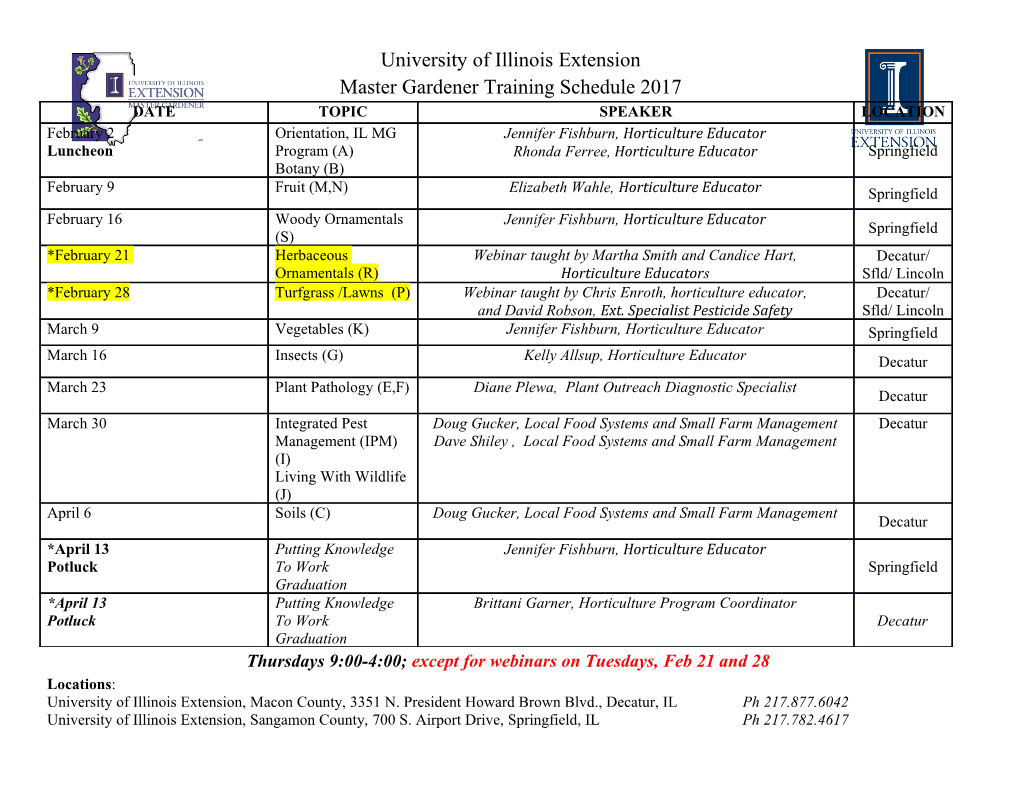
Design and Prototype Development of a Mini-Electric Arc Furnace F.A. Oyawale, Ph.D.1 and D.O. Olawale, M.Sc.2 1 Department of Industrial and Prod. Engineering, University of Ibadan, Nigeria 2 Department of Mechanical Engineering, The Polytechnic, Ibadan, Nigeria 1E-mail: [email protected] ABSTRACT Although information relating to the design and Electric arc furnaces (EAF) have the capabilities fabrication of an electric arc furnace of such a required for furnaces used for metallurgical small size as that fabricated through this research. An electric arc furnace was designed research, was not readily available in literature, and constructed to melt approximately 5kg of the available information relating to the giant steel/cast iron scraps, using locally produced sized electric arc furnaces were used as a guide Soderberg electrodes. Tests carried out showed in the design of this prototype. that it required about 60 minutes to heat up the furnace to the melting temperature of cast iron (1150C – 1400C). It took about 95 minutes to DESIGN THEORY AND CALCULATIONS melt the first charge of 2kg resulting in a melting rate of 21.05g/minute. The average electrode An electric arc furnace should have a powerful consumption rate was 0.0467cm/minute. A transformer, high thermal and electrical transformer efficiency of about 83% was also efficiency, and a lining made of high-grade achieved. refractory [Edneral, 1979]. (Keywords: electric arc furnace, melting rate, Shape and dimensions of the bath electrode consumption rate, transformer efficiency) The bath is usually conical-spherical with the 0 INTRODUCTION banks inclined at an angle of 45 . This form ensures quick melting. One tonne of molten 3 In an EAF, electric arcs are used to provide heat steel occupies 0.145m . The mass ratio of slag for melting and for smelting. The few EAFs in for acid-lined furnaces may be taken equal to the study country (Nigeria) are located in the 0.03 – 0.04. [Edneral, 1979]. integrated steel plant, the Delta Steel Company, and other large industrial plants. They are so The diameter-to-depth ratio of the bath operating complicated in design and so expensive that by the basic process is usually taken as: even national universities cannot afford to buy prototypes for experimental purposes. D = 5H (1) EAFs have numerous advantages required in where D = bath diameter, and H = total depth of furnaces for metallurgical research. Such the bath. features include close temperature and heat In existing furnaces, the height (h1), of the control, accurate analysis of melt, definite metal 1 refining sequence, high thermal efficiency (as spherical portion is roughly /5 of the total bath high as 70%), and production of steel directly depth: from pig iron and steel scrap. h1 = 0.2H (2) The objective of this research work is to design and develop an electric arc furnace for melting and the depth of the conical portion: steel/cast iron scraps using locally available materials. h2 = 0.8H (3) The Pacific Journal of Science and Technology –12– http://www.akamaiuniversity.us/PJST.htm Volume 