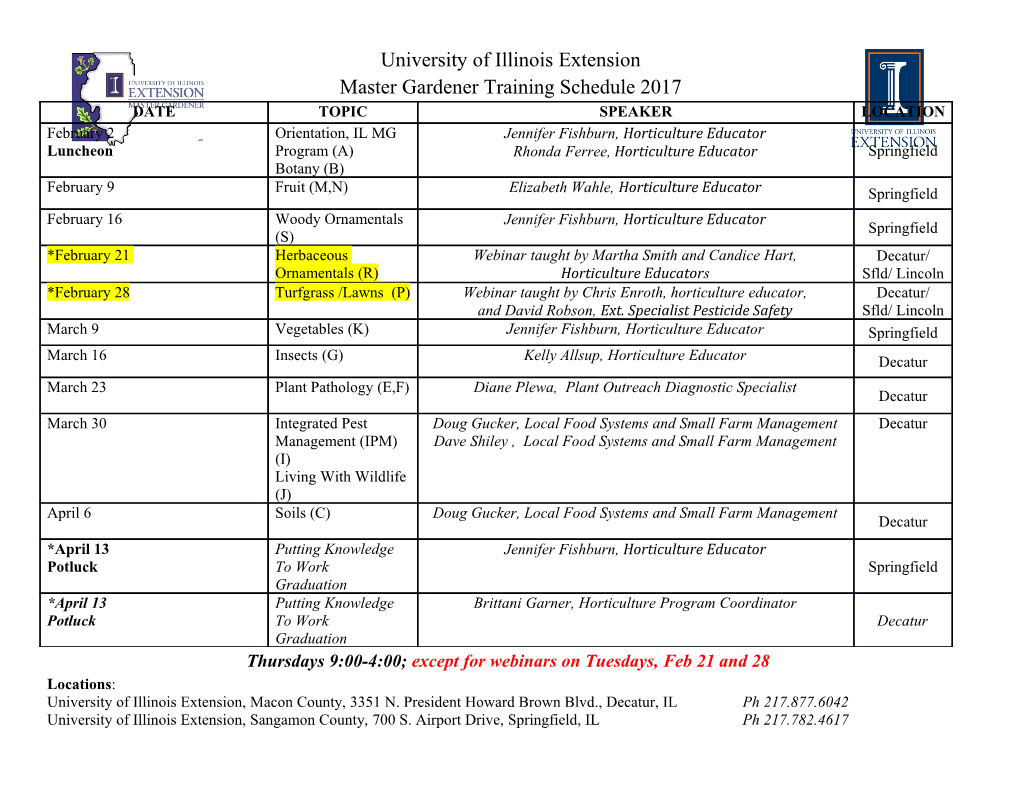
4. 9 & FR0105396 DEVELOPMENT OF MILLER CYCLE GAS ENGINE FOR COGENERATION DEVELOPPEMENT D UN MOTEUR A GAZ A CYCLE DE MILLER DESTINE A LA COGENERATION N. Tsukida , A.Sakakura, Y.Murata, and K. Okamoto Tokyo Gas CO.,LTD , Japan T.Abe and T. Takemoto Yanmar Diesel Engine CO.,LTD , Japan ABSTRACT We have developed a 300 kW gas engine cogeneration system for practical use that uses natural gas.Using a gas engine operated under conditions with an excess air ratio X =1 that is able to use a three way catalyst to purify the exhaust gases,we were able to achieve high efficiency through the application of the Miller Cycle, as well as a low NOx output. In terms of product specifications, we were able to achieve an electrical efficiency of 34.2% and a heat recovery efficiency of 49.3%, making an overall efficiency of 83.5% as a cogeneration system. RESUME Nous avons developpe un systeme de cogeneration de 300 kW avec moteur au gaz natural et tout a fait utilisable dans la pratique. Avec un moteur a gaz fonctionnant dans les conditions d ’un rapport d ’exces d ’air de X = 1 et capable d ’utiliser un catalyseur trois voies pour purifier les gaz d ’echappement, nous avons ete en mesure d ’obtenir un rendement eleve en appliquant le Cycle de Miller, et d ’obtenir egalement une faible emission d ’oxydes d ’azote. En termes de performances techniques du produit, nous avons obtenu un rendement electrique de 34,2 % et un rendement de recuperation thermique de 49,3 %, ce qui donne un rendement total de 83,5 % pour le systeme de cogeneration. DISCLAIMER Portions of this document may be illegible in electronic image products. Images are produced from the best available original document. INTRODUCTION Environmental issues have been the focus of much attention for quite some time, but it is now becoming important that we not only make efforts on a regional level with issues such as air pollution, but on a global scale as well. It is crucial that we the people of this earth act quickly to reduce the level of C02 in order to prevent global warming. The use of gas cogeneration systems that supply both electric power and heat at the same time using natural gas as fuel are steadily growing as an energy source in metropolitan areas because they have high overall efficiency, are energy and cost efficient, and output clean exhaust gasses. Fig. 1 shows the actual growth of cogeneration systems in the areas supplied by Tokyo Gas Co. Moreover, their use is expected to rapidly expand worldwide because of their high overall efficiency and the fact they use natural gas - the main component of which is O £ -86 88 90 92 94 96 98 year Fig. 1 Gowth of Cogeneration i n Tokyo Gis The power scale of the cogeneration system that uses a gas engine as the prime mover is quite large, with a single unit capacity ranging between 15 and 4,000 kW. The majority of the units installed though, are in the 300 to 1,000 kW class that is made up of gas engines having a bore diameter of 150 to 200 mm, and of which there are two types: the stoichiometric mixture combustion type that uses a three way catalyst, and the lean-burn type that does not require a catalyst. In recent years, use of the lean-burn type, which is has high electrical efficiency and with which there is no need to purify the exhaust gases, is growing. However, it is thought that NOx reduction through only the combustion of the gas engine has nearly reached its limit with the current regulation value levels, and there is concern about how to deal with the environmental regulations that can only be assumed will become stricter in the future. The stoichiometric mixture combustion type, on the other hand, is advantageous in that it has a high exhaust gas temperature and efficient exhaust heat recovery, making the high overall efficiency above 80%, so it is well suited for cogeneration systems. However, the electrical efficiency is below that of the lean-burn type, so it is hoped that this can be improved. Furthermore, according to an amendment to the laws within Japan, it is now possible to use those gas fuel generators that are for ordinary use as generators for emergency use as well if the gas supply conduit is deemed earthquake-proof. There is therefore a demand for a gas cogeneration system having high electrical efficiency and low NOx during ordinary use, as well as good characteristics for keeping up with the load during emergency use (bearable load characteristics: the load ratio where instantaneous output is possible with only a slight rpm drop from an idling state). We attempted to achieve high efficiency by applying the Miller Cycle ex(1) to the stoichiometric combustion gas engine that is able to realize a low level of NOx emissions relatively easily using a three way catalyst, in order to achieve high efficiency. As performance, durability and so forth demanded as a cogeneration system were able to be achieved, we will report on that process in this paper. 