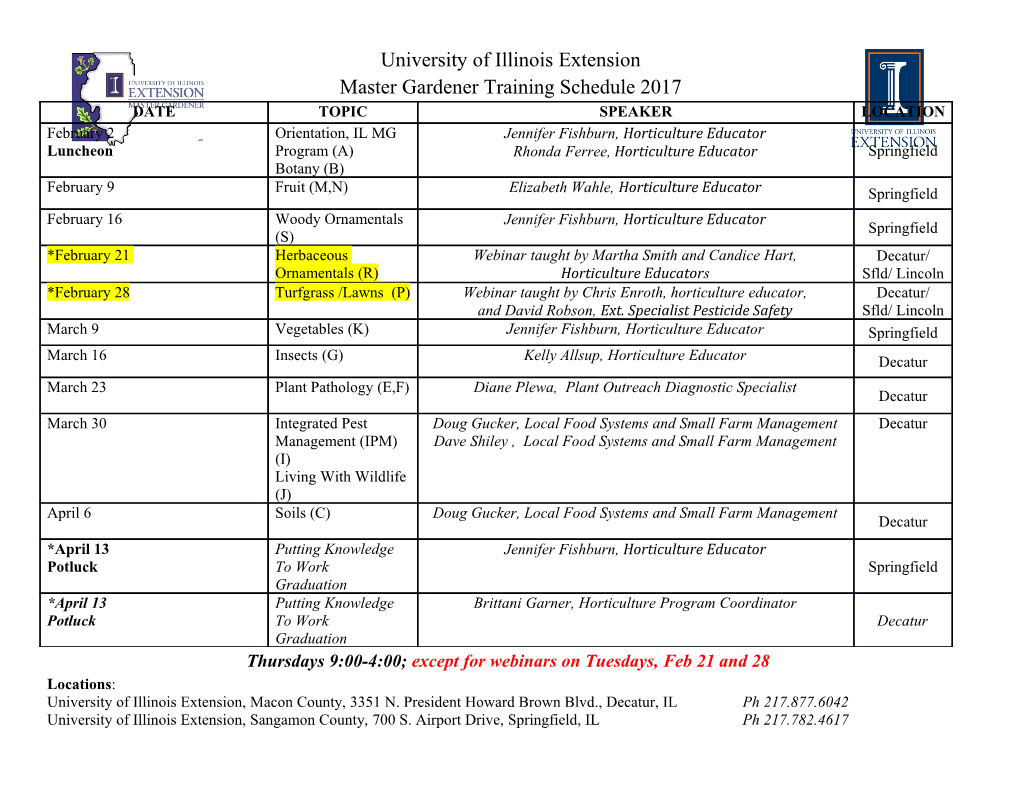
Magnetic Shape Memory Alloys as smart materials for micro-positioning devices. Arnaud Hubert, Nandish Calchand, Yann Le Gorrec, Jean-Yves Gauthier To cite this version: Arnaud Hubert, Nandish Calchand, Yann Le Gorrec, Jean-Yves Gauthier. Magnetic Shape Memory Alloys as smart materials for micro-positioning devices.. Advanced Electromagnetics Symposium, AES’12., Apr 2012, TELECOM PARISTECH, Paris, France. pp.1-10. hal-00720674 HAL Id: hal-00720674 https://hal.archives-ouvertes.fr/hal-00720674 Submitted on 25 Jul 2012 HAL is a multi-disciplinary open access L’archive ouverte pluridisciplinaire HAL, est archive for the deposit and dissemination of sci- destinée au dépôt et à la diffusion de documents entific research documents, whether they are pub- scientifiques de niveau recherche, publiés ou non, lished or not. The documents may come from émanant des établissements d’enseignement et de teaching and research institutions in France or recherche français ou étrangers, des laboratoires abroad, or from public or private research centers. publics ou privés. Magnetic Shape Memory Alloys as smart materials for micro-positioning devices A. Hubert1∗, N. Calchand1, Y. Le Gorrec1, J.-Y. Gauthier2 1Institut Femto-ST UMR 6174, UFC/ENSMM/UTBM/CNRS, 24 rue Alain Savary, 25000 Besanc¸on, France 2Laboratoire Amp`ere UMR 5005, Universit´ede Lyon/CNRS, INSA Lyon, bˆatiment A. de Saint-Exup´ery, Avenue Jean Capelle, 69621 Villeurbanne cedex, France *corresponding author, E-mail: [email protected] Abstract most used adaptive materials for positioning application. Nevertheless, alternative solutions exist and MSMAs are a In the field of microrobotics, actuators based on smart ma- class of active materials which typically generate 6% strain terials are predominant because of very good precision, in- in response to externally applied magnetic fields [12]. In tegration capabilities and high compactness. This paper contrast to conventional heat driven shape memory alloys presents the main characteristics of Magnetic Shape Mem- (SMAs), the magnetically driven MSMAs exhibit higher ory Alloys as new candidates for the design of micromecha- operating frequency, making them attractive for actuation tronic devices. The thermo-magneto-mechanical energy applications. Most of the work on characterization and conversion process is first presented followed by the ade- modeling of MSMAs has been focused on quasistatic ac- quate modeling procedure required to design actuators. Fi- tuation, i.e., strain dependence on magnetic field. Very few nally, some actuators prototypes realized at the Femto-ST studies take into account the dynamical behaviour and even institute are presented, including a push-pull bidirectional fewer propose MSMA based actuator prototypes. The pur- actuator. Some results on the control and performances of pose of this paper is to present a modeling proceduretaking these devices conclude the paper. into account the complex magneto-mechanicalbehaviors of MSMA and the dynamical characteristics of actuators at the 1. Introduction same time, to design new micropositioning devices. Electromagnetic devices have become promising con- tenders in the area of ultra-high precision manufacturing, Among all the offer concerning magnetic active materi- manipulation and sensing. Most of these promising new als, Magnetic Shape Memory Alloy is a relatively new can- technologies