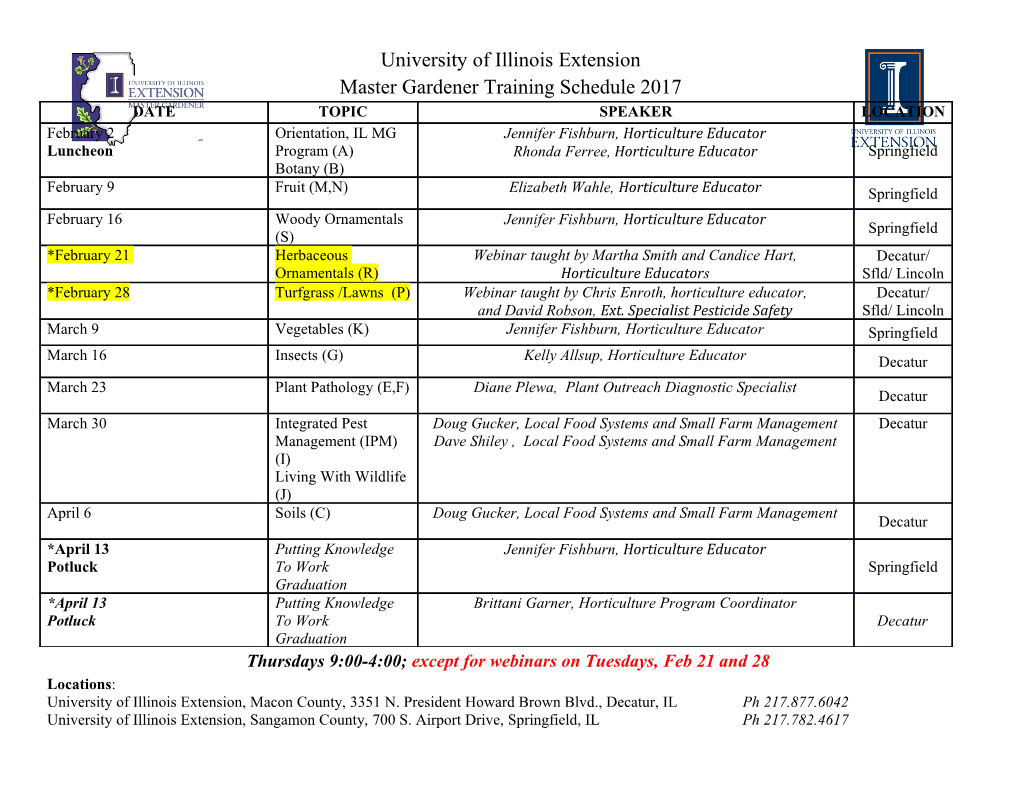
g GER-4206 GE Power Systems Combined-Cycle Development Evolution and Future David L. Chase GE Power Systems Schenectady, NY Combined-Cycle Development Evolution and Future Contents Introduction . 1 Gas Turbine Combined-Cycle Features . 1 Gas Turbine Combined-Cycle Development . 5 First Generation Combined-Cycle Plants. 5 Second Generation Combined-Cycle Plants . 6 Third Generation Combined Cycles. 6 Fourth Generation Combined-Cycle Plants . 9 References. 13 List of Figures . 13 List of Tables . 13 GE Power Systems I GER-4206 I (10/00) i Combined-Cycle Development Evolution and Future GE Power Systems I GER-4206 I (10/00) ii Combined-Cycle Development Evolution and Future Introduction Combined-cycle systems that utilize steam and air-working fluids have achieved widespread Combined-cycle systems utilizing the Brayton commercial application due to: Cycle gas turbine and the Rankine Cycle steam system with air and water as working fluids 1. High thermal efficiency through achieve efficient, reliable, and economic power application of two complementary generation. Flexibility provided by these sys- thermodynamic cycles. tems satisfies both utility-power generation and 2. Heat rejection from the Brayton Cycle industrial-cogeneration applications. (gas turbine) at a temperature that Current commercially available power-genera- can be utilized in a simple and tion combined-cycle plants achieve net plant efficient manner. thermal efficiency typically in the 50–55% LHV 3. Working fluids (water and air) that are range. Further development of gas turbine, readily available, inexpensive, and high-temperature materials and hot gas path, non-toxic. metal surface cooling technology show promise for near-term future power generation com- These combined-cycle systems provide flexibili- bined-cycle systems capable of reaching 60% or ty with features that include: greater plant thermal efficiency. Additional gas 1. High Thermal Efficiency - Combined- turbine technological development, as well as cycle thermal efficiency is higher than increases in steam-cycle pressure and tempera- that of other conventional power ture and steam-turbine stage-design enhance- generation systems. ment, is expected to achieve further STAG™ 2. Low Installed Cost - Combined-cycle combined-cycle efficiency improvement. equipment is pre-engineered and factory- Current General Electric STAG™ (trade name packaged to minimize installation time designation for the GE product line of com- and cost. All major equipment (gas bined-cycle systems) product line offerings, turbine generator, heat recovery steam combined-cycle experience, and advanced sys- generator [HRSG], and steam turbine tem development are used to demonstrate the generator) is shipped to the field as evolution of combined-cycle system technology. assembled and tested components. Auxiliary equipment, such as condensers, Gas Turbine Combined-Cycle Features can be shipped factory-tubed and hydro- The combination of the gas turbine Brayton tested. This greatly reduces the inventory Cycle and the steam power system Rankine of parts that must be managed in the Cycle complement each other to form efficient field and minimizes installation cost. combined-cycles. The Brayton Cycle has high Combined-cycle equipment cost is higher source temperature and rejects heat at a tem- than that for conventional steam plants perature that is conveniently used as the energy due to pre-engineering; however, source for the Rankine Cycle. The most com- combined-cycle plant installation costs monly used working fluids for combined cycles are significantly lower, resulting from the are air and steam. Other working fluids (organ- reduced installation cycle. ic fluids, potassium vapor, mercury vapor, and 3. Fuel Flexibility - Combined-cycle others) have been applied on a limited scale. plants operate efficiently by burning a GE Power Systems I GER-4206 I (10/00) 1 Combined-Cycle Development Evolution and Future wide range of fuels, ranging from clean models, enabling high efficiency natural gas and distillate oil fuels to ash- operation at part load through reduction bearing crude oil and residual oil fuels. in turbine airflow. This is accomplished Operation with coal-derived gas fuels has at nearly constant turbine exhaust been applied in many commercial-size, temperature, so that design steam combined-cycle systems. conditions and low stack loss can be 4. Flexible Duty Cycle - Combined-cycle maintained to provide excellent part-load systems provide flexibility in operation efficiency. for both baseload and mid-range duty 5. Short-Installation Cycle - Combined- with daily startup. Gas turbines in multi- cycle plants can be installed and shaft, combined-cycle configuration can operated in less time than that required be started quickly, bringing about two- for conventional