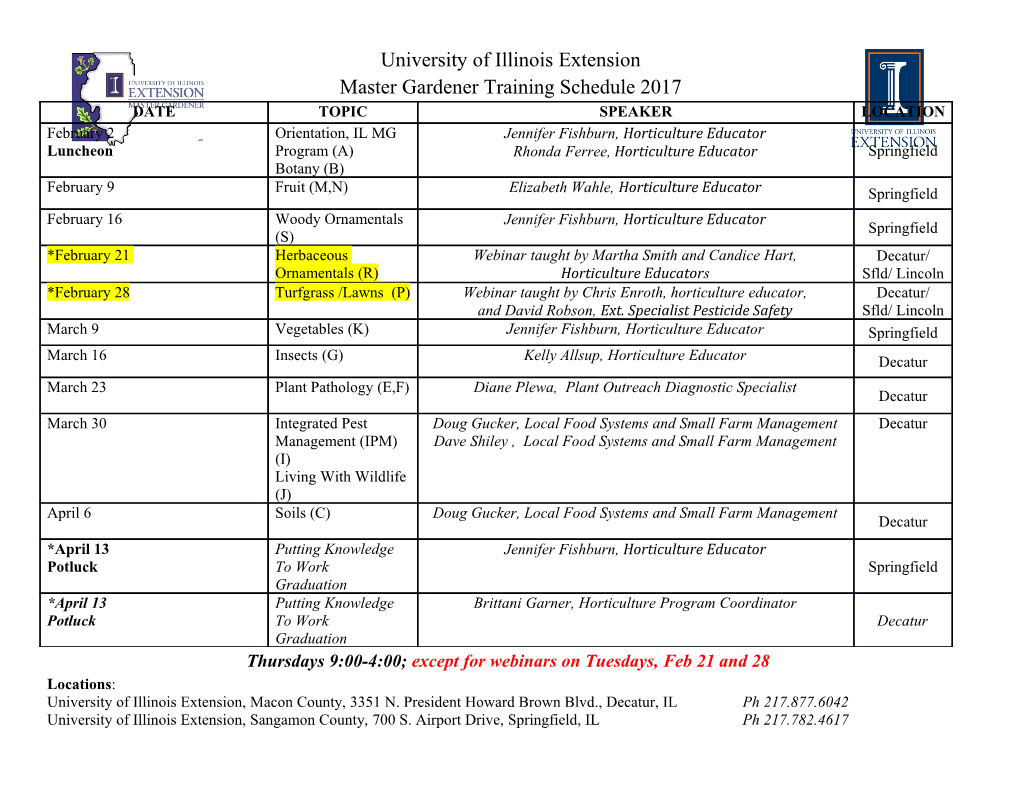
High Temp. Mater. Proc., Vol. 30 (2011), pp. 81–85 Copyright © 2011 De Gruyter. DOI 10.1515/HTMP.2011.011 High Temperature Corrosion Problem of Boiler Components in presence of Sulfur and Alkali based Fuels Debashis Ghosh1; and Swapan Kumar Mitra2 and reheater tubes in advanced thermal power plant. These steels have good creep resistance as well as oxidation resis- 1 Central Mechanical Engineering Research Institute tance at high temperature. These steel also exhibit good (CMERI), CSIR, Durgapur, India combination of mechanical properties, formability, weld- 2 Dept. of Metallurgical and Materials Engineering, Na- ability for manufacturing of pendent tube panels and hor- tional Institute of Technology, Durgapur, India izontal tube banks of superheater and reheater. Different damage mechanisms like creep, fatigue, erosion and cor- Abstract. Material degradation and ageing is of particular rosion are becoming operative during operation and causes concern for fossil fuel fired power plant components. New material degradation and finally leads to failure [2]. The techniques/approaches have been explored in recent years high temperature corrosion problem in coal-based power for Residual Life assessment of aged components and ma- plants is prevalent damage mechanism, which finally af- terial degradation due to different damage mechanism like fects the availability, reliability, and safety of the compo- creep, fatigue, corrosion and erosion etc. Apart from the nents. Oxidation is the predominant mode of corrosion in creep, the high temperature corrosion problem in a fossil most of the industrial environments. During oxidation, the fuel fired boiler is a matter of great concern if the fuel con- formation of protective oxide layer resists the further cor- tains sulfur, chlorine sodium, potassium and vanadium etc. rosion attack. However this protective layer is non pro- This paper discusses the material degradation due to high tective due to the presence of sulfur, chlorine, sodium and temperature corrosion in different critical components of potassium in the fuel and corrosion takes place through the boiler like water wall, superheater and reheater tubes and cracked/spalled unprotective layer [3]. This paper reviews also remedial measures to avoid the premature failure. This different high temperature corrosion mechanism of critical paper also high lights the Residual Life Assessment (RLA) components of boiler like water wall, superheater, reheater methodology of the components based on high temperature tubes etc. Probable corrective actions are also suggested to fireside corrosion. of different critical components of boiler. minimize the high temperature corrosion rate. This paper also highlights the damage assessment and Residual Life Keywords. Boiler, high temperature corrosion, residual Assessment (RLA) methodology of the boiler tubes due to life assessment, water wall, superheater and reheater. high temperature corrosion. 