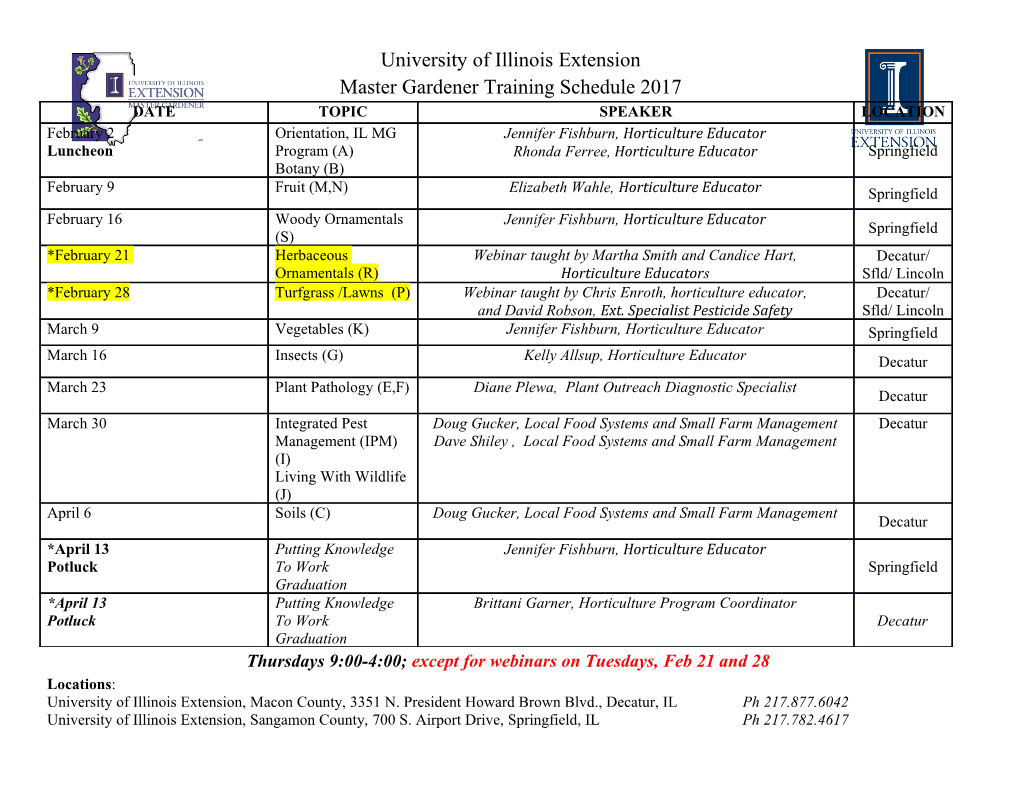
(19) TZZ ¥_T (11) EP 2 957 583 A1 (12) EUROPEAN PATENT APPLICATION (43) Date of publication: (51) Int Cl.: 23.12.2015 Bulletin 2015/52 C08G 18/48 (2006.01) C08J 11/10 (2006.01) C08J 11/12 (2006.01) C08G 65/34 (2006.01) (2006.01) (21) Application number: 14460111.9 C08G 18/36 (22) Date of filing: 16.12.2014 (84) Designated Contracting States: (72) Inventors: AL AT BE BG CH CY CZ DE DK EE ES FI FR GB • Haponiuk, Józef T. GR HR HU IE IS IT LI LT LU LV MC MK MT NL NO 80-344 Gdansk (PL) PL PT RO RS SE SI SK SM TR • Piszczyk, Lukasz Designated Extension States: 80-107 Gdansk (PL) BA ME • Danowska, Magdalena 80-266 Gdansk (PL) (30) Priority: 18.06.2014 PL 40861014 • Strankowsku, Michal 80-177 Gdansk (PL) (71) Applicant: Novapur Sp. z o.o. 80-233 Gdansk (PL) (54) Method of obtaining environment-friendly polyols from waste left after transesterification of plant oils, and method of obtaining rigid polyurethane foams (57) Method of obtaining environment-friendly poly- phuric acid pH 4.5 to 9, preferably from 6.5 to 7.5. Next, ols from waste left after transesterification of plant oils is the reaction mixture is heated under reduced pressure characterized in that the said waste is heated to a tem- to a temperature between 100 and 120°C until water perature in the range between 160 and 240°C, preferably stops to appear. Polyols are also produced from polyg- between 175 and 185°C, under reduced pressure in or- lycols extended with fatty acids and modified fatty acids. der to distill the volatile fraction. The distillation proc eeds The object of the invention is also the method of ob- until no more condensate appears, and the resultant taining polyurethane foams by using polyols that had product has a hydroxyl number between 400 and 1200 been obtained by the method according to the invention. mg KOH/g. Then the mixture is cooled below 100°C, and The foams additionally contain substances which retard acidified with a protonic acid, more preferably with sul- their flammability. EP 2 957 583 A1 Printed by Jouve, 75001 PARIS (FR) 1 EP 2 957 583 A1 2 Description not be completely dehydrated and removed. Moreover, these salts may act as catalysts therefore waste glycerol [0001] The object of the invention is the method of ob- is much cheaper than pure glycerol. taining ecological polyols from natural raw materials and [0006] It is well known that dehydration of glycerin at waste as well as the method of obtaining environment- 5 a temperature above 250°C results in obtaining polyg- friendly rigid polyurethane foams with reduced flamma- lycerins with molecular weights between 1 000 and 30 bility that are based on those polyols to be used in con- 000 which are solid at room temperature. Polyglycerins struction and automotive industries. can be used in the production of polyurethanes however [0002] Polyurethanes are polymers consisting of rigid they do not mix with isocyanates due to high viscosity, and flexible segments. The flexible segments originate 10 hydrophilicity and the large number of hydroxyl groups from hydroxyl-terminated oligomers among which oligo- per molecule. oxypropylenols are the most important compounds ob- [0007] Method of obtaining environment-friendly poly- tained via polymerization of propylene oxide with polyols