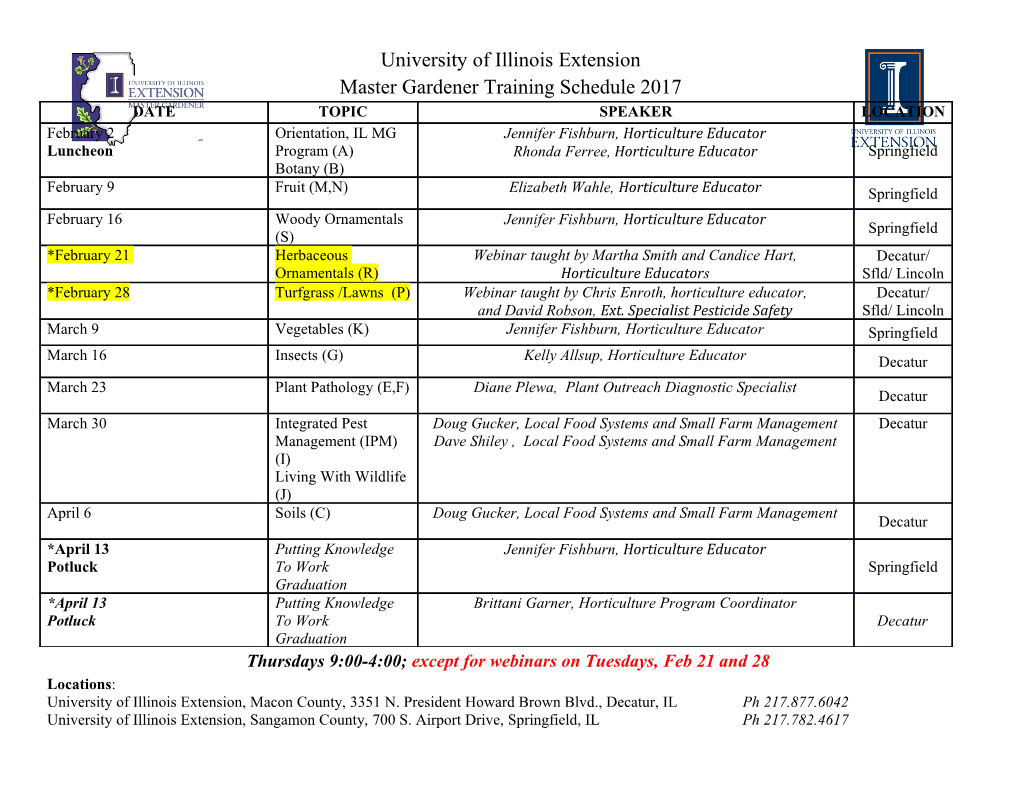
3,®75,8%Z7 United states Q@ Patented Jan. 29, 1963 1 2 atmosphere or by ?lling these spaces with inert gases‘. 3,075,827 7 The reaction vessel 2 preferably includes suitable heating PRGCESS FGR PR?DUCl-NG ANHYDRGUS means 4 and agitating means 6 for respectively heating LETHIUM PERCBEQRATE John W. Cretzrneyer, Minneapolis, Minn., assignor to and agitating the contents of the vessel. If the tempera Lithium Corporation of America, Inc, Minneapolis, ture to which the starting materials are heated to dissolve Minn, a corporation of Minnesota the salts and to effect the et?cient reaction thereof is Filed Sept. 8, 1959, Ser. No. 838,695 above the boiling point of the organic solvent, then an 8 Claims. (Cl. 23-85) excess of solvent is used and the evaporated solvent is fed to a condenser where it is condensed and returned This invention relates to a process and apparatus for 10 to the reaction vessel. To this end, an outlet conduit 8 producing anhydrous lithium perchlorate. The pro extends from the top of the reaction vessel 2 to a suit duction of anhydrous lithium perchlorate by processes able condenser ltl which condenses the evaporated or heretofore known involves the production of lithium per ganic solvent and returns the condensed solvent through chlorate containing water of hydration followed by a de a return conduit 12 to the reaction vessel. hydration procedure at elevated temperatures. The de 15 As previously indicated, the chemical reaction be— hydration procedure is slow and, therefore, costly. It is, tween the dissolved anhydrous starting materials pro~ accordingly, an object of the present invention to provide duces the desired lithium perchlorate dissolved in the a process and apparatus for producing anhydrous lithium organic solvent and a precipitate of the other reaction perchlorate which avoids the disadvantages of these proc product which would be sodium chloride if sodium per esses, particularly the costly dehydration of hydrated 20 chlorate and lithium chloride were the starting materials. lithium perchlorate at elevated temperatures. A discharge conduit 13 having an initially closed valve The process in its broader aspects involves reacting to 14 extends from the bottom portion of the reaction ves gether an anhydrous salt of perchloric acid other than sel 2 to a suitable ?lter 18. When the reaction between lithium perchlorate with an anhydrous lithium salt which the starting materials in the reaction vessel 2 is complete, reacts by double decomposition with said anhydrous salt 25 the valve 14 is opened to allow the contents of the re of perchloric acid, said reaction being carried out in an action vessel to pass through ?lter 18, which removes the organic non-aqueous solvent in which lithium per insoluble reaction product. The ?ltrate passes through a chlorate, said anhydrous salt of perchloric acid and said conduit 19 into a distillation kettle 22, and the ?ltered anhydrous lithium salt are soluble, but in which the salt precipitate is recovered from the ?lter. The distillation other than lithium perchlorate resulting from the reaction 30 kettle 2?. includes suitable agitating means 24 for agitat is insoluble. The thus produced anhydrous lithium per ing contents thereof and heating means 26 which effects chlorate is readily recovered from the organic solvent, the distillation of the organic solvent. The distillation for instance, by ?ltering out the insoluble salt and dis of the organic solvent may be aided, if desired, by ap tilling off the solvent from the ?ltrate. plication of vacuum to the kettle. The distilled solvent ‘ The process works most eifectively when the starting 35 passes through a conduit 28 ‘at the top of the distillation materials are anhydrous sodium perchlorate and anhy kettle to a suitable condenser 30 where the solvent is con drous lithium chloride, dissolved in a low' molecular densed and passed through a conduit 32 to a suitable re weight alcohol, such as methanol, ethanol, propanol or ceiver or storage tank 36. Anhydrous lithium per butanol, preferably a propyl alcohol such as n-propanol ihlorate crystals form in the bottom of the distillation or isopropyl alcohol. Although less preferred, instead of ettle. sodium perchlorate, ammonium, magnesium, strontium When the organic solvent is substantially completely or barium perchlorate can be used; and, instead of lithium evaporated, the heat (and vacuum is used) are cut off and chloride, lithium bromide, lithium nitrate, lithium nitrite an on-otf valve 38 in a conduit 40 extending between or lithium ehromate can be used. Although low mo ,a toluene supply tank 42 and the distillation kettle is lecular weight alcohols are decidedly the preferred sol~ 45 opened to feed toluene to the distillation kettle. Sulli vents, other organic solvents satisfying the foregoing re cient toluene is added to just cover the lithium per quirements can be utilized, particularly acetone which pro~ chlorate crystals in the distillation kettle. Next, the