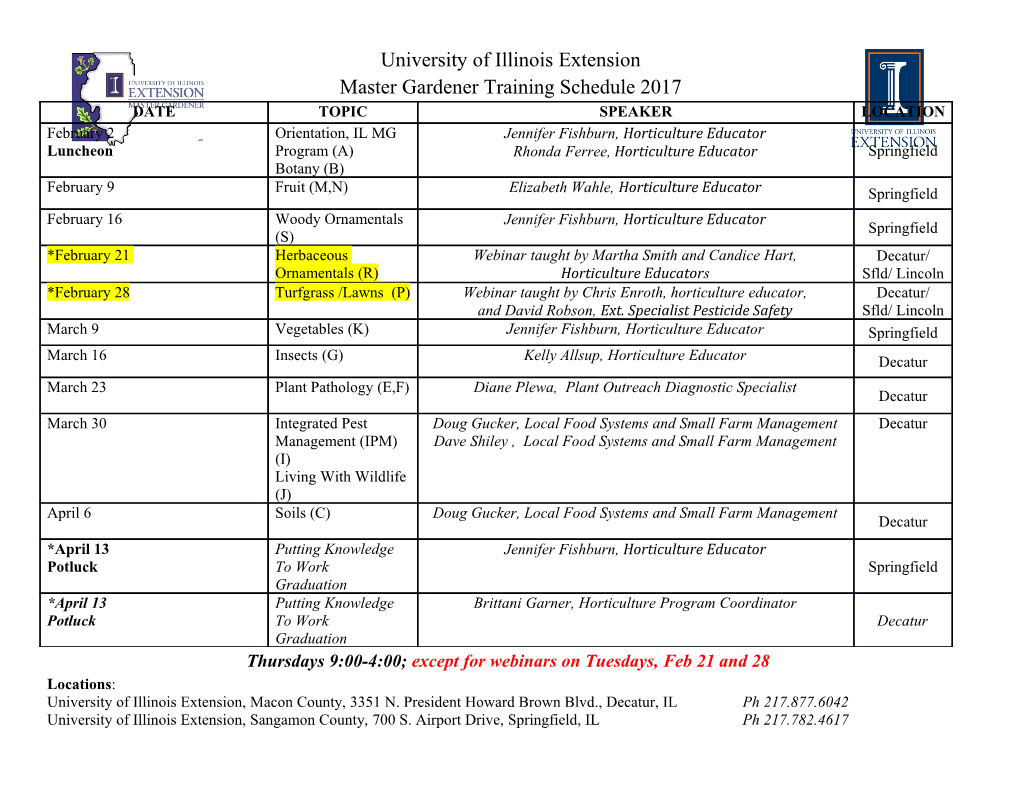
University of Wollongong Research Online Faculty of Engineering and Information Faculty of Engineering and Information Sciences - Papers: Part A Sciences 1-1-2016 Reduction of quartz to silicon monoxide by methane-hydrogen mixtures Xiang Li University of Wollongong, [email protected] Guangqing Zhang University of Wollongong, [email protected] Ragnar Tronstad Elkem AS, [email protected] Oleg Ostrovski University of New South Wales, [email protected] Follow this and additional works at: https://ro.uow.edu.au/eispapers Part of the Engineering Commons, and the Science and Technology Studies Commons Recommended Citation Li, Xiang; Zhang, Guangqing; Tronstad, Ragnar; and Ostrovski, Oleg, "Reduction of quartz to silicon monoxide by methane-hydrogen mixtures" (2016). Faculty of Engineering and Information Sciences - Papers: Part A. 5882. https://ro.uow.edu.au/eispapers/5882 Research Online is the open access institutional repository for the University of Wollongong. For further information contact the UOW Library: [email protected] Reduction of quartz to silicon monoxide by methane-hydrogen mixtures Abstract The reduction of quartz was studied isothermally in a fluidized bed reactor using continuously flowing methane-hydrogen gas mixture in the temperature range from 1623 K to 1773 K (1350 °C to 1500 °C). The CO content in the off-gas was measured online using an infrared gas analyzer. The main phases of the reduced samples identified yb XRD analysis were quartz and cristobalite. Significant weight loss in the reduction process indicated that the reduction products were SiO and CO. Reduction of SiO2 to SiO by methane starts with adsorption and dissociation of CH4 on the silica surface. The high carbon activity in the CH4-H2 gas mixture provided a strongly reducing condition. At 1623 K (1350 °C), the reduction was very slow. The rate and extent of reduction increased with the increasing temperature to 1723 K (1450 °C). A further increase in temperature to 1773 K (1500 °C) resulted in a decrease in the rate and extent of reduction. An increase in the gas flow ater from 0.4 to 0.8 NL/min and an increase in the methane content in the CH4-H2 gas mixture from 0 to 5 vol pct facilitated the reduction. Methane content in the gas mixture should be maintained at less than 5 vol pct in order to suppress methane cracking. Keywords mixtures, quartz, monoxide, reduction, methane, hydrogen, silicon Disciplines Engineering | Science and Technology Studies Publication Details Li, X., Zhang, G., Tronstad, R. & Ostrovski, O. (2016). Reduction of quartz to silicon monoxide by methane- hydrogen mixtures. Metallurgical and Materials Transactions B: Process Metallurgy and Materials Processing Science, 478 2197-2204. This journal article is available at Research Online: https://ro.uow.edu.au/eispapers/5882 1 Reduction of Quartz to Silicon Monoxide by Methane–hydrogen Mixtures 2 Xiang Li1*, Guangqing Zhang1, Ragnar Tronstad2, Oleg Ostrovski3 3 1School of Mechanical, Materials and Mechatronic Engineering, University of Wollongong, 4 Wollongong, NSW 2522, Australia 5 2Elkem AS, Drammensveien 169, Skøyen, P.O