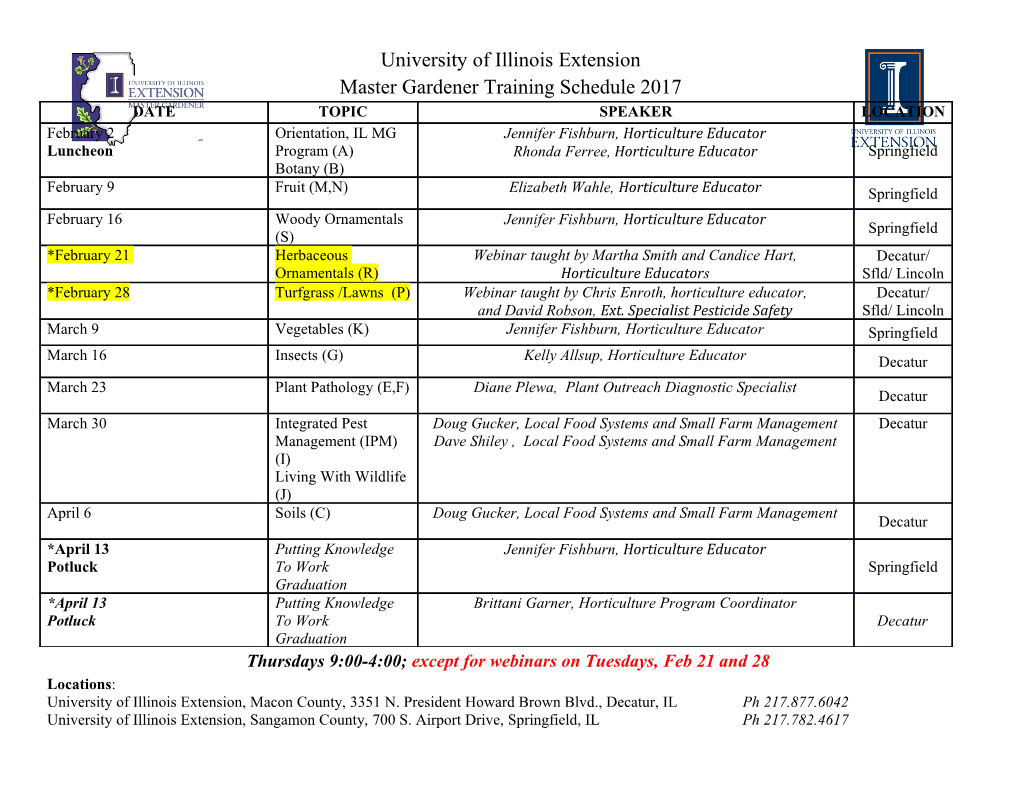
ChemComm Accepted Manuscript This is an Accepted Manuscript, which has been through the Royal Society of Chemistry peer review process and has been accepted for publication. Accepted Manuscripts are published online shortly after acceptance, before technical editing, formatting and proof reading. Using this free service, authors can make their results available to the community, in citable form, before we publish the edited article. We will replace this Accepted Manuscript with the edited and formatted Advance Article as soon as it is available. You can find more information about Accepted Manuscripts in the Information for Authors. Please note that technical editing may introduce minor changes to the text and/or graphics, which may alter content. The journal’s standard Terms & Conditions and the Ethical guidelines still apply. In no event shall the Royal Society of Chemistry be held responsible for any errors or omissions in this Accepted Manuscript or any consequences arising from the use of any information it contains. www.rsc.org/chemcomm Page 1 of 4 Please doChemComm not adjust margins Journal Name COMMUNICATION Core‐shell nanoparticles by silica coating of metal oxides in a dual‐ stage hydrothermal flow reactor a a a a Received 00th January 20xx, H. L. Hellstern , A. Mamakhel , M. Bremholm , B. B. Iversen Accepted 00th January 20xx DOI: 10.1039/x0xx00000x www.rsc.org/ γ‐Fe2O3@SiO2, TiO2@SiO2, and α‐Fe2O3@SiO2 core‐shell syntheses the shell material may nucleate at a higher temperature nanoparticles were synthesized by a surfactant‐free hydrothermal than the core which makes a one‐pot synthesis possible, but this method in a continuous flow dual‐stage reactor. Uniform silica severely restraints the nanocomposites available for synthesis and shells of 2 nm thickness were obtained when grown on γ‐Fe2O3 and doping effects have to be considered. TiO2 nanoparticles while thicker and more irregular shells were Manuscript deposited on α‐Fe2O3 due to low pH. Here we report surfactant‐free syntheses of γ‐Fe2O3@SiO2, TiO2@SiO2 and α‐Fe2O3@SiO2 core‐shell nanoparticles in a dual‐ Core‐shell nanoparticles are an important class of materials. A stage hydrothermal flow reactor, which separates the synthesis of secondary material can be deposited on the core for multiple core and shell into separate regions but maintains continuous purposes incl. functionalization, protection from oxidation or production.21 Hydrothermal flow synthesis of the core material in the 1, 2 agglomeration and improvement of catalytic performance. Silica is primary reactor stage produces nanoparticles of a narrow size a frequently used shell material for coating of core nanoparticles distribution.22 Deposition of the shell material in the secondary 3‐6 7, 8 9, 10 11‐14 15, 16 including TiO2, Au, Fe2O3, Fe3O4, ZnO, and it can be reactor allows for thin nanoshells due to the short residence time. 17 used to improve dispersibility of the core nanoparticle. SiO2 can be Shell thicknesses for γ‐Fe2O3@SiO2 and TiO2@SiO2nanocomposites synthesized from tetraethyl orthosilicate (TEOS) through hydrolysis Accepted were approximately 2 nm, while the α‐Fe2O3@SiO2 shell thickness 18 and condensation in a typical sol‐gel process. Typical shell was up to 5 nm and