steam plants. Again, this thirds of plant power on-line, typically in is primarily due to the pre--engineering Figure 1. STAG 209E combined-cycle part load performance less than 60 minutes. Combined-cycle and packaging of major components in plants also provide efficient operation at the factory. Phased installation of the part load, particularly for multiple gas plant, when gas turbines are installed and turbine combined-cycle systems. This is il- op-erated in the simple-cycle mode lustrated by the variation in plant output during the steam-cycle equipment with variation in plant heat rate curve installation, enables the user to generate shown for a General Electric STAG 200 power and revenue in as little as a year system (See Figure 1). Modulating from order date (See Figures 2–4). A compressor inlet guide vanes are typical combined-cycle plant installation standard features of many gas turbine schedule is presented in Figure 5. GE Power Systems I GER-4206 I (10/00) 2 Combined-Cycle Development Evolution and Future 6. High Reliability/Availability - High development of sound operation and reliability operation results from maintenance practices, which reside evolutionary design development that principally with the user. Manufacturer improves parts and components, and experi-ence and recommendations also quality manufacturing programs that contribute to this feature. offer operational factory testing. High 7. Low Operation and Maintenance availability is achieved through Costs - Low operation and maintenance Figure 2. Six MS7001B gas turbines Figure 3. Two STAG 407B combined-cycle steam system installation GE Power Systems I GER-4206 I (10/00) 3 Combined-Cycle Development Evolution and Future Figure 4. Two STAG 407B combined cycle Figure 5. Typical project schedule costs are achieved through quality Electric heavy-duty, gas turbine-packaged design, prudent operation, and power plant product line includes the equipment design that allow convenient MS6001B (50 Hz and 60 Hz), MS7001 FA access for component inspection. (60 Hz), MS7001B (60 Hz) and the 8. High Efficiency in Small Capacity MS9001 FA (50 Hz) units, which cover Increments - Gas turbine generators are an output range of approximately 37 designed and manufactured in discrete MW to 250 MW. Application of these gas frame sizes. For example, the General turbine models in combined-cycle GE Power Systems I GER-4206 I (10/00) 4 Combined-Cycle Development Evolution and Future systems as single or multiple gas turbine tion in 1952. The heat recovery economizers and HRSG installations can provide from applied in these systems used bare tubes, as was about 50 MW to several thousand typical of heat exchangers in combined-cycle megawatts of power generation at systems installed prior to 1959. essentially constant plant thermal Most combined-cycle power generation systems efficiency. installed during the 1950s and early 1960s in- Gas Turbine Combined-Cycle cluded conventional-fired boilers. These sys- tems were basically adaptations of conventional Development steam plants with the gas turbine exhaust gas The commercial development of combined-cy- serving as combustion air for the boiler. The cle systems has proceeded in parallel with gas efficiency of this type of combined cycle was turbine development. We are presently in the approximately 5–6% higher than that of a simi- third generation technology of combined-cycle lar conventional steam plant. These systems systems and are at the launch point of the could economically utilize bare tubes in the fourth generation. boiler because of the high mean temperature First Generation Combined-Cycle Plants difference between the combustion products and the water/steam. The first gas turbine installed in an electric util- ity in the United States was applied in a com- The repowering of steam power plants with gas bined cycle. This was a 3.5 MW gas turbine that turbine generators and HRSGs is still attractive used the energy from the exhaust gas to heat in many applications today as evidenced by the feedwater for a 35 MW conventional steam unit. recent Colorado Public Service, Fort St. Vrain The gas turbine is shown in Figure 6. A schemat- installation, which was placed in commercial ic showing the combined-cycle system is shown operation in 1999. in Figure 7. This system entered service in June The summary presented in Table 1 characterizes 1949, and a similar system was added to this sta- the first generation combined-cyle systems. Figure 6. Gas turbine in first power generation combined cycle GE Power Systems I GER-4206 I (10/00) 5 Combined-Cycle Development Evolution and Future BOILERS STEAM STEAM TB TB GAS GAS TB TB GEN GEN STACK G G COND COND G.T. EXHAUST LP FEEDWATER
Details
-
File Typepdf
-
Upload Time-
-
Content LanguagesEnglish
-
Upload UserAnonymous/Not logged-in
-
File Pages18 Page
-
File Size-