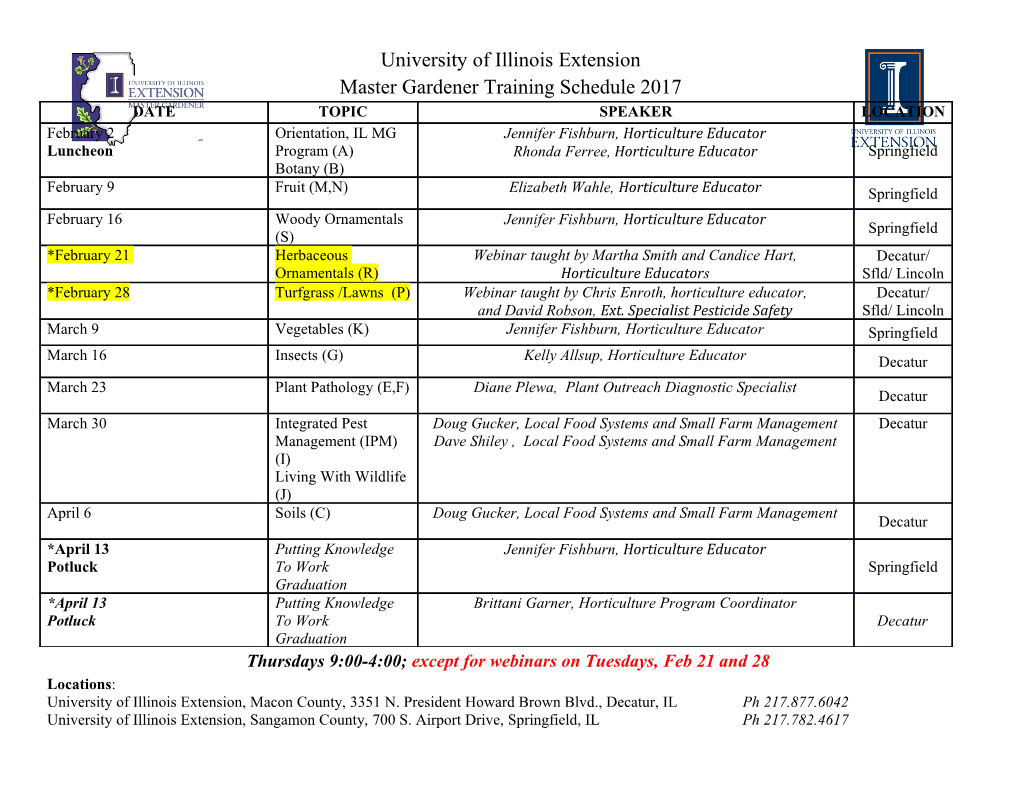
Oct. 3, 1939. L. JONES 2,175,026 FUSION WELDING Filed June 13, 1938 In N/ ent or ; Leonard Jones, bu 7. é du 4 His Attorne U. Patented Oct. 3, 1939 2,175,026 UNITED STATES PATENT OFFICE 2,175,026 FUSON WELDING Leonard Jones, Davyhulme, England, assignor to General Electric Company, a corporation of New York Application June 13, 1938, Serial No. 213,491 In Great Britain June 17, 1937 3 Claims. (C. 219-8) My invention relates to fusion welding, and My invention will be better understood from more particularly to that form of electric fusion the following description taken in connection with Welding known as atomic hydrogen Welding. the accompanying drawing and its scope will be In atomic hydrogen welding, the fusion of the pointed out in the appended claims. work parts is accomplished through the agency In the drawing, Fig. 1 is a diagrammatic illus of a "flame' of atomic hydrogen. This “flame' tration of an atomic hydrogen welding system em * results from the recombination of atomic hydro bodying my invention; and Fig. 2 is a fragmen gen to form molecular hydrogen which occurs tary view illustrating one manner in which a limit with the release of a great amount of heat. switch forming part of the system may be em 10 Atomic hydrogen may be generated by disso ployed for securing reduced heating at the end of ciating hydrogen or a gas containing hydrogen a welding Operation. through the agency of an electric arc across which In atomic hydrogen welding, atomic hydrogen the gas is directed. By controlling the energy of is generated by an instrumentality usually re the arc by regulating its length and voltage, the ferred to as a welding head. The atomic hydro 5 amount of atomic hydrogen generated may be gen welding head illustrated in Fig. 1 may be of 5 controlled and thus the heat available for Weld the type described and claimed in United States ing may be controlled. Letters Patent 1,946,305, James T. Catlett, Feb While my invention will be described in con ruary 6, 1934. This head comprises electrodes 0 nection with a novel atomic hydrogen welding and which are fed toward and away from one system, it is to be" understood that as a method another by a feed motor 2 to maintain between of welding it is applicable to any form of fusion their arcing terminals an arc across which hydro welding. gen or a hydrogen containing gas is supplied (by When fusion welding butt or edge joints, it is a means not illustrated) to be dissociated in the the present practice to maintain the amount of arc for the formation of atomic hydrogen. Elec heat available in the welding zone as constant as trode 0 is fed by motor 2 through worm 3, . possible along the whole length of the joint so Worm wheel 4, bevelled gears 5 and 6, worm that the fusion of the metal parts at the joint f7, worm wheel 8, gear 19 and rack 20; and will be uniform along the whole length of the electrode f is fed by the same motor through joint. This is usually effected in atomic hydrogen Worm 3, Worm wheel 4, bevelled gears 5 and 30 welding by maintaining the arc voltage constant 21, worm 22, worm wheel 23, gear 24 and rack i30 assuming, of course, uniform speed of travel and - 25. Normally, bevelled gear 2 is forced into spacing of the welding electrodes along and from engagement with bevelled gear 5 by means of , the joint as well as uniform arc current and uni a spring 26 compressed between a collar on shaft form flow of gas to the arc region. 27 and the worm 22, but this driving connection It has been observed, however, that when the may be interrupted by withdrawing gear 2 from available heat in the welding region remains un mesh with gear 5 through the agency of knob 28, changed throughout the whole length of the joint, attached to shaft 27. The worm 22 is splined on there is a tendency for the molten metal of the the shaft 2 to which gear 2 and knob 28 are joint, possibly due to surface tension, to leave the attached so that this disengagement may readily 40 finishing end of the joint and flow back toward be accomplished without rotating worm 22. When 40 the middle of the joint, thus leaving a groove at gears 2 and 5 are thus disengaged, the electrode the finishing end. / - may be adjusted independently of electrode It is an object of my invention to eliminate this by turning the knob 28. However, when gears 2 groove at the end of a fusion welded joint by pro and 5 are in mesh, both electrodes O and are 45 viding a method of welding in which a substan