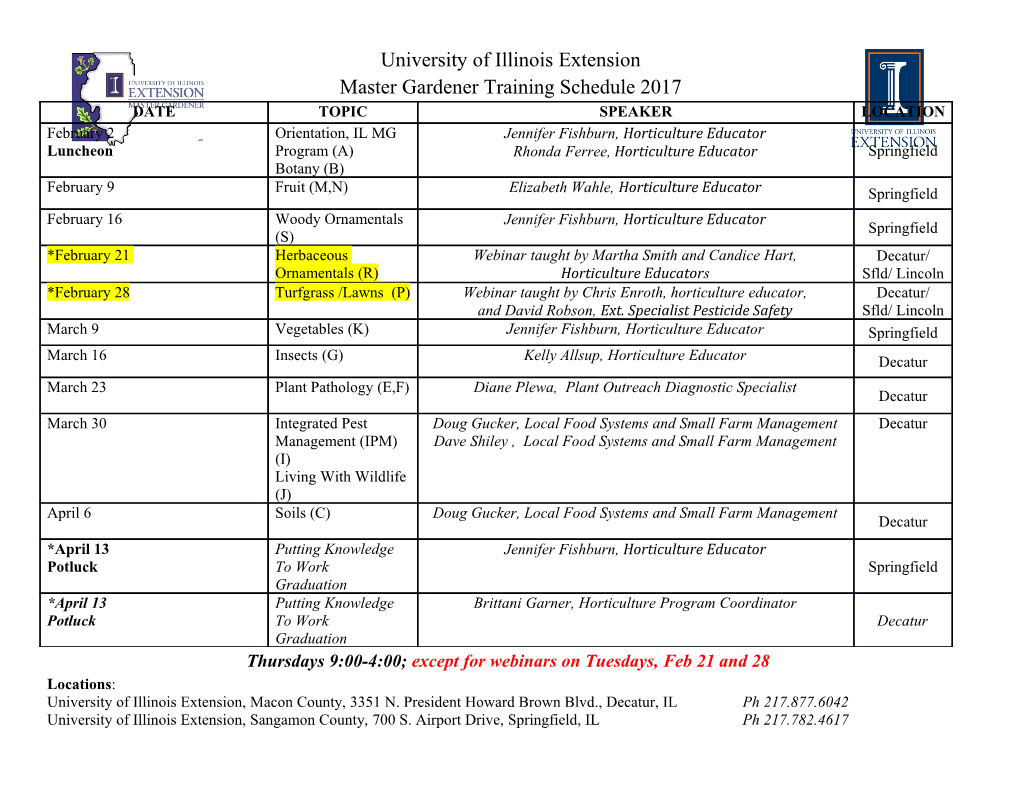
MATCHLESS DOUBLE TREADLE SPINNING WHEEL INSTRUCTIONS, MAINTENANCE & WARRANTY 15 100 100 10 67 49 36 0 42 5 92 4 38 37 94 24 0 76 81 31 90 7 0 36 Find out more at schachtspindle.com Schacht Spindle Company 6101 Ben Place Boulder, CO 80301 p. 303.442.3212 f. 303.447.9273 3 66 100 9 05.11 49 24 0 70 © 20110 Schacht42 59 49 Spindle Company, Inc. Drive Band Tension Knob Rear Maiden Flyer Whorl Flyer Flyer Orifice Bobbin Front Maiden Mother-of-All Scotch Tension Knob T-Knob Front Leg Footman Rear Leg Treadle Adjustable Feet Treadle Support Bar DOUBLE TREADLE WHEEL – 2 – We are pleased that you have chosen one of our Schacht Spinning Wheels. We have taken great care in the design of our wheels to make them efficient and sturdy as well as aesthetically pleasing. Our wheels are constructed using traditional woodworking joinery, following the concept that form follows func- tion. We feel that good design and quality craftsmanship, along with regular maintenance, ensures that your wheel will endure. Each part has been specially designed with function in mind. During manu- facturing, every part is inspected for quality, and the final assembly has been done by a skilled craftsperson. Should you have any questions about the qual- ity of the work or the materials, please do not hesitate to contact your dealer or our customer service department directly. Your Schacht Spinning Wheel is a precision tool, having many moving parts that require regular care and maintenance. The better you understand your wheel, the more able you will be to take advantage of its many features. Please read this booklet before you start spinning on your wheel. UNPACKING YOUR WHEEL Small box: Unpack the accessory boxes and 1– bobbin make sure you have all the parts. 1 – flyer 1 – flyer whorl Large Box: (2nd whorl is attached to the 1 – Lazy Kate back of the rear maiden) 3 – bobbins 2 – cotter pins 3 – Lazy Kate bobbin rods 2 – treadle yoke clevis pins 1 – carrying strap 4 – white nylon washers in small bag: Wood Parts: 1 – threading hook 2 – treadles with treadle yokes 1 – 4mm hex wrench 1 – treadle support bar with 1 – 5mm hex wrench attached hinges and 3 – black retainer rings for bobbin adjuster feet rods 1 – treadle support brace 1 – brake tension spring and cord REQUIRED TOOLS 1 – extra length of drive cord Phillips screwdriver 10 – 1/4" trusshead screws 2 – 1” trusshead screws – 3 – ATTACHING THE TREADLE treadle cross brace SUPPORT BAR support bar Remove the leg bolt, washer and washer small rod from the front leg of the leg bolt wheel. Remove the short rod from barrel the bolt, and insert the leg bolt with nut 4mm hex the washer through the hole in the wrench middle of the treadle support bar. AttACHING TREADLE SUPPORT BAR Replace the short rod on the leg bolt, then insert the leg bolt into the hole front leg in the front leg. Align the short rod with the slot in the front leg. Using short rod treadle the 4mm hex wrench, screw the leg support bar bolt into the barrel nut glued into washer place in the cross brace. treadles leg bolt ATTACHING THE TREADLES REINSTALL THE SHORT ROD Lay the wheel on its back on a table, tilted to either side. Use a towel or treadle hinge left treadle blanket to protect the table and the first screw wheel from scratches. Slide the left (shorter) treadle into place, allowing the treadle to hang off table the edge of the table. Using a Phillips screwdriver, attach the treadle hinge to the treadle using the short screws in the small bag. Insert the screw at the far right and fasten loosely, treadle hangs off edge of table then insert the screw at the far left. ATTACH THE LEFT TREADLE Tighten the screw only until it stops turning. Go back and tighten the right treadle first screw, then insert the remaining three screws. Be sure not to over- first screw tighten the screws. Repeat for the table right treadle. ATTACHING THE TREADLE SUPPORT BRACE Remove the leg bolt. Place the washer and the treadle support brace onto the leg bolt, then insert the leg bolt through the treadle support bar ATTACH THE RIGHT TREADLE – 4 – and short rod and into the front treadle support brace front leg leg. Make sure that the short rod angled edge is aligned in the slot in the front leg treadle treadle and that the support brace angled edge is at the top. Tighten the leg treadle washer bolt only by hand. Use the 1” screws support bar treadle screw support leg bolt to attach the brace to the front of the screw brace treadle support bar (see diagram). Center the treadles between the AttACHING THE TREADLE SUPPORT BRACE back legs of the wheel. If necessary, the treadle support bar can slide a bit to the left or right to center the treadles. Tighten the leg bolt with the 4mm hex wrench. ATTACHING THE FOOTMEN footman footman Attach the footmen to the treadles us- leather wood ing the cotter pins, clevis pins and the treadle yoke cotter pin white nylon washers that are packed clevis pin in the small box with the flyer. The left treadle is attached to the white washer white footman that is closest to the back of washer the wheel. Place the footman leather left treadle inside the treadle yoke and line up right treadle the holes. Put a washer on a clevis AttACHING THE FOOTMEN Backs of treadles, seen from pin and insert the clevis pin from the right side of wheel front of the wheel towards the back. Put another washer on the clevis pin and secure by inserting a cotter pin through the clevis pin until the cotter pin is about halfway through the clevis pin. The right treadle is attached in the same way, but the clevis pin should be inserted through the footman and treadle treadle yoke from the back of the support bar wheel toward the front. lock nut ADJUSTING THE TREADLE HEIGHT foot This adjustment is only necessary if your treadle is either rubbing the drive wheel or hitting the rear leg – 5 – cross support. To adjust the treadle head wrench to adjust the screw in height, remove the cotter pin from the or out as necessary. Fold the front treadle-yoke pin and pull the treadle- maiden up and check the fit. yoke pin out of the treadle yoke. Rotate the yoke clockwise to raise the CHANGING BOBBINS treadle and counterclockwise to lower Loosen the front T-knob on the the treadle. Make only two or three maiden about one turn. Hold the flyer turns and reassemble the footman and with one hand and pivot the front treadle yoke. Repeat this adjustment maiden forward until the flyer orifice until you are satisfied with the posi- is out of the front maiden bearing. tion of the treadle. Hold the drive band up and out of the way as you pull the flyer towards you ADJUSTING THE FRONT LEGS until the flyer shaft is out of the rear The front legs of your spinning wheel maiden bearing. Remove the flyer can be adjusted to accommodate whorl. (Unlike most spinning wheel uneven floors. Simply loosen the lock flyer whorls that screw onto the flyer nut and screw the foot up or down as shaft, our quick-attach whorls need needed, then tighten the lock nut. only to be pushed on and pulled off INSTALLING THE FLYER ASSEMBLY the square part of the flyer shaft.) Remove the bobbin and replace it with Loosen the front maiden T-knob another one. If you are spinning in about one turn. Pivot the front maiden double drive mode, face the small end forward. Insert the flyer-bobbin-whorl of the bobbin toward the flyer whorl; assembly fitting the small end of in Scotch tension mode, the large end the flyer shaft into the rear maiden of the bobbin faces the flyer whorl. bearing. Be sure to lift the drive band up and over the bobbin and whorl pul- DOUBLE DRIVE MODE leys. Pivot the front maiden up and fit We have shipped your wheel set up the flyer orifice into the front maiden for double drive mode, with a medium bearing. Tighten the T-knob. speed flyer whorl. (The fast speed ADJUSTING THE FRONT MAIDEN whorl is attached to the wheel behind the rear maiden.) For double drive We have adjusted the maiden stop mode, the small end of the bobbin (black hex head screw at the bottom faces the flyer. Place one loop of the of the maiden) at the factory, but you drive band over the small end on the should check to see that it is adjusted bobbin and the other loop over one properly for your wheel. Look down of the grooves (pulleys) of the flyer from the top to where the flyer shaft whorl. enters the front bearing. There should be a 1/16” space between the bearing Adjust the tension on the drive band and the black shoulder of the flyer by turning the drive band tension shaft. If there is not, fold down the knob (the mushroom-shaped knob front maiden and use the 5mm hex on top). Start with a loose drive band. – 6 – Begin to slowly treadle, tightening drive band tension knob the tension knob until the flyer and large end small end bobbin both begin to turn. Now you of bobbin of bobbin whorl can begin to spin.
Details
-
File Typepdf
-
Upload Time-
-
Content LanguagesEnglish
-
Upload UserAnonymous/Not logged-in
-
File Pages12 Page
-
File Size-