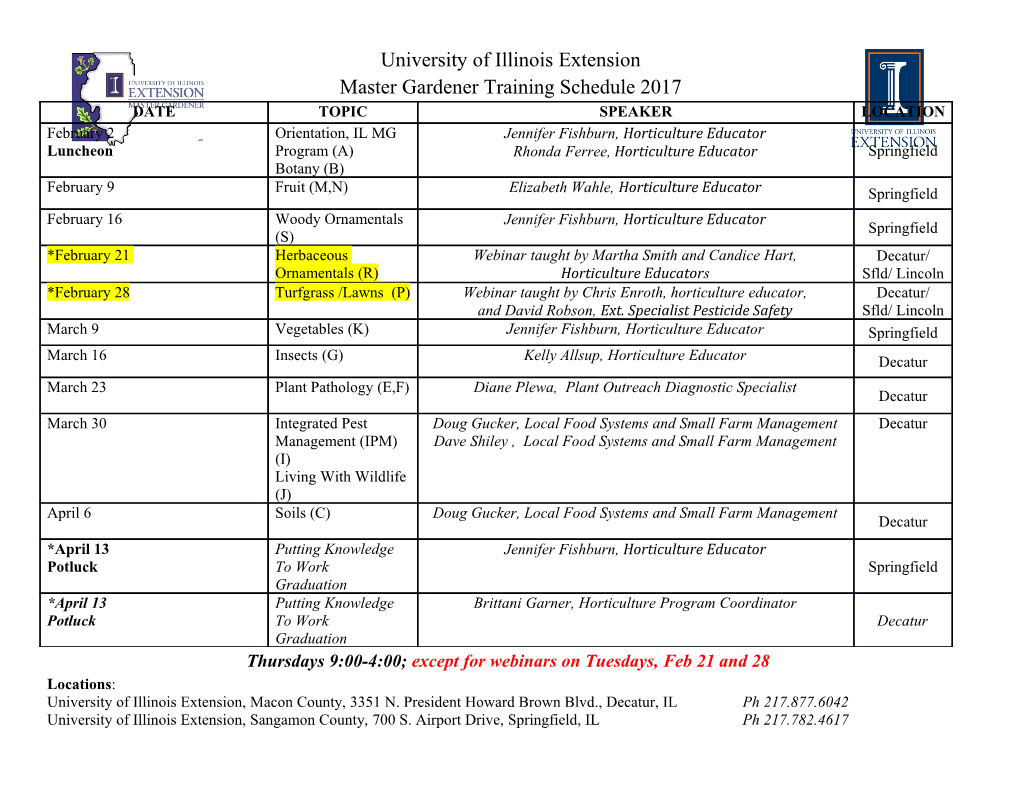
B Manutacturlnq of Forqed and Extruded Gears David J. Kuhlmann P.S.Raghupathi Battelle Columbus Division. Columbus, OH Introduction ience and trial and error. A preliminary ment program is required for every new Traditional. methods of manufacturing die is made, and a few parts are formed, design, which makes the precision precision gears usually ,employ either Measurements are taken of the finished fanning process economically less at- hobbing or shaper cutting. Both of these part, and the die is modified accord- tractive, especially when complex and processes rely upon generating the con- ingly, A second series of trials is con- precise geometries are involved, as with jugate tooth form by moving the work- ducted, and so on, until the final die gears. Therefore. methods need to be piece in a precise relation to the tool, geometry is obtained. Such a develop- developed to apply advancedeompu- Recently, attention has been ter-aided design and manufac- given to .forming gear teeth in a turing (CAD/CAM) single step. Advantages to such technologies (analysis of loads, a process include reduced pro- stresses, and temperatures us- duction time, material savings, ing finite element method based and improved performance approaches, etc.) to gear form- characteristics. Drawbacks in- ing die design and manufacture. elude complicated tool designs, This approach benefits hom the nan-uniformity of gears pro- capabilities of the computer in duced throughout the life ofthe performing complex mathe- tooling, and lengthy develop- matical analysis and mforma- ment times, tion storage, and allows the die Through projects funded by designer to examine the effects the U.S. Army Tank of various changes .0.£ process Automotive Command, Bat- variables on the die design, telle's Columbus Division without trying out each new developed a method for design- change on the shop floor, ing spiral bevel, spur, and helical gear forming dies. This CAD/CAM Applied To article discusses this method and Forging and Extrusion summarizes the current state of En.!ml-. Fo;rm~na In recent years, CAD/CM1i the art regarding the manufac- , lood. lDAlStr ...... techniques have been. applied to I I!I'Id f-onn!"I [ntlty turing of farged and extruded various forging processes. The gears. experience gained in all of these applications implies. a certain Traditi.onal 'Gear overall methodology for CAD I .Fornting Methodology CANt of dies for precision and/ Design/test/modify. The or near-net shape forming. This traditional method of forging computerized approach is also and extrusion die design and applicable to precision cold and manufacture is based on exper- Fig. 1- Methodology for designing gear Forming dies. hot forming of spiral bevel, 36 Gear Technology spur, and helical gears, as seen inFig, 1, analysis of a metal forming process. For used to determine the friction shear fac- The procedure uses as input; the process a given microstructure, the flow stress, tors of various lubricants. This test in- variables and the part: (gear) geometry, a, is expressed as a function of strain, E, volves taking a ring of known dimen- The former consist of: strain rate, t and temperature, T: sions and temperature and upsett-ing it (1) data on billet material under (thickness reduction) between Hat dies, forming conditions (billet and die pro- a = f(e,tT) (1) Measurement of the final imide and perties, such as flow stress as a function outside diameters plus thickness enable of strain, strain-rate, temperatures, and To formulate the constitutive equa- one Itocalculate the friction shear factor heat transfer coefficients), tion (Equation 1) it is necessary to con- of the lubricant. Thus, to accurately (2) the friction coefficient to quantify duct torsion, plane-strain compression, predict the loads when forming gears, it the friction shear stress at the material and uniform axisymmetric-compres- is important that data be obtained and die interface, and sion tests. During anyone of these tests, regarding the friction associated with (3) forming conditions, such as tem- plastic work creates a certain increase in the lubricant to be used. peratures, deformation rates, and sug- temperature of the billet material, which Estimation of Die Corrections, Tem~ gested number of forming operations. must be considered in evaluation and perature Effects. Temperatureaifects all Using the process variables and the use of the test results. forgings in two ways. First, when the part geometry, a preliminary design of Tooling and Eguipment. Theselec- workpiece is heated to be able to form the finish forming die can be made. tion of a machine for a given process is the part, it expands .. In addition, the Next, stresses necessary to finish form influenced by the time, accuracy, and material will always increase in the part and temperatures in the mater- load / energy characteristics of that temperature due to deformation ial and the dies are calculated. The elas- machine. Optimum equipmentselec- heating. After the part is formed, it tic die deflections due to temperatures tion requires consideration of the entire shrinks during cooling, Thus, the final and stresses can be