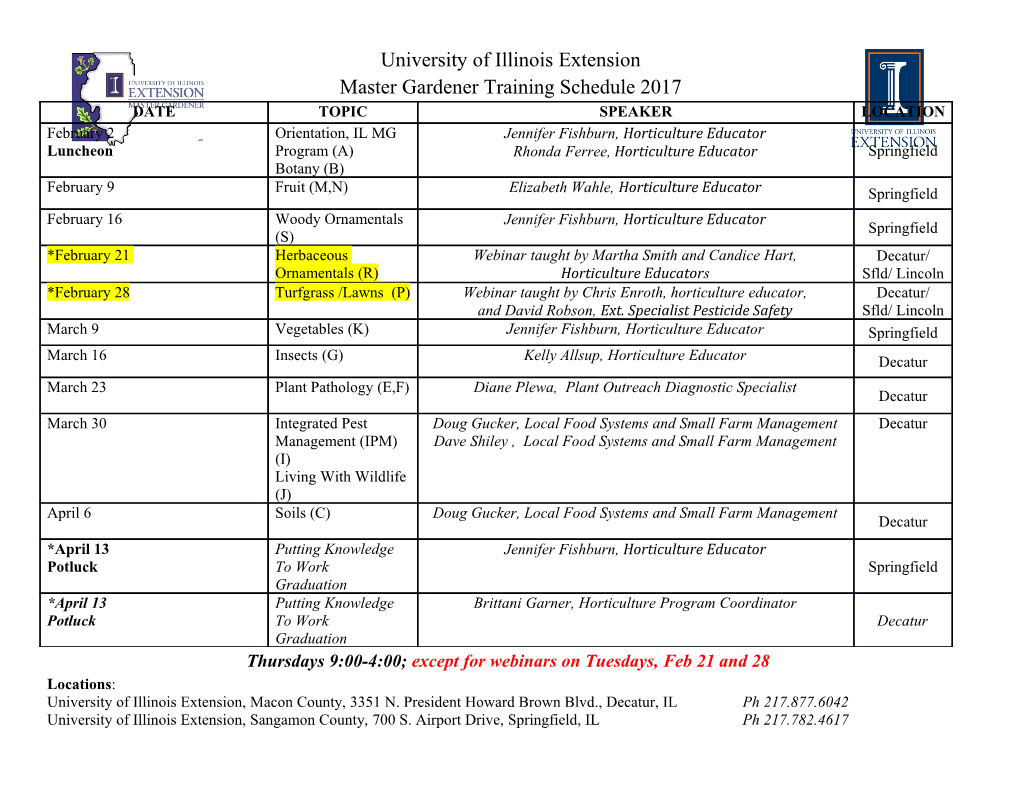
<p>CHARACTERIZATION OF COPPER ELECTROPLATING AND <br>ELECTROPOLISHING PROCESSES FOR SEMICONDUCTOR INTERCONNECT <br>METALLIZATION </p><p>by <br>JULIE MARIE MENDEZ </p><p>Submitted in partial fulfillment of the requirements <br>For the degree of Doctor of Philosophy </p><p>Dissertation Advisor: Dr. Uziel Landau Department of Chemical Engineering <br>CASE WESTERN RESERVE UNIVERSITY </p><p>August, 2009 </p><p><strong>CASE WESTERN RESERVE UNIVERSITY </strong><br><strong>SCHOOL OF GRADUATE STUDIES </strong></p><p>We hereby approve the thesis/dissertation of </p><p>Julie Mendez </p><p>_____________________________________________________ </p><p>PhD </p><p>candidate for the ______________________degree *. </p><p>Uziel Landau </p><p>(signed)_______________________________________________ <br>(chair of the committee) </p><p>Heidi B. Martin </p><p>________________________________________________ </p><p>Frank Ernst </p><p>________________________________________________ </p><p>Chung-Chiun Liu </p><p>________________________________________________ ________________________________________________ ________________________________________________ </p><p>May 12, 2009 </p><p>(date) _______________________ *We also certify that written approval has been obtained for any proprietary material contained therein. </p><p><strong>TABLE OF CONTENTS </strong></p><p><em>Page Number </em></p><p>List of Tables List of Figures Acknowledgements List of Symbols Abstract <br>34910 13 </p><p></p><ul style="display: flex;"><li style="flex:1">1. Introduction </li><li style="flex:1">15 </li></ul><p>15 20 22 24 <br>1.1 Semiconductor Interconnect Metallization – Process Description 1.2 Mechanistic Aspects of Bottom-up Fill 1.3 Electropolishing 1.4 Topics Addressed in the Dissertation </p><p>2. Experimental Studies of Copper Electropolishing <br>2.1 Experimental Procedure <br>26 29 30 34 34 36 38 40 42 44 49 51 52 <br>2.2 Polarization Studies 2.3 Current Steps <br>2.3.1 Current Stepped to a Level below Limiting Current 2.3.2 Current Stepped to the Limiting Current Plateau 2.3.3 Effect of Current Density 2.3.4 Effect of Rotation Speed <br>2.4 Highly Resistive Surface Film 2.5 Electrochemical Impedance Spectroscopy 2.6 Stability of the Film in Presence of Chloride 2.7 Two-Compartment Cell Experiments 2.8 Conclusions </p><p>3. A Mechanistic Model for Copper Electropolishing <br>3.1 Regime I – Buildup of Surface Copper Ion Concentration 3.2 Regime II – Controlling Transport through a Surface Layer 3.3 Model Verification <br>53 53 57 60 67 67 72 <br>3.3.1 Time Delay Prior to the Onset of the Sharp Potential Increase 3.3.2 Effect of Water Concentration on the Limiting Current <br>3.4 Conclusions </p><p>4. Novel Polyether Suppressors Enabling Copper Metallization of High Aspect Ratio </p><ul style="display: flex;"><li style="flex:1">Interconnects </li><li style="flex:1">73 </li></ul><p>75 76 79 89 96 98 <br>4.1 Experimental Procedure 4.2 Results and Discussion <br>4.2.1 Polarization Data 4.2.2 Modeled Via-fill Ratio 4.2.3 Interaction with the Anti-suppressor <br>4.3 Conclusions </p><p>1<br>5. Mechanistic Studies of Polyether Adsorption <br>5.1 Experimental Details <br>99 101 <br>5.1.1 Attenuated Total Reflectance Fourier Transform Infrared Spectroscopy </p><ul