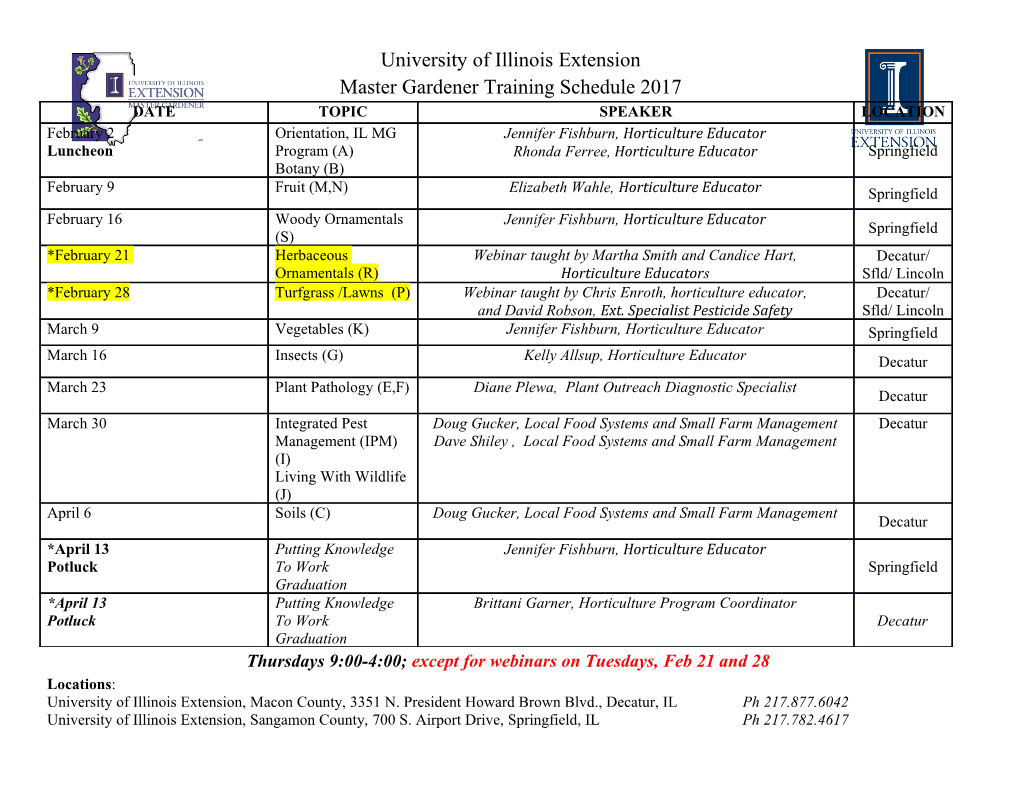
BHR Group Limited Cranfield Bedford MK 43 OAJ United Kingdom Telephone: (0234) 750422 British Hydromechanics Research Group Technical Paper Series Full Power Hydraulic Brake Actuation, Circuit Design Considerations for Off-Highway Vehicles and Equipment David E. Keyser MICO, Inc. Presented at the 10th International Conference on FLUID POWER the future for hydraulics 5 - 7 April 1993 FULL POWER HYDRAULIC BRAKE ACTUATION, CIRCUIT DESIGN CONSIDERATIONS FOR OFF-HIGHWAY VEHICLES AND EQUIPMENT D. E. Keyser MICO, Incorporated 1911 Lee Boulevard North Mankato Minnesota USA 56003-2507 FULL POWER HYDRAULIC BRAKE ACTUATION, CIRCUIT DESIGN CONSIDERATIONS FOR OFF-HIGHWAY VEHICLES AND EQUIPMENT ABSTRACT Standards Organization (ISO) and the Society of Auto- motive Engineers (SAE) can provide recommended The intent of this paper is to create a clear understand- vehicle brake system performance specifications. Infor- ing of full power hydraulic brake actuation system mation on laws that regulate vehicle brake performance design as it relates to off-highway vehicles and equip- can be obtained from Federal, State, and Provincial ment. The paper is divided into four main sections. The Government agencies. Actual vehicle performance is first section outlines six design prerequisites used for determined by the vehicle designer. It will be the vehicle selecting the service brakes and the full power brake designer's responsibility to insure a proper testing actuation system. The second section, Brake Actuation program is defined and conducted to insure validation Systems, includes advantages of a full power brake of the components selected for use in the brake system and a brief description of reverse modulation actuation system. brake systems. Section three is a discussion of open center, closed center and load sensing hydraulic BRAKE TORQUE AND KINETIC ENERGY systems and the integration of a full power brake REQUIREMENTS - The brake torque and kinetic actuation system into these systems. Section three energy required to stop the vehicle is calculated based also explains the operation, related components and on the desired stopping parameters and the vehicle some common problems to be avoided in the actuation specifications. Vehicle specifications include, but are system design process. The fourth section describes not limited to, the gross vehicle weight, vehicle velocity, reverse modulating brake actuation and how it differs static loaded radius of the tires, gear reductions from full power hydraulic brake actuation. between the brake and the ground, the number of braked wheels, the number of brakes to be used and The actual selection of the service brakes is beyond the the road surface. Of the specifications mentioned, scope of this paper. However, it is assumed the vehicle velocity will have the greatest impact on the vehicle's brakes have been properly sized and are fully brake torque and kinetic energy. For example, if vehicle operational. The brakes are referred to throughout to velocity is doubled, the magnitude of the kinetic energy emphasize the importance of their relationship to the is multiplied by a factor of four. Where as, an increase brake actuation system. in vehicle mass will result in a directly proportional increase in kinetic energy, reference 1. DESIGN PREREQUISITES There are many sources for formula's used to calculate brake torque, kinetic energy and the factors that affect The goal of the brake actuation system designer is to them, two of which are given in references 2 and 3. select the proper components to provide optimum brake performance for a given application. To do this the SERVICE BRAKE CAPACITY - Identifying the designer must start at the vehicle service brakes and service brake capacity is the process of matching the “work backward” to the method of actuation. Specific service brake(s) to the vehicle stopping parameters and design prerequisites for the vehicle brakes as well as brake torque requirements. The available brake torque the brake actuation system must be identified. The six is expressed at a given brake line pressure which key prerequisites that will be discussed are: (1) vehicle allows the designer to identify the proper amount of stopping parameters, (2) the resultant brake torque and brake line pressure required to match the vehicle torque kinetic energy required, (3) service brake capacity, requirements. The service brake capacity information is (4) brake line pressure, (5) brake volume and (6) acquired from the brake and or axle manufacturer and operator input effort. the torque versus pressure relationship is generally a linear function. STOPPING PARAMETERS - The stopping parame- ters are identified as performance attributes associated To avoid the pitfalls of either under-braking or over- with stopping the vehicle. They will