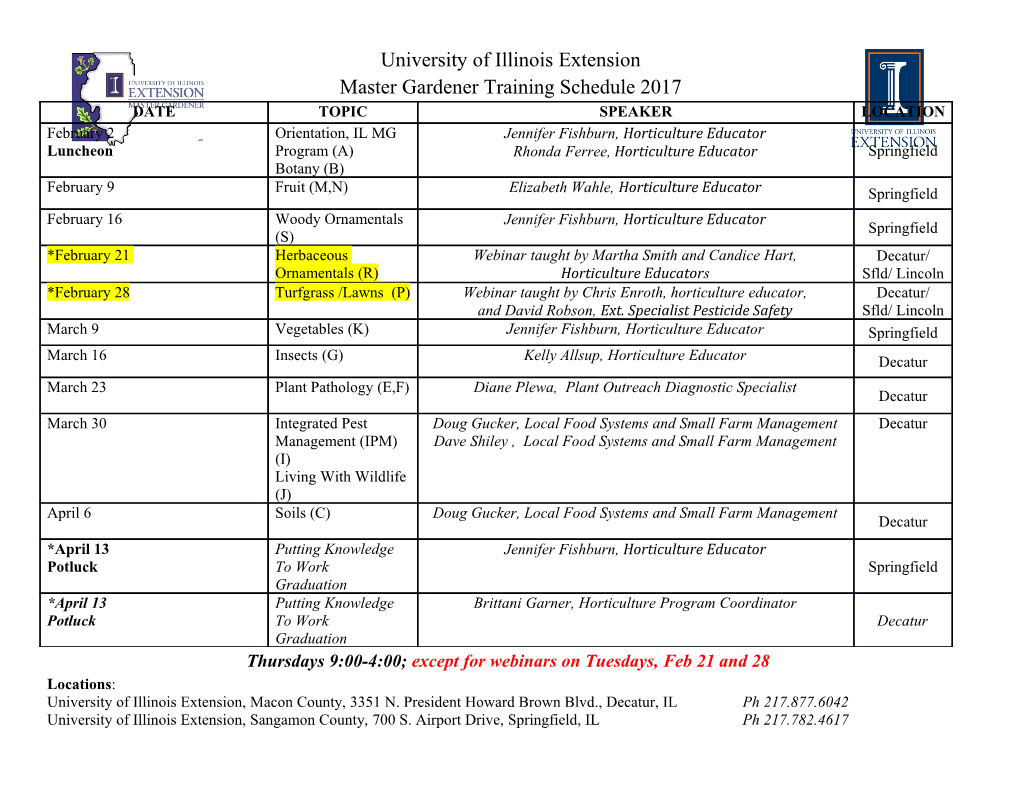
OPTIMIZATION OF CELLULASE-ASSISTED EXTRACTION OF POLYSACCHARIDE FROM COCONUT RESIDUE 1NGA DAO, 2PHANIDA SAIKHWAN Department of Chemical Engineering, Faculty of Engineering, Thammasat University, Thailand E-mail: [email protected], [email protected] Abstract - In the present study, cellulase-assisted extraction of polysaccharides from coconut residue was optimized by response surface methodology (RSM). The optimal extraction parameters comprised an extraction temperature of 59.97°C, an extraction time of 5 h, pH value of 4.53, and cellulase amount of 4000 U/ml. Under these conditions, the relative yield was 6.87%, higher than the yield achieved with conventional methods: Hot water extraction(2.8%) and NaOH extraction(4.87%). Index Terms - Cellulase, coconut, extraction, polysaccharide, response surface method I. INTRODUCTION II. MATERIALS AND METHODS Polysaccharides from natural plants have been used widely in functional foods, dietary supplements, A. Preparation of Coconut Meat Residue health products and cosmetics [1-3]. Polysaccharides provide dietary fiber [3-5] and can be used as an Coconut residue obtained after extraction of coconut emulsifier [2, 6]. Other health benefits, such as milk was collected from local market. The residue was antioxidants, antibacterial, and antidiabetic activity dried at 60oC in an oven to a moisture content of 2-3% have also been reported [7-9]. by weight. This coconut residue (CR) was then The coconut residue obtained after the extraction of defatted with petroleum ether in a Soxhlet apparatus. milk is an inedible byproduct of the coconut milk and Then the residue was washed three times with ethanol virgin coconut oil industry. The use of this residue is before drying at 60°C in an oven to a moisture content currently limited to fertilizer and animal food. of 2–3% by weight. This sample of defatted coconut Recently, the use of polysaccharides extracted from residue (DCR) was kept in an air-tight container at the coconut residue as dietary fiber have been reported room temperature until being used. All the chemicals [4]. used were of analytical grade and purchased from Merck chemicalCo. (Darmstadt, Germany). Hot water and alkali extraction followed by precipitation with alcohol are the most common B. Extraction of polysaccharides techniques used for polysaccharides extraction [9]. Extractions of crude polysaccharides (CP) from both However, these methods require long extraction times CR and DCR were conducted using extraction and high temperatures giving low extraction yields methods explained in next sections. Each extraction [10-11]. The high temperature could also affect method yielded a mixture and CP was obtained from bioactivities of the extracted polysaccharides [5]. the mixture by reducing the mixture to slurry of Enzyme-assisted extraction (EAE) methods are approximately 1/5 of the initial volume using a rotary gaining more attention because of the need for evaporator under vacuum at 60°C (V-850 Buchi eco-friendly extraction [12]. The degradation