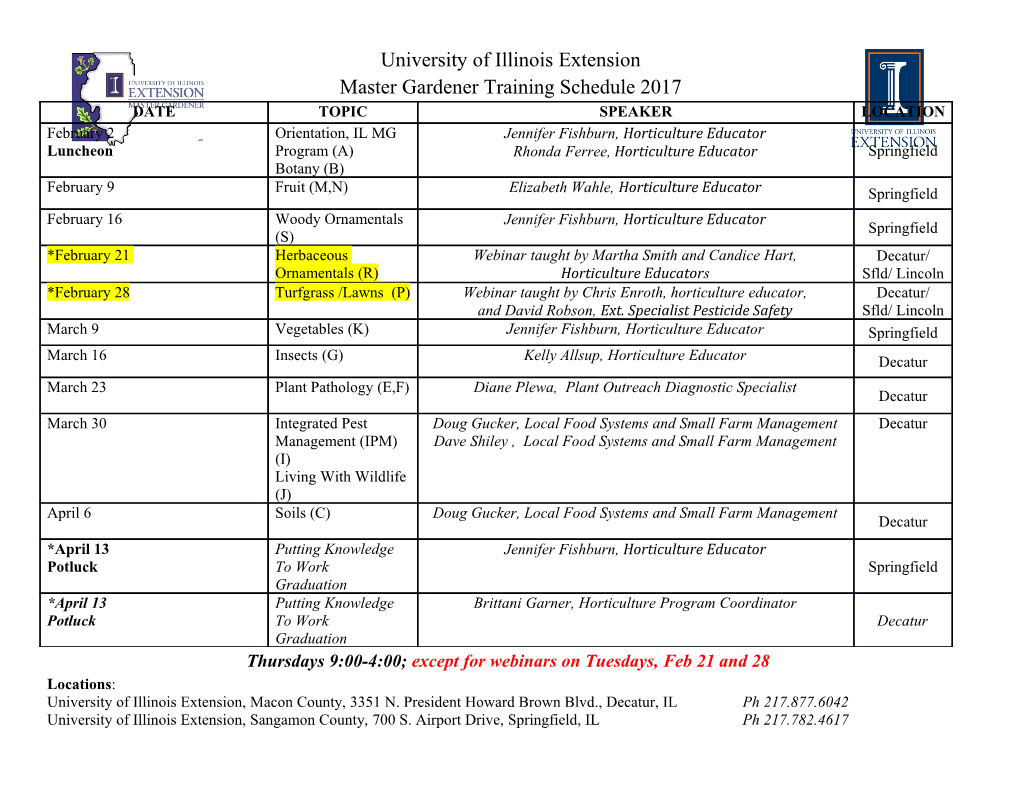
Ocean-Bound Plastics FLAME RETARDANCY 47 [VEHICLE ENGINEERING] [MEDICAL TECHNOLOGY] [PACKAGING] [ELECTRICAL & ELECTRONICS] [CONSTRUCTION] [CONSUMER GOODS] [LEISURE & SPORTS] [OPTIC] From the Sea to Electronics Flame Retardant for Compounds Based on Recycled Ocean-Bound Plastics Plastic waste in the sea has been shaping the negative image of the industry for several years. Various initiatives and mergers of companies have therefore launched projects to tackle this Ocean-bound Plastics (OBP). Components made of OBP could become a symbol for a sustainable use of plastics. For many demand- ing applications, however, such recyclates must also have the necessary flame retardant properties. A recycling project in Haiti shows how these properties can be achieved. ccording to current estimates, 86 mil- Alion t of plastic already circulate in our oceans. There are many initiatives ongoing to collect waste streams and re- cycle plastics, for example polyester fibers for apparel. In this work we describe the use of collected and recycled plastics for flame retarded engineering plastic to be used in electric and electronic equip- ment. One of the best examples for circular economy today is polyethylene tereph- thalate (PET) from bottles. PET recycled grades from bottles can be com- pounded into flame retarded PET or polyester blends and such compounds with recyclates are now spreading into structural parts of electronic equipment. Community collection for bottles in Haiti © HP Flame retardants are added to plastics to prevent ignition or significantly delay the spread of fire. Experts from Lavergne, 60 %), with bottle production accounting fibers can meet the most important fire Montreal, Canada, and Clariant, Muttenz, for about 30 % of the global demand. tests required for electrical and electronic Switzerland, developed flame retarded (E&E) applications, like the Underwriters polyester compounds based on ocean- Flame Retarded Polyester Compounds Laboratories (Northbrook, IL/USA,) UL 94 bound PET. for E&E Applications flammability tests as well as the Glow Wire Ocean-bound plastics are those that Ignition Tests (GWIT) and the Glow Wire are likely to end up in the oceans be- PET and polybutylene terephthalate (PBT) Flammability Test (GWFI). cause they are not properly disposed of. are the most commonly used thermo- Compared to PET, PBT has a lower They are collected in villages and on plastics among polyesters. They are resis- strength, rigidity, and glass transition beaches or coastlines in specific regions tant to solvents, heat-resistant up to temperature. However, it exhibits better – in Clariant’s and Lavergne’s case, these 150 °C and over 200 °C with glass fiber- impact resistance, faster crystallization, are mainly bottles of Caribbean country reinforcement and show good color sta- and better aesthetic properties. More- Haiti (Title figure). bility. Both, PBT and PET, need UV protec- over, it processes at a lower temperature The major portion of OBP is PET, tion if used outdoors, and most grades of profile, which makes it more advantage- which is the most common polyester and these polyesters are flammable, although ous for injection molding applications is used in fibers clothing, bottles and con- additives can be used to improve both UV than PET. Flame retarded PBT com- tainers for liquids and foods, as well as in and flammability properties. Especially pounds with halogen-free flame retar- combination with glass fiber for engin- glass fiber grades can be effectively flame dants show also excellent electrical insu- eering resins. Most of the world’s PET pro- retarded with halogen-free products. lation properties, e. g. comparative track- duction is for synthetic fibers (more than Such compounds with and without glass ing index (CTI) of up to 600 V. That is » Kunststoffe international 5/2020 www.kunststoffe-international.com © Carl Hanser Verlag, Munich. Reproductions, even in extracts, are non permitted without licensing by the publisher. 48 FLAME RETARDANCY Ocean-Bound Plastics Fig. 1. Initial factory facilities are equipped with various tech- used at the start of nology enabling the upcycle of plastic the project to pro- waste. They specialize in formulating, cess Ocean-bound blending, and compounding. The oper- Plastics (OBP) © HP ation begins with post-consumer re- cycled plastics which are transformed into new engineering high-end formulations. The process is carried out to further clean the OBP and make it ready for the com- pounding step, either alone or in a blend with PBT, with other engineering addi- tives and specialty chemicals, Exolit OP from Clariant in this case, to develop en- gineering compounds that can be used in why injection-molded flame retarded PBT that selected Exolit OP grades will be- different high-end applications such as parts have found numerous applications come available as Terra types based on automotive (transportation), and elec- in E&E equipment, more recently also in renewable carbon sources, which allows tronic and electrical equipment. e-mobility, e. g. for high voltage connec- a reduction of the carbon footprint by ca. tors in signal orange color (RAL 2003). 