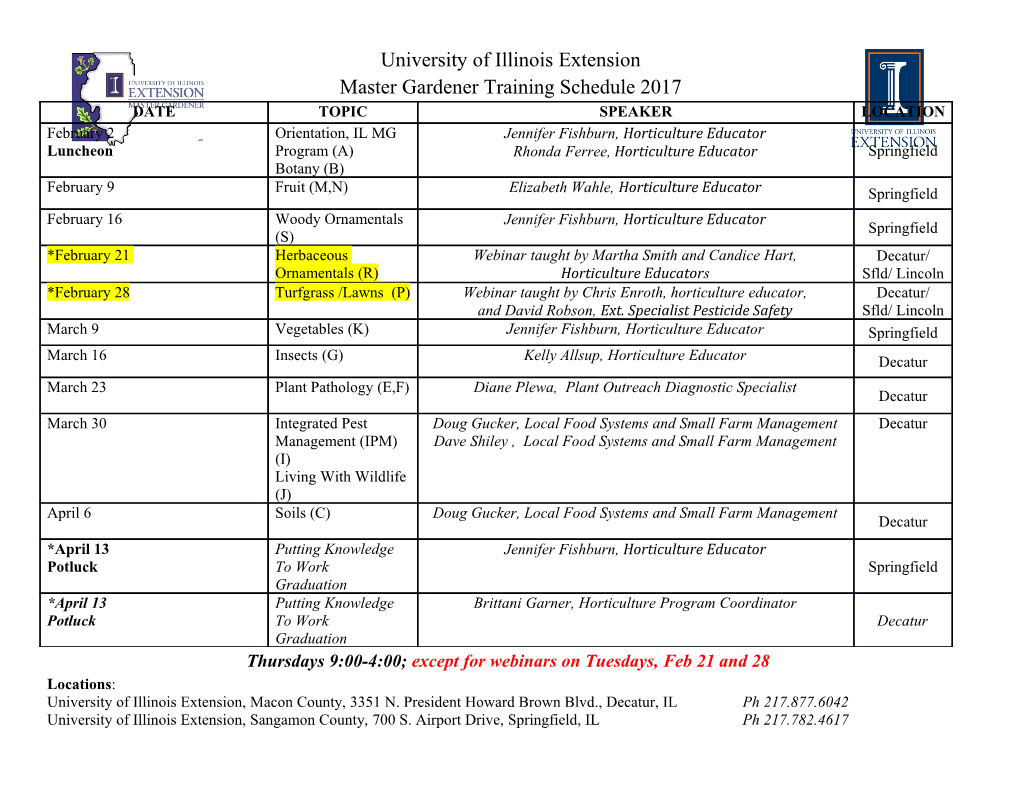
FEATURE FOCUS TRASH AND BURN Synthetic gases derived from industrial and municipal wastes Downloaded from http://asmedigitalcollection.asme.org/memagazineselect/article-pdf/122/11/80/6382529/me-2000-nov2.pdf by guest on 26 September 2021 fuel cogeneration plants in Europe. By Michael Valenti, Senior Editor LCHEMISTS IN MEDIEVAL Eu­ rope sought the philoso­ pher's stone that they be­ lieved would enable them to transform lead into gold. Today, their descendants in Italy and Germany are converting the car­ bon in oil-refining tar, plastic wastes, and steel-furnace gas into a synthesis gas that provides electricity, process steam, and valu­ able chemical feedstock. The modern version of the fabled philoso­ Downloaded from http://asmedigitalcollection.asme.org/memagazineselect/article-pdf/122/11/80/6382529/me-2000-nov2.pdf by guest on 26 September 2021 pher's stone is gasification, a process typicaUy used to convert high sulfur coals into a syn­ thesis gas, or syngas, that can be bu rned cleanly. BasicaUy, the coal is prepared and fed into a reactor, or gasifier, w here it is partly oxidized with steam under pressure. By si­ multaneously reducing the presence of oxy­ gen in the gasifier, the carbon in the coal is converted into a gas that is 85 percent car­ bon monoxide and hydrogen, with smaller portions of carbon dioxide and methane. Sulfur is removed from the gasified coal and is sold in its elemental form, or as sulfu­ ric acid. Inorganic materials such as ash and metals drop out as slag, which is typically used for construction materials. When coal is gasified to generate electrici­ ty, it is typically consumed in an integrated gasification combined cycle, or IGee, con­ figuration, to improve the energy efficiency General Electric modified its gas turbines, such as this 7001FA being installed at the Wabash River project based in West Terre Haute, Ind., for IGCC service. of gasification plants, which are inherently more expensive than conventional coal-fired power built in the next 10 years will be designed to consUl11.e plants. In the combined cycle, gas is burned in turbines coal or oil. rGee can make them cleaner and lower the to produce electricity, and exhaust is recovered to pro­ costs of the electricity they produce." duce steam in a boiler that powers another turbine to Other economics are spurring the development of generate additional electricity. The plant may provide waste-fueled [Gce plants. "When we built Cool Water, process or heating steam as well . the [Gce technology generated electricity at a cost of While mechanical engineers work to make [Gce $2,000 per kilowatt. Since then, we have got the cost of plants more economical, they tout the environmental [GCe-generated electricity down to less than $1,000 per advantages of burning syngas, a cleaner-burning fue l kilowatt. Using waste fuels helps to reduce the cost of than coal. The same ecological benefits underpin the electricity even further," explained Todd. Italian and German plants, which convert waste materi­ This is particularly true for the wastes generated by oil als containing carbon into gas turbine fuel. refining, such as petroleum coke. "Most of GE's orders All of these plants rely on heavy-duty gas