more irregular. The formation of thin, complete thicknesses are in the range of 20‐100 nm, but silica shell thickness shells or thick, incomplete shells is linked to the final pH and the 6 as low as 4 nm has been demonstrated. Functionalization of the isoelectric point of the core nanoparticles synthesized in the primary silica surface with organic molecules allows the coated nanoparticle reactor. to be used as a biosensor or in medicine.19 All syntheses were performed in a hydrothermal continuous flow Hydrothermal flow reactors are powerful tools for continuous dual‐stage reactor. The details of the dual‐stage flow reactor has 20 synthesis of nanoparticles with narrow size distributions. However, been described elsewhere,21 and an outline of the setup is illustrated traditional single‐stage flow reactors are typically not suited for in Supporting Information (Figure S1). 0.1 M ammonium iron(III) synthesis of hybrid nanoparticles as nucleation and growth of the citrate (AIC) (Reactant #1) was pumped at 5 mL/min and mixed with core and the shell occur simultaneously under identical reaction degassed demineralized water at 15 mL/min heated to 350 °C in a conditions which can lead to solid solutions or simple mixtures of ChemComm tee mixer and led into the primary reactor for γ‐Fe2O3 formation. The single‐phase nanoparticles. nanoparticle suspension was cooled down and then mixed with 0.2 M TEOS (Reactant #2) in isopropanol pumped at 5 mL/min, and the In batch experiments synthesis of core‐shell nanoparticles is usually mixture was heated in the secondary reactor (100°C). The composite a two‐step process in which the primary core particle is synthesized product was cooled down and collected from a proportional relief prior to the secondary material used for the shell. For some valve. Anatase TiO2 nanoparticles were synthesized in the primary reactor at 350°C from 0.05 M titanium tetraisopropoxide (TTIP, 97%) a. Center for Materials Crystallography, Department of Chemistry and iNANO, in isopropanol mixed with heated solvent. Solvent was a 1 mM Aarhus University, Langelandsgade 140, 8000, Aarhus C, Denmark. Corresponding solution of acetic acid to adjust the pH to approximately 4. The TTIP author: [email protected] Electronic Supplementary Information (ESI) available: [details of any supplementary precursor was pumped into the system at 5 mL/min, and the solvent information available should be included here]. See DOI: 10.1039/x0xx00000x was pumped at 12 mL/min. The cold suspension was mixed with 0.2 This journal is © The Royal Society of Chemistry 20xx J. Name., 2013, 00, 1‐3 | 1 Please do not adjust margins Please doChemComm not adjust margins Page 2 of 4 COMMUNICATION Journal Name M TEOS in isopropanol pumped at 5 mL/min, and the mixture was characterized with Fourier Transform Infrared (FTIR) spectroscopy heated in the secondary reactor (100°C). The volume of each reactor (Thermo Electron Corporation Nicolet Avatar 380). section is approximately 20 mL, and residence times were roughly 60 seconds for each reactor stage. For α‐Fe2O3@SiO2 the iron precursor Figure 1A shows the powder diffraction patterns for the synthesis was 0.1 M Fe(NO3)3(aq). Single‐phase α‐Fe2O3 nanoparticles were using the AIC precursor and all reflections can be assigned to γ‐Fe2O3 