1. Results of the Basic Research (2>~(5) 1.1 Means to Realize the Miller Cycle The basic research was conducted with an altered commercial gas engine. Table 1 shows the specifications of the test engine. Table.1 Engine Specifications —...... ...... Baseline Tested Otto Cvcle Miller Cvcle Type Spark-Ignited 4 Stroke Cycle cylinders x Bore x Stroke (irm) 6 x f 170 x 170 Displacement Volume (litre) 23.15 Natural Gas : IBV=41.6 MJ/Nrrt3 Fuel Z 88.5 % - CHi , 4.6 % - CaHs \ X 5.4 % - OB . 1.5 % - OHio ' Rated Power (kW / rpm) 220 / 1200 324 / 1500 BMEP (MPa) 0.95 1.12 Equivalence Ratio 1.0 with Three-way Catalyst Supercharging Turbo-charger / Inter-cooler Pressure Ratio of Turbo-charger 1.6 1.8 ~ 2.8 Expansion ratio (Geometric Compression Ratio) 10.3 10-18 Intake Valve IVO (deq.bTDC) 20 Timing IVC (deg. aEDC) 40 -60 , 40-140 Mechanism of (1) EIVC Low Compression Ratio (2) LIVC In realizing the Miller Cycle, numerical calculations and experiments were performed on the early intake-valve closing (EIVC) type and the late intake-valve closing (LIVC) type according to the changes in the cam profile, and were then examined. The experimental conditions were set so that the rated power was 324 kW / 1500 rpm, BMER 1.12 MPa, and the inter-cooler outlet air-fuel mixture temperature was set at 313 K. In addition, with the cogeneration system it was not necessary to take the engine rpm characteristics into consideration because the generator is driven by the engine shaft horsepower. Therefore, the experimental conditions were such that the engine revolutions were set at a general 1500 rpm when the generation frequency was 50 Hz. Fig. 2 shows a diagrammatic drawing of the valve lift of the EIVC type and the LIVC type, and their respective changes in air-fuel mixture mass flow rate at the rated power. Engine Output=324 kW EIVC Base 120 deg. 60 deg. 40 deg. Base 0.4 - 0.2 " -0.2 " -0.4 -270 Crank Angle deg.aEDC Fig.2 Intake Valve Lift and Mass Flow Rate With the EIVC type the maximum amount of lift decreases due to the fact that the shape of the cam profile is similar to that of the base. Furthermore, the mass flow rate peak is high because of the necessity to force air-fuel mixture in a short amount of time. This results in the need for a relatively large pressure boost. With the LIVC type, on the other hand, the maximum lift period is extended compared to the base cam profile and it is clear that the mass flow rate flows back past BDC. During development, it may be said that with the EIVC type, along with matching the supercharger it is highly likely that it will be necessary to reexamine the valve drive system (lift height, seating rate, fixed number of springs, etc.). With the LIVC type, however, that likelihood is quite low. Fig. 3 shows the effective compression ratio as the intake valve is closed with an expansion ratio of 14.2, and the air-fuel mixture temperature at the intake port. The effective compression ratio peaks around 40 aBDC because of the inertia force and an efficient compression ratio reduction effect is evident where there is left and right symmetry with the peak in the center with both types. In addition, with the LIVC type the air-fuel mixture temperature at the intake port rises due to the back flow of intake air, and it is feared that there will be a decline in knocking performance. Engine Output = 324 kW,Expansion Ratio - 14.2 Temperature at Exit of Inter Cooler = 313K -3 16 . oJ A EIVC 14 • □ LIVC Calculated X 12 / X / \ 10 7------ X ii 8 / 8 / 6 320 -150 -100 -50 BDC 50 100 150 IVC Timing deg. aBDC Fig.3 Effect of IVC Timing on Effective Compression Ratio and Intake Temperature Engine Output = 324 KW Tenperature at Exit of Inter Cboler = 313K |l20/15|- 12 14 16 18 Expansion Ratio Fig.4 Effect of Expansion Ratio on Thermal Efficiency 1.2 Thermal Efficiency of the Late Closing Miller Cycle Fig. 4 shows the change in thermal efficiency as the expansion ratio is changed with a fixed rated engine load. The ignition timing was advanced up to the respective knocking limits, and the expansion ratio was increased in an attempt to drastically improve thermal efficiency.
Details
-
File Typepdf
-
Upload Time-
-
Content LanguagesEnglish
-
Upload UserAnonymous/Not logged-in
-
File Pages10 Page
-
File Size-