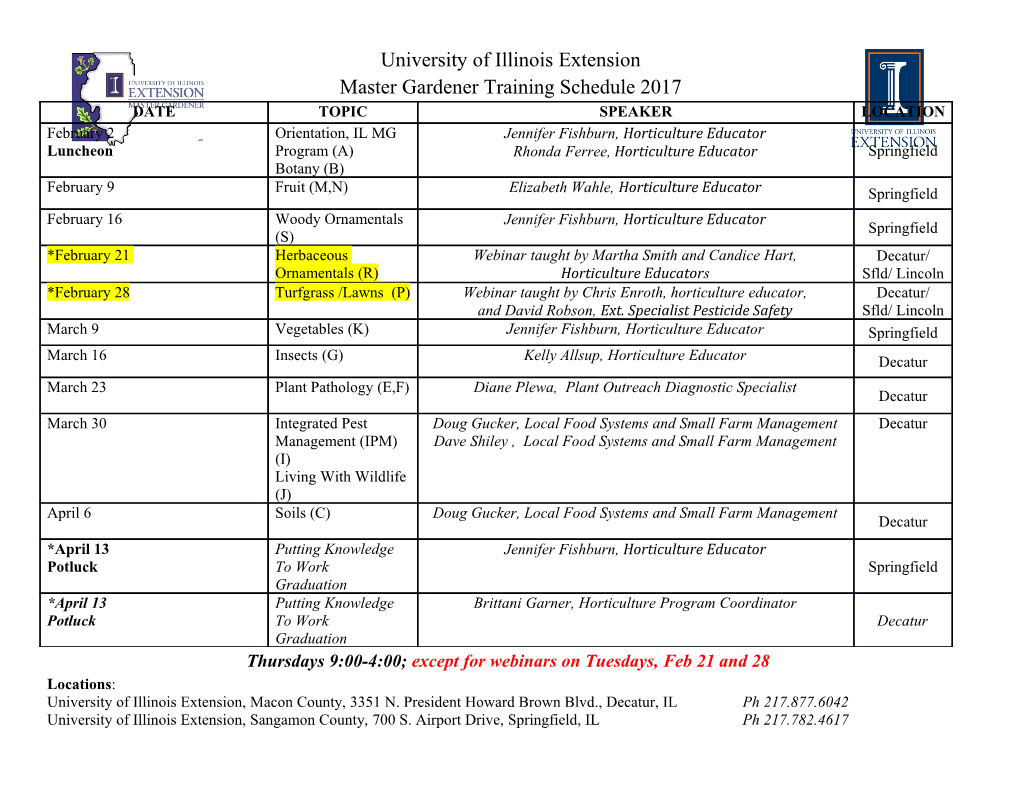
CHAPTER 18 RAPID PROTOTYPING RAPID PROTOTYPING FOCUSES ON BUILDING FUNCTIONAL PARTS A three-dimensional (3-D) model makes it a lot easier to visual- be passed around a conference table for a hands-on inspection ize the size and shape of a prospective new product than any two- and review, providing an opportunity for all present to detect dimensional (2-D) rendering or image. In the past, designers and flaws, omissions, or objectionable features that could create man- engineers who wanted a 3-D model of a planned product to hold, ufacturing problems and lead to its failure in the marketplace. It hand around, and evaluate, had to order one custom-made from is important that these problems be discovered early on in the wood or metal; skilled model makers took a long time to build design phase, before tooling is ordered. Early identification of them, and they were expensive. If, as a result of evaluation, design problems saves time and can eliminate the higher cost of design changes were recommended, more time and money had to making design corrections during the production phase. Any cor- be spent in either correcting the model or ordering a new one. rections that are identified can be made to the CAD drawings so Fortunately, with the introduction of computer-aided rapid proto- they are reflected in a revised prototype. All RP prototypes can typing some 20 years ago, model or prototype-making was accel- be helpful in reducing the time-to-market of the product, espe- erated, and the cost of each model was drastically reduced. Since cially important for highly competitive consumer goods. that time the technology has evolved: older processes have been In addition to model making, some RP technologies have improved and new ones have been introduced. Prototypes can been adapted for the short-run manufacture of functional parts or now be made full size or scaled down from a variety of materials tools. These RP processes are classified under the general head- in a wide range of colors, and the technology has achieved global ing of rapid manufacturing (RM), solid free-form fabrication, status. computer-automated manufacturing, and layered manufacturing. Rapid prototyping (RP) is a class of computer-aided tech- The same or comparable materials—plastic, metal, or ceramic— nologies for building 3-D prototypes from a range of materials that would be used to mass-produce a product can be used for based on data obtained from computer-aided design (CAD) these short runs. Some RP technologies are now being used to drawings. The dimensional data in digital form taken from CAD manufacture replacement or spare parts for maintaining or drawings is converted into build directions for the 3-D model on repairing older existing or obsolete machines. These RP tech- various RP machines or systems. Typically these call for the con- nologies eliminate the high cost and delay incurred in reproduc- struction of the model one layer at a time. The objective of all RP ing the original production tooling. Yet another offshoot of RP, systems is the fabrication of prototypes, molds, and even func- rapid tooling (RT), focuses on the economical design and fabri- tional parts or tools faster and more economically than they could cation of certain specialized functional tools which can also be be made by skilled persons using hand tools or conventional made from the same or equivalent materials as the mass-produced machine tools. tools. A 3-D prototype gives engineers, designers, and others con- The term “rapid” as it applies to RP technologies is, of course, cerned with the design and manufacture of a product a more con- relative; even the fastest RP fabrication process takes from 3 to venient way to evaluate a proposed design and elicit comments 72 hours, depending on the size and complexity of the prototype. on it. Persons participating in the evaluation process typically Nevertheless, all of these methods are faster than the weeks or include manufacturing, marketing, and sales managers, suppliers, even months required to fashion a prototype by traditional hand- dealers, and even prospective customers. The model or models can crafted methods. RAPID PROTOTYPE PROCESSES Most commercial RP technologies are layered or additive pro- from these molds. Other RP processes are subtractive mean- cesses and many call for post-process hand or machine finish- ing that the prototype or functional object is machined from ing to obtain the desired finish or dimensional precision. solid blocks of material under computer control. The materi- Layers of plastic, paper, wax, and powdered metal or ceramic als might be plastic resin or easily machined metals such as are combined to create solid or hollow 3-D objects. Some spe- aluminum, magnesium, or their alloys. This machining is typi- cialized RP processes focus on economical and rapid prepara- cally done automatically by computer numerically controlled tion of sand or wax molds for traditional metal casting. (CNC) milling machines directed by software derived from Magnesium, aluminum, iron, and steel parts have been cast CAD data. 462 RAPID PROTOTYPING STEPS There are five steps in the production of a rapid prototype: 1. Prepare a CAD Drawing of the Prototype: It is necessary to produce a 3-D drawing file with the necessary dimensional data to prepare the software that will direct the RP build process. 