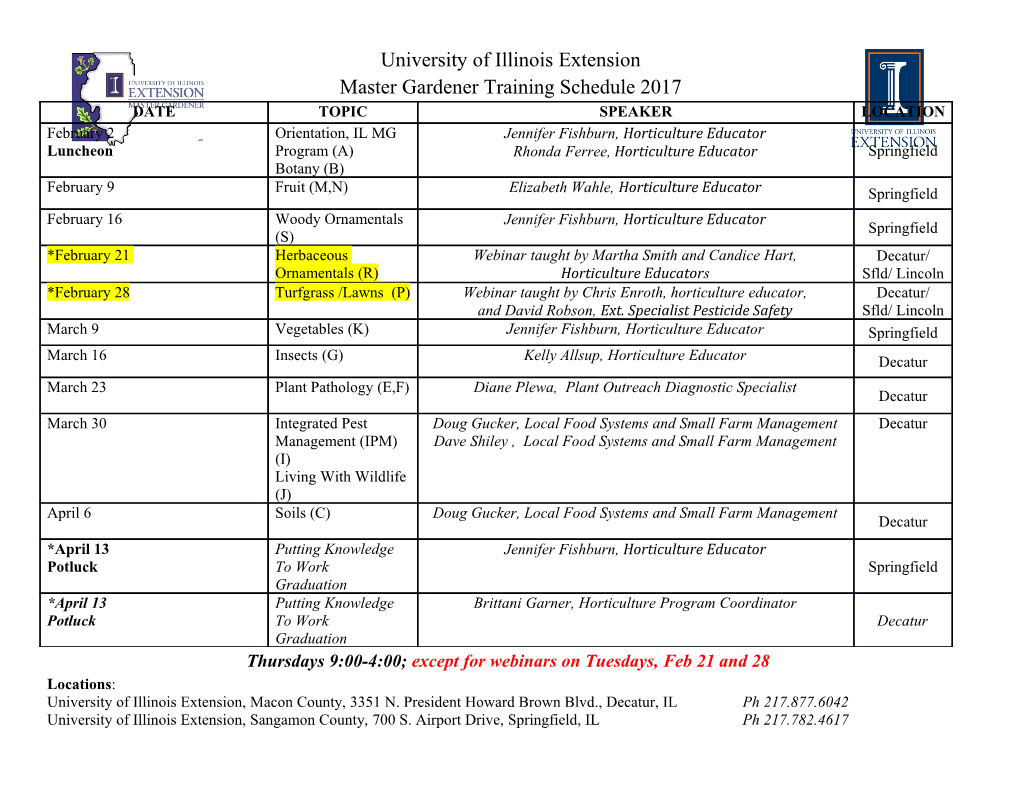
Master's thesis carried out at the Department of Mathematical Sciences and Technology of the Norwegian University of Life Sciences and submitted in partial fulfilment of the requirements for the M.Sc. degree at the Department of Mechanical Engineering of the University of Kassel Free decay testing of a semisubmersible offshore floating platform for wind turbines in model scale Examiners: Prof. Dr.-Ing. Martin Lawerenz Author: Felix Kelberlau Prof. Dr.Ing. Tor Anders Nygaard Abstract Wind turbines can be installed on floating platforms in order to use wind resources, which blow above the deep sea. The presented research investigates the hydro- dynamic behaviour of the Olav Olsen Concrete Star floater in free decay motion. The floater is a new design of a semisubmersible offshore floating platform for wind turbines. The thesis describes the physical free decay testing of a 1/40 plastic scale model in a water basin as well as numerical simulations of the same test cases with the aero- hydro-servo-elastic code 3Dfloat. Tests are performed for the heave and pitch degree of freedom and without mooring lines. The experimental results are compared with the simulation results in order to find adequate added mass and damping coefficients for the numerical model and to validate 3Dfloat for the prediction of heave motions. The overall added mass coefficient for the vertical direction is found to be CM = 2.71 and the damping behaviour is simulated by using a Morison coefficient of CD = 8.0 and a considerable amount of additional linear damping. Subsequently, the results are discussed in order to find possible causes for discrepancies between the results. I \We are like tenant farmers chopping down the fence around our house for fuel when we should be using Nature's inexhaustible sources of energy { sun, wind and tide. [...] I hope we don't have to wait until oil and coal run out before we tackle that." Thomas Edison (1931) (Newton, 1989, p. 31) II Preface and acknowledgement This thesis is submitted in partial fulfilment of the requirements for the Master of Science degree in \Erneuerbare Energien und Energieeffizienz" (Renewable Ener- gies and Energy Efficiency) at the Department of Mechanical Engineering of the University of Kassel. It was carried out between April and September 2013 at the Department of Mathematical Sciences and Technology of the Norwegian University of Life Sciences in As,˚ Norway. I would like to express my very great appreciation to Professor Dr.Ing. Tor An- ders Nygaard for supervising this thesis project and being helpful in all questions concerning my stay in Norway. His support was more than one could expect. I wish to thank Professor Dr.