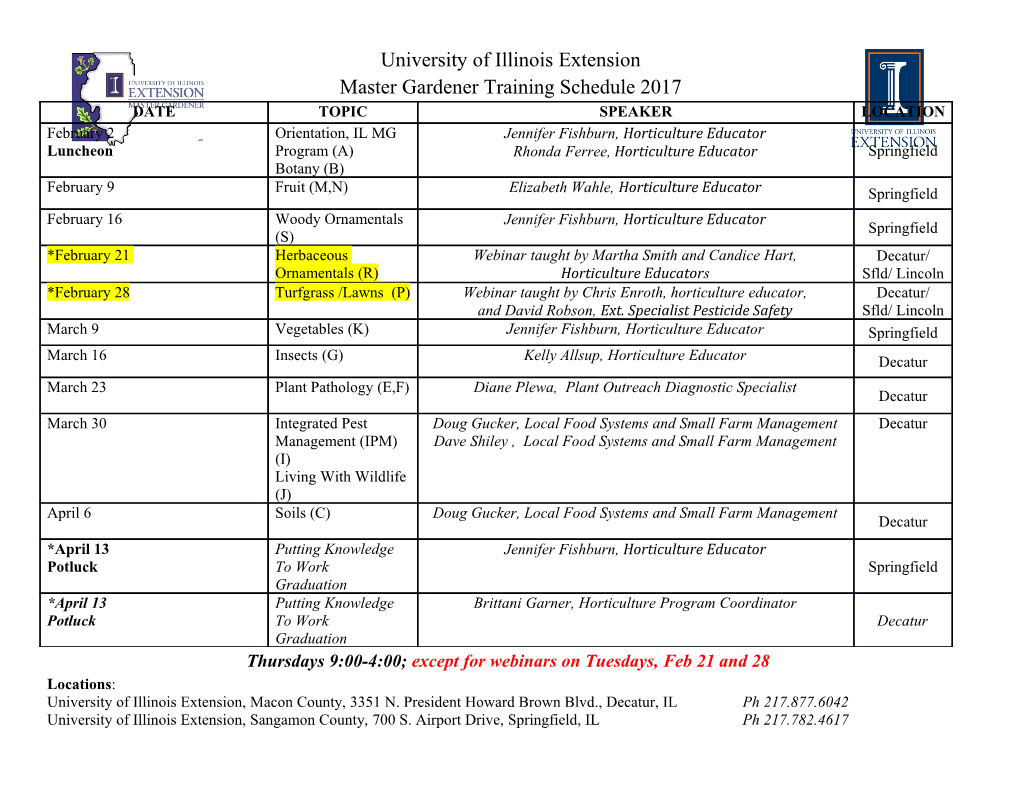
Hydride Bed Activation Zack Trotter Paul Foster Summer Schaufler REVIEWED AND DETERMINED TO BE UNCLASSIFIED. Tritium Engineering THIS REVIEW DOES NOT CONSTITUTE CLEARANCE FOR PUBLIC RELEASE. DERIVATIVE CLASSIFIER: S. J. Mazurek, SRTE DA Mgr. (NAME/PERSONAL IDENTIFIER AND POSITION TITLE) October 2018 DATE: 10/08/2018 Purpose • New hydride material contained in hydride beds needs to be activated prior to use in the facility. • Activation is accomplished by exposing the hydride material to hydrogen isotopes to improve the rate of absorption and capacity of the hydride bed and to remove impurities from the material. 2 History • All hydride beds that have been installed in the facility have been activated. • The same basic cart set-up has been in use since 2003. • Improvements have been made with each activation evolution. • 2017 Activation Improvements include: – Use of protium for first two hydrogen flushes (vs deuterium) – Rail system upgrades to accommodate both types of hydride beds used in the facility – Reduced size of exhaust hoses for improved heating – Elimination of ice bath for cooling – Improved leveling technique – Improved insulation – Improved procedure and simplified data collection tables 3 2017 Preparations – Basic Equipment • Heaters – Watlow Star heaters used to heat nitrogen flowing through bed jacket • Heated nitrogen used to desorb activation gas off the bed • Thermocouples – Used to determine when bed fully desorbed • Connected to nitrogen inlet and outlet as well as process outlet • Mass flow controller – Rumor that the flow controller needed to be replaced • Determined functionality, needed to be calibrated, saved money 4 2017 Preparations – Basic Equipment • Hydrogen compressed gas cylinder gage and safety valve – Previously used rig was used for another project and now tritium contaminated, no direct replacement readily available • Made a new rig, updated CLI information for base rig used and separated from stores to maintain as the activation cart rig Shiny new rig 5 2017 Preparations – Initial Improvements • Gaskets previously used were not rated for the target temperature – Specified and used higher rated gaskets (High temperature Garlock) • Insulation previously used was not rated for the target temperature – Specified, fabricated and used higher rated insulation – New insulation made of Calcil • Heat transfer during heating and cooling steps reconsidered – Reduced exhaust hose size which sped up desorption by reducing hot nitrogen removal – Higher rated insulation covered more of the hydride bed than previous insulation – Removed Calcil insulation during cooling steps – Eliminated ice bath during absorption steps to reduce leak checking requirements and rework 6 2017 Preparations – Other Improvements • Used protium for first two hydrogen flushes – Previously deuterium was used for all three flushes – Deuterium was used for the third and final flush – Protium is significantly cheaper than deuterium and easier to handle (does not need to be tracked by the facility) • Improved rail system used to hold hydride beds to accommodate both types of hydride beds used in the facility – New rail system accommodates Gen 1 and FACE beds – FACE beds were activated in place when installed in 2004 – Upcoming replacements mean FACE beds will need to be activated out of glovebox • Beds can only be activated in place during initial installation – FACE beds are ~1 ft longer than TCAP beds, requiring the rail system to be highly movable. 7 2017 Preparations – Other Improvements • Improved leveling technique – Additional steps • slide horizontally x10 • Final step – lift the process nozzle side about 20° 8 2017 Activation Oct 2017 9 Activation – Oct 2017 • Safety – Barricade – O2 monitor – Earplugs while desorbing • Conduct of Operations (ConOps) – Shift turnover • Between activation shift engineers – Shiftly communication with control room • Radiological Safety – Received numerous activity alarms • Caused by high flow rate of cooling and heating gas into hood and possible Calcil dust during flushes • Evacuated process room until cleared by RCO (radiological control operations) 10 2017 Absorption Data 1st - Protium 2nd - Protium 3rd - Deuterium 11 2017 Desorption Data 1st - Protium 2nd - Protium 3rd - Deuterium 12 Lessons Learned, Future Improvements • Improvements on insulation. Cover more of bed (feet, nozzles, etc) and consider a blanket to drape over that could be easily removed during cooling steps. – Feet of the beds were un-insulated contributing to heat loss – Tucking in hydride beds with a blanket could also help trap heat during desorption • Stock ALOT of earplugs – Exhaust hoses were very loud after switching to a smaller diameter hose 13 Acknowledgements Jared Clark Tommy Gibson Scott Williams Kim Wilson Jimmy Gibson Jim Klein Terri Wannamaker Cale Gustafson Katie Heroux Davis Cyr Chris Johnson Doug Glass David Reece Clark Cason Will Chesson John Dicks Brittany Hodge Wesley Mitchum Steve Funk 14 Thank you for your attention! • Questions? 15.
Details
-
File Typepdf
-
Upload Time-
-
Content LanguagesEnglish
-
Upload UserAnonymous/Not logged-in
-
File Pages15 Page
-
File Size-