2 High Temperature Corrosion in Boiler Components 1 Introduction The function of boiler is to convert water into superheated steam, which is further delivered to a steam turbine. Coal, Residual Life assessment (RLA) and life extension of ag- oil and natural gas with preheated air is burnt in the fur- ing plants is largely concerned with material degradation of nace. The combustion gases flow up through the furnace high temperature components. Material ageing/degradation and evaporate water into steam inside the furnace waterwall of in service components are becoming major issue for tubes.The gas flow at the roof of the furnace is made hor- techno economical justified Renovation and modernization izontal across the banks of superheater and reheater tubes. programme. Ferritic chromium-molybdenum steels (gen- The gases are then move downward, where it encounters erally referred to as “Cr-Mo” steels) are very much used horizontal low temperature superheater and the economizer in the high temperature components of the steam genera- [4]. The gas flow past the fire side of the waterwall, pen- tor/boilers for fossil fuel and nuclear power plant. [1] Gen- dent superheater and reheater, horizontal superheater and erally 1.0 Cr-0.5 Mo steel, 2.25 Cr-1 Mo steel and 9 Cr- reheater and econimiser tube and exists from the boiler. 1 Mo steels are used for the construction of superheater The high temperature corrosion of the different critical components of the boiler is mainly classified into two broad Corresponding author: Debashis Ghosh, Central Mechanical categories Engineering Research Institute (CMERI), CSIR, Durgapur-713209, India; E-mail: [email protected]. 1. Steam side oxidation at inner side of superheater and Received: August 23, 2010. Accepted: September 15, 2010. reheater tubes. 82 D. Ghosh and S. K. Mitra 2. Fire side corrosion of waterwall, superheater and re- 2.2.1 Fireside Corrosion in Water Wall Tubes heater tubes. The material degradation of the boiler tubes can result from the fireside corrosion that causes wastage of the external 2.1 Steamside Oxidation at Inner Side metal surface. One possible mode of the fireside corrosion exists due to the incomplete combustion of the fuel near The superheater and reheater suffer from steam oxidation burner zone. The rate of corrosion is drastic in reducing on the inner surface. It is the formation of oxide scale atmosphere. The atmosphere contains high level of car- at higher temperature at the inner side (steam side) of the bon monoxide and also delivers unburnt carbon particle of tubes. The growth of the oxide scales is a function of tem- the coal to the tube surface. The incomplete combustion perature and time. The steam side oxide scale of a typical of the coal releases volatile sulfur compounds and chloride superheater tube is shown in Figure 1. Different standard compounds (if present) which cause sulfidation and accel- rate laws are used to estimate the tube metal temperature. erated metal corrosion. Sodium and potassium pyrosulfate This tube metal temperature is used in Larson- Miller pa- compounds (if sodium or potassium is present in the fuel) rameter for estimation of Residual Life of the components. which have low melting points (below 698 K) are generally Several expressions have been suggested by and Paterson responsible for the attack. The characteristics features of and Rettig [5] and Rehn and Apblett [6] to describe oxide the corrosion are formation of thick iron oxide and iron sul- scale growth kinetics to estimate the mean tube metal tem- fide scales. The tube wall thinning is due to the wastage of perature. The expressions are given below: external metal from the surface. Tube thinning eventually 1. log x D7:1438 C 2:1761 104T.20C log t/ for leads to the premature failure of the tubes. 