ols from waste left after transesterification of plant oils is in the presence of KOH as a catalyst. In order to produce characterized, according to the invention, in that the polyurethanes, oligomerols containing from 2 to 8 hy- 15 aforementioned waste is heated to a temperature be- droxyl groups per molecule are used; their molecular tween 160 and 240°C, more preferably under reduced weights range from 600 to 10 000 (Wirpsza, Poliuretany pressure in the temperature range from 175 to 185°C, in - chemia, technologia i stosowanie, 1990). order to distill the volatile phase. The distillation proceeds [0003] In recent years, the increased interest of indus- until no more condensate appears, and the resultant try in polyols from renewable resources has been noted, 20 product has a hydroxyl number between 400 and 1200 polyols being one of the two basic components used in mg KOH/g. Next, the product is cooled down below the synthesis of polyurethane materials. Those renewa- 100°C, acidified with protonic acid, more preferably with ble polyols are "Natural Oil Polyols" (NOPs) which are sulphuric acid pH 4.5 to 9, preferably from 6.5 to 7.5. esters of glycerol and higher unsaturated fatty acids. The Then the reaction mixture is heated under reduced pres- most commonly used oils in polyols production are a) 25 sure to a temperature between 100 and 120°C until water rapeseed oil and sunflower oil In Europe, b) plam oil and stops to appear. coconut oil in Asia, and c) soybean oil in the USA. A [0008] Method of obtaining environment-friendly rigid worldwide interest in obtaining polyols from renewable polyurethane foam In the reaction of polyol premix with raw materials is a result of ever increasing prices of gas isocyanate agent is characterized according to the inven- and oil. In Poland, rapeseed oil is most commonly used 30 tion by the use of polyol premix which contains environ- for producing polyols. Rapeseed oil is a triglyceride of ment-friendly polyol produced from waste left after trans- unsaturated higher fatty acids which contains, on aver- esterification of plant oils. The waste is heated to a tem- age, 61% of acid radicals of oleic acid, 21% of acid rad- perature ranging from 160 to 240°C, more preferably icals of linoleic acid, 10% of linolenic radicals and 8% of from 175 to 185°C under reduced pressure, in order to acid radicals originating from higher saturated fatty acids. 35 distill the volatile phase. The distillation proceeds until no The derivatives of rapeseed oil can be used as reactive more condensate appears, and the resultant product has components in the production of polyesters, polyamides a hydroxyl number between 400 and 1200 mg KOH/g. and polyurethanes. Next, the product is cooled down below 100°C, acidified [0004] Methods of obtaining plant polyols are known. with protonic acid, more preferably with sulphuric acid One of the methods is a two-step procedure. In the first 40 pH 4.5 to 9, preferably from 6.5 to 7.5. Then the reaction step, unsaturated fatty acids are subjected to oxidation mixture is heated under reduced pressure to a temper- in order to obtain epoxy derivatives followed by the ring- ature between 100 and 120°C until water stops to appear. opening of epoxides in reaction with hydrogen donors A known isocyanate agent