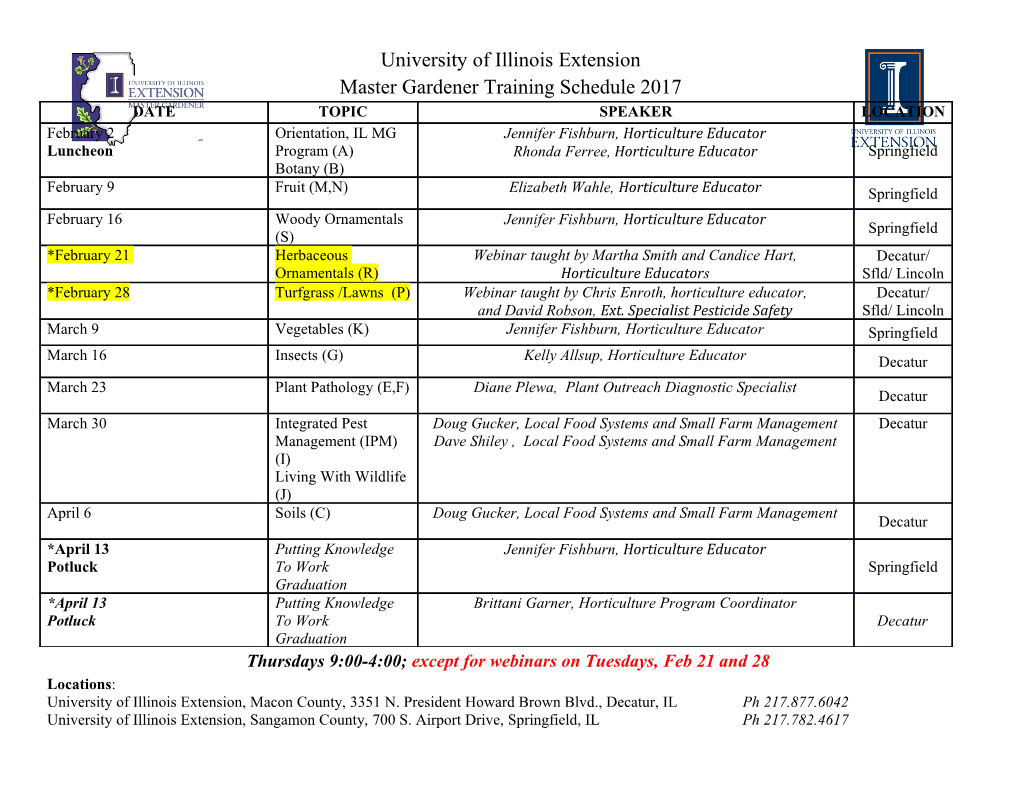
SURFACE MODIFICATION AND MODULATION IN MICROSTRUCTURES: CONTROLLING PROTEIN ADSORPTION, MONOLAYER DESORPTION, AND MICRO-SELF-ASSEMBLY Karl F. Böhringer University of Washington, Department of Electrical Engineering Seattle, WA 98198-2500, USA E-mail: [email protected] Abstract II. CILIARY MICROSYSTEMS The surface-to-volume ratio increases with decreasing During the past decade, several research groups have stud- scale, thus, controlling and changing the surface properties ied arrayed microactuators [2-22], obtaining their inspiration of microstructures can be a powerful tool in the design, fab- from biological cilia and distributed robotic conveyor sys- rication, and use of microsystems. This paper overviews tems. While these systems differ somewhat from the central several recent projects that utilize the modulation of sur- theme of this paper (MEMS cilia are discrete mechanical de- faces from hydrophobic to hydrophilic and vice versa, or vices, while here we want to focus on continuous properties from protein adsorbing to non-fouling, with applications in of surfaces), there are still good reasons to review this earlier biomedical microdevices and self-assembling microelectro- work: First, these systems represent a different kind of “smart mechanical systems (MEMS). surface” able to interact with objects in contact in a con- trolled, programmable fashion. Second, cilia arrays have Key Words: surface modification, self-assembled mono- given raise to a general theory of massively parallel, distrib- layer, hydrophobic, hydrophilic, protein adsorption, bio- uted manipulation [18], which is directly applicable to self- fouling, self-assembly, MEMS. assembling systems. Here, we briefly review some of our work on microactuator arrays and summarize important theo- I. INTRODUCTION retical results on micromanipulation and microassembly. Careful design and control of surface properties can be of Actuator arrays built in single crystal silicon were intro- great benefit in engineered microsystems. The laws of scal- duced in the early 1990’s [7, 11]. Several thousand actuators ing entail that with decreasing size, effects tied to surface were integrated in a dense layout on a single chip (Figure 1). area (e.g., capillarity, electrostatic charge, adsorption of mo- These arrays were able to move small chiplets placed on top lecular layers) increasingly dominate effects tied to volume of them; however, the small range of motion (approximately (e.g., gravity, inertia). This is the well-known cube-square- 5µm) and limited force of each individual actuator rendered law, which relates the cubic scaling of volume to the quad- them less effective for general micromanipulation tasks. ratic scaling of surfaces; one of its consequences is the nec- essary existence of a “crossover point” where the surface (b) effect starts to overtake the volume effect. This crossover point is typically seen at scales of just below 1mm [1]. Thus, a systematic study of surface properties at the mi- croscale, combined with methods for controlling and modi- fying them, has been the topic of extensive recent research. In this paper, we investigate this field in greater detail, spanning a range of research activities from microelectro- mechanical “smart surfaces,” to micropatterned “program- mable chemistry” that controls wettability and bio-fouling, (a) to self-assembling microsystems. The remainder of this paper is organized as follows: Sec- Figure 1: (a) Array of single crystal silicon micro- tion II begins with earlier work on “smart surfaces” com- actuators. Individual actuator size is 240µm 180µm. (b) prising arrays of microactuators, which are employed for × Actuator detail with suspended silicon structures (spacing micropositioning tasks. Section III investigates assembly at between posts: 20µm). Figures from [11]. the microscale, describing massively parallel approaches for self-assembly based on capillary forces. In Section IV, we discuss surface modifications to control hydrophobicity and Suh et al. [15, 19] built several kinds of thermal bimorph protein adsorption, which has various applications in mi- polyimide microcilia, which were successfully used to posi- croassembly and biomedical microdevices. We conclude tion and orient millimeter-sized objects (Figure 2) under opti- this paper with a summary and an outlook on open problems cal and scanning electron microscopes [18, 23]. Employed and future work. upside-down, these cilia arrays also enabled the first “walk- ing” microrobot with full 3 degrees of freedom [24]. rium. These equilibria are the final rest positions for an object that is placed at an arbitrary initial position. We can thus think of microactuator arrays as “programma- ble force fields” (PFF’s). It has been shown that PFF’s can efficiently perform a broad range of