-Ing. Martin Lawerenz for giving me the freedom that was needed to work on this Master's thesis abroad. Trond Landbø and Jos´eAzcona Armend´arizdeserve my gratitude for giving a good introduction to the project and maintaining my work progress by providing all needed information. In the phase of physical model building, Bjørn Brenna was supporting me with tools and useful advice, what I would like to acknowledge. My special thanks go to the colleagues in our office for making the work not only educational but also convivial. III Contents List of tables VII List of figures VIII Nomenclature X 1 Introduction 1 2 Thesis background 4 2.1 Development of wind energy usage . 4 2.1.1 Early mechanical use of wind energy . 4 2.1.2 Wind turbines for producing electricity . 7 2.1.3 Offshore technologies . 10 2.2 Olav Olsen Concrete Star Wind Floater . 14 2.3 Project description . 16 3 Theoretical bases 17 3.1 Coordinates system and degrees of freedom . 17 3.2 Oscillations and damping . 18 3.3 Scaled model testing . 20 3.3.1 Scaling methodology . 20 3.3.2 Froude similitude . 22 3.3.3 Reynolds invariance . 23 3.4 Keulegan-Carpenter number . 24 3.5 Hydrodynamic forces . 25 3.5.1 Morison equation . 25 3.5.2 Linear damping . 29 IV 4 Methodology of model testing 30 4.1 Test case description . 30 4.1.1 General information about the performed tests . 30 4.1.2 Heave drop test case . 31 4.1.3 Pitch drop test case . 31 4.2 Testing environment . 31 4.2.1 Physical testing in water basin . 31 4.2.2 Numerical simulation with 3Dfloat . 33 4.3 Model description . 34 4.3.1 General assumptions . 34 4.3.2 Physical scale model . 35 4.3.3 Numerical scale model . 39 5 Physical and numerical test results 45 5.1 General observations . 45 5.1.1 Heave drop test case . 45 5.1.2 Pitch drop test case . 46 5.2 Period length . 48 5.2.1 Heave drop test case . 48 5.2.2 Pitch drop test case . 50 5.3 Damping behaviour . 50 5.3.1 Heave drop test case . 50 5.3.2 Pitch drop test case . 53 5.4 Keulegan-Carpenter number . 53 5.4.1 Heave drop test case . 53 5.4.2 Pitch drop test case . 55 6 Discussion of results 57 6.1 Period length and added mass . 57 6.1.1 Heave motion . 57 6.1.2 Pitch motion . 58 6.2 Damping coefficients . 59 6.2.1 Heave motion . 59 V 6.2.2 Pitch motion . 61 7 Conclusion and outlook 63 Bibliography i Declaration iv A Appendix v Data sheets of sensors . v Drop test results, single test runs . viii 3Dfloat input file . x Manual calculation of added mass . xiii VI List of tables 3-1 Conversion of units between translational and rotational movements . 20 3-2 Scale factors commonly used for Froude scaling . 23 3-3 Influence of skin friction and form drag on the drag term . 25 4-1 Key figures of the OO Star floater in full scale and model scale . 35 4-2 Masses of the different parts of the scale model and their ballasts . 39 4-3 Volume of water displaced by the scale model . 39 4-4 Cross section areas of one leg of the physical and numerical model . 44 5-1 Key figures of the results of 14 cm heave drop test . 47 5-2 Key figures of the results of pitch drop test . 49 VII List of figures 2-1 Model of a Persian vertical axis windmill . 5 2-2 Overview of the historical development of European horizontal axis windmills . 6 2-3 Wind turbine in Denmark, designed by Poul La Cour . 