1–3 % steel [7] 2. log x D6:8398 C 2:83 104T .13:62 C log t/ for 2.2.2 Fireside Coal Ash Corrosion of Superheater and Re- 2:25 Cr-1 Mo steel [8] heater Tubes: where, Fireside corrosion of superheater and reheater tubes are x D Steam side oxide scale thickness in mils, associated with liquid ash deposits at higher temperature. T D Mean operating temperature 0R D .F C 460/ and This type of corrosion can cause wall thinning and con- t D Service time in hours. tribute to stress rupture failure by increasing the hoop stress. This type of liquid phase corrosion occurs in the temper- ature range from 868 K to 978 K and is associated with deposit related molten salt attack beneath the surface de- posits, if the fuel contains sulfur, sodium and potassium. Metals Substrate The low melting salt of the type alkali iron trisulfate [(Na, K) FeSO4] are deposited to the fireside of the tubes and cause the external wastage of the tubes [1]. The fireside deposits in superheater tubes in a typical thermal power Oxide Scale plant boiler is shown in Figure 2. The alkali iron trisulfate forms by reaction of alkali sulphates with iron oxide in the presence of SO3 and have a maximum melting temperature (1 W 1 mixture of sodium and potassium salts) of 825 K, where as melting points of simple sulfates are 1157 K for Na2SO4 and 1342 K for K2SO4. Although the SO3 lev- Figure 1. Oxide scales at inner side of superheater tube. els in the flue gas are expected to be much lower, catalytic oxidation of SO2 in the stagnant zones beneath a layer of deposit is believed to generate SO3 levels sufficiently high to favour the formation of liquid trisulfates at temperature 2.2 Fireside Corrosion in Boiler Components up to 978 K [7] The different critical components of boiler like Water wall, The coal ash corrosion is temperature dependent. Superheater and Reheater tubes suffer fireside corrosion. Stringer [8] shows that the corrosion increases with the Corrosive impurities (i.e. alkali metals, sulfur or vanadium) increase of temperature reaches up to a certain tempera- present in the fuel are responsible for the fireside corrosion ture and then decreases with temperature for low alloy fer- of critical components of the boiler. These impurities can ritic steel (SA 213 T22) and austenetic stainless steel (321 lead to the formation of non-protective scales or can disrupt grade). The rate of corrosion is less in case of 321 stainless normally protective scales. The principal damage mecha- steel grade in comparison to low alloy ferritic steel (T22 nism is oxidation and hot corrosion. grade) [8] This is due to the higher Cr content of stainless High Temperature Corrosion Problem of Boiler Components 83 Substrate Fireside Deposits Sulfidation attack on grain boundary Metal surface Outer surface Figure 2. Fireside ash deposits on the super heater tube. Figure 4. Grain boundary sulfide attack on eh outer surface of the superheater tube. on the tube steel. This corrosion is particularly aggressive when fuel contains vanadium, sulfur and sodium. Greater Failed Zone wastage material is observed when the tube metal operates Adherent at temperature above 863 K. The severity of oil ash cor- Deposits rosion is affected by temperature, the amount of vanadium, sulfur and sodium, the amount of excess air available for the formation of V2O5.
Details
-
File Typepdf
-
Upload Time-
-
Content LanguagesEnglish
-
Upload UserAnonymous/Not logged-in
-
File Pages5 Page
-
File Size-