micromanipulation tasks such as positioning, orienting, and sorting [18, 25]. In addi- tion, these general results on PFF’s are very useful to devise strategies for massively parallel microassembly. The next (a) section will investigate microassembly in greater detail. III. MICRO-SELF-ASSEMBLY Recent developments in the area of microfabrication tech- niques offer the opportunity to create a large variety of func- tional microdevices (e.g., chemical, electrical, mechanical, (b) and optical transducers). Practical applications require inte- gration of such devices into compact and robust microsys- Figure 2: (a) “Motion pixel” made of 4 polyimide mi- tems. Monolithic integration often faces problems of material crocilia (total size 1.1mm × 1.1mm). (b) Cilia array and process incompatibilities of different functionalities. Ide- transporting an ADXL50 chip (size about 3mm × 3mm). ally, one would like to build each functional subsystem with Figures from [15] by J. Suh. optimized materials and processes, and then assemble them into a complex microsystem. Researchers have been investi- gating the adoption of macroscale “pick and place” methods to assemble micro- or even nanoscale components [27-29]. One major concern in these approaches is the “sticking ef- fect” between assembly manipulators and components, due to electrostatic, van der Waals, or surface tension forces [1]. On the other hand, new assembly approaches have emerged by taking advantage of this sticking effect: Whitesides and co- workers first demonstrated capillary-force-driven assembly of asimplecircuit[30];Srinivasanet al. extended the capillary- force-driven strategy to assemble identical microscopic parts onto a single substrate [31]. In this section, we describe a novel approach based on capillary action to achieve multiple Resultant forces batch assembly and bonding of microcomponents onto a sub- strate. In addition, electroplating as a post assembly process is Figure 3: Concept of a programmable force field (PFF) used to establish electrical connections for assembled compo- for positioning of microparts. The force acting on the part nents in a parallel manner [32-35]. is obtained by integrating the PFF over its surface area. A microactuator array could be used to generate this PFF. III.1 SELF-ASSEMBLY PRINCIPLES In our assembly method, capillary force is exploited to drive the assembly, and the force is created by a hydrocarbon- Coordinating hundreds or thousands of individual cilia to based lubricant between hydrophobic surfaces as in [30, 31]. achieve a micropositioning task has been the topic of exten- A schematic illustration of our assembly process is shown in sive research in robotics [18, 25, 26], which is beyond the Figure 4. We fabricate a silicon substrate with gold patterns scope of this paper. Here, we simply present some key find- as destined binding sites for assembly of parts (Figure 4a). To ings that will be useful in our further discussion. activate the binding sites on the substrate, a hydrophobic al- Modeling of microactuator arrays is conveniently accom- kanethiol (CH (CH ) SH) selfassembled monolayer (SAM) is plished with force vector fields, which assign a lateral force 3 2 n adsorbed on hydrophilic gold patterns. For each batch of mi- to each point in the plane. For example, Figure 3 shows such croparts, only desired binding sites on the substrate are acti- a force vector field and its effect on two objects that are vated by selectively de-activating other binding sites. In the placed on top of it. de-activation process, electrochemical reductive desorption of Even simple fields consisting only of two separate regions the SAM, i.e.,CH(CH ) SAu+ e– → Au + CH (CH ) S– [36, with constant force vectors are sufficient to position an ob- 3 2 n 3 2 n 37] is performed (Figure 4b). Thus we can control the assem- ject without any sensor feedback. Figure 3 shows the under- bly not to occur in the gold regions where the SAM desorp- lying principle: The lateral force on an object in contact in- tion has taken place. To create the driving force, we apply a tegrates over its contact area. The resultant force for the left lubricant to the substrate prior to assembly. Next, the sub- part is a larger force pointing towards the right. The resul- strate is immersed in water and the lubricant forms droplets tant force for the right part, however, is a smaller force to- exclusively on the activated binding sites. After the parts are wards the left, since its contact area encompasses regions of transferred into water, the parts with a hydrophobic side are forces pointing to the left as well as to the right. It is easy to attracted and aligned to the binding sites on the substrate. see that there exist placements
Details
-
File Typepdf
-
Upload Time-
-
Content LanguagesEnglish
-
Upload UserAnonymous/Not logged-in
-
File Pages9 Page
-
File Size-