style="display: flex;"><li style="flex:1">(ATR-FTIR) </li><li style="flex:1">101 </li></ul><p>103 106 118 125 127 <br>5.1.2 Quartz Crystal Microbalance (QCM) <br>5.2 ATR-FTIR Studies of PEG Adsorption 5.3 Quartz Crystal Microbalance 5.4 Effect of Cu<sup style="top: -0.46em;">+ </sup>on Copper Deposition 5.5 Conclusions </p><p>6. Major Conclusions and Recommendations for Future Work <br>6.1 Major Conclusions <br>128 128 128 129 131 <br>6.1.1 Electropolishing 6.1.2 Novel Polyethers Extending Gap-fill Capabilities <br>6.2 Recommendations for Further Studies </p><p></p><ul style="display: flex;"><li style="flex:1">Bibliography </li><li style="flex:1">135 </li></ul><p>2</p><p><strong>LIST OF TABLES </strong></p><p><em>Page </em><br><em>Number </em></p><p></p><ul style="display: flex;"><li style="flex:1">48 </li><li style="flex:1"><strong>Table 2.1. </strong>Ohmic and polarization resistances measured by electrochemical </li></ul><p>impedance spectroscopy. </p><p></p><ul style="display: flex;"><li style="flex:1"><strong>Table 3.1. </strong>Copper electropolishing model parameters. Justification for the </li><li style="flex:1">61 </li></ul><p>estimated values is given in the text. </p><p></p><ul style="display: flex;"><li style="flex:1"><strong>Table 4.1. </strong>Polyethers explored in the polarization studies. </li><li style="flex:1">77 </li></ul><p></p><ul style="display: flex;"><li style="flex:1">90 </li><li style="flex:1"><strong>Table 4.2. </strong>Kinetics parameters fitted to polarization data in Figure 4.1 and </li></ul><p>Figure 4.2. </p><p>3</p><p><strong>LIST OF FIGURES </strong></p><p><em>Page </em><br><em>Number </em></p><p></p><ul style="display: flex;"><li style="flex:1">17 </li><li style="flex:1"><strong>Figure 1.1. </strong>Schematic detailing the dual Damascene process. Both (a) the </li></ul><p>via and (b) the trench are etched into the insulator. (c) A diffusion barrier layer and copper seed layer are both deposited by physical vapor deposition. (d) Copper is electrodeposited to fill the via and trench. (e) The overburden copper is removed by chemical mechanical planarization (CMP). </p><p><strong>Figure 1.2. </strong>Schematic of the transport and diffusion processes inside the via. (a) PEG adsorbs quickly but is diffusion limited; therefore, it adsorbs primarily at the top of the via sidewalls. SPS diffuses quickly but adsorbs more slowly than PEG and adsorbs primarily at the via bottom. (b) As the fill progresses, the bottom surface contracts. The SPS becomes more concentrated at the bottom, bringing about rapid growth at the via bottom. <br>19 </p><ul style="display: flex;"><li style="flex:1">28 </li><li style="flex:1"><strong>Figure 2.1. </strong>Schematic of concentration profiles in the two major proposed </li></ul><p>mechanisms for copper electropolishing. In mechanism (a), an acceptor species (indicated as water) diffuses towards the anode, complexes there with the discharged cupric ions, and diffuses back (as a complex) toward the bulk solution. According to mechanism (b), the concentration of cupric ions increases at the anode until the solubility limit is reached, at which point, a solid film is formed on the anode. Cupric ions then diffuse towards the bulk across a mass transport boundary layer of thickness δ. </p><p><strong>Figure 