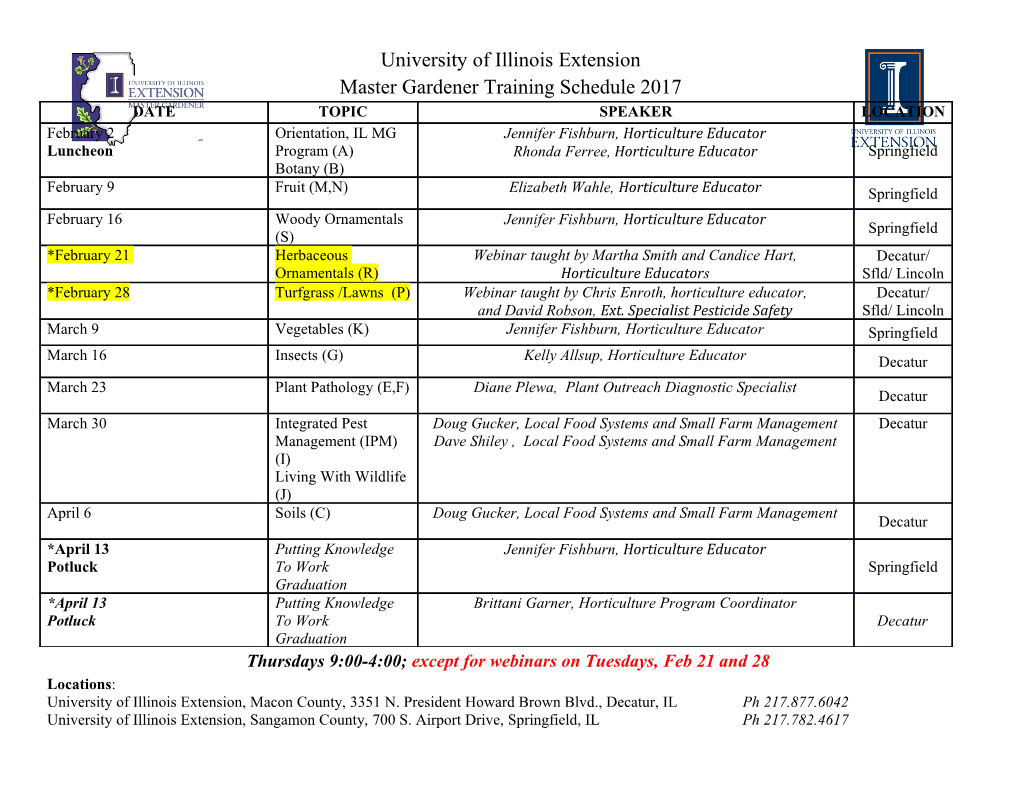
Project TURTLE: Terrapin Undergraduate Rover for Terrestrial Lunar Exploration University of Maryland RASC-AL Presentation June 9-11, 2008 Team TURTLE Avionics Crew Systems Mission Planning and • Andrew Ellsberry •James Briscoe Analysis • Michael Levashov • Sara Fields •David Berg • Joseph Lisee* •AliHusain • Hasan Oberoi • Jacob Zwillinger • Jason Laing* •May Lam •AdamMirvis • Ryan Murphy Loads, Structures, and • Tiffany Russell • Matt Schaffer Mechanisms • Enrique Coello Power, Propulsion, and Systems Integration •Aaron Cox Thermal • Joshua Colver • Stuart Douglas • Jason Leggett •DavidGers •Ryan Levin • Aleksandar Nacev* • Madeline Kirk* • David McLaren* • Ugonma Onukwubiri •Thomas Mariano • Jessica Mayerovitch •StephaniePetillo • Kanwarpal Chandhok •Brian McCall • Ali-Reza Shishineh • Omar Manning • Zohaib Hasnain * RASC-AL Presenters June 9-11, 2008 University of Maryland 2 Project TURTLE Program Rationale • Lunar exploration will become the focus of NASA's future human space program - Constellation Program • Focus mainly on lunar outpost and infrastructure development • Requires dedicated lander-based sortie missions for exploration beyond immediate region of outpost site • System payload constraints limit additional payload for extended range rovers • Project concept: develop a light-weight pressurized rover capable of independent launch and delivery using existing EELVs to augment exploration and science goals of Constellation sortie missions June 9-11, 2008 University of Maryland 3 Project TURTLE TURTLE Project Goals • Design the smallest practical pressurized rover to support Constellation sortie-class missions with independent delivery to moon • Validate critical issues in habitability and crew operations by developing a full-scale mock-up of the rover cabin and external interfaces • Develop a variant of the basic sortie rover to support Constellation outpost construction and operations • Start the design and development process for a fully functional Earth simulation rover for near-term lunar analogue studies 4 TURTLE Overview • 4 wheels, independently steered & powered • Range: 25 km radius around lander over two three-day sorties • Suitports provide astronaut ingress/egress • External Platform – Folds in 3 configurations – Provides suitport access – External driving capabilities • TURTLE total dimensions – Length: 3.45 m – Width: 3.24 m – Height: 2.93 m TURTLE Components • Total initial mass: 1750 kg* * Initial mass does not include astronauts or suits, but does include consumables June 9-11, 2008 University of Maryland 5 Project TURTLE Concept of Operations (Transit) Primary Descent Stage Trans-lunar Injection (LLO – 2 km) Low Lunar Parking Orbit Transfer Engine Separation Descent Stage (2 km) Burn Delta V Delta-IV Heavy to TLI Landing Stage w/ Retro Engine TLI to Low Lunar Parking Orbit 800 m/s Braking Honeycomb Transfer Descent 135 m/s inserts in legs (2 km - 1 m) Retro Engine Braking 1725 m/s crush upon landing Landing 80 m/s Rover Separation Stage (surface) June 9-11, 2008 University of Maryland 6 Project TURTLE Concept of Operations (Mission) Science Goals • Deploy equipment for long- term data collection • Collect data for the lunar base design • Obtain samples for study on Earth • Perform basic analysis of samples on the moon • Increase