8. Number 1. May 2007 (Spring) The total volume of the bath, Vb, is the sum of D1= Drc + S (11) the volumes of the truncated cone and that of the spherical segment. By virtue of the The thickness of the lining is found by thermal relationships given above: analysis from the condition that the furnace shell 0 should not be heated above 200 C at the end of 3 3 Vb = 0.0968 D (m ) (4) the furnace campaign. With the refractory lining δ mm thick, the furnace will have the following inside diameter of the shell: Dimensions of the reaction chamber Di.sh = Drc + 2 δ (12) The banks of a furnace are usually made 100 to 200 mm above the door sill level or the bath The steel shell varies in thickness and may 1 surface, to ensure that the slag does not contact range from /4 inch (6mm) thick for small 1 the brickwork or reach the joint between the wall furnaces and up to 1 /4 in (32 mm) thick on 80 to blocks and banks. The diameter of the reaction 100 ton furnaces [Robiette, 1972]. chamber is: Transformer power and furnace productivity Drc = D + 200 (mm) (5) Table 1 contains some recommendations on It is recommended that the following relationship transformer power for furnaces of different size, be used in determining the height of the reaction which are based on experiences in many chamber (H1) [Edneral, 1979]: countries. H1= (0.04 - 0.6) Drc (6) By analogy with the existing furnaces (using Table 1), the transformer power may be taken as the lower value relating to large-capacity Pap (MVA). Noting the inevitable switching off of furnaces. the furnace during melting required to push the scrap from the banks, partial operation of the The camber of the roof (h3 ) is: furnace at a reduced voltage when the arcs are open and radiation of much heat onto the walls h3 = 0.15Dr (7) and roof, the average power consumed during the melting period can be found by using a factor where Dr is roughly taken 1000 mm wider than of 0.8 – 0.9: Drc. Pav = 0.8 Pap (KVA) (13) Dr= Drc + 1000 h3= 0.15 (Drc + 1000 ) (8) Useful power consumed during the melting period (power consumed for the melting proper) The total height of the roof above the bath level is represented as: is given as: Pu = Pav cos φηel (KW) (14) H2 = H1 + h3 (9) Voltage taps The recommended slope (S) for the inclination of the wall is roughly 10% of the height from the The upper voltage tap of the secondary voltage line of banks to roof skewbacks: for small furnaces can be selected by using the following empirical formulae [Edneral, 1979]: H −100 For basic furnaces S = 1 (10) 10 3 = 15 PV AP (15) The diameter of the reaction chamber at the level of the roof skewbacks (i.e. at the level of For acid furnaces: the upper edge of the furnace shell) is: 3 V += 1570 PAP (16) The Pacific Journal of Science and Technology –13– http://www.akamaiuniversity.us/PJST.htm Volume 8. Number 1. May 2007 (Spring) Table 1: Recommended Transformer Power for Furnaces of Different Sizes. Furnace Capacity (t) Transformer Power (MVA) for 25 50 75 100 150 200 250 400 Making Various Steels (i) Alloy steels 5-18 20-25 - 30-35 - 55-70 - - (ii) Carbon steels 18-22 28-32 