uses active/adaptive materials as a base for didate. It was first experimented in 1995/1996 at the MIT actuation principles because of compactness, integrations for the Ni-Mn-Ga alloy [13] and at the University of Min- and smart use capabilities [1, 2]. This paper reports recent nesota for the Fe-Pd alloy [14]. Since these first works, lots results obtained using a new type of smart material called of researchs have been conducted all around the world (see Magnetic Shape Memory Alloy (MSMA) which is an alloy [15, 16] for reviews) but very few concrete applications ex- of Ni-Mn-Ga. ist today due to the complex dynamic behaviour of MSMA and due to the difficulties to improve its manufacturing pro- Currently, most of the high-precision devices use piezo- cess. Currently, only single crystal samples present signifi- electric materials such as PZT because of their high- cant magneto-mechanical coupling characteristics and even dynamic bandwidth and their nearly linear behaviour. if a lot of studies are conducted concerning thin films de- Piezoelectric materials are used to design microposition- position and polycrystal samples [17, 18], these types of ing devices by using classical mode of working [3, 4] or structures are presently less adequate for actuation applica- by using stick and slip mode of working [5, 6]. In the tions because of a lower magneto-mechanical coupling. field of magnetic active materials, the main applications use magnetostrictive materials [7, 8] especially Terfenol- MSMA can be seen as a mixture of a classical shape D. This material is the most used because of the important memory alloy (SMA) and a magnetostrictive material. In progress in its performances since its first use in 1950 by a way, its microscopic behaviour is similar to SMAs but the Naval Ordnance Laboratory in the USA and its high strain is not only due to a martensite/austenite phase trans- magneto-mechanical coupling compared to the other mag- formation but is also due to a martensite reorientation un- netostrictive materials. Examples of actuators and position- der magnetic fields. In this second mode of working – ing devices using magnetostrictive materials can be found martensite rearrangement –, MSMA can be compared with in [9, 10, 11]. standard magnetostrictive materials but with a much more important magneto-mechanical coupling (6 % of maximal Piezoelectric and magnetostrictive materials are the strain for Ni-Mn-Ga instead of 0.16 % for Terfenol-D). Austenite Martensite variants This paper first explains the working principle of this active material and gives some tools for static and dy- m1 m namic behaviour modeling. Then, some design rules will 2 m be presented to propose efficient actuators. These mod- 3 A M1 M2 M3 eling works will be used as guidelines to design a new (a) micro-positioning stage. It will be based on two antag- onist MSMA-based actuators to perform a one-degree-of- freedom linear axis stage with a full-range motion of the y M1 Cooling + order of millimeters and a micrometers precision. Mea- A M2 x surements conducted on the prototype will be presented and + M3 commented. Heating Heating Stress application 2. Basis on MSMA modeling and behaviour Stress Stress M2 application 2.1. MSMA Properties and Characteristics M1 M2 M1 As seen before, the working principle of MSMA is quite Magnetic Magnetic field field application similar to the working of SMA but its actuation can