Gunasegaran, Assistant Professor, Department of Mechanical Engineering, BSACIST, Chennai - 48 Contd., According to types of automation – Fixed automation – Flexible automation According to no. of spindle – Single spindle – Multi spindle V.Gunasegaran, Assistant Professor, Department of Mechanical Engineering, BSACIST, Chennai - 48 Kinematic System and Working Principle V.Gunasegaran, Assistant Professor, Department of Mechanical Engineering, BSACIST, Chennai - 48 Part descriptions V.Gunasegaran, Assistant Professor, Department of Mechanical Engineering, BSACIST, Chennai - 48 Lathe parts Lathe bed – Made from rigid cast iron – Accurately machined slideways – Slideways guide carriage & tailstock – Headstock on upper end of the lathe bed V.Gunasegaran, Assistant Professor, Department of Mechanical Engineering, BSACIST, Chennai - 48 Lathe parts-Contd., Headstock – Holds lathe spindle and gears – Chuck is fitted to spindle – Spindle is hollow for long bars V.Gunasegaran, Assistant Professor, Department of Mechanical Engineering, BSACIST, Chennai - 48 Lathe parts-Contd., Tailstock – Can be moved along slideways – Can be clamped in any location – Inside tapered to hold drill chuck V.Gunasegaran, Assistant Professor, Department of Mechanical Engineering, BSACIST, Chennai - 48 Lathe parts-Contd., Carriage – Moves along bed between tailstock and headstock – Saddle – across the lathe – Apron – hangs down in front V.Gunasegaran, Assistant Professor, Department of Mechanical Engineering, BSACIST, Chennai - 48 Lathe parts-Contd., Cross Slide – Fitted on the Saddle – Moves cutting tool at right angles to lathe bed V.Gunasegaran, Assistant Professor, Department of Mechanical Engineering, BSACIST, Chennai - 48 Lathe parts-Contd., Top Slide (Compound rest) – Fitted to top of Cross slide – Carries toolpost and cutting tool – Can rotate to any angle – used to turn tapers V.Gunasegaran, Assistant Professor, Department of Mechanical Engineering, BSACIST, Chennai - 48 Lathe parts-Contd., Feed shaft – Used to move the Carriage automatically Lead screw – Used when screw cutting on the lathe V.Gunasegaran, Assistant Professor, Department of Mechanical Engineering, BSACIST, Chennai - 48 Lathe Specifications Distance Between the centres Swing over the bed Swing over the cross slide Horse power of the motor Cutting speed range Screw cutting capacity Accuracy achievable Spindle nose diameter V.Gunasegaran, Assistant Professor, Department of Mechanical Engineering, BSACIST, Chennai - 48 Lathe Accessories V.Gunasegaran, Assistant Professor, Department of Mechanical Engineering, BSACIST, Chennai - 48 Work holding devices Three Jaw Chuck – Self centring – Holds round and hexagonal work – 3 jaws are connected – Jaws are stamped 1,2 & 3 and fitted in order – Chuck key used to open V.Gunasegaran, Assistant Professor, Department of Mechanical Engineering, BSACIST, Chennai - 48 Contd., V.Gunasegaran, Assistant Professor, Department of Mechanical Engineering, BSACIST, Chennai - 48 Contd., Centres V.Gunasegaran, Assistant Professor, Department of Mechanical Engineering, BSACIST, Chennai - 48 Contd., Face Plate V.Gunasegaran, Assistant Professor, Department of Mechanical Engineering, BSACIST, Chennai - 48 Contd., Dogs V.Gunasegaran, Assistant Professor, Department of Mechanical Engineering, BSACIST, Chennai - 48 Contd., Mandrel V.Gunasegaran, Assistant Professor, Department of Mechanical Engineering, BSACIST, Chennai - 48 Contd., Steady Rest and Follower Rest V.Gunasegaran, Assistant Professor, Department of Mechanical Engineering, BSACIST, Chennai - 48 Tool holding devices Toolpost – Fitted on top slide and carries the cutting tool or the cutting tool holder – Can adjust the height on some types – Can carry 4 different tool holders V.Gunasegaran, Assistant Professor, Department of Mechanical Engineering, BSACIST, Chennai - 48 Contd., Tool holders – Used for holding cutting tool bits – Available in Right hand, left hand and straight V.Gunasegaran, Assistant Professor, Department of Mechanical Engineering, BSACIST, Chennai - 48 Cutting Tools Can be High Speed Steel held in tool holders Can