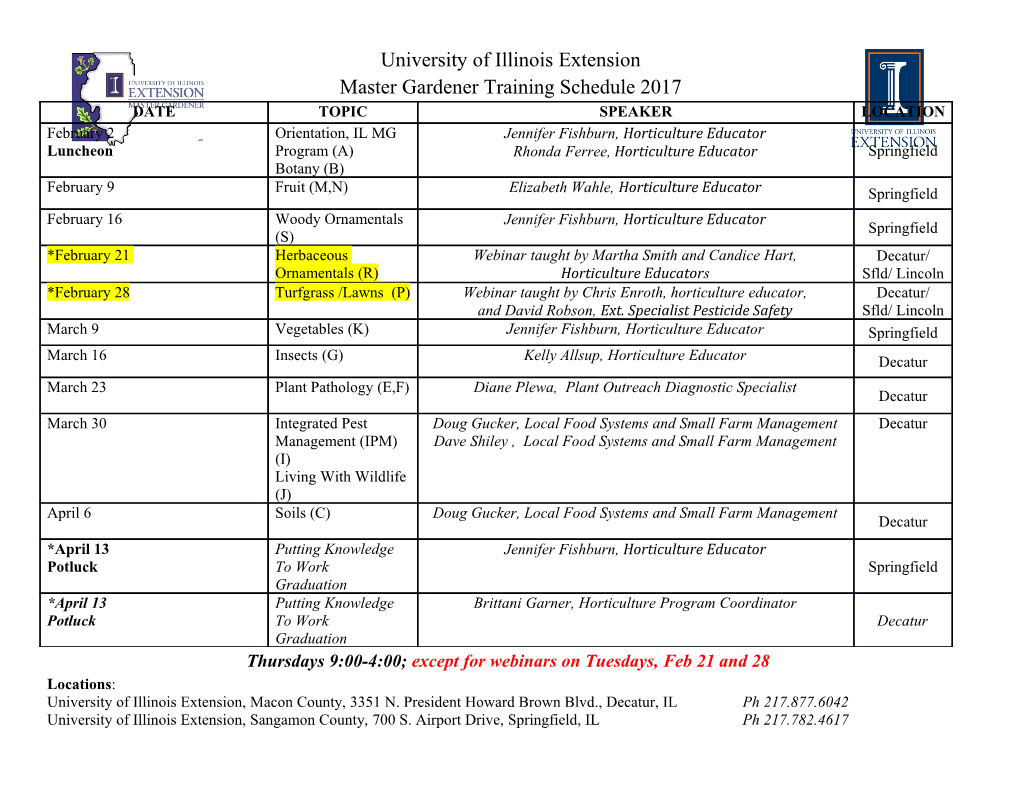
INVESTIGATION OF SILICONE RUBBER BLENDS AND THEIR SHAPE MEMORY PROPERTIES A Thesis Presented to The Graduate Faculty of The University of Akron In Partial Fulfillment Of the Requirement for the Degree Master of Science Yuelei Guo May, 2018 INVESTIGATION OF SILICONE RUBBER BLENDS AND THEIR SHAPE MEMORY PROPERTIES Yuelei Guo Thesis Approved: Accepted: Advisor Department Chair Dr. Kevin Cavicchi Dr. Sadhan C. Jana Committee Member Interim-Dean of the College Dr. Erol Sancaktar Dr. Ali Dhinojwala Committee Member Dean of the Graduate School Dr. Nicole Zacharia Dr. Chand Midha Date ii ABSTRACT Silicone rubber is widely used as an elastomer. This thesis investigates the fabrication and material properties of silicone rubber blended with some inexpensive fillers. The section of this thesis focuses on cornstarch-silicone rubber blends. In acetoxy cured silicone rubber, cornstarch has good compatibility and is able to blend well with the silicone resin. Samples were prepared by simple physical mixing. The crosslinking degree and other mechanical abilities can be investigated as a function of the weight percent of cornstarch and water. The second section of this thesis focuses on shape memory polymers. Shape memory polymers were fabricated by mixing acetoxy silicone with crystalline small molecules. The solid-liquid transition of the small molecule is able to generate reversible solid networks, which enable the shape memory effect. The shape memory effect properties tested as a function of the weight percent of the small molecule in samples. With increasing weight percent of the small molecule, the fixity is increased to ca. 99% and the recovery decreased to ca. 87%. Based on these tests, an optimum blend formulation is found, which shows the best shape memory performance can be found and repeatability through several test cycles. Due to the differences in the interaction degree between the small molecule and the silicone rubber, the choice of the small molecule is also an important factor to influence the shape memory effect. iii ACKNOWLEDGEMENTS First, I would like to show my deepest gratitude to my supervisor, Prof. Kevin A Cavicchi, who has provided me with valuable guidance in the last two years. Without his academic and constructive advice, the completion of this thesis would be impossible. I have learned a lot by joining his group. It is a valuable experience to have him as my supervisor. Second, I would like to express my heartfelt gratitude to all members in our group: Guodong Deng, Junyoung Seo, Marcos Pantoja, Pei-zhen Jian, Tzu-yu Lai, Juan Marin Angel, Bangan Peng, Luis Ruiz-Santiago, Xindi Li, Cheng Li, Lei Zhou and Yi Ting Lo. I’m so glad that I have the chance to work together with you. I appreciate your help and I’ll always remember the time we spent together. Last, my thanks would go to my beloved family for their loving considerations and great confidence in me all through these years. My family always gives me the strongest support and I’ll continue to be a better person. iv TABLE OF CONTENTS LIST OF FIGURES ................................................................................................... VII LIST OF SCHEMES ..................................................................................................... X LIST OF TABLES ................................................................................................................ XI CHAPTER I ................................................................................................................... 1 INTRODUCTION ...................................................................................................... 1 1.1 Silicone rubber .................................................................................................. 1 1.1.1 Introduction of Silicone rubber .................................................................. 1 1.1.2 Vulcanization methods of silicone rubber .................................................. 3 1.1.3 Silicone Rubber Blend ................................................................................ 6 1.1.4 Applications of silicone rubber ................................................................... 8 1.2 Shape memory polymer .................................................................................. 11 1.2.1 Introduction of shape memory polymers ................................................ 11 1.2.2 Application of shape memory polymers ................................................... 14 CHAPTER II ................................................................................................................ 16 EXPERIMENTAL ........................................................................................................ 16 2.1 Materials and tools .......................................................................................... 