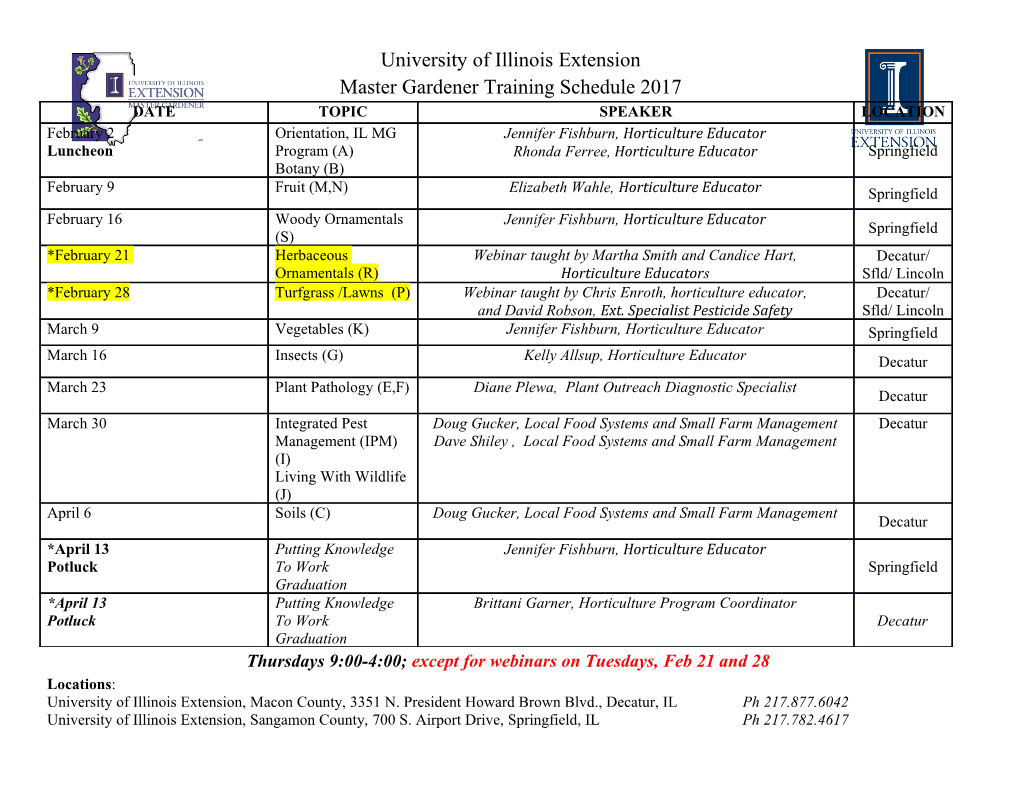
Development and Validation Of a Single Mass Lap Simulation by Jeremy R. Noel Submitted to the Department of Mechanical Engineering in partial fulfillment of the requirements for the degree of Bachelor of Science in Mechanical Engineering at the MASSACHUSETTS INSTITUTE OF TECHNOLOGY May 2020 ○c Massachusetts Institute of Technology 2020. All rights reserved. Author................................................................ Department of Mechanical Engineering May 8, 2020 Certified by. Ian Hunter George N. Hatsopoulos Professor in Thermodynamics Thesis Supervisor Accepted by . Maria Yang Professor of Mechanical Engineering 2 Development and Validation Of a Single Mass Lap Simulation by Jeremy R. Noel Submitted to the Department of Mechanical Engineering on May 8, 2020, in partial fulfillment of the requirements for the degree of Bachelor of Science in Mechanical Engineering Abstract In this thesis, a single mass model lap time simulation was designed, implemented and validated in MATLAB. The goal of this simulation was to accurately predict the velocity of a formula style open wheeled race car on a given track. The simulation was constructed in MATLAB, and features a function based design that will allow the core algorithm to be used with more sophisticated vehicle models. The code was tested and validated using a combination of contrived and collected map data, and a strong correlation of 0.8067 was shown with 95% confidence bounds of 0.8028, and 0.8105. Finally, this thesis outlines proper testing techniques to obtain the data required to complete the validation process of this simulation. Thesis Supervisor: Ian Hunter Title: George N. Hatsopoulos Professor in Thermodynamics 3 4 Acknowledgments There are so many people I would like to thank who have made this research and development project possible. First, of course are my parents and aunt, without whose support and constant requests to please get my stuff out of their garage, I would not have found my passion for vehicle design. Next are the former leaders of the FSAE team, in particular Luis Mora, Cheyenne Hua and Elliot Owen who showed incredible patience with me as I made enough foolish mistakes to learn for myself just how hard developing a a functional car can be. Then are my own FSAE cohort, who made my four years on the team the best possible experience. I thank my friends for putting up with me living in shop for most of my four years, and especially Elizabeth Harkavy for her Latex and editing help. Finally I would like to thank Dr. Christopher Vick, without whom I would never have found myself at MIT. I consider myself truly fortunate to stand on the shoulders of these giants. 5 6 Contents 1 Introduction 13 1.1 Formula SAE Competition . 13 1.2 Team Background . 14 1.3 Motivation . 15 1.4 Objective . 16 1.5 Previous Simulations . 16 2 Design Of Simulation 19 2.1 Vehicle Model . 19 2.2 Simulation Design . 20 2.3 Coordinate systems, and Units . 20 2.4 Assumptions . 21 2.5 High level code structure . 22 2.6 Subsystem Functions . 24 2.6.1 Car Parameters . 24 2.6.2 Path Generation Techniques . 24 2.6.3 Splitting the Lap into Segments . 29 2.6.4 Driver Vision . 32 2.6.5 Driving Function . 33 2.7 Data Visualization . 41 2.7.1 Velocity Plot . 41 2.7.2 Velocity Overlay on Map . 42 7 3 Validation 43 3.1 Validation Goals . 43 3.2 Validation Structure . 43 3.3 Creating Useful Test Cases . 44 3.3.1 Acceleration Run Test Case . 44 3.3.2 Constant Radius Turn . 47 3.3.3 Variable Radius Turn . 50 3.4 Utilization of Testing Data . 51 3.4.1 Small Map Testing . 51 3.4.2 Full Lap Testing . 52 3.5 Next Steps for Validation . 54 3.5.1 Testing Procedure for Simulation . 54 3.5.2 Testing Sweeps to Ensure Predictive Nature . 55 4 Conclusion 57 4.1 Future Work . 57 A Additional Simulated Lap Plots 59 8 List of Figures 1-1 High level block diagram of acceleration simulation [4] . 17 2-1 Vehicle axis system [10] . 21 2-2 High level block diagram of code structure . 23 2-3 Image provided by SAE depicting a single autocross lap [8] . 25 2-4 Overlay of extracted points over the original map . 25 2-5 A car weaves through an autocross slalom section similar to an FSAE track [1] . 27 2-6 Overlay of three different gaussian smoothing windows . 28 2-7 Determining radius and angle from a series of points [3] . 29 2-8 Lap times of 1000 iterations of random segment locations compared to calculated segments . 31 2-9 Example of a simple map split into three segments . 32 2-10 element velocity plot in back step solving . 40 2-11 Final element velocity plot in back step solving . 40 3-1 Model of standard FSAE acceleration track . 