turbines that for lGee turbines are for petroleum coke plants, most the General Electric Co. in Schenectady, N.Y., has been' recently, under construction in France, Spain, and the modifying for rGee service since 1984, when the first United States," Todd said. "For example, the Delaware rGee plant, the Cool Water Demonstration Project in Star refinery in Delaware City, Del., was recently con­ the Mojave Desert in California, came online. verted to gasify solid-waste petroleum coke to power "We've accumulated 320,000 hours of syngas-fueled four GE 6FA gas turbines." power generation worldwide since Cool Water," said General Electric's experience is underscored by the first Douglas Todd, a chemical engineer and manager of World Gasification Survey conducted by SFA Pacific Inc. process power plants at GE. "We joined Cool Water to of Mountain View, Calif., in 1999. This survey was sup­ demonstrate how the advantages of combined cycle costs ported by the U.S. Department of Energy and member could be applied to fuels other than natural gas. We be­ companies of the Gasification Technologies Council in lieve that 30 percent of the world's power plants to be Arlington, Va. The survey identified 160 commercial The integrated gasification combined cycle process was originally designed gasification plants operating, being built, or planned in to convert high sulfur coal into more environmentally benign synthetic gas. 28 countries around the world. M EC H AN ICA L ENG INE ERI NG NO V EMOER 2000 81 The survey showed that in the 1990s, gasification capac­ nies to sell power, and assisted legislation that would set a ity fueled by petroleum-based materials, including residual competitive price for electricity generated by waste­ oil, petroleum coke, and tars, was approximately 60 per­ derived fuels. cent of coal-fueled capacity. However, the survey found The visbreaking tar is a thick liquid that is pumped to that refi ning industry econom.i cs, stricter environmental the gasifier unit, which is licensed from Texaco Inc. in regulations, and electricity deregulation that enable oil re­ White Plains, N.Y. , and was originally used in the Cool fineries to generate power and compete in open energy Water program. markets would increase the use of petroleum material gasi­ Oxygen is added to the gasifier to partly oxidize the fication. The study forecast that after the current year, pe­ tar under press ure. This ca uses the ca rbon and the oil troleum-based gasification capacity would grow almost in the tar to change to carbon monoxide rather than twice as fast as coal-based gasification capacity. carbon dioxide, and the hydrogen present to become gaseous hydrogen, rather than water. The plant then Downloaded from http://asmedigitalcollection.asme.org/memagazineselect/article-pdf/122/11/80/6382529/me-2000-nov2.pdf by guest on 26 September 2021 TURNING TAR INTO SARDINIAN POWER separates the elementally pure hydrogen that Sarlux The survey's findings are supported in the world 's uses to upgrade all its finished fuel products, such as larges t rGee power plant, recently constructed by a gasoline. The remaining sy ngas is sent to the turbines conso rtium including Snamprogetti S.p.A. of Milan and to make power. GE Power Systems of Schenectady on