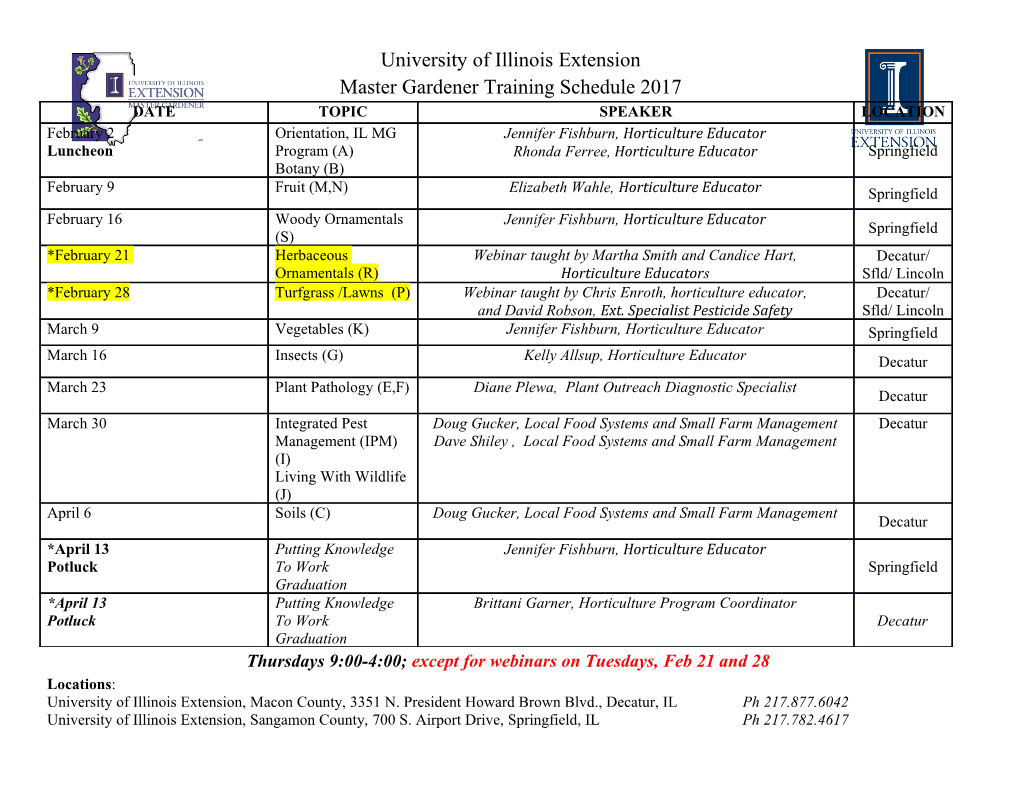
5-1 The Boeing 777: A Look Back Wolf L. Glende Chief Engineer-Systems 777 Airplane Program Boeing Commercial Airplane Group The Boeing Company P.O. Box 3707 Seattle, WA 98124-2207 U.S.A. ABSTRACT The Boeing 777 is the largest twin-engme commercial jet transport in service today. In 1990, approval to proceed with its development was contingent on defining an airplane the airlines would buy at a price Boeing could afford. Innovative processes were developed and implemented that focused on achieving customer preference and reduced program cost. These processes centered on Design Build Teams, Digital Product Definition, and Digital Preassembly. Two years after delivery of the first airplane, the data show that the processes made the 777 the preferred art-plane, lowered program costs as predicted, and set new standards and expectations for the development of jet transport aircraft. Figure 1. 777 First Flight INTRODUCTION The Model 777 (figure 1) is the newest member of the Boeing Its most significant feature, however, is the totally new way the family of airplanes, filling the gap between the Model 767 and air-plane was developed using digital technology and a “working 747. together” philosophy to meet customer requirements at a reduced It can carry from 300 to 550 passengersover distances up to 7,500 cost. This paper takes a look back at the design, the development challenge, the processes used, and how the airplane and those nmi, depending on configuration selected, at speeds of 330 kn/ 0.84 math. Its state-of-the-art features and technolortv. its award- processes are perceived 2 years after initial delivery. winning interior design, and its inservice performance since first delivery in May 1995 have earned it praise and recognition from the technical community, airlines, and passengersalike. Paper presented at the AGARD FVP Symposium on “Strategic Management of the Cost Problem of Future Weapon Systems”, held in Drammen, Norway, 22-25 September, 1997, and published in CP-602. 5-2 THE PREFERRED AIRPLANE The Model 777 was conceived with the strong help of our airline with minimal downtime and cost. The forward and aft cargo customers. Eight airlines in particular, from Europe, Southeast compartments provide 5,056 ft3 of cargo space for both ULD Asia, and the United States, worked with Boeing to configure an containers or pallets, with 600 ft3 capacity in a bulk cargo airplane they preferred. compartment. The result is the largest twin-engine airplane available (figure 2). Airplane systems are based on proven designs with advanced It is offered as a family of airplanes with takeoff gross weights technology features added on the basis of enhanced performance, ranging from 506,000 lb to 660,000 lb in three configurations: reliability, and economy. 777-200, -200IGW, and -300, with additional growth versions The flight deck is designed with extensive human factors and under study (figure 3). The 777 is offered with a choice of engines industrial design influence to enhance pilot comfort and reduce from three manufacturers at various thrust ratings (74,000 lb to fatigue, especially important on long-haul flights. Six large LCD 98,000 lb thrust) depending on the requirements of the customers. displays provide flight control, navigation, engine and alerting The latest materials technology is used for Improved structural information with improved visibility, readability, and reliability durability, maintainability, and inspectability, while providing a at reduced space, weight, power, and heat. New functionality is lightweight and cost-effective design. provided for display management, data communication, and electronic checklist to allow the crew to operate the airplane more An all-new circular fuseIage cross-section offers greater flexibility efficiently. in cabin arrangement and cargo carrying capability. The passenger cabin provides an open and spacious interior with a high level of Fly-by-wire flight controls are provided for primary, secondary, seating versatility, ranging from six abreast in first class to seven and high-lift control surfaces. The design maintains conventional or eight abreast in business class and nine or ten abreast in control characteristics and controllers to retain existing pilot cues, economy class. Lavatory and galley complexes are movable within with selected enhancement functions added to reduce workload. flexibility zones to permit the airline to reconfigure the interior Figure 2.777 General Arrangement 450 0 IeseIvice r “0”” 0 Launched 400 A Study 350 Tri-ClS3S seats 250 Dc-bo-lo 0 A360-60OR 767-3OOER A340-200 A340.6000 -’ B 767-360 ““““8” O 200 767-200 A31 O-300 767-2WER 0 0 0 I I I I I 150 I 3,cOo 4,000 5,OCO 6,ow 7,000 8,WO 9,ow Rangecapability, nmi Figure 3. Family Plan 5-3 The 777 avionics include the first use of an integrated, modular