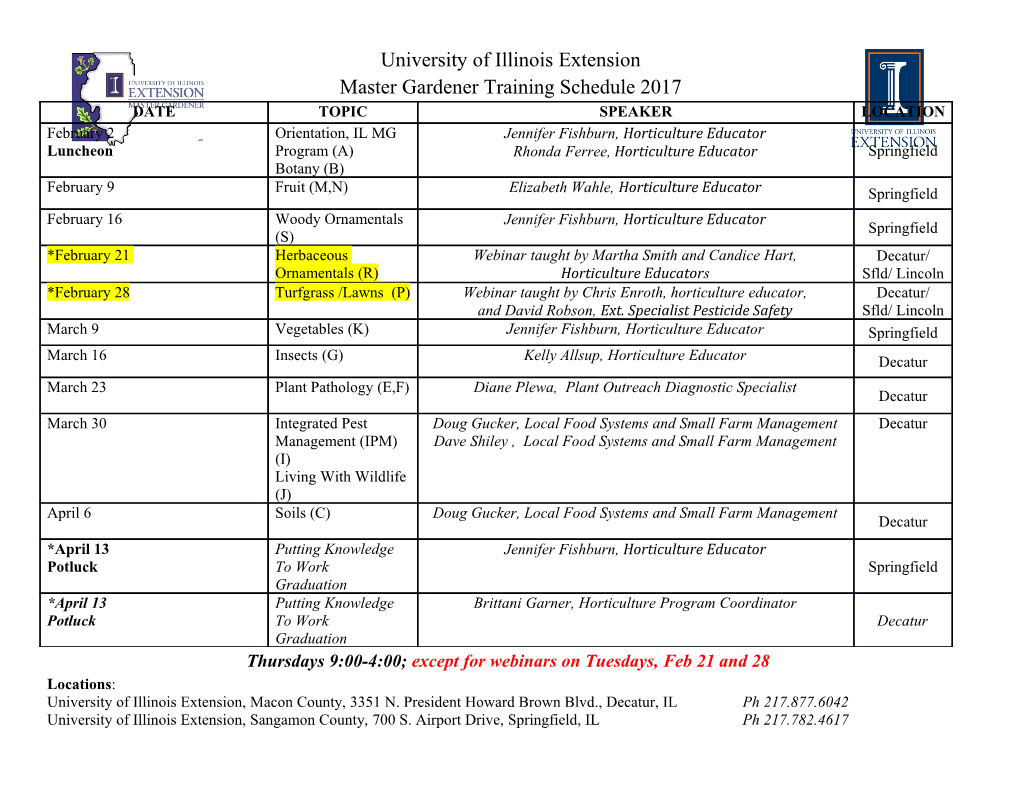
AIRFOIL, PLATFORM, AND COOLING PASSAGE MEASUREMENTS ON A ROTATING TRANSONIC HIGH-PRESSURE TURBINE DISSERTATION Presented in Partial Fulfillment of the Requirements for the Degree Doctor of Philosophy in the Graduate School of The Ohio State University By Jeremy B. Nickol, M.S. Graduate Program in Mechanical Engineering The Ohio State University 2016 Dissertation Committee: Professor Randall M. Mathison, Advisor Professor Michael G. Dunn, Co-Advisor Professor Sandip Mazumder Professor Jeffrey P. Bons Copyright by Jeremy B Nickol 2016 ABSTRACT An experiment was performed at The Ohio State University Gas Turbine Laboratory for a film-cooled high-pressure turbine stage operating at design-corrected conditions, with variable rotor and aft purge cooling flow rates. Several distinct experimental programs are combined into one experiment and their results are presented. Pressure and temperature measurements in the internal cooling passages that feed the airfoil film cooling are used as boundary conditions in a model that calculates cooling flow rates and blowing ratio out of each individual film cooling hole. The cooling holes on the suction side choke at even the lowest levels of film cooling, ejecting more than twice the coolant as the holes on the pressure side. However, the blowing ratios are very close due to the freestream massflux on the suction side also being almost twice as great. The highest local blowing ratios actually occur close to the airfoil stagnation point as a result of the low freestream massflux conditions. The choking of suction side cooling holes also results in the majority of any additional coolant added to the blade flowing out through the leading edge and pressure side rows. A second focus of this dissertation is the heat transfer on the rotor airfoil, which features uncooled blades and blades with three different shapes of film cooling hole: cylindrical, diffusing fan shape, and a new advanced shape. Shaped cooling holes have ii previously shown immense promise on simpler geometries, but experimental results for a rotating turbine have not previously been published in the open literature. Significant improvement from the uncooled case is observed for all shapes of cooling holes, but the improvement from the round to more advanced shapes is seen to be relatively minor. The reduction in relative effectiveness is likely due to the engine-representative secondary flow field interfering with the cooling flow mechanics in the freestream, and may also be caused by shocks and other compressibility effects within the cooling holes which are not present in low speed experiments. Another major focus of this work is on the forward purge cavity and rotor and stator inner endwalls. Pressure and heat transfer measurements are taken at several locations, and compared as both forward and aft purge flow rates are varied. It is seen that increases in forward purge rates result in a flow blockage and greater pressure on the endwalls both up and downstream of the cavity. Thus, even in locations where the coolant does not directly cover the metal surface, it can have a significant impact on the local pressure loading and heat transfer rate. The heat transfer on the platform further downstream, however, is unchanged by variations in purge flow rates. iii Dedicated to my mother, for instilling my love of learning, and to my