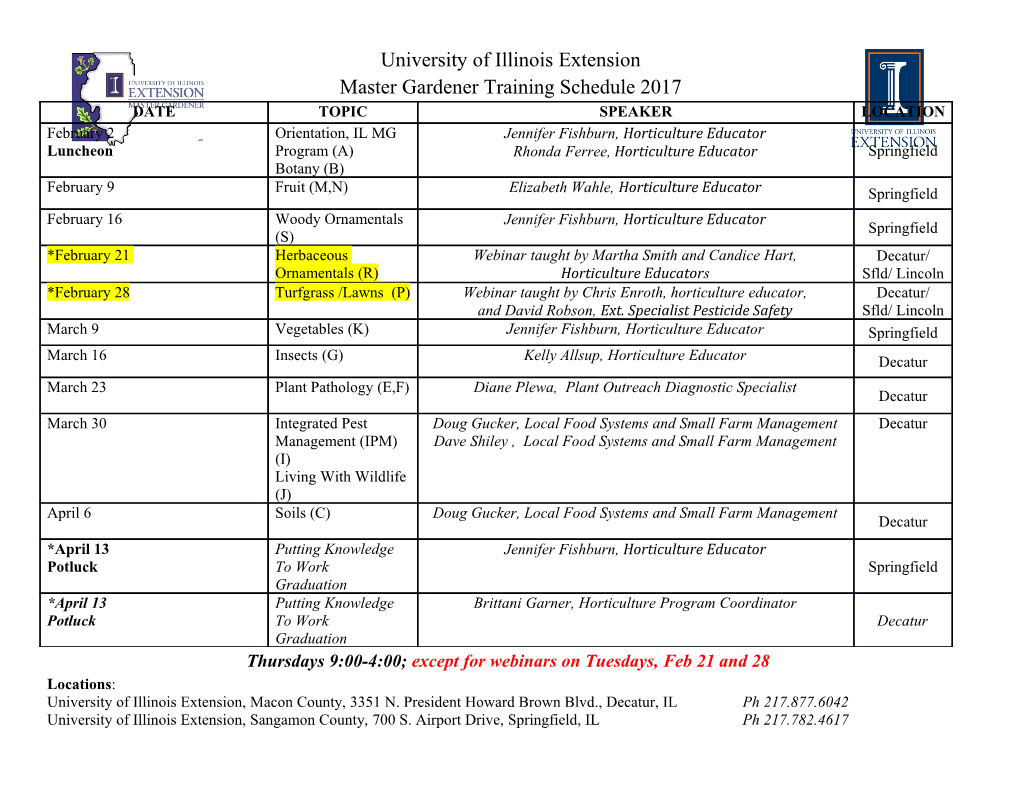
Forming thermal imaging system field of view with afocal lens cap Igor G. Chyzha, Valentin G. Kolobrodova, Volodymyr I. Mykytenkoa, Grygorij S. Tymchika, Paweł Komadab, Ainur Kozbakovac,d aNational Technical University of Ukraine "Igor Sikorsky Kyiv Polytechnic Institute"; bLublin University of Technology; cInstitute Information and Computational Technologies CS MES RK; dAlmaty University of Power Engineering and Telecommunications ABSTRACT Method of infrared lenses field of view step variation is discussed in this paper. Simple afocal lens caps based on the classic Kepler or Galilee telescopic schemes are considered. The afocal cap have to provide acceptable vignetting of the extreme rays and moderate transverse dimensions. Mersenne two-mirror system of Galilean-type was selected as the most suitable lens cap. Equations were obtained to calculate dimensional parameters of the cap in respect that vignetting coefficient should be minimal. Keywords: Galilean-type rotary lens afocal cap, Mersenne two-mirror afocal system, thermal imager field of view, field of view vignetting 1. INTRODUCTION Optoelectronic imaging systems are widely applied to observe environment. Frequently observers need to change viewing angle or field of view of the imager1, 2, 3.Thermal imager field of view is commonly varied with zoom infrared lenses or with afocal lens cap. Zoom lenses provide smooth change in the focal length and field of view of the thermal imager, but they have complex optical system and relatively high cost4, 5. Vario-optic lens cap has less complex optical system. However, it is not free from the shortcomings of zoom lenses due to the difficulty in ensuring adequate image quality at various positions along the axis of it’s medium components6–9. Afocal lens cap with fixed optical system while rotating around the center axis point by 90° and 180° provides three fixed values of the focal length and the field of view. This principle is much easier to implement technically, which contributes to a significant reduction in the cost of the zoom. In this case, the presence of only three pairs of values of focal length and field of view of the thermal imager satisfies the needs of the user in the vast majority of practical applications of this device10–13. In the design of serial thermal imagers rotary afocal lens cap, in addition to providing several required fields of view, the following additional requirements must be taken into account: 1) spectral range of the afocal cap should not reduce the working spectral range of thermal imager; 2) afocal cap does not have to flip thermal image horizontally and/or vertically; 3) afocal cap should not reduce the nominal (without the cap) field of view of the thermal imager through the vignetting of peripheral, inclined to the optical axis beams. That is, when working with afocal cap the image must completely fill the monitor screen without significantly reducing the brightness from center of the screen to its edges; 4) the modulation transfer function (MTF) of the thermal imager optical system with the added afocal cap should not be significantly different from the MTF of the basic lens due to effect of the aberrations of the cap or due to central shielding of the lenz entrance pupil, for example, with a mirror telescopic system. The list of these requirements is oftenly satisfied with the use of purely mirror afocal systems, which have no alternatives in terms of ensuring the requirement for the non-disturbance of the spectral range of the thermal imager14–17. At the stage of conceptual design of lens or mirror afocal systems, it is necessary to coordinate the transverse dimensions and optical forces of their components and their relative position, based on need to provide certain sizes of field of view. Because of need to have a direct image from the afocal cap, it’s telescopic system usually belongs to the Galilean type. However, it is fundamentally impossible to have a field diaphragm in such systems. * [email protected] Therefore, the field of view is limited with vignetting diaphragms. Acceptable vignetting of beams is characterized by a coefficient, which indicates the part of the entrance pupil plane, through which the rays of the beam are received. It is more convenient use linear vignetting coefficient when performing dimensional and energy calculations h k , D where h is height of the segment of zoom lens circular entrance pupil, which is filled with beams inclined to the optical axis, and D is diameter of zoom lens entrance pupil. The value k 1 means complete filling of the entrance pupil with rays and absence of their vignetting. The