2. Convert the CAD Data to STL Format: After the solid model is drawn, its dimensional data must be converted by special- ized software to files that can be used by the RP equipment. Of the available software to do this, the STL format is con- sidered the industry standard. It provides an approximation of the surface and solid characteristics of the model as a net- work of triangles called facets. The STL file contains only approximate information about the shape of the object because curved surfaces cannot be represented precisely by triangles. While increasing the number of facets improves the accuracy of the representation, it involves an accuracy- speed trade-off. The larger the file, the more time it will take to convert the file to build instructions; this means that it will Fig. 1 Build Envelope: The rapid prototyping indus- take more time for the RP equipment to build the prototype. try’s term for the maximum size of any object or 3. Convert the STL File into Cross-Sectional Layers: In the model that can be built with one of the RP technolo- third step, preprocessing software converts the STL file into gies. It is given as length X, width Y, and height Z software that will actually direct the RP system how to build dimensions in inches or millimeters. The size of the the model in layers. Typically this software permits the size, object that can be built depends on the materials location, and orientation of the model to be selected. The X, used in the process or the capacity of the RP equip- Y, Z coordinates of an RP build envelope are illustrated in ment or system. A short Z dimension minimizes the Fig. 1. The size of this envelope for most RP processes is layers required. typically less than 1 ft3. The shortest dimension is usually oriented along the Z direction because this direction directly relates to build time. The preprocessing software “slices” the STL model into many layers; the thickness of these layers depends on the RP process selected and the accuracy require- from the system, removing any temporary structural supports ments. Many RP systems offer a range of “slice” thickness and, in some cases, recycling excess materials. Prototypes made that can vary from 0.0025 to 0.5 in. (0.06 to 13 mm). The from photosensitive plastic resins usually must undergo a final software can also generate the temporary structures needed ultraviolet (UV) curing step to complete the hardening of the pro- to support the model while it is being built. Features such as totype. Other finishing steps might include cleaning and sanding, overhangs, internal cavities, and thin-walled sections require sealing, painting, or polishing the prototype to improve its support; many RP system manufacturers include their own appearance and durability; however it might also need additional proprietary preprocessing software which includes provi- machining to improve its dimensional accuracy. sions for building these supports. Each of the RP processes is focused on a specific market seg- 4. Construct the Prototype in Layers: The fourth step is the ment, taking into account its requirements for model size, dura- actual construction of the model. Using techniques described bility, fabrication method, process speed, and prototype finish. later, the RP system builds the prototype one layer at a time Some RP processes are not suitable for building large models, from materials that are principally polymers, paper, powdered and each process yields a model with a different finish. The metal, or powdered ceramic. Most RP systems are essentially choice of the most appropriate RP method for any given applica- autonomous, so they need very little human intervention. tion depends on the urgency of the project and the cost and time 5. Clean and Finish the Model: The fifth and final step is post- saving of building an RP prototype versus producing the proto- processing. This typically calls for removing the prototype type by conventional model-making procedures. COMMERCIAL RAPID PROTOTYPING CHOICES In 2006 there were eight recognized additive RP systems and at enough prototypes to justify purchasing the systems. For those least one subtractive RP system available commercially and organizations that need only a few per year, there are third- supported by their manufacturers; each has its own unique party contract service providers who will produce them in their strengths and drawbacks.
Details
-
File Typepdf
-
Upload Time-
-
Content LanguagesEnglish
-
Upload UserAnonymous/Not logged-in
-
File Pages11 Page
-
File Size-