include, but are not braking it is important to calculate the actual required limited to, the deceleration rate, stopping distance, torque for the application. Do not assume that the percentage of grade for operation and vehicle velocity. manufacturer's specified maximum brake line pressure Information used in determining these properties can be is the same as the required brake line pressure. procured from professional organizations, government This can be demonstrated in the following examples; agencies and the vehicle designer. one in which the vehicle brake torque requirement is Professional organizations such as the International above the torque limitations of the service brake. In the 1 other, the vehicle torque requirement is below the maximum brake line pressure or maximum desired torque capacity of the service brake. brake torque. Again, there are directing organizations and agencies that make recommendations to assist in Consider a vehicle that requires 680 N-m of brake identifying this value, references 5 and 6. More impor- torque. The torque limitation of the service brake is tantly, the pedal effort must comply with the operator's 450 N-m at a maximum pressure of 70 bar. Supplying ability to effectively control the machine. the maximum 70 bar and consequently generating 450 N-m of brake torque, does not stop the vehicle as required. The vehicle is under-braked. BRAKE ACTUATION SYSTEMS Conversely, consider if the torque requirement is now The system designer can accomplish brake actuation in 110 N-m and the brake is rated for 450 N-m at 70 bar. different ways. One method is the classical method of Supplying the maximum 70 bar will stop the vehicle brake actuation which uses fluid pressure to actuate the immediately (too severely). In this example, the torque braking means. Full power hydraulic brake actuation is requirement is satisfied with 25% of the available pres- a direct means of supplying hydraulic pressure to the sure resulting in aggressive, oversensitive brakes. brakes. This method uses fluid pressure and flow These scenarios will change in magnitude depending generated by the pump of a hydraulic system and on the method of actuation that is selected (reference directs this energy to the service brakes. 4) and the type of brakes on the vehicle. FULL POWER HYDRAULIC BRAKE SYSTEM Through proper brake actuation and circuit design the ADVANTAGES - The full power hydraulic brake system designer can match the actuation circuit to the service has several advantages over traditional brake actuation brakes and avoid poor performance characteristics. systems. These systems are capable of supplying fluid to a range of very small and large volume service BRAKE LINE PRESSURE - The brake line pres- brakes with actuation that is faster than air brake sys- sure, as previously mentioned, is determined by tems. Figure 1 represents a time comparison between a matching the brake torque requirement to the service typical air/hydraulic and full power hydraulic brake brake capacity. By examining the brake torque versus actuation system. brake pressure relationship, the designer can extrapo- Figure 1 late the brake line pressure required to attain brake performance matched to the vehicle stopping parame- ters. The brake line pressure will also used in selection of the hydraulic system pump, determining the system relief valve pressure setting, accumulator dry nitrogen precharge, accumulator charge valve (in open center systems), and the brake modulating valve pressure setting. REQUIRED VOLUME - The brake volume require- ment is critical in determining the method of brake actuation to be used and in component selection. The designer needs to know the minimum, nominal, and maximum volume of fluid required. Different types of actuation components are used in various ranges of brake volume displacements. The brake volume is also used to determine the capacity of the accumulators and the accumulator charge valve charge rate with respect to the desired number of power-on and power-off stops. In open center and load sensing applications that use an accu- mulator charging valve, power-on stops are defined as the number of brake applications that can be attained Response Time between the high and low accumulator charge limit Full Power Brake Actuation settings. Power-off stops are defined as the number of -VS- stops that can be attained between the low accumulator Air/Hydraulic Brake Actuation charge limit setting and the maximum brake line pres- sure with the energy source disconnected. Full power systems can supply significantly higher OPERATOR INPUT EFFORT - Input pedal force brake pressures with relatively low reactive pedal required by the operator is generally expressed
Details
-
File Typepdf
-
Upload Time-
-
Content LanguagesEnglish
-
Upload UserAnonymous/Not logged-in
-
File Pages14 Page
-
File Size-