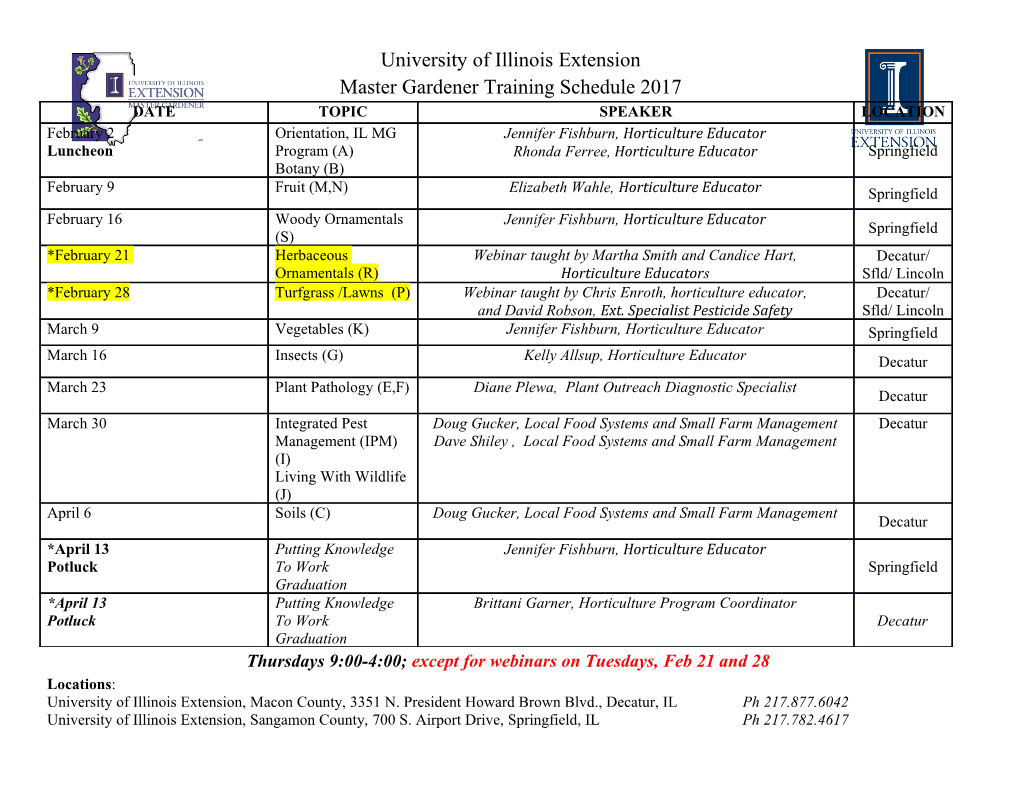
Article Research on Regenerative Braking of Pure Electric Mining Dump Truck Wei Zhang * , Jue Yang , Wenming Zhang and Fei Ma Department of Vehicle Engineering, School of Mechanical Engineering, Beijing University of Science and Technology, Beijing 100083, China; [email protected] (J.Y.); [email protected] (W.Z.); [email protected] (F.M.) * Correspondence: [email protected] Received: 10 May 2019; Accepted: 5 June 2019; Published: 8 June 2019 Abstract: When the pure electric mining dump truck is working, it mainly ascends the slope at full load and descends the slope at no load. The loading state of the vehicle and the slope of the road will directly affect its axle load distribution and braking force distribution. In this paper, the slope dynamics analysis of the pure electric double-axle four-wheel drive mining dump truck was carried out. Based on the regenerative braking priority strategy, four regenerative braking control methods were developed based on the Matlab/Simulink platform and ADVISOR 2002 vehicle simulation software to study the ability of regenerative braking energy recovery and its impact on vehicle economic performance. The simulation results show that the regenerative braking priority control strategy used can maximize the regenerative braking force of the vehicle; the regenerative energy recovery capability of pure electric mining dump truck is proportional to the regenerative braking force that can be provided during braking; the two-axis braking strategy based on the I curve and the β line can make full use of the front and rear axle regenerative braking force when the braking intensity is large, and recover more braking energy; under road drive cycle, the single-axis braking force required to the braking strategy based on the maximized front axle braking force is the largest among all strategies, the motor braking efficiency is the highest, and the recovered braking energy is the most. For the studied drive cycle, the regenerative braking technology can reduce the vehicle energy consumption by 1.06%–1.56%. If appropriate measures are taken to improve the road surface condition and reduce the rolling resistance coefficient from f = 0.04 to f = 0.02, the regenerative braking technology can further reduce the vehicle energy consumption to 4.76%–5.73%. The economic performance of the vehicle is improved compared to no regenerative braking. In addition, the vehicle loading state and the driving motor working efficiency also directly affect the regenerative braking energy recovery capability of the pure electric mining truck. Keywords: mining dump truck; pure electric vehicle; regenerative braking; control strategy 1. Introduction Pure electric mining dump truck (pure electric mining truck) is fully driven by electricity which is supplied by on-board batteries or power wiring. It does not need to burn diesel oil, and can recover regenerative braking energy when braking with high efficiency and no pollution. The traditional electric wheel mining dump truck adopts diesel-electric drive technology. When driving, the chemical energy is converted into mechanical energy by the diesel engine to drive the generator to generate electric energy to be transmitted to the motor to drive the wheels to rotate. When braking, the vehicle kinetic energy is transmitted from the wheel to the motor. The electric motor acts as a generator to convert the braking energy into electrical energy and then it is converted to heat by the braking resistor [1]. Regenerative braking is an important feature of pure electric mining trucks that distinguish World Electric Vehicle Journal 2019, 10, 39; doi:10.3390/wevj10020039 www.mdpi.com/journal/wevj World Electric Vehicle Journal 2019, 10, 39 2 of 17 trucksWorld Electricthat distinguish Vehicle Journal traditional2019, 10, 39 mining trucks. When braking, the drive motor is switched to2 the of 17 power generation state to generate the braking torque. The vehicle kinetic energy is recovered and storedtraditional in the mining vehicle trucks. energy When system, braking, which the has drive a significant motor is switchedeffect on toimproving the power the generation driving staterange to andgenerate economic the brakingperformance torque. of Thethe vehicle vehicle [2]. kinetic energy is recovered and stored in the vehicle energy system,There which are many has a studies significant on regenerative effect on improving braking theof pure driving electric range vehicles and economic [3–13], hybrid performance vehicles of [14,15],the vehicle electric [2]. buses [16,17] or electric light trucks [18]. However, there are few studies on regenerativeThere arebraking many of studiespure electric on regenerative mining dump braking trucks. ofThe pure existing electric literatures vehicles basically [3–13], take hybrid a single-axisvehicles [14 driven,15], electric vehicle buses as the [ 16research,17] or object electric [3–10,14,15], light trucks and [18]. analyzes However, it based there on are the few horizontal studies on roadregenerative driving mechanics braking of model pure electric[3,5–7], miningignoring dump the vehicle trucks. wind The existingresistance, literatures rolling resistance basically take and a slopesingle-axis resistance driven during vehicle driving. as the researchThese resistance object [3–s,10 ,especially14,15], and the analyzes rolling it basedresistance on the and horizontal slope resistance,road driving are often mechanics not negligible model [3 for,5– 7large-load], ignoring mi thening vehicle dump wind trucks. resistance, In this paper, rolling a self-weight resistance and45 t slopewith full resistance load 100 during t pure driving. electric These double-axle resistances, four-wheel especially drive the rollingmining resistance dump truck and is slope taken resistance, as the researchare often object. not negligible Through for the large-load vehicle slope mining dynamics dump trucks. analysis, In this the paper, front aand self-weight rear axle 45 load t with and full brakingload 100 force t pure distribution electric double-axle models are four-wheel established. drive The mining regenerative dump truckbraking is taken priority as the control research strategy object. isThrough adopted the to vehicleestablish slope four dynamics regenerative analysis, braking the front strategies: and rear Based axle loadon vehicle and braking speed, force I-curve, distribution β-line andmodels front are axle established. braking force The regenerative maximization. braking The prioritycharacteristics control strategyof regenerative is adopted energy to establish recovery four storageregenerative control braking are studied strategies: on the Based Matlab/Simulink on vehicle speed, platformI-curve, combinedβ-line with and frontthe vehicle axle braking simulation force softwaremaximization. ADVISOR The 2002. characteristics of regenerative energy recovery storage control are studied on the Matlab/Simulink platform combined with the vehicle simulation software ADVISOR 2002. 2. Principle Analysis of Regenerative Braking Control System 2. Principle Analysis of Regenerative Braking Control System In order to ensure the stability and safety of the brake, the pure electric mining truck brake controlIn system order tostudied ensure thein this stability paper and keeps safety th ofe mechanical the brake, thebrake pure system electric [19] mining and truckadds brakethe regenerativecontrol system brake studied system in this on paperthe front keeps and the rear mechanical axles, as brake shown system in Figure [19] and 1. During adds the braking, regenerative the brakebrake ECU system calculates on the the front braking and rearforce axles, demand as shown according in Figure to the1 brake. During pedal braking, signal and the transmits brake ECU it tocalculates the vehicle the brakingECU. The force vehicle demand ECU according performs to regenerative the brake pedal brake signal through and transmits the motor it to ECU, the vehicle and feedbacksECU. The the vehicle regenerative ECU performs braking regenerativeforce to the brake brake ECU. through The thebrake motor ECUECU, compares and feedbacksthe required the brakingregenerative force brakingwith the force regenerative to the brake braking ECU. force, The brake determines ECU compares the magnitude the required of the braking friction forcebraking with force,the regenerative and adjusts brakingthe hydraulic force, determinespressure to theachieve magnitude compound of the braking friction of braking regenerative force, and braking adjusts and the frictionhydraulic braking. pressure to achieve compound braking of regenerative braking and friction braking. Brake pedal Hydraulic Wheel speed sensor control unit Brake ECU Vehicle Transmission Transmission Motor ECU ECU Converter Motor Motor Battery Oil Current Signal Figure 1. Regenerative braking control system. 3. System Model and ControlFigure Strategy 1. Regenerative braking control system. 3.3.1. System Drive Model Motor, and Battery Control and Regenerative Strategy Braking Force Model 3.1. DriveThe Motor, drive motorBattery andand batteryRegenerative parameters Braking directlyForce Model determine the vehicle’s regenerative braking force and regenerative energy recovery and storage capacity [20]. The drive motor and battery parameters directly determine the vehicle's regenerative braking force and regenerative energy recovery and storage capacity [20]. World Electric Vehicle Journal 2019, 10, 39 3 of 17 World Electric Vehicle Journal 2019, 10, 39 3 of 17 3.1.1. Drive Motor Mechanics Model
Details
-
File Typepdf
-
Upload Time-
-
Content LanguagesEnglish
-
Upload UserAnonymous/Not logged-in
-
File Pages17 Page
-
File Size-