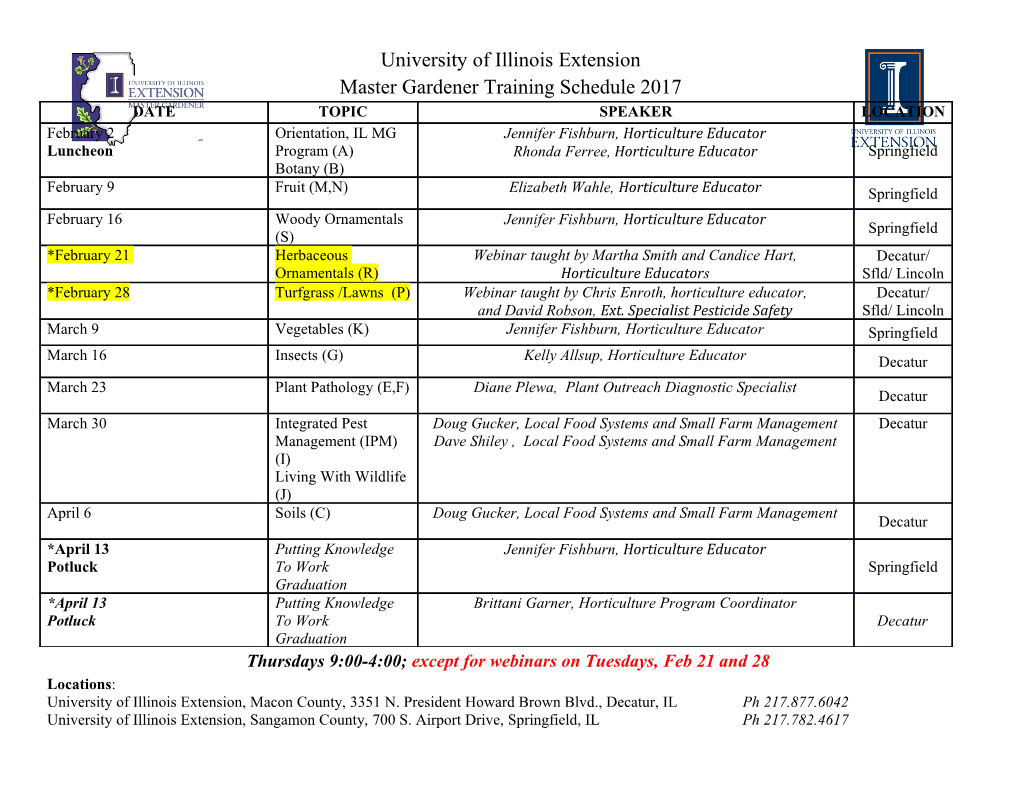
Journal of Manufacturing and Materials Processing Article Probing Magnetic Pulse Welding of Thin-Walled Tubes Koen Faes 1,* , Rishabh Shotri 2 and Amitava De 2 1 Belgian Welding Institute, Technologiepark Zwijnaarde 935, B-9052 Ghent, Belgium 2 Indian Institute of Technology, Bombay, Mumbai 400076, India; [email protected] (R.S.); [email protected] (A.D.) * Correspondence: [email protected] Received: 29 October 2020; Accepted: 9 December 2020; Published: 11 December 2020 Abstract: Magnetic pulse welding is a solid-state joining technology, based on the use of electromagnetic forces to deform and to weld workpieces. Since no external heat sources are used during the magnetic pulse welding process, it offers important advantages for the joining of dissimilar material combinations. Although magnetic pulse welding has emerged as a novel technique to join metallic tubes, the dimensional consistency of the joint assembly due to the strong impact of the flyer tube onto the target tube and the resulting plastic deformation is a major concern. Often, an internal support inside the target tube is considered as a solution to improve the stiffness of the joint assembly. A detailed investigation of magnetic pulse welding of Cu-DHP flyer tubes and 11SMnPb30 steel target tubes is performed, with and without an internal support inside the target tubes, and using a range of experimental conditions. The influence of the key process conditions on the evolution of the joint between the tubes with progress in time has been determined using experimental investigations and numerical modelling. As the process is extremely fast, real-time monitoring of the process conditions and evolution of important responses such as impact velocity and angle, and collision velocity, which determine the formation of a metallic bond, is impossible. Therefore, an integrated approach using a computational model using a finite-element method is developed to predict the progress of the impact of the flyer onto the target, the resulting flyer impact velocity and angle, the collision velocity between the flyer and the target, and the evolution of the welded joint, which are usually impossible to measure using experimental observations. Keywords: magnetic pulse welding; dissimilar material combinations; impact velocity; impact angle; collision velocity 1. Introduction Magnetic pulse welding (MPW) is a solid-state impact welding technology able to create joints between two overlapping parts by a progressive collision, which is generated by an intense electromagnetic (EM) impulse [1]. Figure1 shows a schematic layout for the MPW of overlapping tubes. A capacitor bank is charged by a power supply to store the required amount of energy, which is released instantaneously into a coil by using a high-current switch. The resulting discharge current of high magnitude and high frequency induces an intense transient EM field inside the coil, which induces eddy current in the outer tube [2]. The induced eddy current causes a differential EM field on both sides of the outer tube, resulting in an EM pressure that, in turn, causes the outer tube to impact onto the internal tube with high velocity [3]. As a result of the collision between the outer and the inner tubes at a certain angle, the tubes experience intense localized plastic deformation and a jet is generated along the surfaces of the materials before they make contact, which is able to remove the surface impurities and promote consolidation between the clean mating surfaces under EM pressure [2,3]. J. Manuf. Mater. Process. 