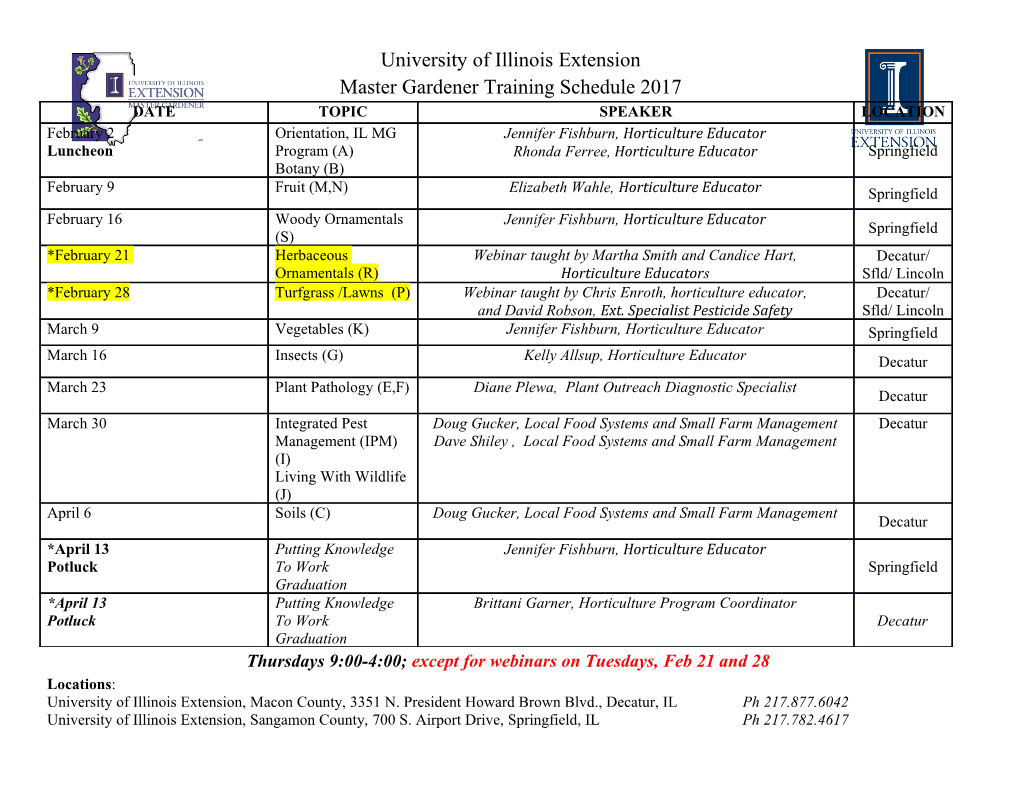
Europäisches Patentamt *EP000889156B1* (19) European Patent Office Office européen des brevets (11) EP 0 889 156 B1 (12) EUROPEAN PATENT SPECIFICATION (45) Date of publication and mention (51) Int Cl.7: D06L 1/00, C12S 11/00, of the grant of the patent: D06P 3/24, D06P 5/02, 08.01.2003 Bulletin 2003/02 D06B 3/04 (21) Application number: 96909363.2 (86) International application number: PCT/JP96/01019 (22) Date of filing: 12.04.1996 (87) International publication number: WO 97/031147 (28.08.1997 Gazette 1997/37) (54) PROCESS FOR PRODUCING WOVEN OR KNITTED FABRIC FROM YARN-DYED RAW SILK VERFAHREN ZUR HERSTELLUNG VON GEWEBEN UND GEWIRKEN AUS GARNGEFARBTEN ROHSEIDE PROCEDE DE FABRICATION D’UNE ETOFFE TISSEE OU TRICOTEE A PARTIR DE SOIE BRUTE TEINTE EN FIL (84) Designated Contracting States: (56) References cited: AT BE CH DE DK ES FI FR GB GR IE IT LI LU MC JP-A- 53 081 788 JP-A- 59 192 771 NL PT SE JP-A- 61 034 274 JP-B- 3 057 205 (30) Priority: 23.02.1996 JP 6182596 • DATABASE WPI Section Ch, Week 197544 Derwent Publications Ltd., London, GB; Class (43) Date of publication of application: F06, AN 1975-73489W XP002151657 & JP 50 07.01.1999 Bulletin 1999/01 031240 B (KANEBO LTD), 8 October 1975 (1975-10-08) (73) Proprietor: Sumitomo Corporation • DATABASE WPI Section Ch, Week 198613 Osaka-shi, Osaka 540-8666 (JP) Derwent Publications Ltd., London, GB; Class F06, AN 1986-086102 XP002151658 & JP 61 (72) Inventor: KANEHISA, Keiichiro 034274 A (NOVO IND AS), 18 February 1986 Takeno-gun, Kyoto-hu 627-01 (JP) (1986-02-18) (74) Representative: von Samson-Himmelstjerna, Friedrich R., Dipl.-Phys. et al SAMSON & PARTNER Widenmayerstrasse 5 80538 München (DE) Note: Within nine months from the publication of the mention of the grant of the European patent, any person may give notice to the European Patent Office of opposition to the European patent granted. Notice of opposition shall be filed in a written reasoned statement. It shall not be deemed to have been filed until the opposition fee has been paid. (Art. 99(1) European Patent Convention). EP 0 889 156 B1 Printed by Jouve, 75001 PARIS (FR) EP 0 889 156 B1 Description Technical Field 5 [0001] The present invention relates to a process for manufacturing woven or knit fabrics using yarn made of dyed raw silk. Related Art 10 [0002] Prior art yarn dyed silk woven fabrics have been manufactured from silk in which sericin or silk glue (about 25 % of the total weight of raw silk) which covers the periphery of the raw silk fibers is removed and thereafter only fibroin is dyed (the same may be applied to the knit silk fabrics). [0003] In order to twist yarn hard after sericin has been removed, twisting is generally carried out after conducting shrink proofing and twist setting for the silk yarns by using starch. However, manufacturing a great quantity of silk 15 fabrics for Japanese and Western clothes by this manufacturing process has encountered processing problems and is