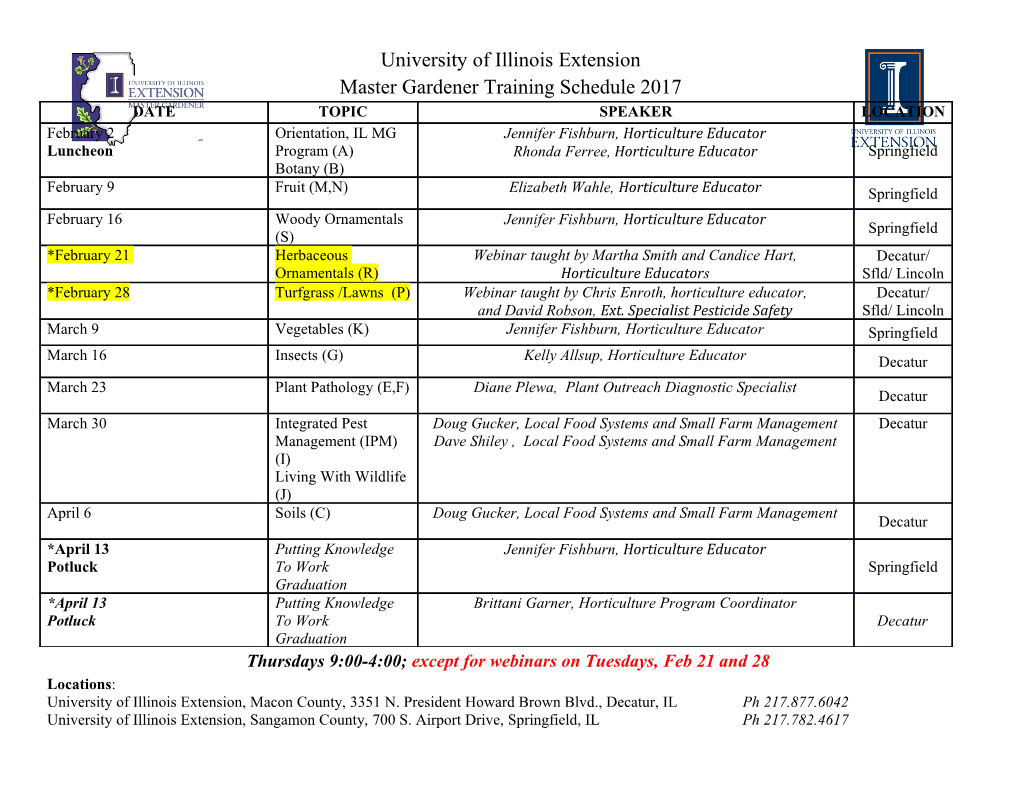
Complex Coolant Fluid for PEM Fuel Cell Systems Satish C. Mohapatra Advanced Fluid Technologies, Inc. dba Dynalene Heat Transfer Fluids 05-24-2005 Project ID # FCP 21 This presentation does not contain any proprietary or confidential information Overview Timeline Barriers For SBIR Phase I Project • Barriers addressed – Technical Barriers (stability of • Project start date: 07-14-2004 the coolant at high • Project end date: 04-13-2005 temperatures and over a • Percent complete: 100% period of time) – Cost Barriers (preliminary cost estimates) Budget • Total project funding – DOE share: $97,390 Partners – Contractor share: in-kind • Funding received in FY04: • Interactions/ $51,114.75 collaborations: • Funding received in FY05: Lehigh University $46,275.25 2 Objectives • Prove that we can fully develop and validate a fuel cell coolant based on glycol/water mixtures and an additive package (with nanoparticles) that will exhibit less than 2.0 µS/cm of electrical conductivity for more than 3000 hours in an actual PEM Fuel Cell System. • Demonstrate the potential for commercializing such a coolant at a price that is acceptable for a majority of fuel cell applications (i.e., < $8.0/gallon). 3 Key Technical and Economic Questions to be Answered • How is the electrical conductivity of the coolant related to the properties of the additives? • Will the additives influence the heat transfer and pressure drop characteristics of the coolant? • Is the coolant and its additives compatible with the fuel cell cooling system components? • What is the raw material and production cost for the proposed ‘Complex Coolant Fluid’? 4 Approach • The proposed Complex Coolant Fluid consists of a base compound (glycol/water mixtures) and an additive package. • The base compound mixture has a freezing point less than –40oC, is non-flammable, and can be used at temperatures up to 122oC. • The additive package consists of non-ionic corrosion inhibitors and ion-suppressing compounds (nanoparticles) to maintain the electrical conductivity of the coolant at a low level. 5 Technical Approach in Phase I • Development of the ion-suppressant (nanoparticles) – Effect of preparation recipe on the electrical conductivity of the final coolant formulation – Study dispersion behavior in the coolant • Building a dynamic test loop (4 L) – Short-term tests (electrical cond. Vs. time) 6 Dynamic Test Loop for Coolant Testing 6 +- 7 3 3 1: Coolant Reservoir 2: Pump 8 3: Piping 9 1 4: Temperature Controller 5: Heater 6: Electrodes 7: Head Electrodes 8: Probes for pH and cond. Air-cooled Coolant Radiator 9: Radiator Reservoir Heater 2 (total system volume: 4 L) 45 Temperature Pump Controller 7 Dynamic Test Loop for Coolant Testing 8 Results from Phase I 100 90 • Titration tests were 80 conducted with 0.01 70 molar NaCl solution. 60 50 • Electrical conductivity 40 increased with the addition 30 of NaCl solution for all 20 the formulations. 