8 2-4 Common types of bottom fixed foundations for offshore wind turbines 11 2-5 Types of floating platforms for offshore wind turbines . 12 2-6 Concrete Star Wind Floater by Dr. techn. Olav Olsen AS . 15 3-1 Coordinates system and degrees of freedom . 18 3-2 Polygons of forces for prototype and model . 21 3-3 Influence of Reynolds number on drag coefficient . 24 3-4 Potential flow around a circular cylinder . 26 3-5 Relative importance of drag vs. inertia forces within Morison equation and its applicability for small vs. large structures . 28 4-1 Breadboard construction for moving the model in heave direction . 32 4-2 Breadboard construction for turning the model in pitch direction . 33 4-3 Scale model of the OO Star platform with tower, without ballast . 36 4-4 Sketch of the OO Star platform in model scale . 38 4-5 Visualization of the numerical scale model in three views . 41 4-6 Cross section of one of three legs, divided into bucket, pontoon and tower area . 42 4-7 Cross section of one of three legs, divided into bucket, pontoon and tower areas: grey and black for physical model, coloured for numerical model . 44 5-1 Heave drop test results, experimental mean data . 46 VIII 5-2 Pitch drop test results, experimental mean data . 48 5-3 Heave drop test damping behaviour, experimental and numerical data 51 5-4 Heave drop test results, experimental and numerical data . 52 5-5 Pitch drop test damping behaviour, experimental and numerical data 54 5-6 Pitch drop test results, experimental and numerical data . 55 6-1 Picture of the DeepCWind 1/8 scale model . 61 A-1 Data sheet of Honeywell 945-L4Y-2D-1C0 ultrasonic distance sensor . vi A-2 Data sheet of SBG IG 500-N inertial navigation system . vii A-3 Heave drop test results, single test runs . viii A-4 Pitch drop test results, single test runs . ix A-5 3Dfloat input file 1/4 . x A-6 3Dfloat input file 2/4 . xi A-7 3Dfloat input file 3/4 . xii A-8 3Dfloat input file 4/4 . xiii A-9 Manual calculation of added mass . xiii IX Nomenclature Symbols Symbol Description A Area C Coefficient D Characteristic Diameter/Spring rate F Force F r Froude number g Gravitational constant K Constant KC Keulegan-Carpenter number L Characteristic length λ Scale factor m Mass π Number Pi Re Reynolds number ρ Density S Submerged length T Period u Velocity u_ Acceleration V Volume x Distance in x-direction y Distance in y-direction z Distance in z-direction ζ Damping ratio X Indices Symbol Description 0 Undamped A Amplitude B Buoyancy b Bucket crit Critical D Drag d Displaced FK Froude-Krylov G Gravitational H2O Water I Inertial l Linear M Added mass m Model p Pontoon/Pressure/Prototype res Resulting S Spring s Structural t Tower V Viscous XI 1 Introduction In view of the limited availability of fossil fuels and the knowledge about anthro- pogenic climate change, it is a common goal of mankind to reduce the emission of greenhouse gases to the atmosphere.
Details
-
File Typepdf
-
Upload Time-
-
Content LanguagesEnglish
-
Upload UserAnonymous/Not logged-in
-
File Pages89 Page
-
File Size-