Box 334, 0213 Oslo, Norway 6 3School of Materials Science and Engineering, University of New South Wales, Sydney, 7 NSW 2052, Australia 8 9 Abstract 10 The reduction of quartz was studied isothermally in a fluidized bed reactor with continuously 11 flowing methane–hydrogen gas mixture in the temperature range of 1623 K (1350 °C) to 12 1773 K (1500 °C). The CO content in the off-gas was measured online using an infrared gas 13 analyzer. The main phases of the reduced samples identified by XRD analysis were quartz 14 and cristobalite. Significant weight loss in the reduction process indicated that the reduction 15 products were SiO and CO. Reduction of SiO2 to SiO by methane starts with adsorption and 16 dissociation of CH4 on the silica surface. The high carbon activity in the CH4–H2 gas mixture 17 provided a strongly reducing condition. At 1623 K (1350 °C), the reduction was very slow. 18 The rate and extent of reduction increased with increasing temperature to 1723 K (1450 °C). 19 A further increase in temperature to 1773 K (1500 °C) resulted in a decrease in the rate and * Author to whom correspondence should be addressed. e-mail: [email protected]; Tel.: +61 02 4211 5293; fax: +61 02 4221 3112. 1 1 extent of reduction. An increase in the gas flow rate from 0.4 to 0.8 NL/min and increase in 2 the methane content in the CH4–H2 gas mixture from 0 to 5 vol pct favored the reduction. 3 Methane content in the gas mixture should be maintained below 5 vol pct in order to suppress 4 methane cracking. 5 I. Introduction 6 Metallurgical silicon and ferrosilicon alloys are produced in submerged electric arc furnaces 7 by carbothermal reduction of silicon bearing oxides (typically quartz) with carbonaceous 8 materials. Coal, coke, charcoal and woodchips are commonly used as reductants in these 9 processes [1]. Carbothermal reduction requires high temperatures and is energy intensive. 10 The contents of trace elements in both quartz and reductants determine the purity of the 11 produced silicon [2]. SiC is also produced by the carbothermal reduction of quartz. 12 13 Silicon monoxide (SiO) vapor is one of the major intermediate species in the production of 14 SiC and metallurgical silicon [3, 4]. SiO2 is reduced by carbon to SiO by the following 15 reaction: 16 17 SiO2 + C = SiO (g) + CO (g) [1] 18 19 SiO further reacts with carbon to form SiC: 20 21 SiO (g) + 2C = SiC + CO (g) [2] 2 1 2 The primary reaction for production of Si is the following: 3 4 SiC + SiO (g) = 2Si (l) + CO (g) [3] 5 6 Methane has the advantage of high purity over conventional carbonaceous reductants such as 7 coal or coke which always contain impurities [5–7]. The gas-phase reaction between SiO and 8 methane with or without a catalyst has been used for synthesis of SiC whiskers [8–12]. 9 However, no reports were found in the literature on the direct reduction of SiO2 to SiO by the 10 methane–containing gas. The purpose of the present study is to investigate the possibility of 11 reduction of quartz to SiO via the gas–solid reaction by methane–hydrogen gas mixture, as 12 described by Reaction [4]. Natural gas contains low harmful impurities of solar silicon, and 13 provides high carbon activity for the reduction of quartz, which makes it an attractive 14 reductant over conventional solid carbon. 