avionics concept on a commercial transport. Functionality for primary displays, flight management, thrust management, control maintenance,data communication, airplane condition monitoring, and flight data recording is implemented in two avionics cabinets cost Of each with eight line replaceable modules. The four input/output change modules and four core processormodules use a common hardware and software architecture. This implementation results in reduced weight and power consumption with increased reliability, simplified system interfaces, and improved fault isolation compared to federated systems. A new multitransmitter data bus (ARINC 629) permits increased communication between all Figure 5. Traditional Cost Drivers systems. resulting in improved functionality, reliability, cost, and weight. Software is onboard loadable to reduce spares costs and Change, error, and rework needed to be reduced, to reduce cost. permit faster incorporation of functionality improvements. Data showed that part interferences and fitup problems in the factory were major reasons for engineering change (figure 5). The electrical power system provides increasedredundancy (three Since the cost of change increases significantly, the later the main generators, two backup generators, one standby ram air change is implemented, major cost savings would be achieved turbine-driven generator, four permanent magnet generators) to by reducing change, error, and rework after design release. satisfy fly-by-wire and ETOPS requirements. We would need to deliver a service-ready, reliable airplane on The onboard centralized maintenance system is designed with the day promised, without benefit of a prototype program. Our the needs of the line mechanic in mind to facilitate rapid problem customers were tired of finishing the airplane development in resolution and return to service. Reliable, redundant systems, revenue service and would only purchase an airplane that worked. combined with the functionality and extensive coverage of the Furthermore, to market the airplane successfully against three- maintenance system, ensure our customers high airplane and four-engined airplanes, the 777 needed to meet stringent availability for revenue service. reliability requirements for 180.min ETOPS (extended-range, twin-engine operations) at entry into service. This would be an THE 777 DEVELOPMENT CHALLENGE industry first, since past models required 2 years of inservice In 1990, the Boeing challenge was how to develop an airplane experience to obtain ETOPS approval. that was preferred by our customers at a price they were willing We would need to communicate more effectively among 4,500 to pay and we could afford to build. Key attributes included: engineers,200 suppliers and 6,500 manufacturing employees.This 1, An airplane preferred over the competition becauseof superior communication would be vital to reduce change, error, and rework functionality, reliability, maintainability, and economics. due to late or incomplete design information. 2. Reduced overall costs. based on a 300-airplane program. This resulted in a program development plan (figure 6) that focused on the following: 3. Service ready at delivery. l Involving the customer to define the preferred airplane. Reducechanges, error, and l Ensuring that all parts are designed to work and fit together reworkafter design release before release, for 50% reduction in change. error, and Customerrequirements rework. l Working together to share facts and data and resolve issues. These goals were implemented by “preferred processes” that were at the heart of the 777 Program: Reducedcast l Design/Build Teams. l Digital Production Definition. l Concurrent Product Detinition. Firm l Digital Preassembly. Managedesired varlablltty l Enhanced Validation. Wotkrng together Figure 4. 777 Development Challenge A review of past programs identified the major challenges that needed to be addressedto make the program a success(figure 4). Most fundamentally, we needed to determine what the customer wanred. This was definitely not an easy task, since requirements from multiple airlines can be quite diverse and even contradictory. Wohg together Figure 6. 777 Development Plan 5-4 DESIGN/BUILD TEAMS (DBT) Development of a jet transport is a large and complex task available for the best possible decision prior to design release. involving many organizations in many locations. This largeness This process, implemented by program direction and extensive and complexity create their own set of problems. Activities tend training and continuously reinforced, encompassed Boeing, its to be conducted in series with results ‘*thrown over the fence”; suppliers, and customer airliners. communication
Details
-
File Typepdf
-
Upload Time-
-
Content LanguagesEnglish
-
Upload UserAnonymous/Not logged-in
-
File Pages11 Page
-
File Size-