2.2. </strong>Polarization curves for electropolishing of a copper disk electrode at various rotation speeds (A – 50 rpm, B – 100 rpm, C – 200 rpm, D – 400 rpm, E – 600 rpm) in 85 wt% phosphoric acid. The potential was scanned at 10 mV/s. <br>32 </p><ul style="display: flex;"><li style="flex:1">33 </li><li style="flex:1"><strong>Figure 2.3. </strong>Limiting current density for phosphoric acid solutions of various </li></ul><p>water concentrations at 800 rpm. The linear relationship between limiting current density and bulk water concentration has led numerous investigators to associate it with the transport of an acceptor species (water) toward the anode. </p><p><strong>Figure 2.4. </strong>Potential response to a current pulse at 100 rpm (a) below the limiting current (6.3 mA/cm<sup style="top: -0.46em;">2</sup>), and (b) at the limiting current (19.6 mA/cm<sup style="top: -0.46em;">2</sup>). The current is stepped up to the specified value at 100 s, held at that value for 400 s, and then stepped down to zero at 500 s. Note that the potential scales in (a) and (b) are quite different. <br>35 <br>4<br><strong>Figure 2.5. </strong>Potential transient responses to current steps from zero to three values on the limiting current plateau. The current was stepped to (A) 18.8 mA/cm<sup style="top: -0.46em;">2</sup>; (B) 17.8 mA/cm<sup style="top: -0.46em;">2</sup>; (C) 17.0 mA/cm<sup style="top: -0.46em;">2 </sup>at 100 s. The disk was rotated at 100 rpm. <br>39 </p><ul style="display: flex;"><li style="flex:1">41 </li><li style="flex:1"><strong>Figure 2.6</strong>. Potential responses to currents steps from zero to 19.6 mA/cm<sup style="top: -0.46em;">2 </sup></li></ul><p>(at the limiting current) for various rotation speeds: A – 90 rpm, B – 100 rpm, C – 110 rpm. The time delay prior to the sharp potential increase shows a strong dependence on the rotation speed. </p><p><strong>Figure 2.7. </strong>Nyquist plots at various applied potentials below the limiting current at 400 rpm. The ohmic resistance remains approximately constant, but the polarization resistance decreases as the potential is increased. <br>46 </p><ul style="display: flex;"><li style="flex:1">47 </li><li style="flex:1"><strong>Figure 2.8. </strong>Nyquist plots at an applied potential of 1.3 V vs. copper (at the </li></ul><p>limiting current plateau) and various rotation speeds. These measurements indicate an ohmic resistance of approximately 2.8 Ω-cm<sup style="top: -0.46em;">2 </sup>and a polarization resistance between 1.6 and 3.4 Ω-cm<sup style="top: -0.46em;">2</sup>, which decreases with increasing rotation speed. </p><p><strong>Figure 2.9. </strong>Potential response to current step of 14.2 mA/cm<sup style="top: -0.46em;">2 </sup>(near the limiting current) in 85 wt% H<sub style="top: 0.125em;">3</sub>PO<sub style="top: 0.125em;">4 </sub>solution containing 100 ppm HCl. The potential oscillations suggest the formation and breakdown of a film. <br>50 </p><ul style="display: flex;"><li style="flex:1">54 </li><li style="flex:1"><strong>Figure 3.1 </strong>Schematics representing (a) Regime I and (b) Regime II of the </li></ul><p>proposed model. In Regime I, the concentration at the anode increases until <em>C</em><sub style="top: 0.125em;"><em>sat </em></sub>is reached. In Regime II, a