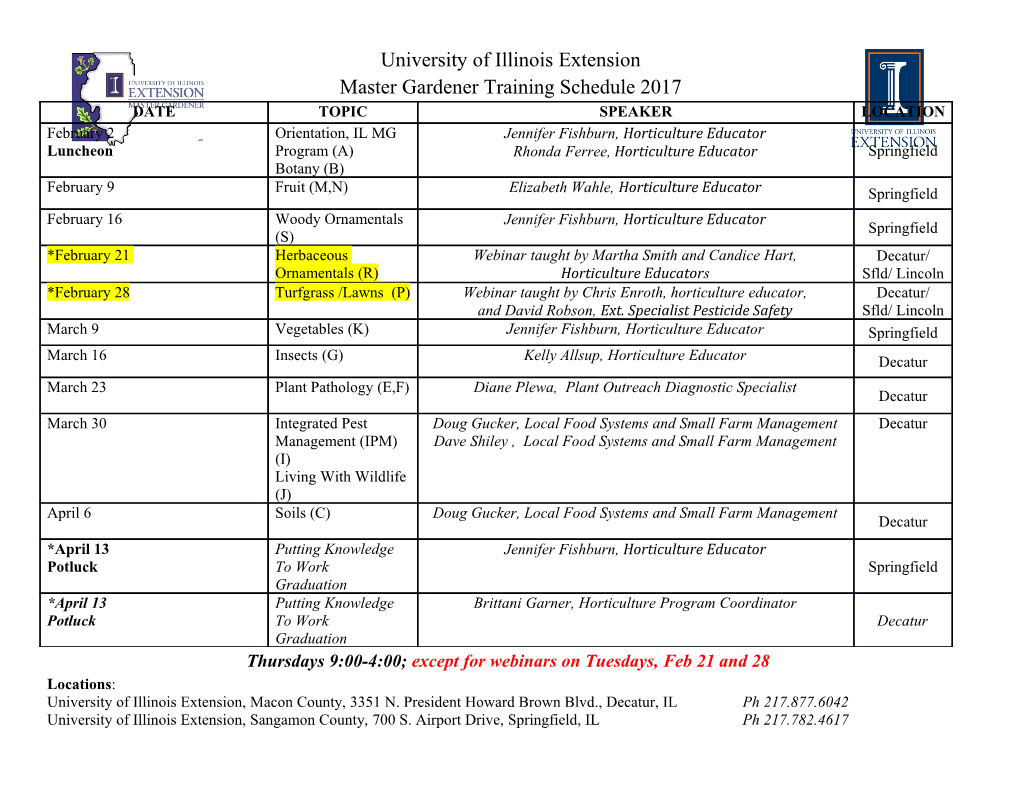
A Novel Method for the Production of Microwires by Alexander Michael Couch B.S., United States Naval Academy (2017) Submitted to the Department of Mechanical Engineering in partial fulfillment of the requirements for the degree of Master of Science in Mechanical Engineering at the MASSACHUSETTS INSTITUTE OF TECHNOLOGY February 2019 Massachusetts Institute of Technology 2019. All rights reserved. redacted A u th o r ...........................................................Signature .. Department of Mechanical Engineering 1, y.- january 14, 2019 Certified by...........Signature redacted ......... Kasey Russell Principal Member of the Technical Staff, The Charles Stark Draper Laboratory Certified by.....SignatureC ertified by ....... redacted Thesis.... .....Supervisor .. Irmgard Bischofberger Assistant Professor of Mechanical Engineering Signature redacted Thesis Supervisor A ccepted by ............. .................. MASSACHUSES INSTITUTE I Nicblas Hadjiconstantinou OF TECHNOWOGY Chairman, Department Committee on Graduate Theses FEB 252019 LIBRARIES ARCHIVES A Novel Method for the Production of Microwires by Alexander Michael Couch Submitted to the Department of Mechanical Engineering on January 14, 2019, in partial fulfillment of the requirements for the degree of Master of Science in Mechanical Engineering Abstract Radio frequency (RF) systems such as cell phones and GPS can perform better and last longer if we can reduce electrical heat loss in the wires. This is typically done in power systems by twisting or weaving the wires, following one of several patterns. Though, at radio frequencies, wire dimensions must scale down by as much as 1000 times in order to achieve the same effects. This project decomposes the problem into two main categories; the manufacturing of micron scale wires and the manipulation of these wires in order to form a twisted bundle. This project aims to produce twisted bundles of wire that have an AC resistance value at GHz frequencies approaching a fundamental limit in which electrical resistance is independent of frequency. This thesis focuses specifically on the first major problem: producing micron scale wires of considerable length. In order to accomplish this, I have developed a bottom-up approach to the manufacturing of microwires. Rather than reducing the diameter of a wire by drawing through successive dies, I have instead formed a wire by metalizing a small nanofiber core to reach the target diameter. Initially, I designed a mechanical system to harvest Nomex nanofibers 200-400 nm in diameter that have been electrospun onto a spinning drum. Next, I designed a system to concentrically coat the harvested nanofibers with a conductive seed layer via sputter deposition. Finally, I have designed a reel to reel system in order to electroplate over a segment of seeded nanofiber in order to achieve the target diameter. This now allows for the creation of microwires of considerable length for use in high frequency applications. Thesis Supervisor: Kasey Russell Title: Principal Member of the Technical Staff, The Charles Stark Draper Laboratory Thesis Supervisor: Irmgard Bischofberger Title: Assistant Professor of Mechanical Engineering 2 Acknowledgments This thesis was prepared at The Charles Stark Draper Laboratory and was funded by the Air Force Research Laboratory (AFRL) and the Defense Advanced Research Projects Agency (DARPA) under Contract No. FA8650-15-C-7543. Draper Labora- tory was instrumental in providing me with both the guidance and funding necessary for a meaningful graduate experience. Every person in the A2P program has pro- vided me with assistance and without them, I would not have been able to contribute meaningful research and write a coherent thesis. Specifically, I would like to thank Kasey Russell, my thesis co-supervisor, for being so supportive and helping me find a project that is both interesting to me and can contribute to the program as a whole. I would also like to thank David Carter, who has been instrumental in helping with my research and the logistics regarding the Draper Fellow Program. Peter Lewis has also greatly helped in my research, helping with SEM imaging and using the Focused Ion Beam at MIT, as well as many other small things. Heena Mutha has also greatly helped, working closely with me on electroplating and providing guidance in an area I had never previously worked in. I would like to thank Irmgard Bischofberger, who served as my thesis co-supervisor and included me in her lab group at MIT over the past two years. Irmgard, through her leadership and passion for research, has cultivated an innovative and welcoming research group culture, and I learned a lot both from her and from the other members of our lab group. Through group presentations of my progress, both Irmgard and my fellow group members have been able to provide meaningful feedback and have thus been instrumental in my work. I am incredibly grateful that the Navy allowed me the opportunity to pursue my Master's Degree through the Immediate Graduate Education Program. Graduate school has provided me with an opportunity to better myself academically and has also allowed me to learn more about myself. I would also like to thank my friends and family for their tremendous support throughout my time here. Without them, I would not be where I am today. 