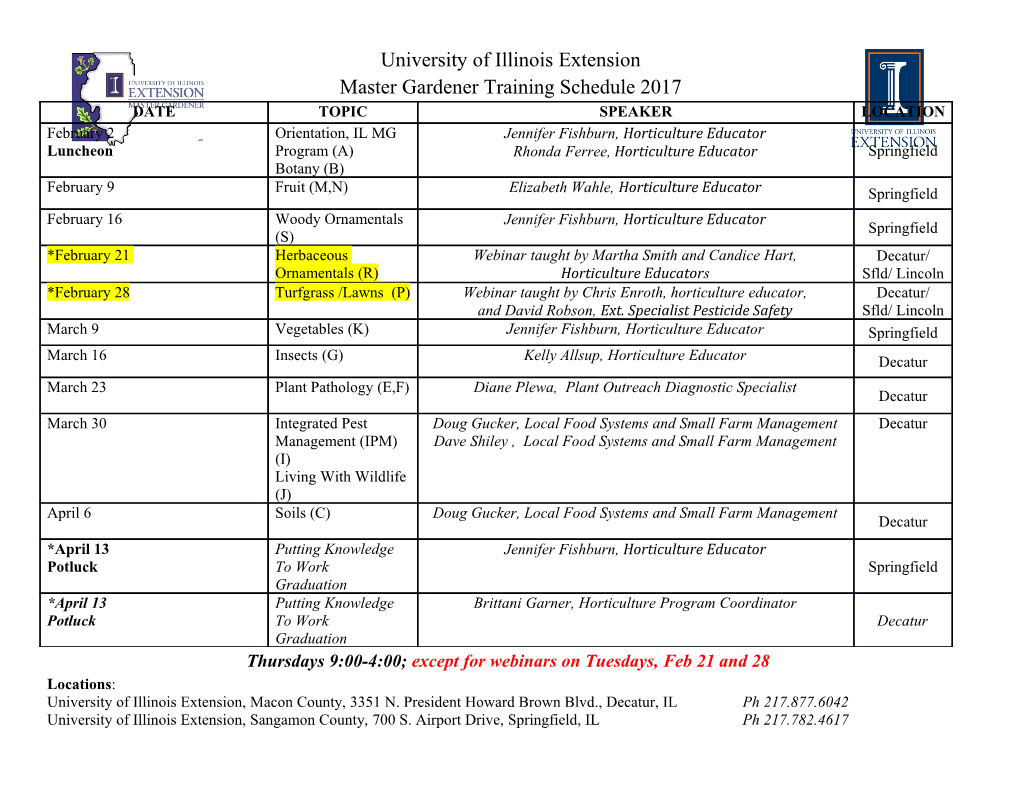
Development of Filler Metals and Procedures for Vacuum Brazing of Aluminum Several brazing filler metal compositions have been developed which offer significant improvements over existing compositions. They braze in vacuum at temperatures lower than normal flow temperatures and have equal or better flowability BY W. J. WERNER, G. M. SLAUGHTER AND F. B. GURTNER Introduction ry cleanliness levels under production vantages. As a single entity, it was This report documents work per­ conditions. The maximum allowable immediately more desirable from a formed toward the development of lag between cleaning and brazing was cleaning, assembling and material found to be 12 hours. handling standpoint. Metallurgically, new brazing filler metals for vacuum- 2 fluxless brazing (1 X 10~6 torr) C. S. Beuyukian developed tech­ the 4045 brazing filler metal with its certain aluminum alloys of interest to niques for vacuum or inert gas fluxless lower silicon content allowed greater the Army. The base metals under brazing of aluminum cold plates for latitude in processing parameters than consideration were alloys 6061, 2219, use in Apollo command modules. In did alloy No. 718. 7075 and 2024. Brazing filler metal this work, brazing filler metal No. 718 Finally, the workers at Aeronca, and No. 23 brazing sheet were evalu­ Inc. completed a study on inert gas flow temperatures needed for these 3 alloys encompass the temperature ated. Alloy No. 718 is nominally 88% brazing of aluminum in early 1967. range 900 to 1200F. Specifically, the aluminum, 12% silicon; No. 23 braz­ Their work was concerned with de­ contract called for the development of ing sheet is comprised of 6951 base velopment of high strength brazed alloys with flow temperatures of 950, alloy clad on one side with 4045 aluminum honeycomb structures 1000, and 1050F. Finally, corrosion brazing filler metal—nominally 90% which would withstand a range of compatibility of the brazing filler met­ aluminum, 10% silicon. Base metals cryogenic (—423F) through elevated al with certain chemical agents was 6061 and 5052 were considered for (600F) temperatures. All of the base necessary and to this end a survey of the main body of the assembly. metals involved in the study, X7005, potentially compatible elements com­ In general, better results were ob­ X7106, and 7039, began to melt with­ piled by the contractor was utilized. tained using vacuum. The techniques in the range of 1080 to 1120F. As a result, a 1050F maximum flow tem­ We began the investigation with a developed are unique in that stringent flatness requirements placed on the perature for the brazing filler metal survey of the literature. Unfortunate­ was needed. ly, there is very little published work assembly by design required that braz­ on fluxless-vacuum and/or inert gas ing operations be performed in heated Three commercial brazing alloys brazing of aluminum. M. M. platen presses at moderate pressures. were evaluated in combination with Schwartz1 et al showed the feasibility The use of pressure during brazing the aforementioned base metals— of vacuum fluxless brazing production undoubtedly influenced oxide penetra­ 716, 718, and 719. Number 716 con­ quantities of aluminum alloy 6061 tion and/or displacement during the tains nominally 86% aluminum, 10% containers of helium leaktight quality brazing operation. Production brazing silicon, and 4% copper; 718 contains by closely controlling process parame­ was carried out in the temperature nominally 88% aluminum, 12% sili­ ters using a commercial brazing filler range 1055 to 1095F using brazing con; and 719 contains nominally 76% metal. Brazing alloy No. 718 (nomi­ times of at least 10 minutes. aluminum, 10% silicon, 10% zinc and nally 88% aluminum, 12% silicon) Under these conditions, aluminum 4% copper. It was found that the was used. This alloy is widely used alloy 6061 was preferred over 5052 aluminum-silicon brazing alloys per­ commercially for both dip and fur­ because alloy 5052 exhibited a greater formed best as claddings. nace brazing and is available in both susceptibility to intergranular penetra­ The researchers developed several wire and foil form. As might be ex­ tion by silicon. Use of alloy 5052 new brazing filler metals during the pected, the success of the endeavor would therefore have required more course of their investigation. Two in was largely due to the use of laborato- rigid time-temperature control during particular showed promise. Both al­ the brazing cycle. In addition, silicon loys had a base composition of 68% diffusion resulted in embrittlement of aluminum, 7% silicon, 15% germani­ MESSRS. WERNER and SLAUGHTER are 5052. um; their compositions were modified with the U.S. Atomic Energy Commission. Tenn. which is operated by Union Carbide No. 23 brazing sheet was chosen with 10% zinc, and 10% silver, re­ Corp. MR. GURTNER is with the Dept. for production over the combination spectively. Both alloys brazed at ot the Army, Technical Support Directo­ rate. Industrial Operations Div., Edge- of brazing alloy Nos. 718 and 6061 1020F. These new alloys looked espe­ wood Arsenal, Md. for both metallurgical and process ad­ cially good in combination with 64-s ] FEBRUARY 1972 Table 1—Nominal Compositions, Li mits and Melting Ra nges of Alloys Under Con sideration Approximate . - Composition weight pe -, melting Alloy designation Si Fe Cu Mn Mg Cr Zn Ti range, °F 6061 (limiting) 0.40-0.8 0.7 0.15-0.40 0.15 0.8 -1.2 0.04-0.35 0.25 0.15 1080-1200 6061 (nominal) 0.6 — 0.27 — 1.0 0.20 — — 1080-1200 22191 (limiting) 0.20 0.30 5.8 -6.8 0.20-0.40 0.02 — 0.10 0.20-0.10 1010-1190 22192 (nominal) — — 6.3 0.30 — — — 0.06 1010-1190 7075 (limiting) 0.40 0.50 1.2 -2.0 0.30 2.1 -2.9 0.18-0.35 5.1 -6.1 0.20 890-1180 7075 (nominal) — — 1.6 — 2.5 0.30 5.6 — 890-1180 2024 (limiting) 0.50 0.50 3.8 -4.9 0.30-0.9 1.2 -1.8 0.10 0.25 — 935-1180 2024 (nominal) — — 4.4 0.6 1.5 — — — 935-1180 1 Vanadium 0.05-0.15, zirconium 0.10-0.25 "- Vanadium 0.10, zirconium 0.18 X7106. Alloy 719 remained the num­ industrially; and alloys with magnesium eter. Our measurements show that it ber one choice for brazing X7005. contents greater than 2.5% are con­ takes 25 minutes for the sample to sidered unbrazeable. This is due to the reach brazing temperature after the Materials fact that state-of-the-art fluxes do not furnace is pushed onto the muffle. The Table 1 shows the nominal com­ remove the tenacious