20 % compared to the use of conven- Challenges in Developing and Using tional raw materials. By using OBP com- Compounds Based on Ocean Bound PET Flame Retarded OBP Compounds pounds the plastic carbon footprint can also be significantly reduced. Compared to virgin resins, recycled For ocean-bound PET, experts from the plastics are in-consistent in properties Canadian company Lavergne were able The Process and contaminated with other plastics. to develop flame retarded formulations Therefore, the key to produce engineer- of their recycled polyester grades in close The project initially started in 2016, with ing compounds using such sources is collaboration with Clariant’s specialists. the goal to create a positive environ- steady feedstock, high technology sort- Clariant’s Exolit OP halogen-free phosphi- mental and social impact in Haiti. The aim ing, processing, quality control and the nate flame retardants have a proven track was to improve the working conditions of use of excellent additives. There were record for a very good environmental and Haitians collecting bottles and to provide some special challenges in developing health profile, as documented by the a path out of poverty for the people who the polyester compound based on OBP. GreenScreen Benchmark 3 assessment work in the landfill. One was to find the right balance be- under the NGO Clean Production Action’s The collection process begins when tween the required level of flame retar- assessment tool, which identifies it as a bottles are recovered from canals, road- dancy together with good flowability and good option to use because of its low sides, and the ocean shores. A new op- good mechanical properties. This was hazard, for the key phosphinate ingredi- portunity for 6000 to 8000 individuals achieved by optimizing the flame-re- ent. In October 2019, Clariant announced who are to gather and collect plastics tardant package in the formulation and containers and bottles and sell them to using further additives. The compound the collection centers. The approximately properties could be further improved by 100 collection centers scattered around using additional halogen-free flame re- The Authors the country are equipped with scales and tardant as a synergist, a lubricant and a Dr. Sebastian Hoerold is since 2012 Head proper equipment to handle the first step process stabilizer. PET is also more sensi- of Technical Service Flame Retardants for of separation. This operation is done tive towards thermo-oxidative degrada- Plastics at Clariant Plastics & Coatings manually (Fig. 1), in order to provide em- tion and hydrolysis than PBT, thus, pre- Deutschland GmbH, Gersthofen, Germany. ployment and economic opportunities drying was essential for the final com- Yoan Lavergne is Marketing Director at for the citizens. pound quality. Lavergne, Montreal, Canada. Once sorted and separated, the Lavergne’s new flame retarded com- plastic waste is transported to a central pound VYPET OBP-FR contains 30 % Lavergne factory in the capital of Haiti glass fiber and has obtained UL 94 V-0 Service Port-Au-Prince, where the material is flame rating at 0.8 mm thickness with shredded into small flakes. A series of ex- flexural strength that exceeds 140 MPa, Digital Version tensive washing, rinsing and drying is per- which makes it suitable for most E&E ap- B A PDF file of the article can be found at formed to clean the material. The wash plications, such as structural and aes- www.kunststoffe-international.com/2020-05 line allows Lavergne to divert three types thetic parts. It benefits from high stiff- German Version of plastics from the ocean, PET, HDPE ness and strength and low mold shrink- B Read the German version of the (high density polyethylene), polypropy- age of PET and good flowability and fast article in our magazine Kunststoffe or at lene (PP), respectively. The clean flakes are crystallization of PBT. Such a polyester www.kunststoffe.de then shipped to Lavergne facilities in glass filled compound reflects a balance North America. Lavergne’s transforming of high stiffness, impact resistance and © Carl Hanser Verlag, Munich Kunststoffe international 5/2020 © Carl Hanser Verlag, Munich. Reproductions, even in extracts, are non permitted without licensing by the publisher. Ocean-Bound Plastics FLAME RETARDANCY 49 3.0 70 130 % % % 2.5 60 120 55 110 2.0 50 45 100 40 Tensile strength Tensile
Details
-
File Typepdf
-
Upload Time-
-
Content LanguagesEnglish
-
Upload UserAnonymous/Not logged-in
-
File Pages3 Page
-
File Size-