30-45 40-50 45-60 60-80 90 120 Transformer power of super - 40 - 60 - 125 - 200 powerful furnaces of the future (Source: Electrometallurgy and Ferro-alloys, 1979) Electrode diameter where, m = mass to be melted (kg), The diameter of electrodes can be found by the c = specific heat capacity of metal to be melted formula: (KJ/Kg0C), 0 406.0 I 2δ θ2 = melting point of the metal ( C), 3 (cm) (17) d = 0 K θ1 = room temperature ( C), and Where I = linear current, (A) L = latent heat of fusion of the metal 3 Pap10 I = , MATERIAL AND METHODS V 3 max The electric arc furnace comprises two Soderbeg self baking electrodes (Afolabi, 2004); δ = electrode resistivity at 5000C (for graphitized an electrode support and sliding mechanism; a electrodes δ = 10 ohm. Mm2/m), and tiltable crucible lined with refractory silica brick in which melting takes place; the roof also lined K = coefficient (for graphitized electrodes K = 2.1 with silica brick, which is removable for charging W/cm2). and for pouring; and the support frame which carries the other parts. The crucible and roof The diameter of electrodes can also be found by were constructed using 4mm thick mild steel the allowable current density (A/cm2). sheet. The furnace is shown schematically in Figure 1 and pictorially in Figure 2. Electrode spacing The recommended ratio of the electrode spacing The furnace is supplied at 50Hz using a tapped diameter to the bath diameter is 0.45 for small power transformer with a high current furnaces, 0.35 for medium sized and large secondary, the connections between the furnaces, and still lower for super powerful transformer and the electrodes is a length of furnaces (Edneral, 1979). flexible cable which allows the electrodes to be moved vertically and also for the complete roof Energy distribution assembly to be lifted and moved horizontally. The energy required for melting of metal scrap is Melting is achieved by the heat generated by the electric arc drawn between the electrodes tips and the scrap metals. The transformer is oil Q = mc(θ2- θ1) + mL (18) cooled. The Pacific Journal of Science and Technology –14– http://www.akamaiuniversity.us/PJST.htm Volume 8. Number 1. May 2007 (Spring) Table 2: Test Data. (cm) (kg) Test Electrode Electrode Time of Consumption Consumption Mass of charge Mass of charge Operation (min) 1 2 1 2 102 1.0 3.0 2 2 89 1.0 3.0 3 2 94 1.0 3.0 4 3 128 2.0 4.0 5 3 130 2.0 4.0 6 3 123 2.0 4.0 Figure 1: Schematic of the Electric Arc Furnace. Vp= 220V, Vo= 62V, Ip= 30.5A, Io= 90A Soderberg Table 2: Average Melting Rate and Electrode electrodes Consumption. Melting Chamber η rate, (cm/min.) consumption (cm) Mass of charge (Kg) Average total electrode Melting temperature (C) Transformer efficiency, Average melting rate (g/min) Electrode Consumption ratio Average time of melting (min.) Oil-Cooled Average electrode consumption Transformer 1150- 2 95 4.0 1:3 21.05 0.042 83 1400 1150- 3 127 6.0 1;2 23.62 0.047 83 Figure 1: Prototype Electric Arc Furnace.
Details
-
File Typepdf
-
Upload Time-
-
Content LanguagesEnglish
-
Upload UserAnonymous/Not logged-in
-
File Pages5 Page
-
File Size-