oxides formed variation in temperature setting was positions and compositional limits of on these alloys. found to be ±5F. It is believed that the base metals under consideration in the inherently poor heat transfer char­ the program, along with their melting Equipment and Experimental acteristics of a vacuum are responsible ranges. Joining of alloys 6061 and Procedure for the 15-minute delay between con­ 2219 is accomplished industrially by The vacuum furnace apparatus for troller indication of the attainment of dip or furnace brazing techniques both flow temperature and wettability de­ brazing temperature and the actual at­ of which employ liberal amounts of terminations is shown in Fig. 1. The tainment of brazing temperature since flux. In addition, alloy 6061 has also system is capable of maintaining a the sensing couple for the controller been brazed without flux using vacu­ vacuum of 1 X 10~r> torr at brazing is outside of the vacuum. um and/or inert atmospheres.1* 2 As temperature. The picture shows the The majority of our brazing filler a result, good cleaning and handling furnace rolled back off the muffle. In metal wettability and flowability de­ procedures are not a problem with a typical brazing cycle the specimen is terminations were done using V2 by these two alloys. In fact, cleaning placed into the cold muffle. After V2 by V16 in. 6061 aluminum base procedures are available in the Metals pump-down, the heated furnace is metal pads. Those tests that were run and Ceramics Division for both of rolled onto the muffle, and the work on the other base metals of interest these alloys since they are routinely very rapidly comes to temperature. were performed on this same standard hot roll-bonded into dispersion type After holding for the proper brazing pad size. Both the pads and the exper­ fuel plates using standard picture time, the furnace is rolled off the imental brazing filler metals were frame techniques. muffle. Simultaneous with the former cleaned prior to undergoing a thermal Alloys 7075 and 2024, on the other operation, helium can be admitted to cycle for determination of melting hand, are not considered brazeable facilitate rapid cooling or quenching temperature and wettability. using established commercial tech­ of the test assembly. Diffusion effects Attention to cleanliness is of prime niques and commercial brazing filler can probably be limited by both of importance to the fluxless brazing alloys. In the first place, both alloys these operations. process. Aluminum oxide forms on have melting points below the flow A typical time-temperature re­ "clean" aluminum surfaces immedi­ temperatures of the commercial braz­ sponse curve for the furnace is shown ately at room temperature. This oxide ing filler metals (Table 1). Secondly, in Fig. 2; the temperature measure­ is one of the most stable known. Its both alloys contain appreciable ments indicated are those of an actual melting point is approximately 3700F, amounts of magnesium (2.5 and sample. Chromel-P versus alumel and it is not reduced by heat and/or 1.5%, respectively).
Details
-
File Typepdf
-
Upload Time-
-
Content LanguagesEnglish
-
Upload UserAnonymous/Not logged-in
-
File Pages7 Page
-
File Size-