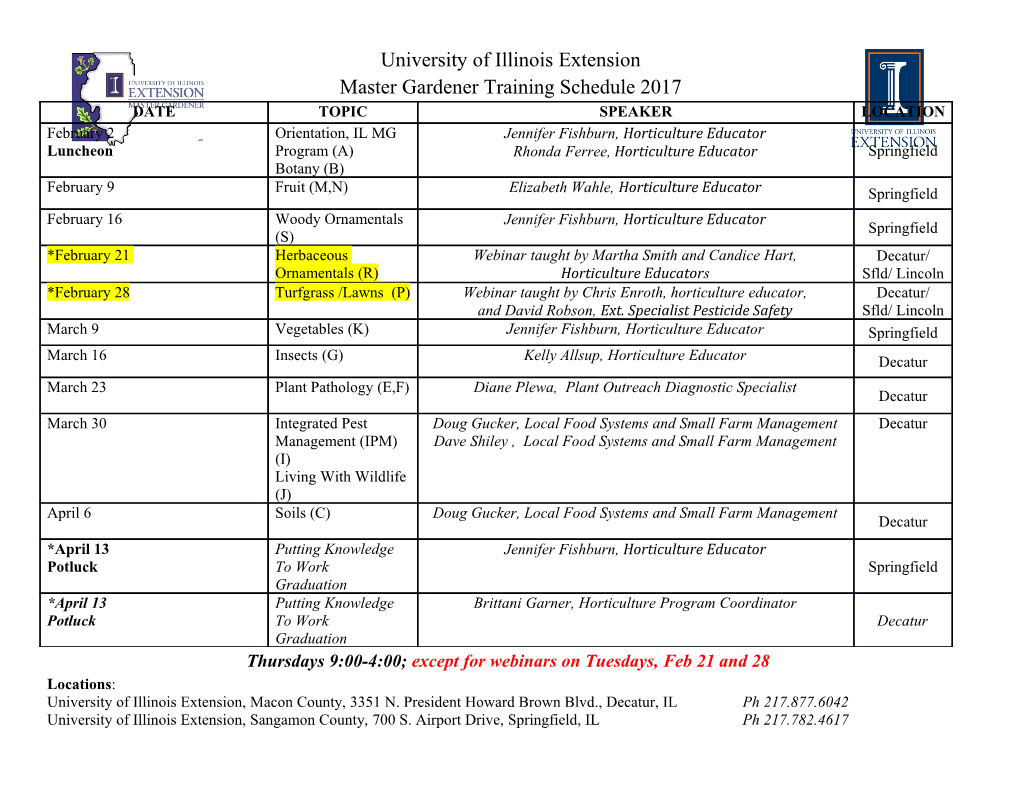
Fundamentals of Drilling Engineering Conversions and Constants Drilling Fluid Considerations Nomenclature 2 3 1 kPa = 0.1450 psi 1 in = 2.54 cm 1 acre = 43,560 ft 1 m = 6.2898 bbl R = 459.67 + °F 1 lbm = 453.59 g Fluid Pressure Gradient Filtration Rate – API Tests Adjusting Weight with Barite Common Variables 2 2 3 1 MPa = 10 bar 1 ft = 0.3048 m 1 m = 10.764 ft 1 bbl = 5.6146 ft K = 273.15 + °C 푂퐷, 퐼퐷 = outer, inner diameter 1 bbl = 42 US gal °F = 1.8 °C + 32 훻푃 = 휌Τ144 [=] 푝푠Τ푓푡 푉30 = 2 푉7.5 − 푉푠푝 + 푉푠푝 푚퐵푎 = 42 푉푓 − 푉푖 휌퐵푎[=]푙푏푚 1 atm = 14.696 psi 1 mile = 5,280 ft 휌 = mud density[=]푝푝푔 3 푚 1 atm = 1.013 bar 1 ft = 7.4805 gal 1 cp = 1.0 mPa-s 휌[=] 푙푏 Τ푓푡3 푚 푉30 = API vol. collected at 30 mins 휌퐵푎 − 휌푖 푞 = flow rate[=] 푔푎푙Τ푚푛 6 2 푉푓 = 푉푖 [=]푏푏푙 휌퐵푎 = 35푝푝푔 1 bar = 1 x 10 dynes/cm 1 lbmΤgal = 0.052 psiΤft Standard Pressure = 14.696 psia 휌퐵푎 − 휌푓 훻푃Τ0.052 [=] 푙푏푚Τ푔푎푙 푉7.5 = volume collected at 7.5 mins 휎푦 = min. yield strength[=]푝푠 5 −3 2 1 Newton = 1 x 10 dynes 1 mD/cp = 6.33 x 10 ft /psi−day Standard Temperature = 60°F 퐸 = Young′s modulus Rotational Viscometer 푉푠푝 = spurt vol. collected at 0 mins Mud Quality Control −6 −9 2 3 6 1 dyne = 2.248 x 10 lbf 1 Darcy = 9.8692 x 10 cm Gas Constant = 10.732 psia ⋅ ft Τlbmol ⋅ R 푓 휌 − 휌 − 휌 + 휌 − 푓 휌 − 휌 퐸 = 30푥10 푝푠 for steel 휇 = 휃 − 휃 [=]푐푝 푉2 − 푉1 푠 퐵푎 푤 푚 푤 표 푤 표 Τ 3 600 300 푉 = 푉 − 푡 푓푙푔 = 3 3 1 hp = 0.7457 kw Water density at SC = 62.37 lbm ft 푠푝 1 1 휌퐵푎 − 휌푙푔 퐼 = moment of inertia 1 g/cm = 62.428 lbm /ft 푡2 − 푡1 푙푏푓 퐽 = polar moment ofinertia 1 hp = 33,000 ft ⋅ lbfΤmin Molar Mass of Air = 28.966 g/mol 휏 = 휃 − 휇[=] 푓 = 푓 − 푓 휌 = 21.7푝푝푔 푦 300 100 푓푡2 When conducting HPHT test, 퐵푎 푠 푙푔 푙푔 1 kgΤl = 8.347 lbmΤgal VIG = 379.3 scfΤlbmol @ 14.696 psia 푆퐹 = safety factor 1 BTU = 778 ft ⋅ lbf M 푉푠푝 & 