10 Electrical Conductivity (µS/cm) 0 0 5 10 15 20 25 30 35 40 45 50 55 60 65 • The coolant formulation 0.01 M NaCl (mL) with nanoparticles showed PG+DI Water+0.05% Nanoparticles (CATAN Mix # 2) much lower increase than PG+DI Water (without Nanoparticles) DI water or glycol/water. PG+DI Water+0.005%Nanoparticles (CATAN Mix#2) PG+DI Water+0.05% Dowex particles (10 microns) DI Water PG+DI Water+0.05% Nanoparticles (CATAN Mix#1) 9 Results from Phase I 80 70 60 S/cm) µ 50 Tested in the Dynamic 40 Test Loop (4 L volume) 30 At 55 oC. 20 Electrical Conductivity ( 10 0 0 5000 10000 15000 20000 Time (minutes) 55% Propylene Glycol + 45% DI Water 55% Propylene Glycol + 45% DI Water + 0.1% Benzotriazole + 0.025% Nanoparticles (CATAN Mix# 2) DI Water 10 Results from Phase I 5 4.5 ) 4 S/cm 3.5 3 2.5 2 1.5 1 Electrical Conductivity (µ 0.5 0 0 2000 4000 6000 8000 10000 12000 14000 16000 18000 20000 22000 Time (minutes) 55% Propylene Glycol + 45% DI Water + 0.1% Benzotriazole + 0.05% Nanoparticles (Mix# 2) 55% Propylene Glycol + 45% DI Water + 0.1% Benzotriazole + 0.025% Nanoparticles (Mix# 2) Electrical Conductivity vs. Time for the Coolant Formulations in a 1 L Dynamic Test Loop at 70oC 11 Results from Phase I 4 3.5 3 2.5 2 ( µS/cm) 1.5 Electrical Conductivity 1 0.5 0 0 20 40 60 80 100 120 Time (hours) 55% Propylene Glycol + 45% DI Water 55% Propylene Glycol + 45% DI Water + 0.1% Benzotriazole + 0.05% Nanoparticles (CATAN Mix#3) Electrical Conductivity vs. Time for the Coolant Formulations in a 1 L Dynamic Test Loop at 70oC 12 Discussion • With CATAN Mix # 1, the nanoparticles remained dispersed, making a uniform colloidal suspension. But the electrical conductivity was high (> 3.0 µS/cm) • With CATAN Mix # 2, the nanoparticles coagulated. But the electrical conductivity was lower than 1.0 µS/cm. • With CATAN Mix # 3, the nanoparticles could be dispersed in the coolant with the help of a sonicator, and the conductivity stayed lower than 1.0 µS/cm. 13 Conclusions • The Phase I research demonstrated the feasibility of utilizing nanoparticles in a glycol/water coolant mixture. • The electrical conductivity of a complex coolant formulation stayed below 2.0 µS/cm for more than 300 hours in short-term tests in a dynamic loop. • Preliminary economic evaluation suggests that the cost of the coolant could meet the target selling price of < $8.0/gallon. 14 Future Work • In Phase II of the SBIR project, the additive package will be optimized • Several non-ionic corrosion inhibitors will be evaluated • Electrodeposition rate of additives on the electrode surfaces will be determined • Material compatibility tests will be carried out • Optimized coolant will be tested in real fuel cell systems • Cost of the coolant will be evaluated 15 Publications and Presentations • None during SBIR Phase I • Before the SBIR Project – “Electrically Resistive Coolants for PEM Fuel Cells”, S. Mohapatra, presented at the Fuel Cell Seminar, Palm Springs, CA, Nov 16-19 (2002) – “Fuel Cell and Fuel Cell Coolant Compositions”, US, Canada and EU Patent Application pending (2002). 16 Hydrogen Safety The most significant hydrogen hazard associated with this project is: N/A (Complex Coolant Fluid development project does not use hydrogen) 17 Hydrogen Safety Our approach to deal with this hazard is: N/A 18 Questions? • Contact: Dr. Satish Mohapatra (PI) – (610) 262-9686, [email protected] • Acknowledgement: – Daniel Loikits (Program Manager), Stephen Dunn, Magaly Quessada, Larry Chiang, Dr. Eric Daniels, Dr. Victoria Dimonie, Dr. David Sudol, and Prof. Andrew Klein 19.
Details
-
File Typepdf
-
Upload Time-
-
Content LanguagesEnglish
-
Upload UserAnonymous/Not logged-in
-
File Pages19 Page
-
File Size-