be also Ceramic (Tungsten carbide) bits held directly in toolpost V.Gunasegaran, Assistant Professor, Department of Mechanical Engineering, BSACIST, Chennai - 48 Contd., We can put different shapes on the High speed tool bits to cut different shapes on the workpiece V.Gunasegaran, Assistant Professor, Department of Mechanical Engineering, BSACIST, Chennai - 48 Lathe Cutting Operations V.Gunasegaran, Assistant Professor, Department of Mechanical Engineering, BSACIST, Chennai - 48 Turning V.Gunasegaran, Assistant Professor, Department of Mechanical Engineering, BSACIST, Chennai - 48 Facing V.Gunasegaran, Assistant Professor, Department of Mechanical Engineering, BSACIST, Chennai - 48 Eccentric Turning V.Gunasegaran, Assistant Professor, Department of Mechanical Engineering, BSACIST, Chennai - 48 Knurling V.Gunasegaran, Assistant Professor, Department of Mechanical Engineering, BSACIST, Chennai - 48 Grooving V.Gunasegaran, Assistant Professor, Department of Mechanical Engineering, BSACIST, Chennai - 48 Parting V.Gunasegaran, Assistant Professor, Department of Mechanical Engineering, BSACIST, Chennai - 48 Chamfering V.Gunasegaran, Assistant Professor, Department of Mechanical Engineering, BSACIST, Chennai - 48 Drilling Quill Drill clamp moving quill Tail stock Feed Tail stock clamp V.Gunasegaran, Assistant Professor, Department of Mechanical Engineering, BSACIST, Chennai - 48 Boring V.Gunasegaran, Assistant Professor, Department of Mechanical Engineering, BSACIST, Chennai - 48 Internal Operations 1) Internal facing and turning 2) Internal Reaming and Boring 3) Internal recess or grooving 4) Internal threading V.Gunasegaran, Assistant Professor, Department of Mechanical Engineering, BSACIST, Chennai - 48 Taper Turning - Methods 1) Form Tool Method 2) Swiveling Compound Rest 3) Taper Turning Attachment 4) Tail Stock Offset Method 5) Manual method V.Gunasegaran, Assistant Professor, Department of Mechanical Engineering, BSACIST, Chennai - 48 To find Taper angle D D tan 1 2 2 L 90° D1 D2 B C A L V.Gunasegaran, Assistant Professor, Department of Mechanical Engineering, BSACIST, Chennai - 48 Form Tool Method V.Gunasegaran, Assistant Professor, Department of Mechanical Engineering, BSACIST, Chennai - 48 Compound Rest Method V.Gunasegaran, Assistant Professor, Department of Mechanical Engineering, BSACIST, Chennai - 48 Taper Turning Attachment V.Gunasegaran, Assistant Professor, Department of Mechanical Engineering, BSACIST, Chennai - 48 Tailstock Off set Method V.Gunasegaran, Assistant Professor, Department of Mechanical Engineering, BSACIST, Chennai - 48 Thread Cutting Lathes are also used to cut threads in round bars These threads take up different profiles e.g ISO (60°) ACME etc., These threads can be seen on bench vices, lathes etc. V.Gunasegaran, Assistant Professor, Department of Mechanical Engineering, BSACIST, Chennai - 48 Contd., V.Gunasegaran, Assistant Professor, Department of Mechanical Engineering, BSACIST, Chennai - 48 Types of Threads V.Gunasegaran, Assistant Professor, Department of Mechanical Engineering, BSACIST, Chennai - 48 Types of Threads V.Gunasegaran, Assistant Professor, Department of Mechanical Engineering, BSACIST, Chennai - 48 Internal Threads V.Gunasegaran, Assistant Professor, Department of Mechanical Engineering, BSACIST, Chennai - 48 Operating Cutting Conditions Feed (f) Depth of cut (d) Cutting Speed (v) V.Gunasegaran, Assistant Professor, Department of Mechanical Engineering, BSACIST, Chennai - 48 Cutting Speed D - Diameter (mm) N – Spindle speed (rpm) V - Cutting Speed (m/min) • Peripheral speed of workpiece past the cutting tool V.Gunasegaran, Assistant Professor, Department of Mechanical Engineering, BSACIST, Chennai - 48 Feed The linear distance of tool advances for every rotation of workpiece V.Gunasegaran, Assistant Professor, Department of Mechanical Engineering, BSACIST, Chennai - 48 Depth of Cut d – depth of cut – Perpendicular distance between machined surface and uncut surface of the
Details
-
File Typepdf
-
Upload Time-
-
Content LanguagesEnglish
-
Upload UserAnonymous/Not logged-in
-
File Pages108 Page
-
File Size-