estimated and used forming system, including lot size, con- part size will.always be smaller than the to predict the small corrections neces- ditions at the plant, environmental ef- die in which it was formed. The second sary on the finish die geometry. Knowl- fects, and maintenance requirements, as temperature effect comes from the tool- edge of the forming stresses also allows well as the requirements of the specific ing. The 'tooling will always be slightly the prediction of forming load and en- part and process under consideration. heated due to the transfer of heat from ergy. The estimation of die geometry The tooling variables include design the workpiece. Inaddition, the die may corrections is necessary for obtaining and geometry, surface finish, stiffness be intentionally heated if the part is to close tolerance formed parts and for and mechanical and thermal properties be formed at elevated temperatures. machining the finish dies to exact di- under conditions of use. This prevents premature toe 1failure or mensions. The corrected finish die ge- Friction and Lubrication aithe T0011 defect formation in the final part. As at ometry is used to estimate the necessary Workpiece Interface. The mechanics of result, the part formed will always be volume, and the volume distribution in interface friction are very complex. One larger than the size of the die manufac- the billet or the preform. Ideally, a way of expressing friction quantita- tured at "room temperature". Both of simulation of the metal flow should be tively is through a friction coefficient, p" conducted for each die design. This is a or at friction shear factor. m. Thus, the AUTHOR: ------- computerized prediction of metal flow frictional shear stress, 7, is -------------~. DAVID J. KUHLMANN, is manager of at each instant during forming. This the Net Shape Manufacturing Section of Bat- simulation allows the determination of T = anop, (2) telle Columbus Division. For the past seven the cavity filling without excessive or years he has been developing interactiVe. loading of the dies and prediction of graphics- oriented computer programs for metal forming processes and luis authored defects. several papers. where an is the normal stress at the in- Process Variables terface, a is the flow stress of the de- DR. P.!;. RAGHUPATHI, former.lywith Billet Material Characterization. (l) forming material, and f is the friction Battelle Columbus Division, is an expert in For a given materialcomposition and factor. the area of cold extrusion, dosed die forging. deformation I heat treatment history Friction estimation. The friction be- deep drawing, metal forming machine tools, (microstructure), the flow stress, and tween the workpiece and the tooling is and computer aided design and manufactur- ing. In addition to being the author/co- in the workability (or formability) dependant upon the die surface, the author of more than 30 publications, he .is various directions (anisotropy), are the temperature.and the type of lubricant. also a co-editor of the Metal Forming Hand- most important material variables in A standard testcalled the ring test, is book (Springer- Verlag. 7985). July/Augustl990 37 these temperature effects must be com- • The flow stress, D', and the temper- The friction force, FE, is equal to the pensated for when designing tooling ature are constant within the sum of the friction forces shown in rig. which one expects to use to form near- analyzed portion of the deforming 2. The remaining forces, Fid and fs]"are net parts. material. computed from measurements of the Shrink fitting. Shrink fitnngrefers to The basic approach for using the slab flow stress of the material being formed. the tedmiqueof pladng the forming die, method is as follows. Once the total punch force is calculated, which contains the cavity in which the 1..The region of materia] undergoing the punch pressure, as well as the radial part is formed, under a residual com- plastic deformation is identified. pressure in the die cavity, can be deter- pressive stress to permit higher forming Thus, the boundary between the mined. This last parameter is required in loads. This compressive stress is elastic and plastic regions of the order to determine and compensate for generated by using an interference be- workpiece material is identified. die deflections. tween the die and one or more outer 2. One of the three principal stresses Case 2: Forging. A typical too] setup for rings. As a result of this shrink fitting, (assuming TRESCA's yield condi- forging spuror helical gears is given in the dimensions of the die cavity wiU be tion will be used) should be deter- Fig. 3 In this case, the slab method is smaller than when it was machined. mined. Inmost cases it will be easy applied in similar fashion to extrusion, This dimensional shrinkage must also to determine certain points where except that in this case, each tooth can be accounted for when designing the one of the principal stresses must be thought of as being extrudedindivid- forming dies for near-net shape manu- be zero.
Details
-
File Typepdf
-
Upload Time-
-
Content LanguagesEnglish
-
Upload UserAnonymous/Not logged-in
-
File Pages8 Page
-
File Size-