understanding of lunar habitability Sample Sortie Mission Nasa Image TURTLE will autonomously Two crew members will Upon return, two rendezvous with crew who board TURTLE for a other astronauts will will land less than 10 km three day mission with board TURTLE for a away three EVAs traveling up second three day to 25 km from base mission June 9-11, 2008 University of Maryland 7 Project TURTLE Level One Requirements The following are excerpts from the 25 Level One Requirements initially provided to highlight those with the largest design impacts • Launch on an existing EELV as a stand-alone addition to a Constellation sortie mission • Capable of autonomously driving up to 10 km to rendezvous with the crew • Fully support two astronauts for a pair of three day missions plus 48 hours contingency • Capable of traveling a 25 km radius from the lander with a total travel distance of 100 km between two sortie missions • Accommodate crew size from 95th percentile American male to 5th percentile American female • Support two-person EVAs without cabin depressurization • Have a maximum operating speed of 15 km/hr on flat, level terrain • Accommodate a 0.5 m obstacle at minimal velocity and a 0.1 m obstacle at 7.5 km/hr • Accommodate a 20° slope with positive static and dynamic margins June 9-11, 2008 University of Maryland 8 Project TURTLE Rover Variations There are four rover variations to fulfill separate goals and missions Flight Rover Design Rover Mock-up The baseline rover design Test Full size model of flight rover that fits the requirements Results cabin and suitports for use as listed above for one time use a design tool Field Rover Outpost Rover Fully functional Earth A flight rover designed to based rover to test the concepts of the flight support a lunar outpost rover for multiple missions June 9-11, 2008 University of Maryland 9 Project TURTLE Mock-up Rover Testing Goals • Determine suitport functionality and ease of use • Confirm window placement and sizing Original • Determine most effective interior layout Flight Design – Bed, chairs, driving console, storage Tested in Mockup Modified Flight Design June 9-11, 2008 University of Maryland 10 Project TURTLE Mobility System Wheels • To clear 0.5 m obstacle, wheels have 1 m diameter • Bekker’s Theory was used to determine number of wheels, grousers, and wheel width • Wheels are non-pneumatic Aluminum 2024 Number of wheels 4 Height 1 m Width 0.3 m Drawbar Pull vs Slope for 4, 6, 8 Number of contact grousers 8 Wheels Grouser height 1.5 cm June 9-11, 2008 University of Maryland 12 Project TURTLE Motors • DC brushless motors (TRL 6) mounted to the strut of the suspension system • The motors extend a drive shaft into a 5:1 parallel reduction gear train which is centered in the wheel • Encased in aluminum housing for dust protection Performance Ratings Critical Ratings Nominal Motor Torque 26 N-m Average Power Draw 0.821 kW Max Motor RPM 540 rpm Max Power Draw 6.19 kW Max Torque per Motor 62 N-m Acceleration 0.23 m/s² Efficiency 0.91 Average Waste Heat 48.6 W Total Mass 171 kg Total Length 22 cm June 9-11, 2008 University of Maryland 13 Project TURTLE Steering and Braking •Steering – A linear actuator (TRL 5) mounted on the suspension strut controls the steering of each wheel with a maximum rotation of 60° – Highest power draw from each actuator is