or vacuum controller). If CR was used, fat layer was disruption of cell walls and membranes, thus removed after this stage using filter paper (Whatman accelerating the mass transfer of target compounds no. 42). After that the obtained slurry was centrifuged into extraction solvent and as a consequence enabling (6000 rpm, 15 min) to obtain supernatant which was a better release and more efficient extraction of then mixed with 95% ethanol at a ratio of 1:3 v/v. This bioactive compounds [13]. Enzymes such as mixture was then allowed to precipitate by keeping the pectinases, cellulases, and hemicellulases have been mixture at 4°C overnight. The precipitate was widely used for pretreatment of plant material prior to collected by filtration (Whatman no. 42) and washed 3 conventional methods for extraction [12], which can times with 80% ethanol to obtain CP samples. All the also significantly reduce the amount of solvent extractions were done in triplicate. requirement. Application of EAE has been proved to For cellulase-assisted extraction (CAE), 10g of be effective for natural ingredients, such as phenolic coconut residue was treated with cellulase (1000, 2000, compounds, oils, and pigments when aiming for high 3000, 4000, 5000 U/ml), pH (3.5, 4, 4.5, 5.0, 5.5), time extraction yields [14-15]. (2, 3, 4, 5, 6 h) and temperature (30, 40, 50, 60, 70°C). Temperature was controlled using a water bath. After In the present study, cellulase-assisted extraction of the enzymolysis, the obtained mixture was heated in a crude polysaccharides was developedand the water bath and stirred (90°C, 1500 rpm, 1 h). extraction conditions were optimized using a response For hot water extraction (HWE), 10g of coconut milk surface method (RSM). residue was added to 0.1M NaOH (1:5 w/v) and the Proceedings of 191st The IIER International Conference, Tokyo, Japan, 26th-27th September, 2018 38 Optimization of Cellulase-Assisted Extraction of Polysaccharide from Coconut Residue mixture was incubated at 55°C for 24 h. This mixture theindependent variables were kept within range, was then filtered and ethanol was added to the filtrate while the Table 1a: Coded and real levels of input (pH 6.0-7.0). parameters involved in experimental design to For sodium hydroxide (NaOH) extraction (NaE), 10 g estimate cellulase-assisted extraction of of coconut milk residue was added to 0.1M NaOH (1:5 polysaccharide. w/v) and the mixture was incubated at 55°C for 24 h. Levels This was then filtered and ethanol was added to the Independent filtrate to give a mixture of pH 6.0-7.0. variables Symbol -2 -1 0 1 2 Enzyme C. Deproteinization amount CP sample was deproteinized following the Sevag (U/ml) X 1000 2000 3000 4000 5000 method as described in [16]. The CP sample was 1 pH X 4.0 4.5 5.0 5.5 6.0 mixed with Sevag reagent (CHCl3:n-BuOH at 5:1 2 Extraction v/v) and stirred for 30 min. Then the mixture was time (hr) X 2 3 4 5 6 centrifuged resulting in Sevag solution layer at the 3 Extraction bottom, CP solution layer at the top and white protein temperature layer in the middle. The