value k 0 indicates complete vignetting of beams that enters the optical system from a point located either on the edge of the field of view or outside the optical system’s field of view. Other values of the coefficient in the range of 01k may indicate the acceptable vignetting of extreme rays, which limits the system’s field of view without a field diaphragm. The purpose of this work is to obtain formulas for calculating the field of view of a zoom lens with mirror or lens afocal cap, taking into account the geometric and optical parameters of their components. Also size and position of thermal imager basic lens entrance pupil and acceptable value of vignetting coefficient k , which limits the zoom lens field of view, are considered. 2. LENS AFOCAL CAP CALCULATION Afocal lens caps are telescopic systems based on the classic Kepler or Galilee schemes. When using the Kepler scheme, the image will be flipped. This contradicts item 2) of the above requirements. This limites Kepler's scheme usage without additional improvements. The Galileo scheme allows you to have direct image. Moreover, it is shorter than the previous one. Therefore, it is widely used in afocal lens caps. However, it does not have a field diaphragm, and therefore its field of view is limited by vignetting of peripheral beams. In this case correct choice of dimensional parameters of the afocal cap components and its location relative to the thermal imager lens is important. The focal lengths and light diameters of the afocal cap components are the dimensional parameters that need to be defined. For their calculation, it is necessary to provide initial data: a) the entrance pupil diameter of thermal imager standard lens; b) the distance between the first optical surface of thermal imager lens and its entrance pupil; c) field of view of thermal imager lens; d) the required values of the thermal imager field of view when it is enlarged and reduced by an afocal cap; e) the acceptable value of coefficient k of vignetting for rays coming from the edge of the field of view. It is assumed that afocal cap will have three different positions relative to thermal imager lens (Fig. 1 – Fig. 3).Then the problem arises to provide three necessary values of the thermal imager field of view at the acceptable values of the vignetting coefficient. 1 2 2 1 b 3 D D D d a'p Figure 1. Afocal system according to Galilee scheme. 1 3 D 2 c Figure 2.Galilean-type afocal system is rotated 90° relative to the lens optical axis around the point O. 2 1 3 D a'p Figure 3. Galilean-type afocal system is rotated 180° relative to the lens optical axis around the point O. The following definitions are used in the figures: D1 is diameter of the component with a positive focal length f1 , D2 is diameter of the component with a negative focal length f2 , D3 is diameter of the entrance pupil of thermal imager objective lens with fixed optical force, D4 is diameter of the aperture for passing the light between the lens components, d is axial distance between the corresponding principal planes of the components of Galilean system, a p is acceptable distance between the entrance pupil of the lens and the posterior principal plane of the neighboring component (see Fig. 1 and Fig. 3), с is distance between remote hole in telescope barrel and entrance pupil of the lens. The afocal cap, shown in Fig. 1, reduces the field of view of the entire lens system in times. The cap in Fig. 2 does not change the field of view of thermal imager. The system in Fig. 3 increases the field of view of the whole system in f times, where 1 is the angular magnification of Galilean system. f2 Formulas for calculations the afocal cap field of view, which were obtained for three positions of the cap relative to the basic lens, are given below. In the formulas 2 is the size of thermal imager field of view in front of the cap, 2 is the field of view in the image space after the focal cap. It should be noted that the value must be consistent with the nominal value of the thermal imager basic lens field of view, that is, to be equal to this value, or at least not to exceed it. The formulas in Fig. 3 are given for the case when the field of view is vignetted with the frame of component 2. Formulas to the scheme in Fig. 1 k=1: DD DD 22 arctg 13; 22 arctg 13; 2(ap +d) 2(ap +d) k=0.5: D D 22 arctg 1 ; 22 arctg 1 ; 2(ap +d) 2(ap +d) k=0: DD DD 22 arctg 13; 22 arctg 13. 2(ap +d) 2(ap +d) Formulas to the scheme in Fig. 2 k=1: DD 22 arctg 43; 2c k=0.5: D 22 arctg 4 ; 2c k=0: ()DD 22 arctg 43.
Details
-
File Typepdf
-
Upload Time-
-
Content LanguagesEnglish
-
Upload UserAnonymous/Not logged-in
-
File Pages8 Page
-
File Size-