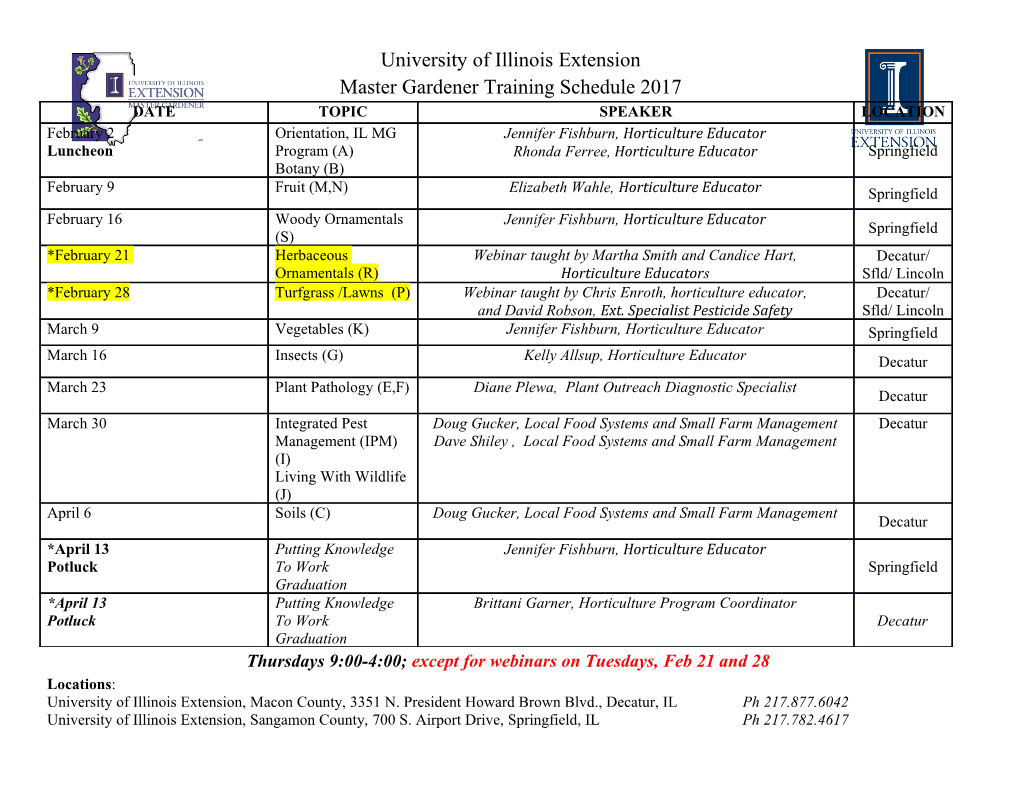
® 2016 a *+ *6 */01- . - / w"#$ - 9 COMPLEX METHODOLOGY OF POKA-YOKE IMPLEMENTATION IN CONDITIONS OF WELDED STEEL TUBES PRODUCTION NOSKIEVI OVÁ Darja, SKOUMALOVÁ Monika VSB - Technical University of Ostrava, Faculty of Metallurgy and Material Engineering, Ostrava, Czech Republic, EU, [email protected] Abstract Poka-yoke (mistake-proofing) is one of the lean manufacturing methods. It ensures that proper conditions exist before actually executing a process step, preventing mistakes from occurring in the first place. Where this is not possible, poka-yoke has a detective function, eliminating defects in the process as early as possible. The application of simple poka-yoke methods in product and process design can eliminate both mechanical and human errors. Modern production systems are based on principles and instruments of the lean, agile and resilient approaches to manufacturing. For these conditions the poka-yoke system preventing errors is the most desirable. This paper deals with design of the complex methodology for poka-yoke implementation for such manufacturing. The methodology is based on the following principles: 1. principle of prevention; understanding poka-yoke as a change and innovation; implementation of poka-yoke as a change and innovation management. In the paper there are described particular steps of the designed methodology: 1. identification of all potential risks; 2. giving reasons for suitability of the poka-yoke implementation; 3. selection of the poka-yoke type; 4. design verification and its realization; 5. description and documentation. In the last part of the paper two cases of implementation of the designed methodology in conditions of the production of welded steel tubes are described: poka-yoke preventing usage of the non-correct rollers and poka-yoke preventing undesirable interchangeability and loss of the production dispatch notes. Keywords: Lean approach, agile manufacturing, resilience, poka-yoke 1. INTRODUCTION Modern production systems are based on principles and instruments of the lean, agile and resilient approaches to manufacturing. The lean approach is widely considered to be the next big step in the evolution of manufacturing beyond Ford’s mass production. It can be described as a strategy based on cost reduction and flexibility, focused on the process improvements via systematic identification and reduction of all ”wastes“ (non-value adding operations (muda), results of unevenness in workloads (mura), and results of overloading (muri)) in order to create value for the customer . It can be said that lean manufacturing is all about minimizing costs. It also focuses on the organization´s core competencies whereas outsourcing many other productive activities. Lean production is not just a technological system but also a concept implemented through the whole company, which especially requires consensus on corporate culture [1]. The lean approach performs better in conditions where there is a higher volume, low variety, and predicable demand with certain supplies. Agile manufacturing is often viewed as the next step after lean in the evolution of the production methodologies. One of the former definitions of agile manufacturing states that it is “the ability of an enterprise to survive in a competitive environment with continuous and unanticipated change and to respond quickly to rapidly changing markets that are driven by the customer valuing the products and services” [2]. Agile manufacturing is especially oriented to low volume/high mix production adding responsiveness (velocity) and flexibility to the manufacturing process. It is the most effective in conditions where customized configurable or specialized orders offer a competitive advantage. 1631 ® 2016 a *+ *6 */01- . - / w"#$ - 9 Agility development in organization requires dynamic and truly integrated management systems that are able to support a continuous change, and hence agile manufacturing cannot effectively operate without an optimal supply chain. Agile manufacturing will be really effective when there is a potential market for a personalized fast-delivery version of one of the current products; there is a new product that can be developed within the company’s sphere of competence (or alternately co-developed with a partner) that would strongly benefit from personalization and fast delivery. Resilience is the ability of a system to return to its original state or move to a new desirable state after being disturbed . In fact, agile principles should be seen as a natural extension and evolution of the lean principles. Katayama and Bennet [3] say that lean, flexible and agile production systems considerably overlap (increased product variety and lower fixed costs for the new product development and grouping parts into families in order to decrease