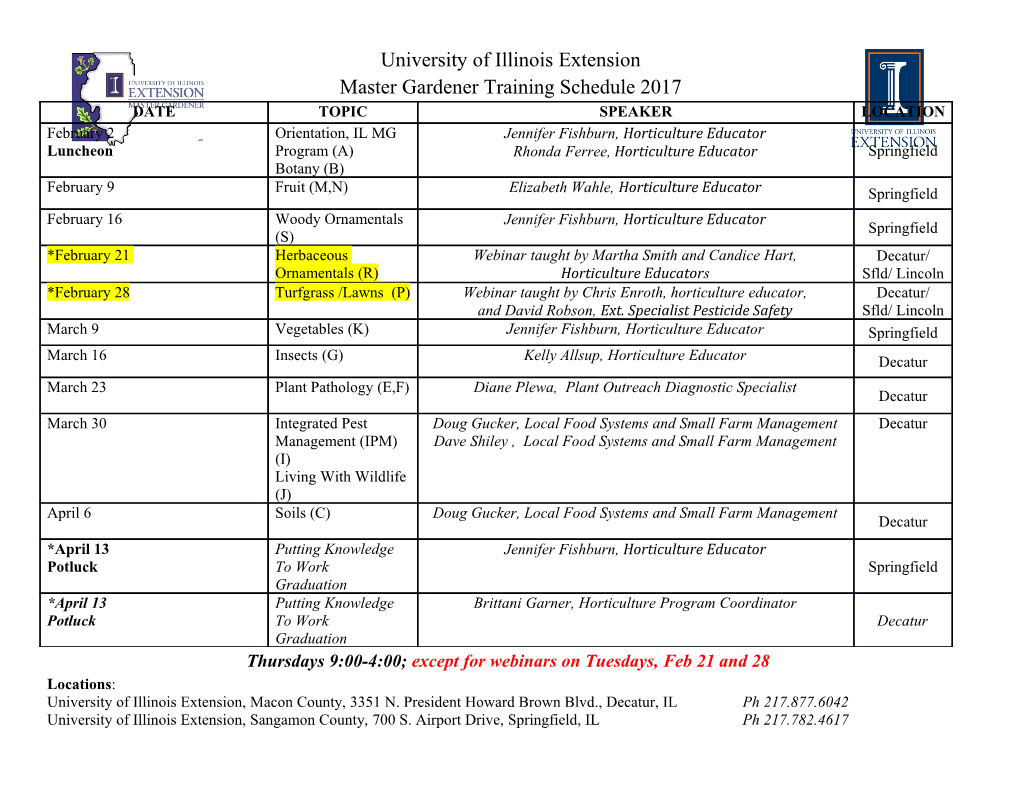
Journey on the Waveform By Joshua France, Riegl USA (www.rieglusa.com), Orlando, Fla., and A step-by-step description Craig Glennie, University of Houston (www.uh.edu), Texas. of a mobile mapping he following project was motivated by a highway paving company’s need for better data so it could manage its costs and bidding approach more effectively to generate a better project reveals the return on investment. The information needed was the tricks of the trade. as-built slope of an existing road deck. TTraditional surveying methods would’ve taken about a week, while exposing survey crews to traffic and dangerous conditions. The same survey collected with mobile scanning equipment took Riegl USA Riegl less than two hours and provided more information than a survey crew could collect in a month. More importantly, no one was exposed to potentially hazardous working conditions. Project Specifics Hardware consisted of two Riegl VQ-250 2-D laser scanners, an inertial navigation system (INS)/global navigation satellite system (GNSS) receiver and an on-board computer in a portable case. The INS-GNSS unit comprised the electronics for real-time kinematic (RTK) satellite navigation and three sensors: the INS sensor; the GNSS receiver sensor, including antenna; and a wheel sensor, or distance measuring indicator (DMI). The laser scanners and the INS-GNSS unit were attached to a stable mounting platform that can be mounted on any vehicle. A single cable connected the measuring head to the control unit box, which was housed in a case and contained the power supply; a com- puter running Riegl’s RiACQUIRE software package for data acquisi- tion; removable hard drives; and a handy touch screen, providing a convenient control interface for the operator. The area to be scanned was a nine-mile, two-lane section of Interstate 95 in Florida, beginning at mile marker 149 and finish- ing at mile marker 139, with a single base station located near The acquisition vehicle (inset) traveled a nine-mile, two-lane section of Interstate 95 near Vero Beach, Fla. The collection route is shown in purple. A plot shows the PDOP during the collection window. 28 JULY/AUGUST 2011 © 2011 Earthwide Communications LLC, www.eijournal.com Riegl USA Riegl mile marker 145. The northbound and p.m., the planned time window for the southbound lanes were collected twice to data acquisition. ensure no vehicle blocked any section of the road’s surface during data collection. Data Collection Details Only one overpass obstructed the clear- A quick hour drive from Riegl’s sky view of the GNSS receiver during data Orlando, Fla., office brought us to the collection. Vero Beach area, where we stopped to set up the mobile mapping system by attach- Mission Planning ing the DMI to the driver’s side rear wheel First, GNSS satellite coverage was and carefully attaching the camera system evaluated by examining the positional di- and laser scanner measurement head to lution of precision (PDOP), which is a cal- the pre-installed roof rack. culation of the strength from the predicted Now it was time to collect the data, so GNSS satellite constellation at the time we began our final checklist. All collec- and location of data acquisition. A PDOP tions begin after a 5-minute static waiting The camera system and laser scanner measurement head number works like a golf score—the period for the INS-GPS solution to achieve was carefully secured to the pre-installed roof rack of the acquisition vehicle (inset). Upon arrival at the starting mile marker, we to clear to give us an unobstructed view switch the scanner’s mode from on to logging, of the fast lane and shoulder from our and a 2-D point cloud swath is traced on the steady pace in the slow lane. The two laser scanners are enabled to ensure everything screen as we head south. is communicating as expected. Now we’re taking light detection and ranging (LiDAR) lower the number, the better the expected a good initial location. The higher the measurements at a rate of 600,000 per quality of the positioning data the GNSS accuracy of the initial position, the better second. receiver will collect. Typically, a PDOP of the Kalman filter can estimate IMU biases As we watch our path on the RiAC- three or less is ideal. This measurement is to create an accurate kinematic model of QUIRE screen, we can also see returns performed only with Global Positioning the trajectory, correct the GNSS position from each laser scanner. The quality of the System (GPS) satellites, because the best estimates and fill in gaps created by out- trajectory data is also being monitored in trajectory solutions only use GPS position- ages. System initialization can be checked real time. Upon arrival at the starting mile ing information to calculate the output of off the list. marker, we switch the scanner’s mode