푉30 must be multiplied by WBM Maximum Solids Fraction Casing Design Rig Power Requirements Viscosity is Newtonian 4 due to smaller HPHT filter cell 퐷퐹 = design factor if yield point is zero, if 푓푠,푚푎푥 = 0.0289휌푚 − 0.139 푡 = pipe wall thickness[=]푛 not it’s plastic viscosity Recommended Clearance Ratio Hoisting Power Typical WBM In general, the OBM 푓푠,푚푎푥 is about 30% Drilling Fluid Considerations Hoisting Efficiency Clearance between 푊푣푏 퐶 퐼퐷표푢푡 − 푂퐷푖푛 Plastic Viscosity Limits 휃# = reading at # rpm tube centered in 0.13 ≤ ≤ 0.18 퐶 = 푃푖푛푝푢푡 = [=]ℎ푝 n E VAPI Limits for Yield Point 푂퐷 2 퐸(33,000) larger tube 푖푛 6 0.874 휇푚푎푥 = 2.94exp(0.164휌푚) Typical OBM/SBM −1.15 휏푦 = yield point 휏푦,푚푎푥 = 353휌푚 휏푦,푚푖푛 = 0.07휌푚 − 0.45 푊 = hook load[=]푙푏푓 8 0.841 푂퐷 = inside tube 푂퐷 퐼퐷 = outer tube 퐼퐷 푉푠푝 푚퐵푎 = Barite mass to add 푖푛 표푢푡 휇푚푖푛 = 1.58exp(0.171휌푚) 푣푏 = velocity ofblocks[=] 푓푡Τ푚푛 10 0.810 Altering suspended low 훾 solids normally keeps 휌퐵푎 = Barite density Mud Window and Casing Point Selection 퐸 = hoisting efficiency 12 0.770 휇 [=]푐푝 time mud parameters within recommended ranges 14 0.740 휌푖 = initial mud density[=]푝푝푔 Equivalent Mud Density 푛 = number of lines strung through blocks Routine Pipe Calculations Well Trajectory Surface Casing 휌푓 = final mud density[=]푝푝푔 Rotating Power Pumping Power Capacity and Volume Directional Drilling Definitions 푓푙푔 = low gravity solids fraction DF 푤푇 푞푃푑 2 2 2 N = 0° N 푃 = [=]ℎ푝 퐻 = [=]ℎ푝 퐼퐷 푂퐷 − 퐼퐷 DF = Derrick Floor 휌푤 = base water [=]푝푝푔 푇 푖푛푝푢푡 퐶 = 퐶 = 33,000 1714휂 푝푖푝푒 푎푛푛푢푙푎푟 휌 = oil density[=]푝푝푔 1029.4 1029.4 270° 90° 표 휀 훼1 Intermediate Casing 푤 = 2휋푁[=] 푟푎푑Τ푚푛 푞 = flow rate[=] 푔푎푙Τmin 푀퐷1 푓 = fraction of total solids Τ 푠 푁 = rotary speed[=]푟푝푚 푃 = discharge pressure[=]푝푠 퐶[=] 푏푏푙 푓푡 푉[=]푏푏푙 퐼퐷, 푂퐷[=]푛 퐿[=]푓푡 180° Depth 푑 휀 = azimuth TVD 훼 = inclination 푓표 = oil fraction 푇 = rotary torque[=]푓푡 ⋅ 푙푏 휂 = overall pump efficiency 2 2 2 푓 퐼퐷 퐿 푂퐷 − 퐼퐷 퐿 KOP = Kick-Off Point 휌푙푔 = drilled low gravity solids 푉 = 푉 = 훼2 푃 = torque horespower normally 휂 = 0.9 푝푖푝푒 푎푛푛푢푙푎푟 2 푇 1029.4 1029.4 훽 = Dog Leg Angle 푀퐷2 휏푦,푚푎푥, 휏푦,푚푖푛 [=] 푙푏푓Τ100 푓푡 Pumps Production Casing Using Pipe Weight OD 푅 Rig Power Requirements KOP 푐 Pore Pressure Gradient Single Acting Pumps 2 푊 ID 훽 THD 푤 = angular velocity ”Bottom-Up” Casing Selection 푂퐷 푝푖푝푒 푅푐 Pore Pressure + Trip Margin 퐶푝푖푝푒 = − THD = Departure can also do 2 Well Trajectory Fracture Gradient 푞 = 0.0034 푑 푁 퐿 푁휂 [=] 푔푎푙Τ푚푛 1029.4 5.615휌푝푖푝푒 “Top-Down” Casing Selection 푝 푝 푠 푣 N Frac Gradient – Kick Margin 푅푐 = radius ofcurvature 푙푏푓 푙푏푚 5729.6 deg. BHL 푑푝 = plunger diameter[=]푛 푁푝 = number of plungers 퐷퐿푆 = [=] 푊푝푖푝푒[=] 휌푝푖푝푒[=] 3 푇푉퐷 = true vertical depth Common Bit Sizes Conventional Casing Strings 푓푡 푓푡 푅푐 100 푓푡 푁 = pump speed[=] 푠푡푟표푘푒푠Τ푚푛 퐿푠 = stroke length[=]푛 푀퐷 = measured depth 퐷퐿푆 = Dog Leg Severity Casing Size Common Bit CSG BIT 2 DF Departure (OD in.) Sizes (in.) in. in. 휂푣 = volumetric efficiency which is usually between 0.8 − 0.9 푂퐷 푊푝푖푝푒 푇퐻퐷 = total horizontal distance Annular Space Annular 퐼퐷 = 24 − AnnularSpace 훼2 − 훼1 휀2 − 휀1 1 11 24 휋휌푝푖푝푒 훽 = 2arcsin sin2 + sin훼 sin훼 sin2 퐵퐻퐿 = bottom hole location 4 2 6,684 ,6 Down Hole Motors 2 1 2 2 1 3 Routine Pipe Calculations 5 624 ,6 7 6 1 7 8 Output Shaft Torque Cement 1 73 2 푊푝푖푝푒 = pipe air weight 5 2 788 ,8 푞휂푣훥푃 Leak-Off Test – Good Cement 731 5 푇 = 3.064 [=]푓푡 ⋅ 푙푏푓 Common Properties 24 Hour Compressive Strength (psi) Pumps 6 78 ,8 8 ,8 2 8 8 푁 5 1 53 API Class A H Curing Temperature and Pressure (psi) 푞 = flow rate under load 훥푃 6 8 82 ,8 8 ,8 4 훥푃 = 훥푃 through motor 푁[=]푟푝푚 휂 = volumetric efficiency Desired Pressure 7 1 푣 