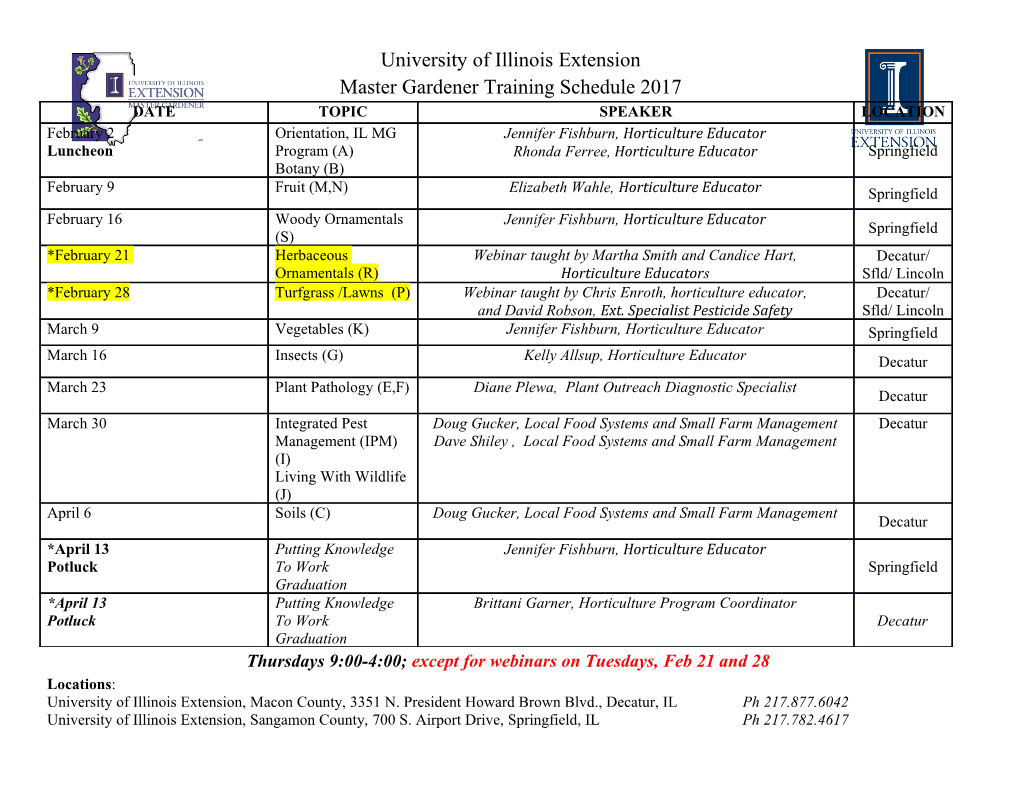
energies Article Simulation of the Optimal Refrigerated Floor Design for Ice Rinks Wenjie Zhou 1,2, Zhihua Gan 1,* and Lei Han 3 1 Institute of Refrigeration and Cryogenics, Zhejiang University, Hangzhou 310027, China; [email protected] 2 Hangzhou Forstar Special Material Corporation, Hangzhou 310018, China 3 School of Mechanical and Electrical Engineering, Wenzhou University, Wenzhou 325035, China; [email protected] * Correspondence: [email protected]; Tel./Fax: +86-517-87951930 Abstract: A good design of the ice rink floor could save a great deal of capital and operational costs for hockey arenas. This ice rink floor design focuses on a cost-effective tube arrangement and an optimal concrete coverage over the tubes that could provide sufficient heat transfer rate between the coolant and the freezing ice. This paper reports a theoretical model to simulate the heat transfer characteristic of a different tube diameter, spacing distance, and thickness of the concrete coverage of the tubes of an ice rink. In addition, calcium chloride and ethylene glycol with water solutions are compared to figure out the pros and cons of these two secondary coolants. This model prediction is compared to the typical ice floor arrangement in order to determine the best floor construction scenario. Keywords: heat transfer; optimal floor design; ice rink 1. Introduction Citation: Zhou, W.; Gan, Z.; Han, L. Simulation of the Optimal Ice rinks are among the most energy consuming public facilities needing refrigeration, Refrigerated Floor Design for Ice heating, ventilation, and air conditioning. The refrigeration system accounts for almost Rinks. Energies 2021, 14, 1535. 43% of the total operational cost for a typical ice rink arena [1]. Increasing the efficiency https://doi.org/10.3390/en14061535 of the refrigeration system could potentially save a large amount of annual energy cost. There are several loads in the ice rink [2–4]: envelope, radiation, lighting, comfort cooling, Academic Editor: Alessandro Mauro heating, convection, re-condensation heat transfer to the ice slab, etc. The optimal ice rink refrigerated floor design could save capital investment cost as well as energy and long-term Received: 4 February 2021 operational cost. Accepted: 6 March 2021 Recently, there have been several studies focusing on improving the energy efficiency Published: 10 March 2021 of the ice rink. Nilsson [5] investigated the performance of carbon dioxide as secondary coolant for the ice rink refrigeration system. Ahmed [6] presented three theoretical models Publisher’s Note: MDPI stays neutral to predict the heat transfer, the airflow patterns, and the humidity distribution in a 3D with regard to jurisdictional claims in section for an ice rink. Their simulations are consistent with published Computational published maps and institutional affil- Fluid Dynamics (CFD) and experimental results. Krarti, Mun, and Lin [7–10] published iations. several papers about the heat transfer behavior and thermal insulation layer beneath the ice rink floors. Their models and study approaches demonstrate a good explanation of the heat transfer phenomenon underneath the ice rink floors. Hepbasli and Caliskan [11] used energy and exergy analysis for ice rink buildings at varying reference temperatures. The Copyright: © 2021 by the authors. total exergy input rate is 253.66 kW with the exergy destruction rate of 227.45 kW from the Licensee MDPI, Basel, Switzerland. simulation. Radermacher and Wang [12] reviewed the secondary loop refrigeration system This article is an open access article with carbon dioxide as the coolant. Galanis and Seghouani [13,14] studied a case of the distributed under the terms and interaction between an ice rink and its refrigeration system. They found that it is possible conditions of the Creative Commons to save energy by reducing the ceiling emissivity and increasing the coolant temperature Attribution (CC BY) license (https:// without affecting the quality of the ice. Zmeureanu and Teysedou [15,16] developed a creativecommons.org/licenses/by/ benchmarking model to simulate the operational parameters of a commissioning ice rink 4.0/). Energies 2021, 14, 1535. https://doi.org/10.3390/en14061535 https://www.mdpi.com/journal/energies Energies 2021, 14, 1535 2 of 12 facility. Kuyumcu [17] reported the energy performance of the swimming pool and ice rink coupled system. The previous research focuses on the model simulation and experimental study of the entire ice rink arena. Although the American Society of Heating Refrigerating and Air-conditioning Engineers (ASHRAE) refrigeration handbook provides some rough recommendations on the cooling load of the ice rink, researchers rarely reported optimal ice rink floor arrangement that delivered a sufficient amount of cooling during the steady state operation. In addition, in the construction phase of the refrigerating concrete floor, it is often difficult to tell whether the designed floor piping arrangement could potentially deliver enough cooling and save the