this process—the smoothed best estimate The IMU sensor’s alignment takes a from on to logging, and a 2-D point cloud of trajectory (SBET). few well-executed maneuvers to bring swath is traced on the screen as we head The second consideration was the the heading, roll and pitch estimated so- south. amount of traffic on the road. In this lution errors within five hundredths of a Driving at near the posted speed limit case, the surveyed section project area is degree. The best way to accomplish this to keep up with traffic and avoid areas of a commuting route for the Fort Lau- is to spin the vehicle around, with rapid missing data because of passing vehicle derdale and Jupiter areas. Therefore, an heading and rotation changes to excite obstructions, we soon reach the first acquisition window was set from 11 a.m. the three gyros and accelerometers in- control maker. The markers are set at to 12:30 p.m. to avoid the high traffic side the IMU—basically driving a figure- 1,500 U.S. survey feet intervals, with the volume of morning and evening rush eight pattern. Now IMU alignment can exception of two control points set right hours. Having the road clear of car noise be checked off the list, and the system is after the overpass. As we continue our col- is important when the road’s slope is ready to begin data collection. lection, we pass the survey crew collecting measured, because missing data makes Merging into traffic, southbound on some validation points we’ll use to further the process more difficult. The figure at I-95 toward Miami, we have two miles be- confirm data accuracy and quality. left shows the PDOP in green. Note it’s fore the collection area begins. We watch Traditional surveying ground control less than three between 11 a.m. and 12:40 the mile markers pass, waiting for traffic is needed to assess the quality of the data © 2011 Earthwide Communications LLC, www.eijournal.com JULY/AUGUST 2011 29 collected. To effectively check the mobile Upon completing the second northbound pass, LiDAR data, several considerations need to be accounted for unless specific control we were confident the processed data would requirements are in place by an agency or client. In this case, our own control provide complete road surface information for requirements could be used. the project site. The typical pattern is every 1,500 to 2,000 U.S. survey feet for a control point as overhanging vegetation, a tunnel or from the first pass. Upon completing the unless an obstruction is in the path. In the an overpass—a control point is placed second northbound pass, we were con- case of a line-of-sight obstruction—such afterward to check how well the trajec- fident the processed data would provide tory solution was processed after a loss of complete road surface information for the satellite lock. project site. Riegl USA Riegl As shown in the image at left, the After acquisition, we returned to our shape of the target used for both control starting system initialization location for and validation points is a chevron to help another 5 minutes of static data to achieve the processor determine the horizontal a good final fixed location to complete the accuracy. The recorded survey control data collection. The overall collection point is at the tip of the chevron. White time was one hour and thirty minutes. asphalt tape is used to mark the targets, Following the mission, the scanner, which show up clearly in the LiDAR data DMI and camera system were removed because of the tape’s high reflectivity. from the roof and placed inside the car. At the end of the first pass, we had With the scanner safely inside the vehicle, collected 10 separate records—one for we headed home, knowing the data we each mile driven—and roughly 1.8GB of collected met the mission’s objectives. data. A second pass was needed because The only question left unanswered is how of several gaps in the road surface cover- well it will compare with the survey vali- The target used for control and validation points was age from car noise. A little luck and some dation points. In the next issue of Earth shaped like a chevron to help the processor determine good driving allowed for the second pass Imaging Journal, we’ll take you inside the the horizontal accuracy. in both directions to remove all data gaps processing portion of our mission. Don’tDon’t MissMiss anan Issue!Issue! Subscribe to Earth Imaging Journal FREE! www.eijournal.comwww.eijournal.com Also check out Earth Imaging Journal's online resources! • Intriguing Image of the Day • Comprehensive Articles • Industry Insights & Trends • International Industry Directory • Events Calendar Earth Imaging Journal is available free to those who live in the continental United States.
Details
-
File Typepdf
-
Upload Time-
-
Content LanguagesEnglish
-
Upload UserAnonymous/Not logged-in
-
File Pages3 Page
-
File Size-