Reached Water (%) by 531 9 8 11 12 4 46 38 60°F 80°F 95°F 110°F 140°F Down Hole Motors 7 88 ,8 4 ,9 2 Cement Weight Key Notes on Motors Class A 0 0 800 1600 3000 5 75 푁 = shaft speed 7 8 988 ,10 ,11 - Motor provides torque at the bit depending on 푞 and 훥푃 Water Cement 5.19 4.29 3000 4050 5500 6700 8400 5 1 (gal/sack) Drill String Considerations 8 8 11,12 4 - A motor is a speed multiplier, adding to top drive or rotary speed 1 95°F 110°F 140°F 170°F 200°F 퐹 = drag due to friction 9 5 121 ,14 3 15 17 2 Slurry Density 퐷 8 44 - Torque from the motor helps the bit drill in highly deviated 15.6 16.4 Class H 800 1600 3000 3000 3000 (ppg) 푊 = traveling equipment 3 sections where it’s difficult to apply WOB Pressure Pipe Drill 푇퐸 10 4 15 Cement Slurry Yield 615 1905 2085 2925 5050 13 3 17 1 - 푞, 훥푃, and 푁 are interrelated and depend on how motor is made Pumping Shut-in & Bleed-off 1.18 1.06 푊퐵,퐷푆 = buoyed drill string 8 2 ft3Τsack 16 26 - If motor cannot supply the required torque to break rock, the 0 Time (mins) 20 훼 = hole inclination[=]deg 20 24,26 motor will stall and motor damage can occur Casing Loads 푇 = rotating torque Drill String Considerations 푊푐푟 = critical weight on bit Collapse Pressure Burst Pressure Worst Case Scenario for Collapse and Burst Casing Loads Weight Indicator Buoyed Pipe Weight Collapse: Lost Circulation During Drilling 푃푐 = 푆퐹 푃푒 − 푃푖 + 푃푇 푃푏 = 푆퐹 푃푖 − 푃푒 + 푃푇 푃푒 = external pressure 푊푖푛푑 = 푊퐵,퐷푆 + 퐹퐷 + 푊푇퐸[=]푙푏푓 푊퐵 = 푊 − 푊푓[=] 푙푏푓Τ푓푡 푊퐵 = 푊 1 − 휌푚Τ휌푝푖푝푒 푆퐹 = 1.125 푃푐 = 푆퐹 0.052휌푚 퐷 퐷 = csg shoe depth = 푓푡 푃퐵푅 = burst resistance 푃푖 = internal pressure 퐹 − value moving down 퐹 + value moving up Collapse resistance 퐷 퐷 푊 = pipe air weight 푊 = fluid weight 푊 = 푊 1 − 0.0153휌 Burst: Gas Kick Fills Casing 푓 퐵 푚 determined by four 2휎푦푡 푃푇 = 푃 due to temp change 푃 = 퐷퐹 