setup times and WIP inventory). Flexible manufacturing, agility and leanness are considered as mutually supporting concepts. Poka-yoke (mistake-proofing) is one of the lean manufacturing methods. It ensures that the proper conditions exist before actually executing a process step, preventing mistakes from occurring in the first place. Where this is not possible, poka-yoke has a detective function, eliminating defects in the process as early as possible (see Figure 1 ). The application of simple poka-yoke methods in product and process design can eliminate both mechanical and human errors. Figure 1 Principle of poka-yoke [4] For the conditions of the modern combined manufacturing system based on the synergic effect of the lean, agile and resilient approaches the poka-Yoke system preventing mistakes is the only acceptable form. This paper deals with design of the complex methodology for poka-yoke implementation in the manufacturing conditions combining approaches mentioned above. The methodology is based on the following principles: 1. principle of planning and prevention; 2. understanding poka-yoke as a change and innovation; 3. deployment of poka-yoke as a change and innovation management. 1632 ® 2016 a *+ *6 */01- . - / w"#$ - 9 In the paper there are described particular steps of the designed methodology: 1. identification of all potential risks; 2. giving reasons for suitability of the poka-yoke implementation; 3. selection of the poka-yoke type; 4. design verification and its realization; 5. description and documentation. In the last part of the paper two cases of application of poka-yoke on the welded steel tubes production are described: poka-yoke preventing usage of the non-correct rollers and poka-yoke preventing undesirable interchangeability and loss of the production dispatch notes. 2. DESIGN OF COMPLEX METHODOLOGY OF POKA-YOKE IMPLEMENTATION FOR METALLURGY The design of the methodology of poka-yoke implementation is based on three principles (see subchapter 2.1) and consists of 5 steps (see subchapter 2.2). 2.1 Principles of the designed complex methodology of the poka-yoke implementation The designed methodology is based on the following principles: 1. principle of planning and prevention; 2. understanding poka-yoke as a change and innovation; 3. deployment of poka-yoke as a change and innovation management. For the conditions of the modern manufacturing system based on the synergic effect of the lean, agile and resilient approaches the poka-yoke system preventing mistakes identified in the phase of the planning the production process is the only acceptable form (see Figure 2 ). Very suitable method for realization of principle 1 is the modified FMEA (see chapter 3). Figure 2 Principle of poka-yoke suitable for the modern combined manufacturing systems (own source) Poka-yoke could be considered an operating change in processes, technology and projects [5] as it is some mechanism or equipment that enables to prevent workers or production equipment doing mistakes (principle 2). Management of this change represents a set of actions and processes that enable smooth change in system incorporating technology and people (principle 3). Poka-yoke as a change must be considered to be a process innovation. 2.2 Steps of the Complex Methodology of Poka-Yoke Implementation In this subchapter there are described particular steps of the designed methodology: 1. identification of all potential risks; 2. giving reasons for suitability of the poka-yoke implementation; 3. selection of the poka-yoke type; 4. design verification and its realization; 5. description and documentation. 1633 ® 2016 a *+ *6 */01- . - / w"#$ - 9 Step 1 Identification of all potential risks The main goal of step 1 is definition of all potential mistakes that can be done in the planned process and their risks (negative effects) including also possibility to produce nonconformities. It can be realized through the realization of very simple well-known approach - brainstorming. But very effective method for this analysis is FMEA in the modified form which was designed in the frame of [5]. As compared to the conventional process FMEA the central object of the modified FMEA is not potential nonconformity (defect) but the potential mistake (error). The first step in the modified FMEA is defining all possible mistakes that can occur during the process steps. The next step is an analysis of the effect of these possible mistakes. After that the causes of the mistakes are defined and suitable poka-yoke or other mechanisms to prevent such mistakes are designed. The modified FMEA serves for the evaluation of severity (SM), occurrence (OM) and detectability (DM) of the mistakes. It is designed to use
Details
-
File Typepdf
-
Upload Time-
-
Content LanguagesEnglish
-
Upload UserAnonymous/Not logged-in
-
File Pages7 Page
-
File Size-