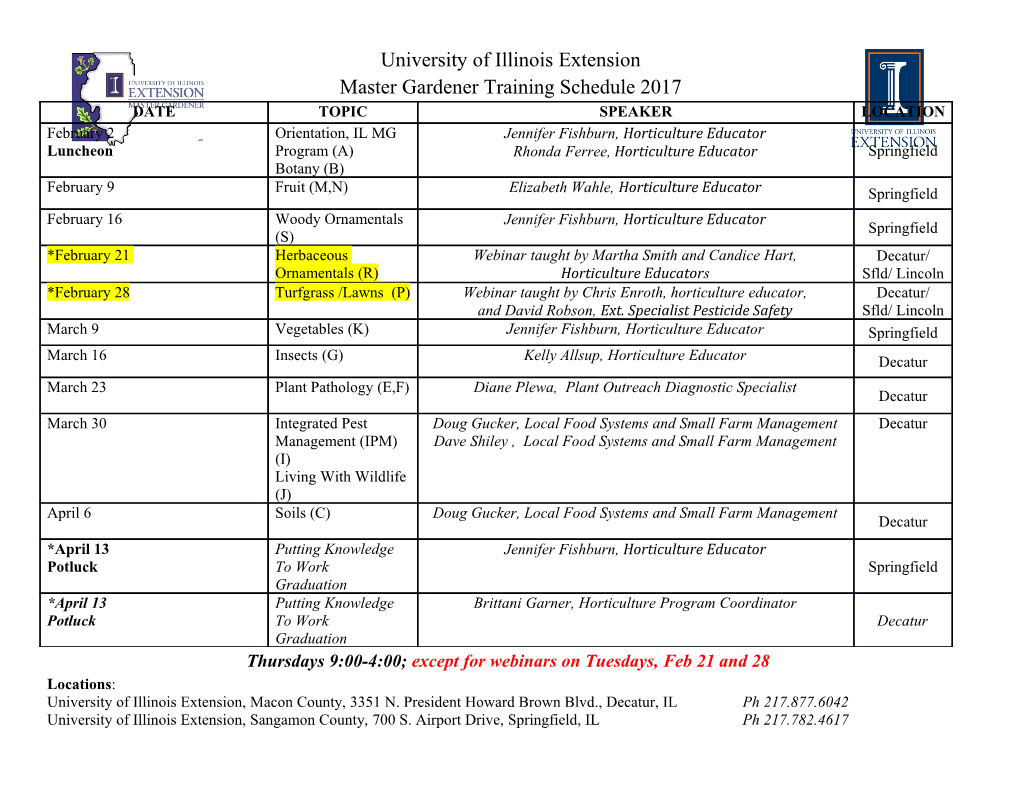
Parametric Design Constraints Management Using the Design Structure Matrix: Creation of an Electronic Catalog for a Safety Belt System by Jerrold I. Lavine M.E., Mechanical Engineering Cornell University, 1993 B.S., Mechanical Engineering State University of New York at Binghamton, 1991 SUBMITTED TO THE SYSTEM DESIGN AND MANAGEMENT PROGRAM IN PARTIAL FULFILLMENT OF THE REQUIREMENTS FOR THE DEGREE OF MASTER OF SCIENCE IN ENGINEERING AND MANAGEMENT AT THE MASSACHUSETTS INSTITUTE OF TECHNOLOGY February 2000 @ Jerrold I. Lavine 1999. All rights reserved. The author hereby grants to MIT permission to reproduce and to distribute publicly paper and electronic copies of this thesis document in whole or in nart Signature of Author Uystem Design and Management Program December 1, 1999 Certified by el E. Whitney Senior Research Scientist Center for Technology, Policy, and Industrial Development Thesis Supervisor Certified by Ali A. Yassine Research Scientist Center for Technology, Policy, and Industrial Development Thesis Supervisor Accepted by Thomas A. Kochan LFM/SDM Co-Director -Rrri M Rtinkirrnf=nnnr nf Management Accepted by Paul A. Lagace L"..--LFM/SDM Co-Director Professor of Aeronautics & Astronautics and Engineering Systems MASSACHUSETTS I TITUTE OF TECHNOLOGY JAN 2 01 LIBRARIF.R Parametric Design Constraints Management Using the Design Structure Matrix: Creation of an Electronic Catalog for a Safety Belt System by Jerrold I. Lavine Submitted to the System Design and Management Program On December 1, 1999 in Partial Fulfillment of the Requirements for the Degree of Master of Science in Engineering and Management ABSTRACT A framework was developed for a comprehensive evaluation of a product development process that encompasses the physical system and system level requirements to assure their coordination for efficiency and optimization. With this analysis, efficient information flows and requirements can be incorporated into the process so that the optimum product will be delivered, consistent with the organizational structure, while satisfying system and sub-system level constraints. An evaluation of this form also identifies required enablers for process and product improvement. Traditional systems engineering relies on a top-down product and target-setting decomposition process with aligned organizations. For modular products that have standard interfaces and with experienced organizations with established procedures, this process is appropriate. For integral products and processes, this approach is not effective at delivering an optimized system in performance, program or organizational metrics. An approach that allows system development to occur in parallel with sub-system system design is preferred. Based on process, product and requirement metrics, a preferred alternative and improvements can be identified. The case study presented in this thesis involves the design and development of automobile safety belts constrained by regulatory location requirements. Based on a Design Structure Matrix evaluation of the process, an electronic catalog of parametric constraints was created that allowed process changes, resulting in a 90% staffing requirements reduction while improving quality and consistency. This new process also supports system level performance optimization by allowing effected sub-system design and development to occur based on the full envelope of permissible locations. Thesis Supervisor: Dr. Daniel E. Whitney Thesis Supervisor: Dr. Ali A. Yassine Title: Senior Research Scientist Title: Research Scientist 2 Acknowledgements Dr. Dan Whitney and Dr. Ali Yassine from the Center for Technology, Policy and Industrial Development at MIT have been instrumental in the development of this thesis' topic and content. Their desire for knowledge and teaching demonstrates their commitment to education and industry. I would like to thank Ford Motor Company for their support while pursuing this degree. Ford's support financially and professionally of individuals who are continuing their education demonstrates the importance of people to its organization. With these types and levels of support, and the people it develops, Ford will continue to be a world class organization. My wife Faith supported my countless hours of school and work with encouragement and motivation. I will always be grateful for her help, patience and understanding. My parents and in-laws have instilled in me a work ethic that has allowed me to thrive both academically and professionally. 