estimated at 100 W •Braking – Stopping distance is 4.34 m in 2.1 s from top speed which is determined by crew sight lines – Magnetic braking from motors and friction titanium carbide brakes (TRL 4) June 9-11, 2008 University of Maryland 14 Project TURTLE Suspension & Stability • Independent, MacPherson struts (TRL 4) Reaction to Loads – Required to absorb impact forces from: Case Max Settling • Driving over 10 cm boulder at 7.5 kmph Force Time • Landing on one wheel, 1 m/s impact velocity Landing 28 kN 0.1 s – Spring constant: 35 kN/m Rock Hit 6.5 kN 0.1 s – Damping constant: 1 kN*s/m – Max 15 cm compression – System mass: 120 kg (for 4 wheels) • Stability & performance – Static stability critical angles • 37° longitudinal • 48° lateral – 9.2 m turning radius at 15 kph, on level ground – Pitch and roll angles < 3° during motion over bumpy terrain MacPherson Strut June 9-11, 2008 University of Maryland 15 Project TURTLE Structures Chassis • Aluminum Alloy 6061-T6 (TRL 9) • Loads (Safety Factor = 1.4) – Takeoff: 6g axial, 2g lateral – Forces transferred from suspension – Temperature variation • All members sized to resist buckling, bending, shear, and axial loads with > 15% MOS • 90 separate circular, hollow members Chassis Design • Final mass: 163 kg Critical loads and structural sizes in chassis regions Region Load Critical Load Inner/Outer Safety Source diameter (mm) Margin Shock Tower Driving 180 Nm moment 16/28 0.45 Main Chassis Launch -35 kN axial force 34/52 0.25 Suitport Support Launch 2.3 kNm moment 36/62 0.23 Long. Strut Launch -20 kN axial force 22/42 0.16 June 9-11, 2008 University of Maryland 17 Project TURTLE Cabin: Pressure Shell • Graphite epoxy T300/934 (TRL 9) Region Front Rear Cylinder • Loads (safety factor = 3) Endcap Endcap – Internal pressure Thickness 10 mm 10 mm 8.4 mm – Thermal stress Sources of Window Suitports --- – External loads (drive, land, launch) Extra Stress •Geometry Max Stress 190 MPa 198 MPa 190 MPa – Cylindrical region: 2.43 m long, 1.83 m diameter – Semielliptical endcaps extend 0.325 m • Two layers, enclosing chassis – Inner layer: resists loads – Outer layer: uniform 2 mm thickness to protect against micrometeoroid strike • Margin of safety: 1% (rear endcap) • Total mass 240 kg Inner Shell: Stress from pressure, chassis loads June 9-11, 2008 University of Maryland 18 Project TURTLE Cabin: Additional Structure • Fiberglass grated flooring (TRL 4) – Corrosion, fire, and impact resistant – Eight removable panels – 0.1 mm deflection under 360 N load – Total mass: 33 kg • Driving Window – FOV: 45° L/R, 20° down, 5° up – Two-pane system derived from space shuttle design Driving Window Dimensions • Material TRL 9; System TRL 5 Pane Glass type Thickness Purpose – Vitreloy frame molds to cabin Resist shape Inner Fused silica 20 mm pressure • Material TRL 8; System TRL 4 Heat, micro- – Total mass: 54 kg Alumino- Outer 13 mm meteoroid silicate shield Window Construction June 9-11, 2008 University of Maryland 19 Project TURTLE Crew Systems Cabin Interior Layout 1. First aid kit, AED, supplemental oxygen 9 2 2. Fire extinguishers 6 3. Food / food waste storage 7 3 5 4. Clothing storage 5. Suitports 8 4 6. Computers 6 9 7. Storage locker 1 8.
Details
-
File Typepdf
-
Upload Time-
-
Content LanguagesEnglish
-
Upload UserAnonymous/Not logged-in
-
File Pages55 Page
-
File Size-