dis duces very satisfactory results when barium or strontium tillation kettle is sealed by closure of the various valves perchlorate is used as a starting material. in the conduits leading thereto, and heat and vacuum are Another aspect of the present invention resides in the applied to distill the toluene. As the toluene distills, it apparatus for carrying out the basic process of the inven carr1es with it as an azeotrope any solvent or moisture tion briefly described above. Examples of this apparatus which may still be in the distillation kettle. The distilled are described in the speci?cation to follow and illustrated toluene passes through the conduit 28 into the condenser in the drawings wherein: 30, and the condensed toluene may then be carried to a FIG. 1 is a diagrammatic illustration of apparatus suit 55 suitable location through a discharge conduit 44 having able for carrying out the process of the present inven an on-otf control valve 46. After‘the toluene has been tion; and completely distilled, the contents of the distillation FIG. 2 is a diagrammatic illustration of other appa; kettle are preferably heated and agitated for several hours ratus for carrying out the process of the present inven or more to free the lithium perchlorate of any volatile tion. 60 materials. Referring to FIG. 1, the starting ingredients are initially Reference is now made to FIG. 2 which shows a pre charged into a reaction vessel 2. As above indicated, the ferred form of apparatus for producing lithium perchlo starting ingredients are (a) an anhydrous salt of per rate. That part of the system illustrated following the chloric acid other than lithium perchlorate, most desir reaction vessel 2, is identical with the corresponding por ably sodium perchlorate, (b) an anhydrous lithium salt, tion of the system shown in FIG. 1, and thus will not again such as lithium chloride, and (c) a substantially non be described, and all common elements used in the two aqueous or anhydrous organic solvent, preferably a low systems are similarly numbered. molecular weight alcohol, in which the above mentioned The apparatus illustrated in FIG. 2 di?’ers from that salts are dissolved. The spaces within reaction vessel 2 shown in FIG. 1 in the addition of an extractor 50 be— and the other conduits and vessels to be described are kept 70 tween the condenser 1d and the reaction vessel 2. In essentially free of moisture in any suitable way, such as the preferred process, only the lithium salt starting ma v by mechanically sealing the spaces from the surrounding terial, such as lithium chloride, and the organic solvent 3,076,827 4 are initially placed in the reaction, vessel 2. The per to 180° C. and maintained there, for example, for from chlorate salt starting material, such as sodium perchlo 2 to 4 hours while the contents of the kettle are continu rate, is placed in its crystalline form in the extractor 50. ously agitated. White crystals of anhydrous lithium per The extractor has a discharge opening 51 in the bottom chlorate form and these are removed from the distillation thereof which communicates with the top of the reaction kettle. vessel and this opening is covered by a porous disk 52 It is important that the anhydrous perchlorate used as made, for example, of sintered glass which prevents the one of the starting materials in the practice of the present passage of the perchlorate salt crystals to the extractor 5G. i invention be essentially free of chlorates. Thus, for in The perchlorate salt crystals in the extractor 50 stance, the readily available commercial solutions of sodi are thus gradually dissolved in the liquid organic solvent 10 um perchlorate, from which anhydrous sodium perchlo being returned from the condenser 10F to the reaction rate is obtained, contain about 0.5 to 0.67%, by weight, vessel 2. This process of feeding perchlorate salt to the of sodium chlorate. Unless this sodium chlorate is re reaction vessel is of particular utility where the perchlo moved, for instance, prior to the drying of the sodium per rate salt has only a limited solubility in the organic solvent chlorate solution, safety hazards would arise in the prac involved. For example, sodium perchlorate has only 15 tice of the process of the present invention because of limited solubility in organic solvents such as propanol, the unstable nature of sodium chlorate. It has been so that a rather large volume of solvent would otherwise found that the following procedure is very satisfactory be required in order to carry out the practice of the pres for reducing the chlorate content. Thus, hydrochloric ent invention of the perchloratecrystals were to be initial acid (or other acids or reducing agents), when added to ly placed in the reaction vessel as in the embodiment of 20 sodium perchlorate solutions containing sodium chlo the invention illustrated in FIG.
Details
-
File Typepdf
-
Upload Time-
-
Content LanguagesEnglish
-
Upload UserAnonymous/Not logged-in
-
File Pages4 Page
-
File Size-