2020, 4, 118; doi:10.3390/jmmp4040118 www.mdpi.com/journal/jmmp J. Manuf. Mater. Process. 2020, 4, 118 2 of 19 J. Manuf. Mater. Process. 2020, 4, x FOR PEER REVIEW 2 of 19 The consolidation between the two parts occurs without any bulk melting [4], although local melting [2,3]. The consolidation between the two parts occurs without any bulk melting [4], although local at scattered locations along the joint interface is reported for MPW of AA6060 flyer tubes and copper melting at scattered locations along the joint interface is reported for MPW of AA6060 flyer tubes and target rods [5], AA1050 flyer and target sheets [6] and AA6060 flyer tubes and AlSi10Mg target rods [7]. copper target rods [5], AA1050 flyer and target sheets [6] and AA6060 flyer tubes and AlSi10Mg target For the overlapping assembly, the outer part is referred to as the flyer and the inner part is referred to rods [7]. For the overlapping assembly, the outer part is referred to as the flyer and the inner part is as the target. Since the bulk melting of materials is avoided, MPW is increasingly considered for the referred to as the target. Since the bulk melting of materials is avoided, MPW is increasingly joining of dissimilar materials [8]. considered for the joining of dissimilar materials [8]. Figure 1. Schematic layout of magnetic pulse welding (MPW) set-up forfor joiningjoining ofof tubes.tubes. TheThe joining ofof tubular parts with MPW involves thethe use of a thick circular coil, with the assembly ofof thethe overlappingoverlapping flyerflyer andand targettarget tubestubes placedplaced insideinside thethe coilcoil [[9].9]. The coil imposesimposes a radialradial EMEM impulseimpulse pressurepressure onon thethe flyerflyer tubetube forfor aa veryvery shortshort duration,duration, thatthat forcesforces thethe flyerflyer toto impactimpact ontoonto thethe targettarget tubetube in in a progressivea progressive manner, manner, resulting resulting in jetting in jetting of surface of surface impurities impurities from the from original the interface, original ainterface, controlled a controlled plastic deformation plastic deformation and bonding and between bondingtwo between tubes two [10]. tubes The [10]. welded The interface welded interface in MPW isin characteristicallyMPW is characteristically similar to similar that in to explosion that in ex welding,plosion welding, which is which created is ascreated a result as ofa result a traverse of a oftraverse collision of collision points, followed points, followed by plastic by deformation plastic deformation at a high at strain a high rate strain and rate jetting and out jetting of surface out of impurities,surface impurities, and consolidation and consolidation between cleanbetween metallic clean layers metallic along layers the interfacealong the between interface the between impacting the flyerimpacting and target flyer [and5]. Thetarget phenomena [5]. The phenomena of jetting due of jetting to the due high to velocity the high impact velocity between impact the between flyer and the targetflyer and and target the consequent and the consequent shearing of veryshearing thin layersof very from thin the layers metallic from surfaces, the metallic the composition surfaces, the of thecomposition metal jets of and the the metal possible jets and effect the of possible