flux imbalance leads to the buildup in thickness (<em>x</em>) of a surface film. </p><p><strong>Figure 3.2. </strong>Comparison of measured and modeled overpotential response to a current pulse in Regime I. The measured data are from Figure 2.4a, while the predicted response is based on the numerical solution of Eqs. [3.1] and [3.5]. The two curves are in reasonable agreement. The small deviation can probably be attributed to the spatial distribution of the copper ions. <br>63 <br><strong>Figure 3.3. </strong>Comparison of the model governing Regime II (Eq. [3.12]) to the experimental potential response displayed in Figure 2.4b (region C-D). Note the highly expanded time scale. <br>65 </p><ul style="display: flex;"><li style="flex:1">66 </li><li style="flex:1"><strong>Figure 3.4. </strong>Sensitivity analysis for parameters <em>A </em>and <em>M </em>(Eq. [3.12]). The </li></ul><p>lines indicate values for these parameters such that the model correlates the data from Figure 2.4b (region C-D) within the indicated percentages. </p><p>5<br><strong>Figure 3.5. </strong>The model (Eq. [3.22]) predicts a nearly linear relationship between the limiting current density and the bulk water concentration for copper electrodissolution in phosphoric acid. Also indicated is a linear approximation for Eq. [3.22]. <br>71 </p><ul style="display: flex;"><li style="flex:1">80 </li><li style="flex:1"><strong>Figure 4.1. </strong>Polarization data for solutions containing 0.5 M CuSO<sub style="top: 0.125em;">4 </sub>(pH~2), </li></ul><p>70 ppm Cl<sup style="top: -0.46em;">-</sup>, and 100 ppm of the specified polyether, all with molecular mass of approximately 1000 g/mol. The points for polyoxyethylene lauryl ether (diamonds) and polyoxyethylene cetyl ether (circles) fall nearly on top of one another. </p><p><strong>Figure 4.2. </strong>Polarization data for solutions containing 0.5 M CuSO<sub style="top: 0.125em;">4 </sub>(pH~2), 70 ppm Cl<sup style="top: -0.46em;">-</sup>, and 100 ppm of the specified polyether with molecular mass of approximately 600 g/mol. <br>82 83 85 86 88 <br><strong>Figure 4.3. </strong>Polarization data for additional solutions containing 0.5 M CuSO<sub style="top: 0.125em;">4 </sub>(pH~2), 70 ppm Cl<sup style="top: -0.46em;">-</sup>, and 100 ppm of the specified polyether with molecular mass of approximately 600 g/mol. </p><p><strong>Figure 4.4. </strong>Polarization data for solutions containing 0.5 M CuSO<sub style="top: 0.125em;">4 </sub>(pH~2), 70 ppm Cl<sup style="top: -0.46em;">-</sup>, and 100 ppm of the specified polyether with molecular mass of approximately 300 g/mol. </p><p><strong>Figure 4.5. </strong>Polarization data for solutions containing 0.5 M CuSO<sub style="top: 0.125em;">4 </sub>(pH~2), 70 ppm Cl<sup style="top: -0.46em;">-</sup>, and 100 ppm of the specified polyether with molecular mass in the range of approximately 2000 g/mol to 4000 g/mol. </p><p><strong>Figure 4.6. </strong>Overpotentials at 5 mA/cm<sup style="top: -0.46em;">2 </sup>as a function of the number of ether oxygen atoms in the polyether. The circles correspond to PEG, and the squares are all other polyethers studied (listed in Table 4.1). Although some trend is indicated between increased overpotential and the number of ethereal oxygen atoms, the data spread implies