the Italian island There are three GE 109E, single-shaft combined cycle of Sardinia. The rGee plant is lo cated at the Saras Oil systems built by GE and its subsidiary, Nuovo Pignone of R efin ery in Sarroch, the second largest European refin­ Florence. Each GE STAG (steam and gas) system consists ery. The plant has been running on syngas since Au­ of a GE MS9001E gas turbine, a GE 109E condensing gust, and produces 551 megawatts of electricity, 285 steam turbine, a double-end generator, and a heat recov­ metric tons of process steam for the refinery, as well as ery steam generator. 20 million standard cubic feet a day of hydrogen feed­ The turbines are started up by distillate oil, are injected stock. The Sardinian facility is owned by Sarlux S.r.I., a with steam to control rutrogen oxide formation, then are joint venture formed by Saras R affi enerie S.p.A. of Mi­ switched over to syngas. Distillate oil also serves as the lan and Enron Corp. of Houston. backup fu el for the Sarlux turbines. The Sarlux rGee plant gasifies the tar-like residue pro­ "We designed the turbines to handle syngas with 40 duced by vacuum visbreaking at the Sarroch refin ery. percent moisture, and a hea ting valu e one-sixth that of natural gas. The combustor design has to handle six times the amount of sy n­ gas compared to natural gas . This means the fuel delivery system must deliver the higher volume and be ex­ plosion-proof, due to the hydrogen fuel," said Todd, who added that these proprietary modifica tions grew out of GE's Cool Water experience. Each Sarlux turbine produces up to 186 MW of electricity while meeting Italian elTlission levels of 30 parts per million for nitrogen oxides and sulfur oxides. GE adds the 40 percent mois­ ture to the fuel to reduce NOx forma­ tion. Noise levels must be less than 85 decibels at the equipment. The Sarlux rG ee plant will generate The Schwarze Pumpe plant in Spreewitz, Germany, gasifies a variety of wastes, ranging from about four billion kilowatt-hours of elec­ scrap plastic to junked railroad ties, to produce electricity, steam, and chemical fe edstock. tricity annually that will be sold to Vac uum visbreaking is a form of thermal cracking of pe­ ENEL. This energy will be distributed throughout Sar­ troleum that dates back to the 1930s. Visbreaking in­ dirua's electrical grid. Sarlux will also generate fresh water. volves subjecting heavy crude oil to pressure and heat to WE GASIFY ANYT HING physically break its large molecules into smaller ones to produce lighter fu els, such as gasoline and diesel fuel. In Spreewitz, Germany, north of Dresden, Sekundar­ Originally, the visbreaking tar at Sarlux was incinerated rohstoff-Verwertungszentrum Schwarze Pumpe GmbH in boilers to make electricity for ENEL, the nationalltal­ operates an rGee facility that converts an eclectic mix of ian power company. By 1990, environmental regulations 450,000 metric tons of solid waste, and 50,000 metric tons prohibited the practice. rGee was already an ecologi­ ofliquid wastes, into electricity, steam, and lTlethanol call y viable alternative, so GE and its Itali an partners feedstock.
Details
-
File Typepdf
-
Upload Time-
-
Content LanguagesEnglish
-
Upload UserAnonymous/Not logged-in
-
File Pages5 Page
-
File Size-