Required Drill Collar Length different eqns based 퐵푅 Pressure high enough to fracture rock at shoe of the casing 퐹 = tensile load 푊퐵 = buoyed pipe weight 휌푚 [=]푝푝푔 휌푠푡푒푒푙 = 65.5 푝푝푔 푂퐷 푡 Τ 푆퐹 ⋅ 푊푂퐵 on the 푂퐷 푡 ratio 푃 = 푃 − 푃 푃 = 푃 inside casing at the surface 퐷퐹 = 0.875 푂퐷, 푡 = 푛 푖푆 푖퐷 푔 푖푆 푊 = casing air weight 퐿퐷퐶 = [=]푓푡 Buckling – Vertical Hole (more info: API Bulletin 5C3) 푊퐵,퐷퐶cos훼 퐷 = depth below bend 푃푖퐷 = 푃푓푟푎푐 + 훥푃푓푟푖푐 푃푖퐷 = pressure inside casing at D 푏 푊 = 1st order buckle = 1.94푚푊 [=]푙푏 Casing in Tension 푊퐵,퐷퐶 = buoyed drill collar 푊푂퐵 = weight on bit 푐푟,1 퐵,퐷퐶 푓 3 퐸퐼 퐹푇 = force due to temp change 훥푃푓푟푖푐 ≈ 0.015퐷 푃푓푟푎푐 = fracture pressure at D 푚 = 퐹푡 = 푆퐹 푊 퐷푏 + 퐹푇 + 퐹퐵[=]푙푏푓 푆퐹 = 1.8 퐹 = force due to bending Linear Pipe Drag 푊퐵,퐷퐶 퐵 푊푐푟,2 = 2nd order buckle = 3.75푚푊퐵,퐷퐶[=]푙푏푓 푃 훾 푃 = estimated 퐶퐻 gas column 푃 6퐾퐿 퐿 = 푓푡 푖퐷 푔 푔 4 퐷퐿푆 = dogleg severity 퐹 = 휇푁 = 휇퐹sin훼 퐹 = 퐹 − 푊 푗 푗 푃푔 = 0.0187퐷 퐷 푎푥 퐵 Critical WOB for deviated hole usually outside 휋 퐹퐵 = 64(퐷퐿푆)(푂퐷)푊 푇퐷 푇 = temperature at D[=]푅 퐼 = 푂퐷4 − 퐼퐷4 tanh 6퐾퐿 퐾[=]푛−1 퐷 퐾 = bending constant 푁 = normal force 퐹 = axial force 푗 푎푥 recommended range for effective drilling 64 Τ 퐾 = 푊퐷푏 퐸퐼 푇퐷 = 퐷훼푇 + 푇푠푢푟푓푎푐푒 훼푇 = local temperature gradient 퐿푗 = joint length 휇 = friction coefficient and is usually 0.15 − 0.6 Maximum Pull on Pipe Depth to Stuck Point Well Control 훥푃푓푟푖푐 = 푃 to overcome friction Rotational Pipe Drag 휎푦 훾 = gas specific gravity 퐹 = 퐴[=]푙푏 훥푙 Pressure Balance Kick Indicators Kick Control Methods 푔 푂퐷 max 푓 퐿 = 퐸 퐴[=]푓푡 푆퐹 훥퐹 - Flow rate/pit volume increase Driller’s Method Well Control 푇 = 휇 퐹sin훼[=]푛 ⋅ 푙푏푓 푃 = 푃 + 0.052휌 푇푉퐷 2 퐵퐻 푑푝 푚 푙푏푚 - Two circulations 휎푦 = pipe min.
Details
-
File Typepdf
-
Upload Time-
-
Content LanguagesEnglish
-
Upload UserAnonymous/Not logged-in
-
File Pages2 Page
-
File Size-