also result from magnetic field application. This second mode (b) of working allows to increase significantly the dynami- cal bandwidth of the device because it uses a magneto- Figure 1: MSMA behaviour: (a) austenite phase and the mechanical energy conversion process instead of a thermo- three martensite variants and (b) martensitic reorientation: mechanical. Since fifteen years, these materials knew some effects of mechanical stress, magnetic field and tempera- improvements concerning mainly the working temperature ture. range and the maximum available strain. When actuated by magnetic fields, a large strain (6 to 10 %) is obtained with a response-time in the range of milliseconds (to com- pare with tenth of seconds or even seconds for SMA). Besides these interesting properties, the material also The MSMA used in this paper is a non-stoechiometric Ni- has some important drawbacks. They are the brittleness Mn-Ga monocrystal corresponding to the most currently of the single-crystal, the high required magnetic field (400 used MSMA materials. In this alloy, the martensite phase kA/m), the large dependence of the material parameters on appears in three different variants corresponding to the temperature changes, a small blocking stress (2-3 MPa) and three possible crystallographic directions in the sample (see a large hysteretical thermo-magneto-mechanical behaviour. Fig. 1 (a)). More details about the structural properties of this material The martensitic reorientation principle is presented in can be found in [15]. Fig. 1 (b): at high temperature, the MSMA sample is in austenitic phase (A). After a cooling process, the austenite 2.2. Quasi-Static Modeling of MSMA phase is transformed into a martensite phase without any favoured variants. Therefore the resulting sample contains Two theories can be used to model the behaviour of martensite variants into three equal portions (M1, M2 and MSMA: M3). If a mechanicalstress is applied in a specific direction, • The first one is based on microscopic properties and then the fraction of variant with its short axis in this direc- physics of solid. The following papers are represen- tion grows. If this stress is high enough then the sample will tative of the works done on MSMA materials with only contain this variant (for example M2 in Fig. 1 (b)). If this approach [19, 20, 21, 22]. the stress decreases, the volume fraction of the M2 variant also decrease but in an irreversible behaviour (large hystere- • The second one is based on macroscopic properties sis). In a same way, if a magnetic field is applied, the vari- and thermodynamics. In [23, 24, 25], such mod- ant with its easy magnetization axis in the field direction, is els are proposed whereas in [26, 27, 28], a more favoured. For MSMA, the easy magnetization direction is mechatronics-based approach is taken. They explic- the same as the short axis of the M1 variant. In this case, itly take into account the salient features (dynamics this variant fraction increases as shown in Fig. 1 (b) by the of system) required to make actuators. application of a magnetic field perpendicular to the stress field. The balance between magnetic field and mechanical While the first theory is prefered by physicists, the second stress allows a control of the macroscopic strain.
Details
-
File Typepdf
-
Upload Time-
-
Content LanguagesEnglish
-
Upload UserAnonymous/Not logged-in
-
File Pages11 Page
-
File Size-