15 16 SiO2 + CH4 (g) = SiO (g) + CO (g) + 2H2 (g) [4] 17 18 Above 1729 K (1456 °C), Reaction [4] has a negative Gibbs free energy change under 19 standard conditions (∆Go); at 1873 K (1600 °C), ∆Go = -63.2 kJ (calculated using HSC 20 Chemistry 6.1). However, methane is unstable at temperatures above 823 K (550 °C); it 21 cracks with deposition of solid carbon (Reaction [5]) at temperatures above 1273 K (1000 °C) 22 [13]. Solid carbon deposits on the sample surface, hindering further progress of the reduction 3 1 by blocking the quartz particle surface. 2 3 CH4 (g) = C + 2 H2 (g) [5] 4 5 Therefore, reduction of metal oxides by the methane-containing gas should be conducted 6 under conditions at which cracking of methane is limited. 7 8 This study examines the effects of temperature, gas composition and gas flow rate on the 9 reduction of quartz in the fluidized bed reactor by the CH4–H2 gas mixture with a low CH4/H2 10 ratio to suppress methane cracking. Reduction of quartz to SiO can be of commercial interest; 11 however, scaling up and further study of this process are needed to find feasibility of the 12 industrial reduction of quartz by the methane-containing gas. 13 II. Experimental 14 A fluidized bed reactor was adopted to mitigate the effect of carbon deposition on the surface 15 of quartz particles. Quartz powder with a particle size of 100–140 μm was obtained by 16 crushing and grinding quartz lumps (supplied by Elkem AS, Norway) by an agate mill and 17 sieving to the size range. The impurity contents in quartz lumps were provided by the supplier, 18 as shown in Table I. The gases (CH4, Ar and H2) used in the investigation were of 99.999 pct 19 purity, supplied by Coregas Pty Ltd, Australia. 20 21 (Table I) 4 1 The fluidization of quartz particles was first verified using a cold model of the fluidization 2 reactor made of Perspex material. It consisted of two zones, a fluidization zone (inner 3 diameter 20 mm) in which a fluidized bed was formed, and a settling zone (inner diameter 40 4 mm). The settling zone had an enlarged intersection and therefore a lower gas flow rate, 5 which allowed the quartz particles brought into the settling zone by ascending gas stream to 6 settle and return to the fluidized bed. A connector with a filter was installed at the bottom of 7 the fluidized bed which played a role of a gas distributor. Fluidisation of quartz powder with 8 particle size in the ranges of 53–100 μm, 100–140 μm and 140–200 μm in the cold model 9 was examined using nitrogen with different flow rates. The change of quartz bed was 10 recorded by a video camera (D5100, Nikon Corporation, Tokyo, Japan). 11 12 The schematic of the fluidized bed high-temperature reactor for the reduction experiments is 13 presented in Figure 1. The reactor was made from graphite; it was installed within an alumina 14 tube of 50 mm ID.
Details
-
File Typepdf
-
Upload Time-
-
Content LanguagesEnglish
-
Upload UserAnonymous/Not logged-in
-
File Pages35 Page
-
File Size-