expensive due to the cost of yarn twisting or fabric manufacturing. Thus, the fabrics manufactured by this process have been used in only a restricted field of high grade Japanese clothes, such as kimono. Such a traditional technology, has a tendency to decline with the time due to problem in finding technically skilled successors. [0004] Due to these problems, few yarn dyed, hard twisted silk fabrics have been used. Piece dyed woven or knit 20 fabrics have been predominantly used in silk fabrics. There is a restriction that shrink-proofing and twist setting of silk yarns can not be achieved unless almost 100 % sericin is left in order to manufacture the fabrics using both wefts and warps of hard twisted yarns. Under this condition, the piece dyed fabrics are manufactured by following the steps as follows: (1) manufacturing of raw silk; (2) soaking and drying; (3) winding ; (4) first twisting; (5) doubling and twisting: (6) final twisting and twist setting; (7) weaving or knitting; (8) scouring (degumming) at a plant; (9) dyeing; (10) product. 25 [0005] The scouring at the plant consists of five steps as follows: 1. Preliminary scouring 98°C, 320 minutes (5 hours 20 minutes) (alkali scouring) 2. Main scouring 98°C, 600 minutes (10 hours) 30 (alkali scouring) 3. Finishing scouring 98°C, 60 minutes (one hour) (alkali scouring) 4. Drying finishing 5. Tentering, softening finishing 35 [0006] It takes an extended time. In order to shorten the period of time taken for preliminary and main scouring steps, a high pressure scouring may be conducted. Since the fabrics are dyed after removal of sericin to produce the piece dyed fabrics, the finished fabrics have various problems which will be described hereafter. 40 [0007] These problems occur due to the dyeing method which is adopted to conduct the piece dyeing method. A prior art method of dyeing 100 % silk fabrics having a large width will be briefly described with reference to Fig. 1. The prior art method which has previously been adopted as a method of dyeing fabrics having a large width is referred to as "suspend dyeing". An elongated and wide fabric 14 which is disposed in serpentine or spiral manner as shown in Figs. 1(b) and 1(c), respectively is suspended from parallel, or radial bars 10 with threads 12 in a predetermined interval 45 so that it is dipped into hot water and dye 16 in a dyeing tub 18 as shown in Fig. 1(a). [0008] A first problem of the piece dyed fabric resides in that the upper side of the fabric 14 to which threads 12 are bound is dyed to a color different from that of the lower side thereof if the fabric 14 has a width of about 114 cm or more. The condition of the dyed fabric 14 is schematically illustrated in Fig. 2. The fabric 14 is actually extended in a transverse direction in Fig. 2. The upper portion 14a (from the upper side 14c of the fabric 14 to about 114 cm lower 50 position) is dyed to a specified color although the lower portion 14b (from the about 114 cm position to the lower