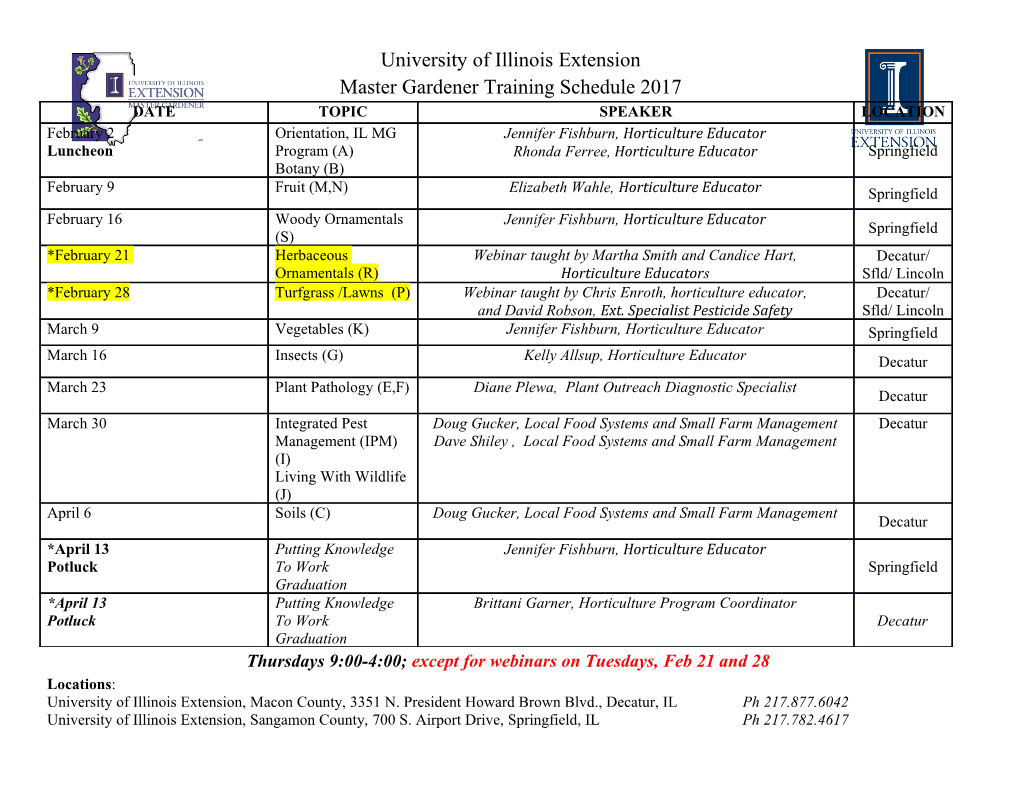
Downloaded from orbit.dtu.dk on: Oct 07, 2021 Clinker Burning Kinetics and Mechanism Telschow, Samira Publication date: 2012 Document Version Publisher's PDF, also known as Version of record Link back to DTU Orbit Citation (APA): Telschow, S. (2012). Clinker Burning Kinetics and Mechanism. Technical University of Denmark. General rights Copyright and moral rights for the publications made accessible in the public portal are retained by the authors and/or other copyright owners and it is a condition of accessing publications that users recognise and abide by the legal requirements associated with these rights. Users may download and print one copy of any publication from the public portal for the purpose of private study or research. You may not further distribute the material or use it for any profit-making activity or commercial gain You may freely distribute the URL identifying the publication in the public portal If you believe that this document breaches copyright please contact us providing details, and we will remove access to the work immediately and investigate your claim. TECHNICAL UNIVERSITY OF DENMARK (DTU) Clinker Burning Kinetics and Mechanism Samira Telschow Ph.D. Thesis Kim Dam-Johansen (DTU) Flemming Frandsen (DTU) Supervisors: Stig Wedel (DTU) Kirsten Theisen (FLSmidth A/S) Department of Chemical and Biochemical Engineering Combustion and Harmful Emission Control Research Centre Preface The present dissertation summarizes the research activities between March 2008 and August 2011 performed as a member of the Combustion and Harmful Emission Control (CHEC) research center at The Department of Chemical and Biochemical Engineering at the Technical University of Denmark (DTU) and is submitted as a partial fulfillment for obtaining the Ph.D. degree at the DTU. The dissertation was supervised by Kim Dam-Johansen (DTU), Flemming Frandsen (DTU), Stig Wedel (DTU) and Kirsten Theisen (FLSmidth A/S). Experimental was mainly carried out at DTU and at the FLSmidth laboratories in Dania (Denmark). Financial support was granted by The Danish National Advanced Technology Foundation and FLSmidth A/S. I would like to thank my supervisors Kim Dam-Johansen, Kirsten Theisen, Flemming Frandsen and Stig Wedel for their guidance and support during the study. Discussions have been always interesting and challenging, catalyzing my professional and personal development immensely. I would like to especially acknowledge Anders Tiedje for all the energy and support with the designing and constructing of the new setup. The swift help on some operational challenges is very much appreciated. Furthermore, I like to thank Nikolaj Nissen, Mette Larsen, Thomas Wolfe, Henrik Kløft and the KT workshop for all the technical support. I owe many thanks to all the staff at the FLSmidth laboratories in Dania for providing me with help in the XRD, XRF, Free lime- and Light microscopy- analysis. The vast amount of sample analyses wouldn’t have been possible without their help. M.Sc. and B.Sc. students Anette Münther and Ingeborg Jørgensen are gratefully acknowledged for their contribution to the project. A special thanks to M.Sc. Lars Jørgensen for his great effort and patience to test the maiden setup, especially in extracting results. May he never need to grind any clinker again. At last, many thanks to my family for all their support through the last 4 years. Big thanks to Matthias, who has been there, when times were though. Kgs. Lyngy, January 31st, 2012 i Summary The industrial cement process is subject to several changes in order to reduce the high energy consumption and thereby increase the profitability of cement production. These changes also affect the core of the entire cement producing process: the clinker formation in the rotary kiln. Thus, in order to maintain or even improve clinker quality (and output), we need a better understanding of the development of clinker properties inside the kiln to react upon the impact of process changes. Clinker formation in industrial rotary kilns is very complex due to a vast number of interacting parameters: kiln dimensions, rotation velocity, temperature, gas composition, heat transfer phenomena, etc. These conditions can only be partly simulated in ordinary lab-scale experiments. Thus, the objectives of this project have been to establish test equipment to simulate the industrial clinker burning process on a laboratory scale and to conduct clinker formation experiments in order to derive knowledge on gradual clinker property development, as a function of different process parameters. A new lab-scale setup rotary kiln simulator (RKS) was designed and built for this purpose. It is assembled of two parts: an ordinary lab-scale heating furnace and a sample motion system. The motion system consists of a SiC tube, which moves the sample, placed