PC solution was collected (oC) X 40 50 60 70 80 and further deproteinized with Sevag reagent for 5 4 times until no protein layer was observed. The CP Table 1b: Central composite design matrix and the response solution was ensured to be free of proteins by UV values for the polysaccharide extraction yield. absorption (260 and 280 nm). Ethanol was then added No. Yield X X X X to the CP solution and the mixture was kept at 4°C 1 2 3 4 (%) overnight for CP to precipitate. The precipitates were 1 2000 4.5 3 40 0.73 then collected by centrifugation (6000 rpm, 15 min) 2 4000 4.5 3 40 1.1 and washed successively with acetone and ethanol 3 2000 5.5 3 40 1.96 several times. The washed precipitates then were 4 4000 5.5 3 40 3.9 subjected to lyophilization to get CP. The CP yield 5 2000 4.5 5 40 4.33 (%) was calculated using the following equation: 6 4000 4.5 5 40 6.73 7 2000 5.5 5 40 3.3 Yield Weight of CP (g) 100 (1) 8 4000 5.5 5 40 3.16 (%) Weight of CR (g) 9 2000 4.5 3 60 4.03 10 4000 4.5 3 60 3.07 D. Experimental Design 11 2000 5.5 3 60 3.33 A Central composite experimental design was used to 12 4000 5.5 3 60 3.4 optimize cellulase-assisted extraction conditions of 13 2000 4.5 5 60 4.27 polysaccharides based on the single-factor experiment. 14 4000 4.5 5 60 7.43 Knowing that the enzyme amount (X1), pH (X2), 15 2000 5.5 5 60 5.27 extraction time (X3), extraction temperature (X4), and 16 4000 5.5 5 60 6.83 can significantly influence the yield of CP, a 17 1000 5 4 50 1.93 four-factor model at five levels was selected to 18 5000 5 4 50 5.1 evaluate their interactions.The uncoded levels of four 19 3000 4 4 50 2.37 independent input parameters for the extraction are 20 3000 6 4 50 3.33 listed in Table 1a. The extraction yield of crude 21 3000 5 2 50 2.4 polysaccharide (Y, %) was taken as the dependent 22 3000 5 6 50 5.23 variable of design experiment. The whole design 23 3000 5 4 30 2.9 consisted of 30 experimental points from single-factor 24 3000 5 4 70 4.37 experiments (Table 1b). An empirical second-order 25 3000 5 4 50 3.13 polynomial model was fitted to correlate the response 26 3000 5 4 50 3.1 and independent variables as follows: 27 3000 5 4 50 3.23 4 4 4 28 3000 5 4 50 3.23 2 29 3000 5 4 50 2.8 YXXXX0 i i ii i ij i j i=1 i=1 i < j 2 30 3000 5 4 50 2.87 (2)where Y is the dependent variable, and β0, βi, βii, and βij are the regression coefficients for model response was maximized. Additional triplicate intercept, linear, quadratic, and interaction terms, experimentswere carried out under optimal extraction respectively; while Xi and Xj are the independent conditions in order to determine the validity of variables. optimized conditions. The average value of the Numerical optimization was carried out to predict the validation experiment was compared with the exact optimum level of independent variables leading predicted value of the developed condition in order to to the desirable response goal.
Details
-
File Typepdf
-
Upload Time-
-
Content LanguagesEnglish
-
Upload UserAnonymous/Not logged-in
-
File Pages6 Page
-
File Size-