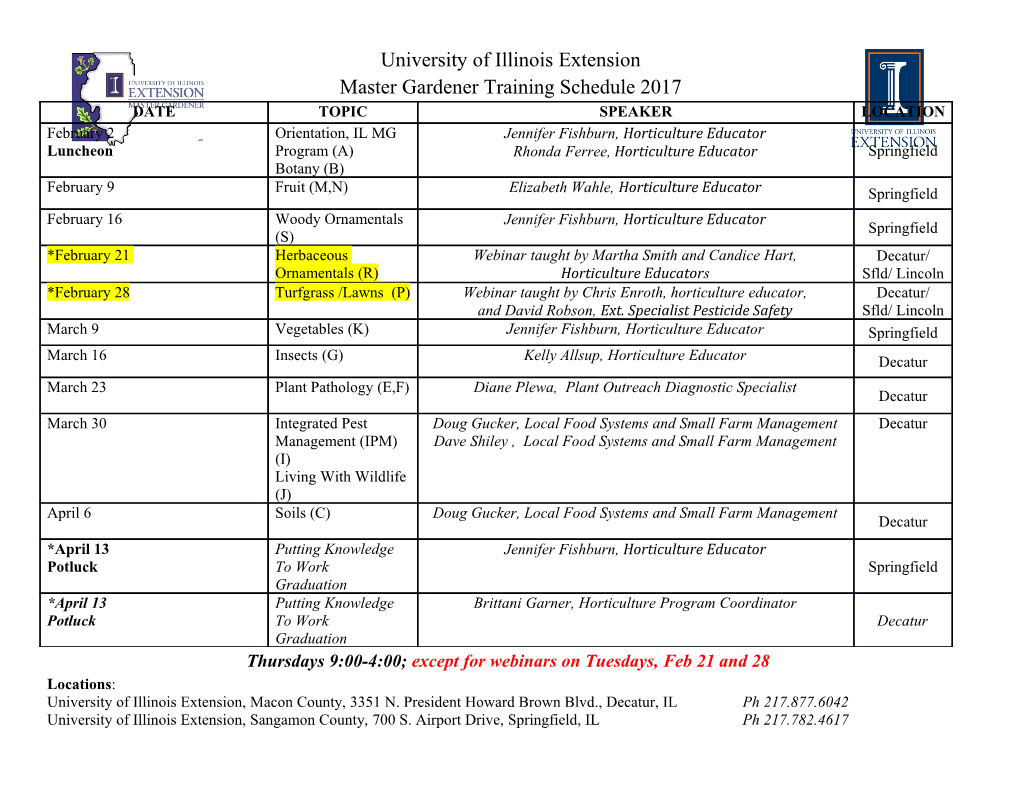
A Thesis entitled Ultraviolet Bonding of Diamond Abrasive Tools for Lap-Grinding Process by Lei Guo Submitted to the Graduate Faculty as partial fulfillment of the requirements for the Master of Science Degree in Mechanical Engineering _________________________________________ Dr. Ioan D. Marinescu, Committee Chair _________________________________________ Dr. Hongyan Zhang, Committee Member _________________________________________ Dr. Sarit Bhaduri, Committee Member _________________________________________ Dr. Patricia R. Komuniecki, Dean College of Graduate Studies The University of Toledo December 2012 Copyright 2012, Lei Guo This document is copyrighted material. Under copyright law, no parts of this document may be reproduced without the expressed permission of the author An Abstract of Ultraviolet Bonding of Diamond Abrasive Tools for Lap-Grinding Process by Lei Guo Submitted to the Graduate Faculty as partial fulfillment of the requirements for the Master of Science Degree in Mechanical Engineering The University of Toledo December 2012 Different from grinding, the lapping process is always taken place on higher precision machining process at low speed and low pressure. Conventional lapping process is based on a slurry process, abrasive particles mixed with lapping fluid supplied during the process and the abrasives keep rolling and scratching in the working zone. By these actions, the material is removed from the work piece. As known, the lapping efficiency is limited due to the abrasion mechanism that is illustrated as three-body abrasion. In order to improve the lapping efficiency and surface finishing, a novel manufacturing method of lapping plate fabrication is proposed in this research. Since the ultraviolet-curable resin first introduced to industry, the rapid prototyping technology developed significantly and become one of the most important techniques. Recently, researchers studied on the manufacturing of abrasive tools by ultraviolet-curable resin and some promising achievements have been made. Therefore, our idea is typically base on the rapid prototyping technique. By curing the mixture of ultraviolet-curable resin and abrasive particle to fabricate the lapping plate, the grains bonded within the mixture. Thus, the abrasion type during lapping change from three- iii body mechanism to two-body mechanism and the lapping efficiency can be improved then. In this research, the material properties of the ultraviolet-curable resin and mixture are studied. The optimum combination of resin and diamond abrasive is selected. Moreover, in order to see the practical lapping performance, the lapping plate is developed. Based on rigid brittle material lapping experiments, the lapping efficiency and surface finishing is discussed and concluded. At last, two ways to improve the performance of lapping plate is carried out. One of them is based on the influence of abrasive type, and the other one focused on the polymerization of resin and bonding strength of the mixture. iv This thesis is dedicated to my parents, Yaohui Guo and Aimin Zhang. Thank you for bringing me to this world and give me unconditional love and support. XieXie, Wo Ai NiMen. v Acknowledgements I wish to convey my deepest appreciation to Dr.Marinescu, my advisor, for his enthusiasm, dedication, and expertise. Thanks for his continued concern and support through my study. I would like to thank the group member of PMMC and Mr.Todd.Gearig. I really appreciate their help in my study and experiments. I would also like to show my gratitudes to the MIME machine shop staff members Mr. John Jaegly, Mr. Tim GrIvanos and Mr. Randall Reihing. This research could not have gone so far without their help. Finally, I want to say thanks to my girlfriend, Ting Wen. Thanks for your love and support. I love you. vi Table of Contents Abstract ............................................................................................................................... iii Acknowledgements ............................................................................................................. vi Table of Contents ............................................................................................................... vii List of Tables .......................................................................................................................x List of Figures ..................................................................................................................... xi List of Abbreviations ........................................................................................................ xiv 1 Introduction ...................................................................................................................... 