is added in the amount cor- which leads to the creation of hydroxyl groups. Epoxida- responding to the value of IC index between 0.5 to 4.0. tion of plant oils can also be conducted in situ by using 45 [0009] Preferably the flame retardants are added in the acetic acid and hydrogen peroxide or other oxidizing amount ranging from 0.01 to 40 parts by weight of the agents. By modifying plant oils, polyols with hydroxyl foam mass. numbers ranging from couple tens to over 400 mg KOH/g [0010] Preferably phyllosilicate nanofillers are used as and viscosity of couple hundred to over 10 000 mPas flammability-reducing compounds, preferably nanosili- can be obtained. 50 cates, bentonites, smectites, halosites, montmorillonites [0005] In the process of converting plant oils to mo- and/or their modified forms, preferably organophilic mod- noesters of fatty acids, a waste (glycerol phase) is pro- ified with cations of organic salts and/or acid-activated duced which consists of glycerol, water, salts of fatty ac- and/or substituted with transition-metal ions. ids, inorganic salts, an excess of base used to neutralize [0011] Preferably silsesquioxanes are used as nano- the reaction mixture, and remnants of methanol or etha- 55 fillers. nol from transesterification of oils. Glycerol present in the [0012] Preferably the following halogen-free flame re- waste from biodiesel production is difficult to remove tardants are applied: compounds based on phosphate mainly due to the presence of hydrophilic salts that can- esters, ammonium polyphosphate, phosphites, organo- 2 3 EP 2 957 583 A1 4 phosphates, metal phosphates, red phosphorus, phos- tween 0.5 and 4.0. phorus-basedderivatives of melaminesuch as melamine [0016] Preferably flame retardants are added in the phosphate, melamine pyrophosphate, and other prod- amount ranging from 0.01 to 40 parts by weight relative ucts containing nitrogen and phosphorus derivatives, bo- to the foam mass. ron compounds, preferably zinc borate, melamine bo- 5 [0017] Preferably phyllosilicate nanofillers are used as rates and other boric acid-based derivatives, metal hy- flame retardants, preferably nanosilicates, bentonites, droxides, preferably aluminum hydroxides and magne- smectites, halosites, montmorillonites and/or their mod- sium hydroxides, mineral fillers and additives such as ified forms, preferably organophilic modified with cations ammonium salts, molybdenum derivatives and magne- of organic salts and/or acid-activated and/or substituted sium heptahydrate sulfate, melamine and its derivatives, 10 with transition-metal ions. and expanded graphite. [0018] Preferably silsesquioxanes are used as nano- [0013] Preferably the nanofiller-antipyrene systems fillers. with 0.01 - 20 wt.% of nanofiller and 1 - 40 wt.% of anti- [0019] Preferably halogen-free compounds are used pyrene are used as flame retardants. as flame retardants, i.e. compounds based on phosphate [0014] Another invention is the method of obtaining en- 15 esters, ammonium polyphosphate, phosphites, organo- vironment-friendly polyols from waste left after transes- phosphates, metal phosphates, red phosphorus, phos- terification of plant oils.
Details
-
File Typepdf
-
Upload Time-
-
Content LanguagesEnglish
-
Upload UserAnonymous/Not logged-in
-
File Pages13 Page
-
File Size-