simultaneously fed at the same rate by feed :45 tially constant amount of heat is supplied along motor 2 through the gearing just described. The the length of the joint until the weld approaches independent control of electrode through the the end of the joint when the heat is reduced agency of knob 28 thus enables the welding oper sufficiently to complete the weld without having ator to adjust the electrodes relatively to one an the molten metal at the end of the joint flow back other if for any reason they are consumed in the :50 toward the middle of the joint. welding arc at unequal rates. It is a further object of my invention to pro The armature of the electrode feed notor 2 vide a control system for electric fusion welding is connected in Series with its field 29 through the by means of which my above described method contacts of reversing contactors 30 and 3 f to a 55 may be performed automatically. source of supply 32. The operating coils of con 2. 2,175,026 tactors 38 and 38 are connected through the con point of Welding due to the reduced energy of tacts 33, 34 and 35, of a voltage relay 36 to the the arc and consequent reduction of atomic hy same source of supply 32. The operating winding drogen generated. The lower operating voltage of voltage relay 36 is connected across the elec of the arc will depend mainly upon the value of is trodes A and through an adjustable resistance resistance 38 which may be made adjustable to 3, a fixed resistance 38, and the contacts of a provide an adjustment of this lower operating relay 39. The operating coil of relay 39 is con voltage. Thus, for example, supposing the arc nected in series with an arcing circuit 40 through between electrodes 0 and i? is normally main which power is supplied for maintaining an arc tained at a voltage between 60 and 85 Volts, the between the electrodes 0 and f. closure of limit switch 42 may lower the arc The adjustable resistance 37 in circuit with the voltage to a range of 30 to 35 volts. operating winding of the voltage relay 36 is As explained above, the arrangement is Such Shunted by a limit SWitch 42. This limit Switch that the reduced arc voltage, obtained when the may be attached to the work 43 or the work sup limit switch 42 is closed, sufficiently reduces the 36 port 4 by a suitable clamp 45 so that its operat heating of the metal and its fluidity at the end ing member is in the path of travel of a project of a joint to prevent molten metal flowing back ing member A6 attached to the welding head em along the weld to any noticeable extent. It has bodying electrodes 9 and it. Any other means been found that a suitable point at which to may be employed for positioning the limit switch close the limit switch 42 is when the electrodes 2 42 so that the relative movement of the welding are positioned between a quarter and a half inch head and the Work produces a closure of this from the end of the joint being Welded. Switch near the end of the joint being welded. In Although my invention has been described in fact, if an automatic system is not desired, switch connection with a control for atomic hydrogen 42 may be located in any convenient position and welding, it is apparent that as a method of 26 closed manually by the welding operator. fusion welding it is not limited thereto. Fusion The System above described operates as foll welding is performed by electric arcs as Well aS OWS: When an arc is established between the by gas flames. In atomic hydrogen welding both electrodes ?o and by bridging their arcing an electric arc and a gas flame are instrumen terminals with a piece of carbon or by manu talities in the welding operation and, conse 36 ally feeding the electrodes toward one another quently, the performance of my method of Weld until their arcing terminals engage one another, ing by means of atomic hydrogen serves to illus the flow of current through the operating wind trate its application in both fields of fusion ing of relay 39 closes its contacts thus connect Welding. ing the operating winding of voltage relay 36 Furthermore, the system illustrated for auto 35 through resistors 37 and 38 across the arc be matically performing my method of Welding may tween electrodes 0 and . Relay 36 will thus be variously modified to meet conditions encoun be responsive to arc voltage and Will, during tered in performing various welding operations.
Details
-
File Typepdf
-
Upload Time-
-
Content LanguagesEnglish
-
Upload UserAnonymous/Not logged-in
-
File Pages4 Page
-
File Size-