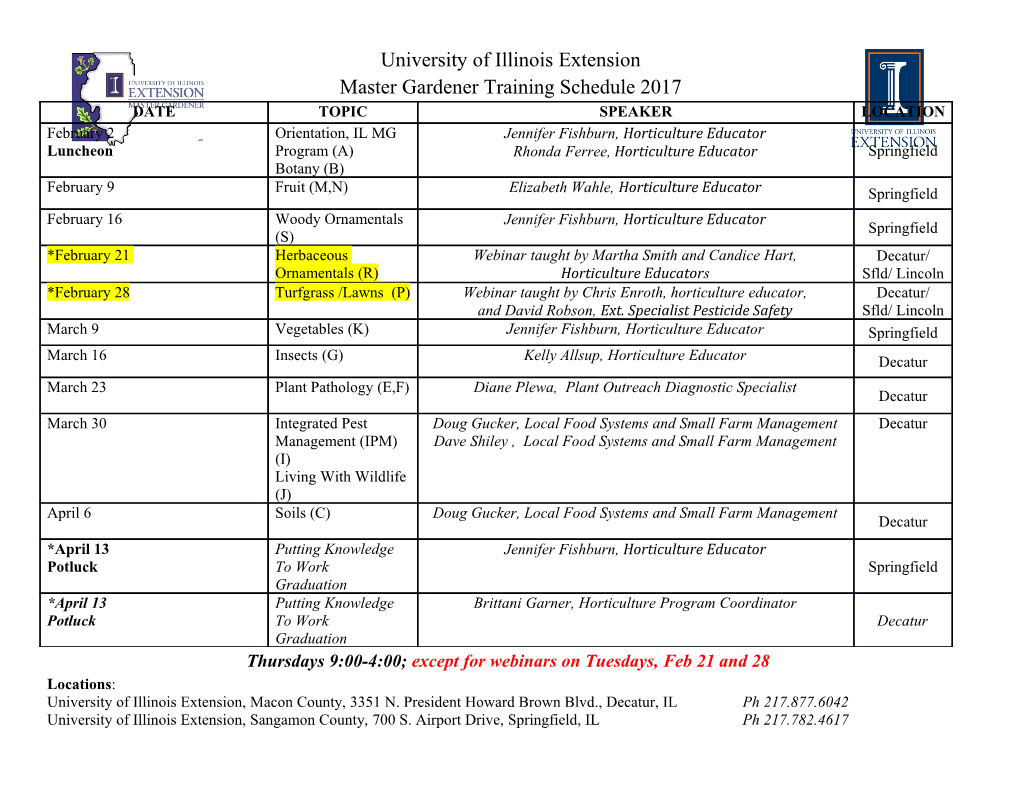
October 1946 October 1, 1946 MONTHLY BUSINESS REVIEW 3 GRAY IRON FOUNDRIES The ability of American industry to produce ade­ million or 26 percent of the national total. quate quantities of motor vehicles, farm machinery, The gray iron and semi-steel casting manufacturers railroad equipment, household appliances, plumbing produced about six million tons of castings in 1939. fixtures, furnaces, stoves, industrial machinery, and a Of this total, Ohio and Pennsylvania accounted for host of other essential commodities depends to a large 28.5 percent. About one-third of all castings were degree upon the supply of castings from the gray iron consumed in the producing plants and this proportion casting industry. It is currently estimated that over may be taken as a measure of the importance of 500 industries and branches of agriculture use gray “captive” foundries to the whole industry. iron castings, either in their product or as an integral part of their productive equipment. History The first iron works in the United States It is probably inaccurate to refer to the collection of any historical importance was built in of manufacturers that produce an infinite variety of 1643 at Lynn, Massachusetts and consisted of a cast iron products as an industry, since wide differ­ furnace, forge, and slitting mill. It produced kettles, ences exist in the character of their operations. A pots and other hollow ware cast directly from the part of the industry is “captive” and part of it is furnaces as was then the English custom. Iron was “jobbing.” The former represents shops operated by also run into sows, or pigs, which were later heated manufacturers of motor vehicles or stoves, for example, and hammered into wrought bars. Pigs were also that produce castings for their own use and incorporate exported to England. them in finished products. The facility may occupy a corner of the manufacturing establishment and be Foundries, trip hammer forges, furnaces, and slitting treated as a department or it may be a separate com­ mills soon sprang up in considerable number in the pany or subsidiary created to handle this phase of the colonies, and after the Revolution, multiplied with general operations. The output of the “captive” great rapidity. The early foundries did custom work foundry may be 'consumed entirely by the manufac­ for other manufacturers but produced chiefly cooking turer owning it and the rate of operation geared to utensils, domestic articles, sugar and potash kettles. established needs. Other “captive” foundries produce By about 1805, the domestic demand for hollow ware for the open market on a contract basis when excess was completely met by United States production, and capacity is avilable. the industry was approaching an era of great ex­ “Jobbing” foundries, on the other hand, are pansion due to the part it would play in the manu­ separate companies which produce castings for buyers facture of steam engines. Before long, most foundries on a contract basis. However, this type of foundry for heavy castings were connected with engine works. exists in many different forms. Some are known as Specialization increased and foundries exclusively “production” shops. That is, output is limited to a produced stove plates, plow iron, etc. few items for a small number of customers, but on a The first iron foundry west of the Alleghenies was large tonnage and long term basis. Other shops erected in Pittsburgh in 1804 and an engine works produce a wide variety of castings for many customers started two years later. The census of 1820 found and for relatively small orders. In nearly all cases, engine builders in Pittsburgh, Steubenville, and Cin­ there is a high degree of specialization. Foundries may cinnati. During the next decade, at least six foundries become attached to the machine tool trade, automotive in Pittsburgh were making 20-30 steam engines industry, railroad, farm equipment, steel industry, annually. Castings up to four tons in weight were etc., and tend to be identified with a particular industry poured in Pittsburgh in 1828, and a few years later rather than with the gray iron foundry industry as in Wheeling, shafts and bed-plates for engines were such. cast weighting up to 30-40 tons. Differences as to the amount of work performed The first iron furnace in Ohio was completed in 1804 on the castings as between shops should also be noted. and was located on Yellow Creek a short distance Some merely pour the castings and ship them after above its junction with the Mahoning River. Two they have been cleaned, chipped and rough ground. years later another furnace was built nearby on the Other foundries have quite elaborate machine shops present site of the city of Struthers. This furnace in which the castings may be ground, milled, drilled, yielded about two and one-half tons of metal a day or shaped to the required finished dimensions. which