owner’s capital and operational costs. Therefore, it is worthwhile to conduct a theoretical study of the heat transfer behavior of the pipe floor at the steady state condition so that it can provide guidance for the ice rink construction and operation. The paper provides a good sample study of the best ice rink floor refrigeration design, promoting both economical operation and easy maintenance of the hockey arena. There are four sections in this paper including this Introduction. Section2 provides a theoretical heat transfer model for the pipe, secondary coolant, concrete, and ice. Section3 analyzes the cooling capacity influenced by the material and diameter of the pipe and distance between the pipes. The cooling performance affected by the thickness of the concrete and different refrigerant is also discussed in Section3. Section4 delivers the preliminary results of the study. 2. Ice Rink Discrete Thermal Resistance Circuit Model The refrigeration system is regarded as the core of the ice rink because it is responsible for the quality of the ice. The ice rink refrigeration system could be direct, indirect, or a combination of both called a partly indirect system. In the direct system, the refrigerant is pumped directly below the ice pad, and all of the primary coolant pipes are regarded as a huge evaporator. The direct system is less often used because there is a need for a massive refrigerant charge such as R22, R407C, R510A, or ammonia. R22 is banned now in many countries because of its large global warming potential and ozone depletion potential. Ammonia has a charge limit because of its hazards and cannot be used in a large system including the ice rink direct system. The indirect system consists of primary and secondary refrigeration systems. This is the most conventional approach for an ice rink. The secondary coolant is known as “brine”. It is pumped below the ice pad and returned to the evaporator. The partly indirect system has either an evaporator or condenser connected to the sink or source by a secondary fluid for heat exchange. In a partly indirect system, some portion of the cooling is also provided by a direct system. For the typical hockey rink, as shown in Figure1, the total length of the ice-covered space is 61 m and the width is 26 m [18]. Its area is around 1586 m2. The half layout of the typical hockey rink is shown in Figure1. The insulation pad is installed between the low temperature concrete and the normal temperature concrete to prevent cooling loss from ice to the curb. Either steel or polyethylene pipes are embedded underneath the ice surface inside the concrete to provide continuous cooling to the solid ice to ensure that the high-quality ice is evenly distributed. The secondary coolant in the pipes is typically ethylene glycol or brine water solution. Both have a low freezing point and good thermal properties. The pipe delivering the secondary coolant to the ice pad serves as a heat exchanger between ice and coolant. The geometry, characteristics of the fluid, and the concrete are important parameters affecting the performance of the embedded heat exchanger. In the ice-rink experiments, some parameters need to be measured, such as temperatures, geometry parameters, and the mass flow of the secondary coolant etc. Other parameters such as thermal properties of the materials can be determined by the standard properties. A thermal resistance network heat transfer model is proposed to study the performance of this heat exchanger. The cross-section area of the pipe is shown in Figure2. The thickness of the ice is shown as thice. The rink pipes are embedded inside the concrete, and their surface is thcu away from the top of concrete. The two layers of vapor retarder are Energies 2021, 14, 1535 3 of 12 built on the top and bottom surface of the isolation material, as shown in Figure2, and are used to prevent the moisture migrating to the freezing concrete. The insulation material underneath the refrigerated concrete isolates the heated concrete and the refrigerated concrete. The warm glycol or brine pipe is embedded in the heated concrete to avoid heaving of the ice rink. Figure 1. Typical hockey rink geometry parameters (half layout). Figure 2. Cross section area of typical ice rink. The largest cooling load demand, typically around 560 kW, is during the last period of the hockey game. Figure3 illustrates the discrete thermal resistance network model for the ice rink. The model conducts a steady state heat transfer model for the largest load demand. The radiation load from the ceiling, the convection heat transfer between air and ice pad, and the envelop load are not modeled here because the model is built to simulate the steady state condition for the maximum load demand. These loads affect the ice surface temperature which is the highest concern for the hockey game. Therefore, the ice surface is maintained at −3 ◦C and concrete temperature is around −5 ◦C.
Details
-
File Typepdf
-
Upload Time-
-
Content LanguagesEnglish
-
Upload UserAnonymous/Not logged-in
-
File Pages12 Page
-
File Size-