that other factors, including the chemical structure, are important. </p><p><strong>Figure 4.7. </strong>Bottom-up fill ratio (<em>i</em><sub style="top: 0.125em;"><em>B</em></sub>/<em>i</em><sub style="top: 0.125em;"><em>SW</em></sub>) as a function of total current simulated for a 300 mm wafer with 15% feature loading (pattern density) for solutions containing one of the following suppressors: PEG 1000, polyoxyethylene lauryl ether, or polyoxyethylated β-naphthol. Significant improvement (3 ~ 4x) is expected by replacing PEG with either of the above listed other polyethers. <br>93 <br>6<br><strong>Figure 4.8. </strong>SEM cross-sections of vias with aspect ratio close to 10 electroplated with copper after PVD seed deposition.<sup style="top: -0.46em;">48 </sup>Fill quality is compared for copper plating in the presence of two different suppressors: (a) PEG 1000, exhibiting center-line voids due to inferior bottom-up fill rate (Figure 4.7), and (b) polyoxyethylated (POE) β-naphthol, indicating voidfree fill on account of its improved suppression and higher bottom-up fill rate. <br>95 </p><ul style="display: flex;"><li style="flex:1">97 </li><li style="flex:1"><strong>Figure 4.9. </strong>Voltage transient response at 5 mA/cm<sup style="top: -0.46em;">2 </sup>to SPS injections into </li></ul><p>polyether polarized deposition. The solution initially contained 0.5 M CuSO<sub style="top: 0.125em;">4 </sub>(pH~2), 70 ppm Cl<sup style="top: -0.46em;">-</sup>, and 100 ppm of the specified polyether. After steady-state was reached, 10 ppm SPS was injected into the solution. Polyoxyethylated β-naphthol has a similar voltage response to that of PEG. </p><p><strong>Figure 5.1. </strong>Schematic of ATR-FTIR system (not to scale). The laser beam is introduced from the back, through a thin Si wafer coated with Cu. Only a thin region (~1 μm) at the electrode/electrolyte interface is sampled. <br>102 105 108 <br><strong>Figure 5.2. </strong>Schematic of QCM cell (not to scale). The top electrode is exposed to the solution, while the bottom electrode is in contact with air, serving as the reference. </p><p><strong>Figure 5.3. </strong>Spectrum for solid PEG relative to ZnSe-air. The most prominent peaks are the C-O-C stretch at 1109 cm<sup style="top: -0.46em;">-1 </sup>and the C-H stretch at 2885 cm<sup style="top: -0.46em;">-1</sup>. Since it is believed that the ethereal oxygen is important in the adsorption of polyethers, the C-O-C stretch peak is of interest. </p><p><strong>Figure 5.4. </strong>Spectrum for solid cupric sulfate pentahydrate relative to ZnSeair. The most prominent peaks are at 670, 3630, and 3730 cm<sup style="top: -0.46em;">-1</sup>. There is also a peak at 1090 cm<sup style="top: -0.46em;">-1</sup>, which is near the C-O-C stretch peak of PEG at 1100 cm<sup style="top: -0.46em;">-1</sup>. <br>109 110 112 <br><strong>Figure 5.5. </strong>Spectrum for 0.5 M CuSO<sub style="top: 0.125em;">4 </sub>and 70 ppm Cl<sup style="top: -0.46em;">- </sup>on a Cu substrate, relative to water. A prominent sulfate peak is evident at 1100 cm<sup style="top: -0.46em;">-1</sup>, near a peak of interest for PEG. The peaks at 3280 and 1640 cm<sup style="top: -0.46em;">-1 </sup>are due to error in referencing to the spectrum for water on Cu. </p><p><strong>Figure 