1 1.1 Overview ................................................................................................................... 1 1.2 Research Objective.................................................................................................... 3 2 Lapping Processes............................................................................................................ 5 2.1 Introduction ............................................................................................................... 5 2.2 Two-Body and Three-Body Abrasion (Mechanisms) ............................................... 6 2.3 Classification of Lapping Process ........................................................................... 11 2.3.1 Single Side Lapping.......................................................................................... 13 2.3.2 Double Side Lapping ........................................................................................ 14 vii 2.3.3 Cylindrical Lapping .......................................................................................... 15 2.4 Lapping Component ................................................................................................ 16 2.4.1 Lapping Plate .................................................................................................... 16 2.4.2 Lapping slurry and fluid ................................................................................... 21 2.4.3 Lapping Abrasive.............................................................................................. 22 3 Ultraviolet-Curable Resin .............................................................................................. 24 3.1 Ultraviolet-Curable Resin Research Development ................................................. 24 3.2 UV-Curable Resin Introduction .............................................................................. 28 3.3 Key Factors in the UV-Curing Process ................................................................... 30 3.4 Bonding Mechanism of Abrasives .......................................................................... 31 3.4.1 Mechanical Bonding ......................................................................................... 31 3.4.2 Adsorption bonding .......................................................................................... 33 4 Experiments Design and Set up ..................................................................................... 34 4.1 Material and Equipment Preparation....................................................................... 34 4.1.1 Ultraviolet-Curable Resins ............................................................................... 34 4.1.2 Abrasive Particles ............................................................................................. 35 4.1.3 Ultraviolet Curing System ................................................................................ 37 4.1.4 Lapping Machine .............................................................................................. 41 4.2 Experimental Procedure .......................................................................................... 41 viii 4.2.1 Tensile Strength ................................................................................................ 41 4.2.2 Porosity ............................................................................................................. 44 4.2.3 Hardness and Wear Resistance ......................................................................... 46 4.3 Manufacturing of the Lapping Plate........................................................................ 50 4.3.1 Spin-Curing Method ......................................................................................... 50 4.3.2 Slices Curing Method ....................................................................................... 51 4.4 Silicon Wafer Lapping Experimental Program ....................................................... 53 5 Optimization and Improvements in Lapping Performances .......................................... 56 5.1 MA Abrasive and Surface Treated MA Abrasive ................................................... 56 5.1.1 Lapping Experimental on Aluminum Oxide .................................................... 57 5.1.2 Experiments Results and Discussion ................................................................ 59 5.2 Influence of Nano-Particle Additives...................................................................... 63 5.2.1 Nano-Particle Additives Introduction ............................................................... 63 5.2.2 Nano-Particle mixed Resin Material Experiment Details ................................ 64 5.2.3 Lapping Performance
Details
-
File Typepdf
-
Upload Time-
-
Content LanguagesEnglish
-
Upload UserAnonymous/Not logged-in
-
File Pages91 Page
-
File Size-