father, for creating my obsession with how things work iv ACKNOWLEDGEMENTS This research was partially funded by the Aviation Applied Technology Directorate under Agreement No. W911W6-08-2-0011 and partially funded by the Federal Aviation Administration under Agreement No. DTFAWA-10-C-00040. The U.S. Government is authorized to reproduce and distribute reprints for Government purposes notwithstanding any copyright notation thereon. The views and conclusions contained in this document are those of the authors and not should not be interpreted as representing the official policies, either expressed or implied, of the Aviation Applied Technology Directorate, the Federal Aviation Administration, or the U.S. Government. Approved for public release: distribution is unlimited. First I would like to thank my original advisor, Professor Michael G. Dunn, for first giving me the opportunity to work in The Ohio State University Gas Turbine Laboratory, providing me with four years of financial support through a Graduate Research Associateship, and paying for me to attend conferences in San Antonio, Düsseldorf, Phoenix, and Seoul. Your door has always been open to me, and I can’t count the times you’ve explained something to me, or helped me see the big picture when bogged down with insignificant details. I’ll also miss our Monday-morning quarterbacking, discussions on the relative merits of flat plates, and all of your great stories and one-liners. It has not v only been an honor to work for you for five years, but also a great pleasure. “I haven’t had this much fun since the hogs ate my sister!” Second I’d like to thank my advisor Dr. Randall Mathison. You’ve been my main mentor since I first arrived, teaching me not only the specific processes and systems in place at the GTL, but answering my questions about gas turbine operation and theory, and general engineering and aviation principles as well. You’ve been a great resource to bounce ideas off of, and have always been willing to take the time to point me in the right direction when I got stuck. I would also like to thank the other two professors on my dissertation committee: Dr. Sandip Mazumder, and Dr. Jeff Bons. In addition to serving on my committee, they have been two of the best teachers I have had the privilege of learning from. I would also like to thank Honeywell Engines in Phoenix, Arizona for their continued support of me and this project. Honeywell provided the majority of the engine hardware utilized for this work, as well as much of the funding. In particular, I would like to thank Jong Liu, Kuo-San Ho, and Benjamin Kamrath for performing the CFD computation that is used in this dissertation, Rajiv Rana for extensive work in the design of the experiment, Malak Malak for management of the project, and Mark Morris for many thoughtful comments and contributions. Thanks also go to fellow graduate student Matt Tomko for performing much of the early analysis on the pressure data in the purge cavity, providing me with a good foundation from which to work. vi This dissertation would not have been possible without the technical expertise of Jeff Barton, Dr. Igor Ilyin, Ken Fout, and Jonny Lutz in the design, building, and instrumenting of the experiment. Additionally, thanks to Josh Guith for assisting me in the machine shop on more than one occasion, and undergraduate research assistants Chris Cosher, Kevin