45 3-2 Velocity of the car on a straight track shown as a function of distance 46 3-3 Velocity of the car on a straight track shown as a function of distance 47 3-4 Map created using debugging map creator with straights and a constant radius . 48 3-5 Compettiont skidpad course[7] . 49 3-6 The velocity plotted against the distance traveled comparing the sim- ulation to competition results . 50 9 3-7 Velocity of the U-Turn map . 50 3-8 The velocity plotted against the distance traveled . 51 3-9 Velocity of the Variable radius U-Turn map . 51 3-10 The velocity plotted against the step number overlayed with testing data 53 3-11 Velocity shown as colors on the practice map . 53 A-1 The velocity plotted as a function of time overlayed with endurance data 60 A-2 Velocity shown as colors on the endurance map . 60 A-3 The velocity plotted against the step number overlayed with testing data 60 A-4 Velocity shown as colors on the practice map . 60 A-5 The velocity plotted against the step number overlayed with testing data 61 A-6 Velocity shown as colors on the practice map . 61 A-7 The velocity plotted against the step number overlayed with testing data 61 A-8 Velocity shown as colors on the practice map . 61 10 List of Tables 1.1 FSAE Competition Points Breakdown . 14 2.1 Car Parameters . 24 11 12 Chapter 1 Introduction 1.1 Formula SAE Competition The Formula SAE (FSAE) Competition is a collegiate design competition where students deign, build and race an open wheel formula-style racecar. The competition has a series of scored events. These events consist of two separate categories, dynamic and static, and when combined they create a total score upon which a winner is de- cided. The dynamic events test the performance of the car in straight line acceleration (75m drag race: 100 points), skidpad (steady state cornering on a dry surface: 75 points), autocross (single lap around a cone track: 125 points) and endurance (22km auto-cross that includes a change of driver at the midpoint: 275 points plus efficiency: 100 points). The dynamic events make up a total of 675 points [7]. The static events seek to reward excellence in engineering knowledge as well as design decisions. There are three events: cost (points awarded based on proper book keeping and overall cost: 100 points), presentation (a mock business presentation highlighting logistics, production and technical advancement: 75 points) and design (evaluation of engi- neering effort, design goals and overall comprehension of the team: 150 points) [7]. The static events make up a total of 325 points. The competition is a race to collect as many of the 1000 available points as possible. The point breakdown is summarized in table 2.1. 13 Table 1.1: FSAE Competition Points Breakdown Event Points Available Acceleration 100 Skidpad 75 Autocross 125 Endurance 275 Efficiency 100 Cost 100 Presentation 75 Design 150 Total Points 1000 The FSAE competition originated in 1981, and consisted of a total of 6 teams [2]. The internal combustion (IC) competition rapidly grew and now has multiple compe- titions across the United States. In 2013 the first electric variant of the competition was introduced with a partial set of rules. This competition featured 20 registered teams of which 9 made it to the actual competition[9]. In a similar swell the electric competition is now flourishing with the 2019 competition boasting 30 registered teams with 27 making it to competition. 2020 will mark the first year that FSAE has not hosted an in person competition since its inception, due to the COVID-19 pandemic. 1.2 Team Background MIT Motorsports is an FSAE team that competes annually in the electric class. The team is made up of about 40 students who are a mix of mechanical, electrical and software engineers with the occasional business minded student leading the charge to raise enough money to stay afloat. The team is entirely student run, and isledbya few adventurous juniors, who are in way over their heads. MIT Motorsports began in 2001, a small team lead by Nick Gidwani who led the team to build the first IC car. The team grew and climbed the ranks oftheIC competition, culminating in a 16th place finish out of 105 teams competing in 2012. The team then transitioned to the electric competition, and in 2015 successfully built 14 the first electric racecar that ran, although not in time to compete. The team’s performance grew quickly, culminating in a dominant performance in 2018, when the team was disqualified after winning the endurance race by over a minute, due toan alleged overpower event.
Details
-
File Typepdf
-
Upload Time-
-
Content LanguagesEnglish
-
Upload UserAnonymous/Not logged-in
-
File Pages63 Page
-
File Size-