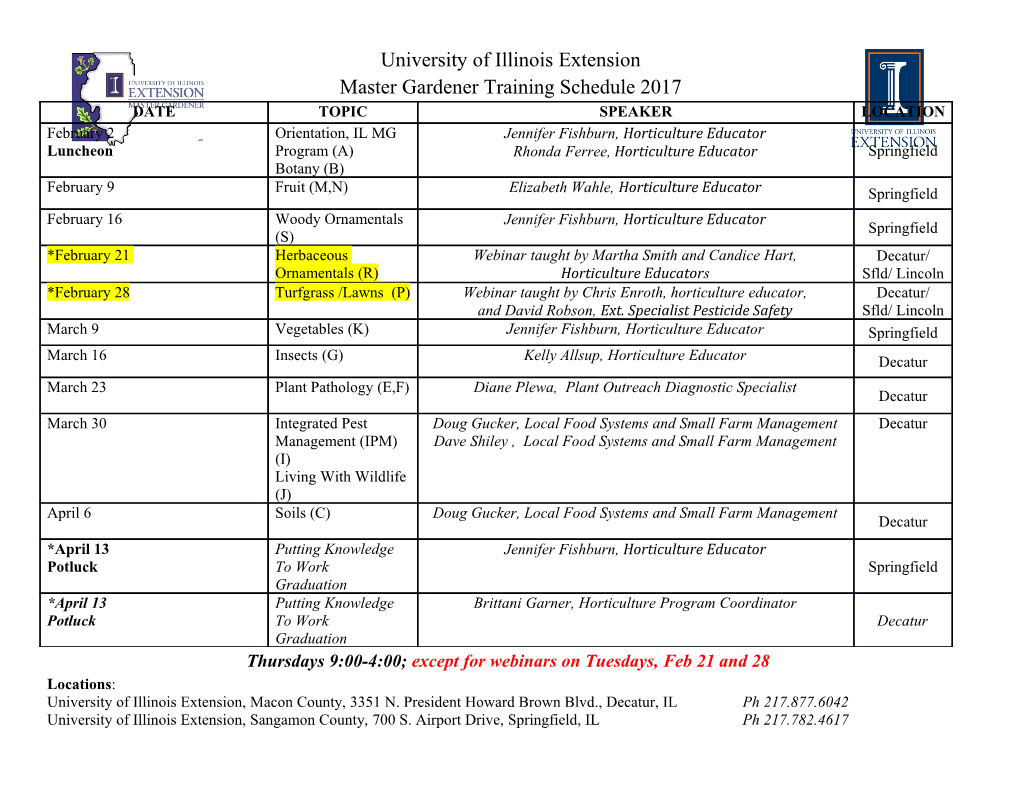
Present Status of Vacuum Metallurgy in the Iron-Steel Industry of Japan* Report of Vacuum Metallurgy S ubdivision, Nell' Technique Development Division, Joint Research Society By M llS ayoshi Hasega IV a**, Toshihiko Asakuma*** all d Tetsuya Watallabe*** * 1. Introduction arc melting of titanium, and since around 1957, steel The Vacuum Metallurgy Subdivision, establish­ m elting by vacuum arc melting furnace has been draw­ ed in 1958 within the Steel T echnology J oint R esearch ing the attention of industry. At present, 12 furnaces Society in order to promote the exchange of technical of 10 companies are in operation, including a 20-i nch informa tion among the mills concerned, a nd to push diameter furnace Cor 4-ton ingots imported from NRC rapid progress of domestic technique and improvement Equipment Corporation and a 640-mm diameter fur­ oCfacilities, has been m a king efforts to improve vacuum nace for 6.8-ton ingots. Although the latter is the larg­ metallurgy through a nnouncing the results oC technical e t at p resent, severa l larger furnaces- of 30-inch dia­ research, holding discussions, and publishing research meter-for melting ingots of over 10 tons will make reports. The history a nd the present status of vacuum their debut w ithin this year. metallurgy in J apan is outli ned hereunder. The vacuum induction melting process was initiated Vacuum techniques a lready employed on a commer­ by Tohoku Metal Industries, Ltd., which imported a cia l basis include vacuum degassing, vacuum arc melt­ 50-kg furnace from N R C Corporation in 1954 to ing a nd vacuum induction melting. Vacuum heat start commercial manufacturing of m etallic materials for electronic instruments. In the same year, Sa n yo trea tment is as yet not widely used industrially, while skull m elting and electron bombardment melting are Special Steel Co., Ltd. commenced manufacturing sti ll in an experimental stage, req uil-ing m ore time be­ bearing steel with a 100-kg induction furnace imported Core they are put into industrial use. As in other from N R C. Thereafter, other companies became countries, the id ea of vacu um degassing in J apan dates more and more interested in this field. T he furnace back many years. In 1905, the low-press urc casting capacity g radua ll y increased as Tohoku Metal import- m ethod was patented, and in 1925, engineers of T he 20.--,---.--,---.--,,-- ,-- -,--,--, Institute of Phys ical a nd Chemical R esearch conceived the id ea of using vacuum to eliminate blow-holes in 15 ,-,- castings, a nd thereafter, such methods as th e con­ c " tinuous degassing casting process and the degassing '0 10 casting process were worked out. These methods wel-e .; z fundamentally no different from the present industrial methods. Nevertheless, they could not be put on a commercial scale because they were not accompanied 1954 1955 1956 1957 1958 1959 1960 196 1 1962 1963 by the necessary vacuum technique, or because of Year economic reasons. Fig. 1. Status of vacuum m elting in Japan . (Figures for H owever, stimula ted with the success by Bochumer vacuum degassing denote number of companies Verein A . G. oC \Vest Germany, the industri a li zation applying the degassing process.) of vacuum degassing in Japan mad e ra pid p rogress led Comprc s~ cd air by K a nto Specia l Steel \Norks, Ltd. which established ----~ - a ten-ton ingot unit in 1957. The appearance of large I 3 I m echanical booster pumps (20,000 m /h) has contri­ I I I buted to the developm ent of degassing. This vacuum f.-­ I degassing process is now being ad opted in 18 factories I I of 17 companies. Although there a re records of large I r-- I ingot making, such as a 160-ton ingot by a 250-ton uni t, I I I I I I this technique is appli ed mostly for processing com­ I I I I paratively sma ll amounts oC molten steel, that is, for I I r I processing small ingots, using many molds. An exam­ I I I I Filter F ilter ple of the arrangement is shown in Fig. I . Ii _____________________ L: _______________________ _ ~I In early 1954, the Furukawa Electric Co., Ltd., Cooling water Sumitomo M etal Industries, Ltd. and K obe Steel ' '''orks, Ltd. succeed ed in consumable electrode vacuum Fig. 2 Arrangement of vacuum degassing unit * M anuscript received on