was run into molds for bake-ovens, kettles, According to the Census of Manufactures, 1235 stoves, flat irons, andirons and other items needed by establishments were engaged in the production of gray a frontier society. Surplus iron was made into pigs iron and semi-steel castings, and cast iron pipe and and exported to the Pittsburgh market. fittings in the United States and employed 75,000 The Hanging Rock region, which includes Greenup, wage earners in 1939. The total value of product was Boyd, Carter, and Lawrence counties in Kentucky, $275 million out of which wage earners received $88 and Lawrence, Jackson, Gallia, and Vinton counties million. In addition, about $113 million of gray iron as well as part of Scioto county in Ohio, was an early and semi-steel castings were made as secondary famous iron producing area dating from about 1820. products in other industries. Ohio and Pennsylvania The first foundry in Portsmouth was completed in together had 256 establishments with 17,500 wage 1830. It produced the castings used in the rolling earners whose value of product amounted to $70.5 mill that was built there in 1832. Digitized for FRASER http://fraser.stlouisfed.org/ Federal Reserve Bank of St. Louis October 1946 4 MONTHLY BUSINESS REVIEW October 1, 1946 The beginning of iron industries in the counties Molding machines were used in 1892; tumbling barrels along Lake Erie probably began about 1825. Bog and sand blast machines were advertised in 1893; iron, which was found in swales and swamps along mechanical sand mixers, temperers, sand conveyors, the ridge marking an ancient shore of the lake, was pneumatic hammers, and chippers were also avaiable. used. Lack of wood for charcoal had all but stopped production in this area by the middle of the century. Ohio Ranks According to 1939 Census data Ohio First was the leading state in the manufac­ Conversion from The Mahoning Valley began to ture of gray iron castings. It ranked Charcoal to assume importance when raw coal first by a wide margin in the number of establishments, Raw Coal was used successfully as a blast number of wage earners, and value of product. Al­ furnace fuel at Lowell in 1846 and though Pennsylvania had the second largest number charcoal furnaces were converted rapidly to this fuel. of establishments it was outranked by Michigan and The iron industry in Youngstown dates from about Illinois in the value of product and number of wage 1835. earners. Alabama produced nearly 50 percent of all cast iron pipe and fittings and was the home of one- The manufacture of iron stoves and furnaces, after third of the manufacturers of these items. In terms their adaptation to coal, became a rapidly expanding of value of product, Pennsylvania ranked as the third iron founding business between 1830-1860. Cincinnati largest pipe producing state (with an output one- and Pittsburgh became important centers for their seventh that of Alabama) and Ohio was a close fourth. manufacture and in 1850, foundries in these towns The following table illustrates the importance of these produced about 70,000 stoves used for both cooking industries in the Fourth District. Data for West and heating. These two cities also became large Virginia are not available, and Kentucky which had producers of hollow cast iron wheels for the spreading only nine foundries with a value of product of less railroad network. than a million dollars is not show separately. In addition to iron ware made since the beginning of the industry in this country, new products were developed. At the time of the Civil War such items as Recent Data on the Gray Iron and Semi-Steel bath tubs, builders’ hardware, cast iron railings, Castings Industry fountains, and lawn ornaments were turned out. United States Ohio Pennsylvania Growth of cities and development of water and gas Number of establishments.......... 1,161 122 119 works led to a demand for cast iron pipes, hydrants, Average number of wage earners 58,428 10,697 4,837 and lamp posts. Foundries were also producing many Manufacturing wages.................. $ 70,750,000 $14,350,000 $ 5,500,000 of the components of a lusty engine-manufacturing Value of product.......................... $209,800,000 $43,500,000 $19,500,000 business since most large and small parts were made Value added by manufacture___ $130,750,000 $26,600,000 $10,500,000 of cast iron as metal finishing tools had not as yet been extensively developed. Cannon, press screws, and rolls for sugar and iron works were important Cast Iron Pipe and Fittings products. United States Ohio Pennsylvania Number of establishments.......... 74 5 10 Better foundry irons also were developed. During Average number of wage earners. 16,488 652 1,334 the 1870’s there was a strong prejudice in favor of Manufacturing wages.................
Details
-
File Typepdf
-
Upload Time-
-
Content LanguagesEnglish
-
Upload UserAnonymous/Not logged-in
-
File Pages6 Page
-
File Size-