synthesized in a separate experiment using only the primary reactor (maghemite). The average crystal sizes were refined to 18.8 and 18.6 stage at 250°C, 300°C, 350°C and 400°C. All of the above mentioned nm for the uncoated and coated sample, respectively as calculated chemicals were purchased from Sigma‐Aldrich. from the peak broadening. Powder X‐ray Diffraction (PXRD) data was collected in Bragg‐ The crystal sizes are in good agreement with results obtained by in‐ 24 Brentano geometry (Rigaku SmartLab, Cu Kα1) and Rietveld situ PXRD studies. From XRF the Si/Fe molar ratio is 0.1, and pH of refinements were performed using the FullProf23 software. the suspension was approximately 6. STEM (Figure 2) shows γ‐ Structural models from the ICSD database (γ‐Fe2O3 ICSD 247036, TiO2 Fe2O3@SiO2 as a core‐shell structure. The diffraction patterns of anatase ICSD‐92363 and α‐Fe2O3 ICSD‐5840) were used for the initial maghemite (γ‐Fe2O3) and magnetite (Fe3O4) are very similar but the 25 models. Data was refined on a linearly interpolated background. AIC precursor has been shown to produce mainly maghemite. From Instrumental broadening was accounted for by using a LaB6 standard. the EDX images in Figure 2 the maghemite particle size is estimated Peak profile was the Thompson‐Cox‐Hastings function. All diffraction to be approximately 4 nm smaller than the silica shell, and thus the patterns were refined by the Rietveld method and parameters are silica layer thickness is ~2 nm (see Figure S20). Additional TEM and summarized in Supporting Information, Table S1. HR‐TEM are included in Supporting Information Figure S4‐S28. Manuscript Accepted Figure 1: PXRD data for A) γ‐Fe2O3@SiO2 and γ‐Fe2O3. B) TiO2@SiO2 and TiO . C) α‐Fe O @SiO and α‐Fe O . Bragg reflections (green tick 2 2 3 2 2 3 marks) and model intensities from Rietveld refinements (solid back lines) are included for each pattern. Blue lines (top) are Figure 2: A) TEM image of γ‐Fe2O3@SiO2 nanocomposites. B) HAADF nanocomposites while red lines (bottom) are the phase pure metal view of selected particles. C‐E) Elemental maps of Fe (D), Si (E) and a oxide. A broad feature from amorphous silica can be seen at around superposition of B, D and E (C). Unreacted TEOS precursor can be 25°. seen by a high Si background in C and E. ChemComm Samples were investigated with Scanning Transmission Electron The crystal size of anatase is also unaffected by the deposition of the Microscopy (STEM) (FEI Talos F220A, operated at 200 kV) including secondary material as was the case for γ‐Fe2O3. Rietveld refinements Transmission Electron Microscopy (TEM), High Angle Annular Dark show that TiO2 forms phase pure anatase with an average crystallite Field (HAADF) and Energy Dispersive X‐ray spectroscopy (EDX). size of 6.5 nm and 7.3 nm for the coated and uncoated sample, Elemental composition was investigated with X‐Ray Fluorescence respectively (Figure 1B). This is in agreement with previous results.21 spectroscopy (XRF) (Spectro Xepos‐II) and chemical bonding was The calculated crystal sizes confirm that the silica deposition does not change the observed diffraction pattern except for the addition 2 | J.
Details
-
File Typepdf
-
Upload Time-
-
Content LanguagesEnglish
-
Upload UserAnonymous/Not logged-in
-
File Pages5 Page
-
File Size-