in a Pt/Rh-crucible, at a chosen velocity through the heating furnace. Simultaneously, the sample is rotated around its horizontal axis with a chosen rotation velocity. The heating furnace consists of five individual heating zones, which are set to obtain a temperature ramp from ~900-1540 °C. Furthermore, the atmosphere in the system can be set to any mixture of N2, O2 and CO2. Thus, the rotary kiln simulator features most important parameters of the industrial cement rotary kiln (ICRK): gradual temperature increase, rotation velocity and gas phase composition. An investigation of clinker formation vs. heating profile and rotational velocity were conducted, and the influence on the clinker phase composition and clinker agglomeration was deduced. Independent of the raw meal used, the different clinker phases were formed in three stages: 1. C2S, C3A and C4AF formation at ~900-1350 °C; 2. Clinker melt formation at ~1350-1400 °C; and 3. C3S formation at >1350 °C. The first temperature of clinker melt occurrence varied slightly depending on the type of raw meal used. ii The influence of different heating profiles on clinker formation was studied, and it was observed that C3S formation was more complete, the faster the sample was heated to a temperature >1400 °C. However, only with relative long residence times above this temperature clinker phase compositions similar to industrial clinker, i.e. with high C3S concentration and low CaO concentration, were obtained. It was concluded, that the maximum temperature of 1540 °C in the RKS does not simulate the maximum temperature in the ICRK. Thus, the maximum temperature of 1450 °C, as is often stated in literature, is likely often not applicable. Agglomeration of the raw meal was observed to start already at 900 °C. The agglomerates formed are first rather weak, but increase in hardness with increasing temperature. The size of the agglomerates as well as the amount formed was found to be dependent on the rotation velocity: the higher the rotation velocity, the higher was the amount of agglomerates < 1mm. The higher rotation velocity also resulted in a decrease of the total amount of agglomerates, whereas the amount of material lining on the reactor walls increased. The establishment of the RKS setup will allow more realistic clinker formation studies in future and thus potentially an experimental lab-scale access to the understanding of important parameters in the ICRK. The obtained qualitative and quantitative data on clinker phase composition and on agglomerate formation depended on operational parameters are essential for the development/improvement of models for bed material process in the ICRK, and for the development steps to improve the reactor technology. iii Dansk resumé: Cementproduktion i industriel skala har gennem årene undergået flere betydelige ændringer med henblik på at nedbringe energiforbruget og dermed øge rentabiliteten af processen. Disse ændringer har naturligvis også påvirket klinkerdannelsen i rotérovnen. Med henblik på at forbedre eller opretholde klinkerkvalitet (og -kvantitet), har cementproducenterne derfor brug for bedre forståelse af udviklingen af klinkerkarakteristika og -egenskaber i rotérovnen. Klinkerdannelse i industrielle cement rotérovne er en kompleks proces der er influeres af et utal af interagerende parametre: ovndimension (længde + diameter), rotationshastighed, temperaturprofil igennem ovnen, gassammensætning i ovnen, varmetransportfænomener, osv. Disse forhold har det hidtil kun i yderst begrænset omfang været muligt at simulere i lab-skala eksperimenter. Derfor har det primære formål med dette projekt været at etablere lab-skala testudstyr der kan simulere den industrielle cementklinkerbrændingsprocess, samt anvendes til at studere klinkerdannelse med henblik på at udlede viden om dynamikken i klinkerdannelsesprocesserne, som funktion af forskellige drifts- og procesparametre. Et nyt lab-skala set-up, en rotérovnssimulator (RKS), er blevet designet og bygget til dette specifikke formål. Den består af to dele: en høj-temperatur ovn, og et set-up som kan bevæge og rotere prøven. Sidstnævnte består af et SiC rør der anvendes til at bevæge prøven med en given hastighed gennem høj-tempetratur ovnen og samtidigt rotere prøven omkring dens vandrette rotationsakse med en foruddefineret rotationshastighed. Prøven er placeret i en Pt / Rh-smeltedigel for enden af SiC røret. Høj-temperatur ovnen har fem individuelle opvarmningszoner, der er indstillet således at temperaturen øges fra ~900 til ∼1540 ° C med en given temperaturprofil. Atmosfæren i systemet består af enhver blanding af N2, O2 og CO2. Rotérovnssimulatoren kan derfor simulere alle de vigtige driftsparametre der karakteriserer
Details
-
File Typepdf
-
Upload Time-
-
Content LanguagesEnglish
-
Upload UserAnonymous/Not logged-in
-
File Pages180 Page
-
File Size-