Dec. 29, 1962. J apanese text was p rinted in Tetsu-to-Hagane (Journal, Iron & Steel Institute, J apan), 49, 797- 837. ** Dr. Eng., Chief of the Subdivision, Prof., \'Vaseda U niversity. *** Manager of the Subdivision, K a nto Special Steel Co., Ltd. **** Dr. Eng., Manager of the Subdivision, Nippon Yakin Kogyo Co., Ltd. Report of the Joint Research Society ( 148 ) Te tsu-to-H a gane Ove rseas Vol. 3 No.2 Jun e 1963 ed a 500-kg furnace fr om N R C in 1958 and Shim ura a nd equa ll y interes ting is the m ethod of m a nufacturing K ako Co., L td . bought a one-ton furnace from F . J. rimmed steel by casting in a ir in to m olds within the Stokes Corpora tion in 1960. A t p resen t, 18 furnaces vacuum chamber and evacua ting. are being commercia lly opera ted, including the one­ For the vacuum pump, steam ~ j ectOl-s a re used by ton furnace, 350 kW, m anufactured by Stokes, a nd the only three companies, w hile mechanical booster pumps one-ton furnace, 660 kVV , manufactured by J apa n are widely utilized . The vacuum tanks a re water­ Vacuum E ngineering Co., Ltd. I n spi te of the fact cooled, a nd the dust catchers consist of bag filters, oil tha t J apan tod ay has no military ind ustries a nd very sepa ra to rs a nd cyclones. The pouring ra te of molten few a ircra ft a nd nuclear energy a pp li cations, h er pro­ steel is a round 2 t/min, a nd the degree of vacuum is g ress in the fi eld of vacuum meta llu rgy is very rem ark­ a pproximately 1- 5 mmHg, while it is below 1 mmHg able. J apan's vacuum m eta llu rgy, as shown in Fig. I , with steam ej ectors. Although the steel pouring ra te m ad e rapid strides in the period 1959- 1960. is 2- 2.5 t/min and the tem perature d rop 50°-80°C in stream ladle degassi ng, it p roduces the sam e effect as vacuum ingot casting. The capacity per charge of II. Vacuum Degassing the D-H unit a t Yawata is as much as 70 tons. The ci rcula tion d egassing process (H eraeus-Ruhr­ This m ethod is app lied for manufac turing rimmed sta ll process) is expected to be in troduced into J apan steel, carbon steel, low a ll oy steel and stainless steel. shortl y. With the exception of Yawata I ron & Steel Also m a nufactured a re tu rbine sha ft s, power genera tor Co., L td ., which adopted the D-H process, the m ethod shafts, sili con steel electrical sheets, thick plates, deep m ost popula rl y used is vacuum stream degassing. The drawing steel plates, boil er pl a tes, forged steel roll s, J a pa n Steel Works, Ltd., K obe Steel W orks, L td. a nd cast steel roll s, die blocks, castings a nd structural steels. Mitsubishi Steel M a nufac turing Co., Ltd. exclusively The foll owing is a summa ry of quality impz-ove ments use the a foresaid m ethod of The Institute of Phys ical brough t a bout by vacuum d egassing, as compiled from a nd C hemical R esearch applying it to ingot maki ng the many research repor ts avail abl e on the vacuum a nd casting or developing it to m eet their specifi c needs, degassing process with regard to its equipment, opera­ except for the Bochumer process induced fro m Bochum­ tion m ethod, basic stud y a nd appli cati on . er V erein A. G. a nd Leybold H och-Vakuum-Anlagen ( I) M a nufac turers of steel for fOl-gings report GmbH. spectacular success by a pplying the vacuum d egassing V a rious improvem en ts have been made on m a nu­ process to r em ove h ydrogen in order to preven t fl aking. facturing m ethods a nd equipment as a result of which Generall y speaking, a bou t 60 per cen t of the h yd rogen is m a ny pa tents were ta ken out, such as those on the con­ eli m in ated, a nd the rem a inder is di stributed uniforma ll y tro l of degree of spraying of steel insid e vacuum ta nks, in the ingot. T a bl e I shows the amount of h ydrogen pon y ladle tightness, equipment for m a king plura l in­ removed by vacuum degassing in the various com­ gots, ind uction stirring of ladle degassing, the vacu um pani es. T he opera ting capacity a nd the h yd mgen casting pmcess for castings a nd the d uplex process to valu e are obviously related to each other where vacuum h eat and to secondarily d egass by vacuum induction ingot casting is a pplied .
Details
-
File Typepdf
-
Upload Time-
-
Content LanguagesEnglish
-
Upload UserAnonymous/Not logged-in
-
File Pages12 Page
-
File Size-