jetting on effect the profileof jetting of theon the welded profile interface of the welded are examined interface by severalare examined researchers by several for MPW researchers of similar for and MPW dissimilar of similar materials and dissimilar [11–13]. materials [11–13]. Often,Often, an internal support is employedemployed to enhanceenhance the stistiffnessffness andand avoidavoid excessiveexcessive plasticplastic deformationdeformation and fracture fracture of of the the tube tube assembly assembly as asa re asult result of the of thehigh high velocity velocity impact impact of the of flyer the flyertube tubeonto ontothe target the target tube [14]. tube Especially, [14]. Especially, tubes with tubes a withsmall awall small thickness wall thickness need to needbe supported, to be supported, because becausethey can theyhardly can resist hardly radial resist forces. radial A study forces. comp A studyaring comparing the weld performance the weld performance in terms of the in terms contour of thedeformation, contour deformation, microstructure microstructure and tensile strength and tensile of tubular strength joints, of achieved tubular joints, with and achieved without with internal and withoutsupport, internalwas found support, in [15]. was An found aluminium in [15 ].AA6060-O An aluminium flyer tube AA6060-O (outer diameter: flyer tube 76 (outer mm × diameter: 2.5 mm) 76 mm 2.5 mm) was joined onto a steel 34 (St34 mod) target tube (outer diameter: 76 mm 2.5 mm). was joined× onto a steel 34 (St34 mod) target tube (outer diameter: 76 mm × 2.5 mm). Other× sources Otherreport sourcesthe use reportof an internal the use suppo of an internalrt placed support inside the placed target inside tube the for target MPW tube of AA5052 for MPW flyer of AA5052tubes of flyerwall thickness tubes of wall of 1 mm thickness and SS304 of 1 mmtarget and tubes SS304 of wall target thickness tubes of of wall 1 mm thickness [16], and of for1 mmMPW[16 of], AA6060 and for MPWflyer tubes of AA6060 of wall flyer thickness tubes of of wall 1.5 thicknessmm and ofCu-ETP 1.5 mm target and Cu-ETP tubes of target walltubes thickness of wall of thickness1 mm [17]. of 1Although mm [17]. these Although studies these showed studies the showed need thefor needan internal for an internalsupport supportduring duringMPW of MPW tubular of tubular parts, parts,detailed detailed quantitative quantitative analyses analyses of MPW of MPWwith and with without and without an internal an internal support support are not are provided. not provided. TheThe plastic deformation ofof thethe flyerflyer and target tubetube during MPW is influencedinfluenced byby the nature and magnitudemagnitude ofof the the applied applied discharge discharge current, current, the original the original joint configuration, joint configuration, the mechanical the mechanical properties ofproperties the tube materials,of the tube the materials, wall thickness the wall of thethickness tubes andof the the tubes initial and stando theff initialdistance standoff between distance them, between them, and the impact velocity of the flyer. For example, typical AA6061 flyer tubes (diameter: 40 mm × 2 mm) experienced a radial plastic deformation in the range of 1 to 2 mm during J. Manuf. Mater. Process. 2020, 4, 118 3 of 19 and the impact velocity of the flyer.
Details
-
File Typepdf
-
Upload Time-
-
Content LanguagesEnglish
-
Upload UserAnonymous/Not logged-in
-
File Pages19 Page
-
File Size-