16 2.2 Sample Preparation......................................................................................... 17 v 2.3 Characterization ............................................................................................. 18 2.3.1 Crosslinking Degree ................................................................................. 19 2.3.2 Strain-Controlled Shape Memory Experiments ....................................... 20 2.3.3. DMA (Dynamic Mechanical Analysis) ................................................... 21 2.3.4 TGA (Thermogravimetric Analysis) ......................................................... 22 2.3.5 DSC (Differential Scanning Calorimetry) ................................................ 22 2.3.6 Microscope ............................................................................................... 22 CHAPTER III .............................................................................................................. 24 RESULTS AND DISCUSSION ............................................................................... 24 3.1 Cornstarch-PDMS Blend ................................................................................ 24 3.2 Shape Memory Silicone Rubber Blend ........................................................... 33 CHAPTER IV ................................................................................................................... 47 CONCLUSIONS ...................................................................................................... 47 REFERENCES ............................................................................................................ 49 vi LIST OF FIGURES Figure Page 1.1 Structure and the basic unit of the silicone rubber................................................ 3 1.2 Structure of fillers (a) Cornstarch (b)1,10-Decanediol (c)12-Hroxystearicacid (d) Stearic acid ................................................................................................................. 7 1.3 Structure of shape memory polymer ................................................................... 13 1.4 Mechanism of thermally induced SMP (schematic) ........................................... 14 2.1 (a) Mixer (b) Micro milling machine (c) Mold (5mmx5mmx1mm) (d) Modified crescent wrench ........................................................................................................ 17 2.2 Procedure to prepare a sample ............................................................................ 18 3.1 Solubility test of non-crosslinked silicone rubber in different solvents (a) silicone rubber in Toluene (b) silicone rubber in Chloroform ................................. 24 3.2 Swelling capacity vs Different amount of cornstarch ......................................... 25 3.3 Swelling capacity vs Amount of water ............................................................... 26 3.4 The amount of cornstarch vs Swelling capacity ................................................. 27 3.5 DMA strain sweep curves (storage modulus vs strain) for different weight percent sample, the ratio means water:PDMS:cornstarch (a) strain sweep curves for different weight percent cornstarch sample (b) strain sweep curves for different weight percent water ................................................................................................. 28 3.6 DMA stress-strain test for different weight percent cornstarch samples (the vii amount of silicone:cornstarch = 30:30, 30:35, 30:40, 30:45, 30:50, 30:55 and pure PDMS) ...................................................................................................................... 30 3.7 TGA tests for (a) PDMS, cornstarch and 1:30:30 sample (b) different weight percent samples (the amount of water: silicone: cornstarch=1:30:30, 1:30:35, 1:30:40, 1:30:45, 1:30:50, 1:30:55) .......................................................................... 32 3.8 A series of shape memory effect (a) the initial shape (b) use tweezer to keep a shape (c) put the sample into hot water for 5 seconds (d) the temporary shape (e) put the sample back into the hot water for 5 seconds (f) the sample recovers to the initial shape ............................................................................................................... 33 3.9 TGA curves for PDMS, Decanediol and 50% Decanediol-Silicone blend. Experiments were conducted using a nitrogen atmosphere with a heating rate of 10oC min-1 from 25°C to 800°C .............................................................................. 34 3.10 (a) DSC curves for Decanediol Silicone Blend with different weight percent Decanediol (10%, 20%, 30%, 40%, 50%,
Details
-
File Typepdf
-
Upload Time-
-
Content LanguagesEnglish
-
Upload UserAnonymous/Not logged-in
-
File Pages65 Page
-
File Size-