side 14d of the fabric 14) generally exhibits dense and light fading colors. It is estimated that this is due to the fact that the temperature of the hot water and mixing ratio of the dye 16 in the vicinity of the surface level in the tub 18 is delicately different from that in the vicinity of its bottom. [0009] A second problem of the piece dyed fabrics is that defects such as creases, rub marks, and wrinkles may 55 occur on the surface of the fabric 14. Since the fabric 14 is moved up and down and the water and dye 16 is heated with steam to about 100°C during the dyeing process, the fabric 14 that is suspended only through threads 12 could be waved or the lower side 14d of the fabric 14 could be rolled up so that the above-mentioned defects occur. It is obvious that a rub mark 15a is formed in the vicinity of the center of the fabric 14, a wrinkle 15b is formed in the vicinity 2 EP 0 889 156 B1 of a position to which a thread 12 is attached and a crease 15c is formed in the vicinity of the lower side 14d which is liable to be rolled up. [0010] A third problem of the piece dyed fabrics is that creases 15d and wrinkles 15e occur in the vicinity of upper and lower sides 14c ,14d of the fabric 14 when the fabric 14 has a width of 114 cm or more (refer to Fig. 4). This is due 5 to the fact that the center of the fabric 14 is loosened by the weight of the fabric and me water contained therein as represented by a two-dot-and-chain line in Fig. 4(a) since tentering to the fabric 14 is conducted in a wet condition during finishing treatment. If the loosened fabric 14 is tensioned as represented by a solid line in Fig. 4(a), an inward force acts against the outward tension so that the fabric 14 is not balanced. Thus, the creases 15d and 15e wrinkles may occur as shown in Fig. 4(b). 10 [0011] Due to the above-mentioned problems of the piece dyed fabrics, it has previously been very hard to piece- dye the silk fabric having a width of 150 cm. Accordingly, fabrics of a high yield rate having a width of 96 to 114 cm have been mainly manufactured so that defects such as crease, rub marks, wrinkles can be eliminated. [0012] However, there have been demands for silk fabrics having a large width (e.g. 150 cm) for various reasons which will be described hereafter. 15 [0013] A first reason why silk fabrics having a width of 150 cm are demanded is that a great cutting loss occurs if, for example, a double-breasted suit is produced from a piece dyed silk fabric having a width of 96 to 114 cm. The Japanese apparel sewing systems are currently on the top level in the world and are adapted to 150 cm width cloth. A great cutting loss of fabric occurs if one double-breasted suit is made from a fabric having a width of 96 to 114 cm. [0014] Fabric loss during manufacture of a double breasted suit is calculated with reference to Figs.5 and 6.
Details
-
File Typepdf
-
Upload Time-
-
Content LanguagesEnglish
-
Upload UserAnonymous/Not logged-in
-
File Pages19 Page
-
File Size-