3 Contents 1 Introduction 11 1.1 Motivations for the Production of Microwires .............. 11 1.2 Current Methods for the Fabrication of M icrow ires ........... ............ .......... 13 1.2.1 The Wollaston Process . ........ ....... ...... 14 1.2.2 Taylor-wire Process ............... ......... 15 1.2.3 Further Developments of the Taylor-wire Process ....... 16 1.2.4 Other Methods for Creating Fine Wires .... ......... 17 1.3 A Proposal for a New Method of Creating Fine Wires ........ 18 1.3.1 Electrospinning .. .............. .......... 18 1.3.2 Sputter Deposition ....... ............ ..... 22 1.3.3 Electroplating .......... ............ ..... 25 2 Nanofiber Harvesting 27 2.1 Challenges Associated with Small Diameter Fibers ... ........ 27 2.2 Initial Harvesting Efforts .. ............ ........... 30 2.3 Fluidic Tensioning of Nanofibers . ......... ......... .. 31 2.4 Mechanical Spooling System ....... ............. ... 32 3 Sputtering a Conductive Seed Layer onto a Nanofiber 36 3.1 Sputtering System and Requirements .................. 36 3.2 Fiber Sputtering Assembly Design .................... 37 3.3 Sputtering Results ..... ............ ........... 39 4 4 Electroplating Over a Conductive Nanofiber 41 4.1 Initial Electroplating Efforts ... ......... 41 4.2 Contactless Electroplating in a Reel-to-Reel System 44 4.3 Reel-to-Reel Electroplating . ............ 47 4.4 Proof of Concept for Reel-to-Reel Electroplating 52 5 Conclusions 54 5.1 Thesis Summary .................. 54 5.2 Future Work. .................... 55 A Bill of Materials and Engineering Drawings for Mechanical Spool Design. 57 B Bill of Materials and Engineering Drawings for Fiber Sputtering Assembly 65 C Bill of Materials and Engineering Drawings for Electroplating As- sembly 72 5 List of Figures 1-1 Graph showing the effect of frequency on skin depth for a copper wire in the G H z range. ..... ............ ........... 12 1-2 Schematic demonstrating typical wire drawing equipment. The wire is pulled from a coil onto a rotating bull block, passing through a die and is reduced in diam eter [4]. .................... .... 13 1-3 Taylor-wire drawing cylinder. f, 2mm diameter holes used for drawing. c, steel rod used to hold the copper cylinder in position. a, copper cylinder containing holes used for drawing [7]. ........... 15 1-4 Taylor-Ulitovski process in progress at Microfir Tehnologii Industriale Ltd. Shown is a glass tube with a drop of metal alloy heated by a high frequency inductor. This glass tube with molten metal is then drawn through an orifice to create a glass coated microwire [15]. ....... 17 1-5 Schematic illustration of the electrospinning process. The illustration also shows a typical SEM image of the nonwoven mats often formed and a drawing of the Taylor cone [22] ................... 19 1-6 Plexiglas disk with copper wires used by P. Katta et al to collect aligned nanofibers formed via electrospinning. [23]. ... ........ .... 20 6 1-7 Top: Image of equipment used to electrospin fibers with the metallic needle appearing in the top left of the image and the grounded col- lector appearing in the center of the image [25]. Bottom: Functional schematic illustrating how electrospinning is implemented. The left of the image represents the metallic tip where the fiber originates. This metallic tip is able to move laterally along the length of the grounded and spinning collector, allowing for the collection of a continuous fiber. 21 1-8 Aligned Nomex fibers on the spoked-drum collector. ....... ... 22 1-9 Schematic of a simplified DC sputtering system [291. Shown is a target (cathode) from which metal atoms are ejected, the substrate (anode), a pump to evacuate the chamber, and an argon feed. ........ 23 1-10 Image of the KDF 900 series system [30]. This system is an example of a DC Magnetron sputtering system and is used in this research. 24 1-11 Schematic demonstrating the establishment of a charge on a metal when placed into an electrolyte solution [32]. .......... .... 25 1-12 Schematic demonstrating the main components of a DC electroplating system [32]. .......... ............ .......... 26 2-1 Graph demonstrating the scaling issues associated with Nomex fibers of small
Details
-
File Typepdf
-
Upload Time-
-
Content LanguagesEnglish
-
Upload UserAnonymous/Not logged-in
-
File Pages84 Page
-
File Size-