McManus, Eric Barbe, Miles Reagans, and Richard Celestina for help with the many miscellaneous tasks associated with the experiment. I am also grateful for the administrative assistance I received. Thanks to Cathy Mitchell, and Steve Pruchnicki for assistance out here at the GTL with purchasing and travel authorization and reimbursement. Janeen Sands was also instrumental for helping me to cut through the red tape and answering my countless questions about the convoluted processes and copious paperwork required to do anything at this University. This dissertation is just one in a long line of works on rotating turbine stages presented by previous graduate students at the Gas Turbine Laboratory. While I have never actually met most of them, I am indebted to countless former GTL graduate students, particularly Dr. Charlie Haldeman, James Murphy, Brian Cohen, Dr. Randy Mathison, Dr. Brian Green, and Dr. Matt Smith for performing previous work that helped lay the groundwork for this experiment, and for learning a number of lessons the hard way so I wouldn’t have to. Despite the overall good experience that working in the GTL has been, I would have gone crazy long before reaching this point had it not been for the many friends that I met along the way. Thanks go to Sanjay Ramdon, Shauna Adams, Imani Adams, Steven vii Ramirez, Arvind Mohan, Bingya Li, Jiazheng Hong, Venkata Subramanian, Yibo Shao, Xiao Wu, Emily Dreyer, Ben Grier, Anna Wu, and Soohyun Im for helping me to escape work when I needed to. Further thanks go to the friends that surrounded me at work every day. Through academic and intellectual discussions, tea breaks, Friday lunches, debugging expeditions, mutual complaining sessions, football arguments, lab cricket, and after-work drinks, I owe my sanity and perseverance to having you guys around me every day. Thanks to Alex Habib, Jonny Lutz, Anshuman Pandey, Chris Cosher, Hannah Pier, Tim Lawler, Matt Tomko, Kiran D’Souza, Miles Reagans, Richard Celestina, Eric Kurstak, and Meng- Hsuan Tien for the countless distractions, conversations, lessons, and for being awesome friends and colleagues. viii VITA January 3, 1990 ..............................................Born—Mayfield Heights, Ohio May 2011 .......................................................B.S. Mechanical Engineering, Rose-Hulman Institute of Technology May 2013 .......................................................M.S. Mechanical Engineering, The Ohio State University October 2011-Present.....................................Graduate Research Associate, The Ohio State University Gas Turbine Lab PUBLICATIONS Nickol, J.B., Mathison, R.M., Malak, M.F., Rana, R., Liu, J.S., 2015, "Time-Resolved Heat Transfer and Surface Pressure Measurements for a Fully Cooled Transonic Turbine Stage", ASME J. Turbomach, 137(9), pp. 091009. Nickol, J.B., Mathison, R.M., Dunn, M.G., 2014, "Heat-Flux Measurements for a Realistic Cooling Hole Pattern With Multiple Flow Conditions", ASME J. Turbomach, 136(3), pp. 031010. Nickol, J.B., Mathison, R.M., Dunn, M.G., Liu, J.S., Malak, M.F., 2016, "Unsteady Heat Transfer and Pressure Measurements on the Airfoil of a Rotating Transonic Turbine with Multiple Cooling Configurations", ASME Turbo Expo 2016, Seoul, Republic of Korea, ASME Paper No.
Details
-
File Typepdf
-
Upload Time-
-
Content LanguagesEnglish
-
Upload UserAnonymous/Not logged-in
-
File Pages207 Page
-
File Size-