3 Table of Contents Page Title Page 1 Abstract 2 Acknowledgements 3 1. Introduction 5 A. Product Development Process 7 B. Types of Design Processes 9 C. Ford's Product Development Process 14 D. C3P Initiative 18 E. Safety Belt Design 19 2. Original Safety Belt Sub-System Design Process 21 3. Design Structure Matrix Methodology (DSM) 26 A. DSM Process Example 26 B. Process Evaluation and Development 30 4. Use of DSM for Safety Belt Validation Process 33 A. Data Collection 33 B. Matrix of the Original Process 37 C. Development of an Improved Process 40 D. Additional DSM Insight 44 E. DSM Limitations 46 F. Re-Engineering Framework Using DSM 47 5. System Engineering and Process Evaluation 50 A. System Types and Evaluation 50 B. Level of Decomposition 52 C. Connectivity Map 54 D. Safety Belt Application 57 6. Electronic Catalog Initiative 65 A. Catalog Concept 65 B. Catalog Hierarchy 66 C. Catalog Item Life Cycle 69 D. Safety Belt Application 71 E. Parametric Constraints 78 F. Item Naming and Numbering Convention 78 G. Launching the Catalog 79 H. Additional Potential Applications 80 7. Conclusion 82 8. References 85 4 1. Introduction The product development process develops and delivers a system on the basis of fulfilling a customer need. The organization and management of the process is dependent on the industry's infrastructure and experiences. Traditionally, complex mechanical systems development begins with decomposing the system into functionally organized sub-systems. The components that make up the sub- system are then optimized for select criteria and integrated to form the system. This top-down approach works well for modular systems with a well-established architecture. When sub-systems are tightly coupled to provide system level attributes, this approach can result in sub-system optimization with non-optimal system level performance. The systems engineering approach and process selected must account for the interactions between the sub-systems and their ability to deliver system level performance. An interconnected sub-system and system mechanical design process insures that constraints are satisfied while allowing for system level multi-attribute optimization. For design problems that are utilizing already available sub-systems or concepts, the use of a selection design process can facilitate this. This thesis investigates a thorough and proactive approach for driving the design process based on using sub-system selection and requirements to define feasible boundaries for the affected system level designs. The case study documented as a part of this thesis involves the automobile safety belt and child seat anchorages design and development process. The 5 primary constraints used to drive this process are regulatory location requirements. These requirements were selected because they are defined spatially, and demonstrating compliance to regulatory requirements is a prerequisite to product market availability. Thus, without exception, they must be satisfied. In addition, these constraints are interrelated with the system level comfort and performance attributes. The original design and development process was evaluated using the Design Structure Matrix (DSM) methodology in order to capture the sub-system interactions, information flows and requirements, along with organizational interactions. Based on an objective evaluation of this model, improvements were identified that resulted in a new process being developed that uses the associativity of CAD files and an electronic catalog of parametric requirements. As a result, the staffing resource requirements to demonstrate compliance with safety belt and child seat anchorage regulatory location requirements have been reduced 90%, saving over $1 million annually. This new process and tools also assure consistent interpretation and demonstration of compliance to the requirements, reduced interfacing system design changes, and improved system level performance. This thesis addresses the problem of how to address systems engineering problems by developing a holistic evaluation of the process, physical system, and functional requirements in order to develop and implement a new process that supports system level performance optimization based on the spatial envelope of permissible locations. This desired approach allows system development to 6 occur in parallel with sub-system design. In addition a new concept called a Connectivity Map was developed. It presents in one array the relationships between the process steps, the functional requirements addressed by each step, and the physical components that participate in delivering those requirements. It is an original approach for identifying the system architecture type, and causes and types of process iteration. The remainder of this chapter provides an overview of the product development process and types of design processes that are a part of it. In addition, information about Ford Motor Company's product development process is presented with background information regarding
Details
-
File Typepdf
-
Upload Time-
-
Content LanguagesEnglish
-
Upload UserAnonymous/Not logged-in
-
File Pages85 Page
-
File Size-