5.6. </strong>FTIR spectra for solutions containing 0.5 M CuSO<sub style="top: 0.125em;">4</sub>, 70 ppm Cl<sup style="top: -0.46em;">-</sup>, and 100 ppm PEG 1000 on Cu (bottom) and on Si (top) substrates. The spectra indicate similar behavior on both Si and Cu. The spectra were shifted vertically for clarity. </p><p>7<br><strong>Figure 5.7. </strong>Spectra for various solutions on Cu. The solutions contain the specified components in the following concentrations: 0.5 M CuSO<sub style="top: 0.125em;">4</sub>, 70 ppm Cl<sup style="top: -0.46em;">-</sup>, 100 ppm PEG 1000, and 0.67 M Na<sub style="top: 0.125em;">2</sub>SO<sub style="top: 0.125em;">4</sub>. No peak is observed with a solution of 100 ppm PEG and 70 ppm Cl<sup style="top: -0.46em;">- </sup>in water. <br>114 <br><strong>Figure 5.8. </strong>FTIR spectrum for a solution containing 0.5 M CuCl<sub style="top: 0.125em;">2 </sub>and 100 ppm PEG 1000, relative to 0.5 M CuCl<sub style="top: 0.125em;">2</sub>. The C-O-C stretch peak of PEG at 1100 cm<sup style="top: -0.46em;">-1 </sup>can be detected in the absence of sulfate. <br>115 </p><ul style="display: flex;"><li style="flex:1">117 </li><li style="flex:1"><strong>Figure 5.9. </strong>FTIR spectrum for a solution containing 0.5 M CuSO<sub style="top: 0.125em;">4</sub>, 70 ppm </li></ul><p>Cl<sup style="top: -0.46em;">-</sup>, and 100 ppm PEG 1000, relative to 0.5 M CuSO<sub style="top: 0.125em;">4 </sub>and 70 ppm Cl<sup style="top: -0.46em;">-</sup>. Different solutions were introduced using a flow cell. A peak associated with the C-O-C stretch of PEG is evident at 1100 cm<sup style="top: -0.46em;">-1</sup>. </p><p><strong>Figure 5.10. </strong>Frequency response upon addition of small volumes of 0.5 M CuSO4 to the cell initially containing 0.5 M CuSO<sub style="top: 0.125em;">4 </sub>solution. The arrows indicate times when additional solution was introduced into the cell. The frequency signal stabilizes to nearly the original value, indicating that additional solution does not affect adsorption on the substrate. <br>119 </p><ul style="display: flex;"><li style="flex:1">121 </li><li style="flex:1"><strong>Figure 5.11. </strong>Frequency response upon addition of Cl<sup style="top: -0.46em;">- </sup>and PEG to a 0.5 M </li></ul><p>CuSO<sub style="top: 0.125em;">4 </sub>solution. When 70 ppm Cl<sup style="top: -0.46em;">- </sup>was added to the cell, a change in frequency difference of ~30 Hz, corresponding to ~130 ng/cm<sup style="top: -0.46em;">2</sup>, was observed. When 100 ppm PEG (molecular mass 1000 g/mol) was added to the Cl<sup style="top: -0.46em;">-</sup>-containing solution, a similar change in frequency difference of ~30 Hz (~130 ng/cm<sup style="top: -0.46em;">2</sup>) was observed. </p><p><strong>Figure 5.12. </strong>Frequency response upon addition of PEG and Cl<sup style="top: -0.46em;">- </sup>to a 0.5 M CuSO<sub style="top: 0.125em;">4 </sub>solution. When 100 ppm PEG (molecular mass 1000 g/mol) was added, a small decrease in the frequency difference was observed. When 70 ppm Cl<sup style="top: -0.46em;">- </sup>was added to the PEG-containing solution, an increase in frequency difference of ~50 Hz (~220 ng/cm<sup style="top: -0.46em;">2</sup>) was observed. <br>123 </p><ul style="display: flex;"><li style="flex:1">126 </li><li style="flex:1"><strong>Figure 5.13. </strong>Overpotential response to injection of 10 ppm Cu<sup style="top: -0.46em;">+ </sup>into </li></ul><p>acidified (pH~2) 0.5 M CuSO<sub style="top: 0.125em;">4 </sub>solutions containing the indicated additives. The cathode was polarized at 10 mA/cm<sup style="top: -0.46em;">2</sup>. When Cu<sup style="top: -0.46em;">+ </sup>is added to a solution containing no additives, the overpotential decreases by ~30 mV. No change in overpotential is observed when Cu<sup style="top: -0.46em;">+ </sup>is added to solutions containing PEG or PEG and Cl<sup style="top: -0.46em;">-</sup>. </p><p>8</p><p><strong>Acknowledgements </strong></p><p>I would like to thank Professor Uziel Landau for his guidance in the completion of this dissertation. I would also like to thank the other members of my committee, Professor Heidi Martin, Professor C. C. Liu, and Professor Frank Ernst for helpful comments and suggestions regarding this work. <br>Funding from the Intel Research Council supported this work. I would like to thank Rohan Akolkar at Intel for his collaboration in this work and for the opportunity to spend a summer working at Intel. I also thank Tatyana Andryushchenko at Intel for contributions to the electropolishing work. <br>I would like to thank Jim Adolf for helpful suggestions regarding the polyether work and the students in the Landau Group for their helpful comments and support. Professor Heidi Martin assisted with the FTIR measurements. Professor Kathleen Kash provided assistance with electron beam deposition. Professor Jim Burgess and Professor Robert Savinell provided use of QCM equipment. Craig Virnelson and Dan Shelberg assisted with data acquisition for the QCM. Cliff Hayman and the students in the Diamond Lab have helped with various things in the lab. Professor E. Gileadi and Professor J. Newman are acknowledged for helpful discussions regarding electropolishing. <br>I appreciate the support and encouragement from my parents, sister, and extended family. I am grateful to the friends I have made here in the last four years. <br>To J.D., my husband, thank you for your understanding and for always being there for me. </p><p>9</p><p><strong>List of Symbols </strong></p><p>film resistance parameter (Eq. [3.11]) </p><p><em>A</em></p><p><em>A</em><sub style="top: 0.125em;"><em>B </em></sub><em>A</em><sub style="top: 0.125em;"><em>supp </em></sub></p><p><em>B</em></p><p>area at bottom of features area at feature sidewalls and wafer top surface film resistance parameter (Eq. [3.11]) Cu<sup style="top: -0.46em;">2+ </sup>concentration </p><p><em>C</em></p><p><em>C</em><sub style="top: 0.125em;"><em>b </em></sub><em>C</em><sub style="top: 0.125em;"><em>e </em></sub></p><p>bulk Cu<sup style="top: -0.46em;">2+ </sup>concentration Cu<sup style="top: -0.46em;">2+ </sup>concentration near the electrode concentration of water </p><p><em>C</em><sub style="top: 0.125em;"><em>H2O </em></sub></p><p><em>C</em><sub style="top: 0.125em;"><em>H3PO4 </em></sub>concentration of phosphoric acid </p><p><em>C</em><sub style="top: 0.125em;"><em>m </em></sub><em>C</em><sub style="top: 0.125em;"><em>sat </em></sub></p>
Details
-
File Typepdf
-
Upload Time-
-
Content LanguagesEnglish
-
Upload UserAnonymous/Not logged-in
-
File Pages140 Page
-
File Size-